Introduction to Chamfered holes
Chamfered holes are a type of mechanical feature commonly found in various engineering and manufacturing applications. These holes are characterized by a beveled edge or angled transition at the entrance of the hole, which serves several important purposes. In this comprehensive article, we will delve into the world of chamfered holes, exploring their definition, applications, benefits, and the various methods used to create them.
What is a Chamfer?
Before we dive into the specifics of chamfered holes, let’s first understand what a chamfer is. A chamfer is an angled or beveled edge that is created by removing material from a sharp corner or edge of a workpiece. Chamfers can be found on both external and internal features of a component, and they are typically specified by the angle and depth of the cut.
Definition of Chamfered Holes
A chamfered hole is a circular opening in a workpiece that features a chamfer at its entrance. The chamfer is usually located at the top edge of the hole, where it transitions from the surface of the workpiece to the inner diameter of the hole. Chamfered holes can be created in various materials, including metals, plastics, and composites, and they are used in a wide range of industries, such as automotive, aerospace, and manufacturing.
Benefits of Chamfered Holes
Easier Insertion of Mating Components
One of the primary benefits of chamfered holes is that they facilitate the insertion of mating components, such as bolts, pins, or shafts. The angled edge of the chamfer acts as a guide, helping to align the mating component with the hole and reducing the risk of misalignment or damage during assembly. This is particularly important in applications where tight tolerances and precise fit are required.
Reduced Stress Concentration
Another advantage of chamfered holes is that they help to reduce stress concentration at the edge of the hole. When a hole is drilled or punched into a material, the sharp edge created at the entrance of the hole can act as a stress riser, leading to increased stress concentration in that area. By adding a chamfer to the edge of the hole, the stress is distributed more evenly, reducing the risk of cracking, fatigue, or failure under load.
Improved Aesthetics
In addition to their functional benefits, chamfered holes can also enhance the overall aesthetics of a component. The angled edge of the chamfer creates a visually appealing transition between the surface of the workpiece and the hole, giving the component a more polished and professional appearance. This is particularly important in applications where the appearance of the final product is a key consideration, such as in consumer goods or architectural elements.
Methods for Creating Chamfered Holes
There are several methods that can be used to create chamfered holes, each with its own advantages and limitations. The choice of method will depend on factors such as the material being worked, the size and depth of the hole, the required precision, and the available equipment and tooling.
Drilling with Chamfer Drills
One of the most common methods for creating chamfered holes is by using chamfer drills. These specialized drill bits feature an angled cutting edge at the tip, which creates the chamfer as the hole is being drilled. Chamfer drills are available in a range of sizes and angles, and they can be used with standard drilling equipment, making them a versatile and accessible option for many applications.
Counterboring
Counterboring is another method that can be used to create chamfered holes. In this process, a two-step drilling operation is performed, where a larger diameter hole is first drilled to the desired depth of the chamfer, followed by a smaller diameter hole that extends beyond the chamfer to the required depth of the hole. Counterboring is often used when a precise chamfer depth or a specific chamfer angle is required, as it allows for greater control over the final geometry of the hole.
Reaming with Chamfer Reamers
Reaming is a finishing process that is used to improve the accuracy, smoothness, and consistency of a hole that has already been drilled or bored. Chamfer reamers are specialized tools that feature a chamfered cutting edge, which creates the angled transition at the entrance of the hole as it is being reamed. Reaming with chamfer reamers is often used in applications where a high degree of precision and surface finish is required, such as in the production of high-performance engine components or medical devices.
Punching with Chamfered Punches
Punching is a high-speed, high-volume process that is used to create holes in sheet metal or other thin materials. Chamfered punches are specialized tools that feature an angled cutting edge, which creates the chamfer as the hole is being punched. Punching with chamfered punches is often used in applications where a large number of holes need to be produced quickly and efficiently, such as in the production of electronic enclosures or automotive body panels.
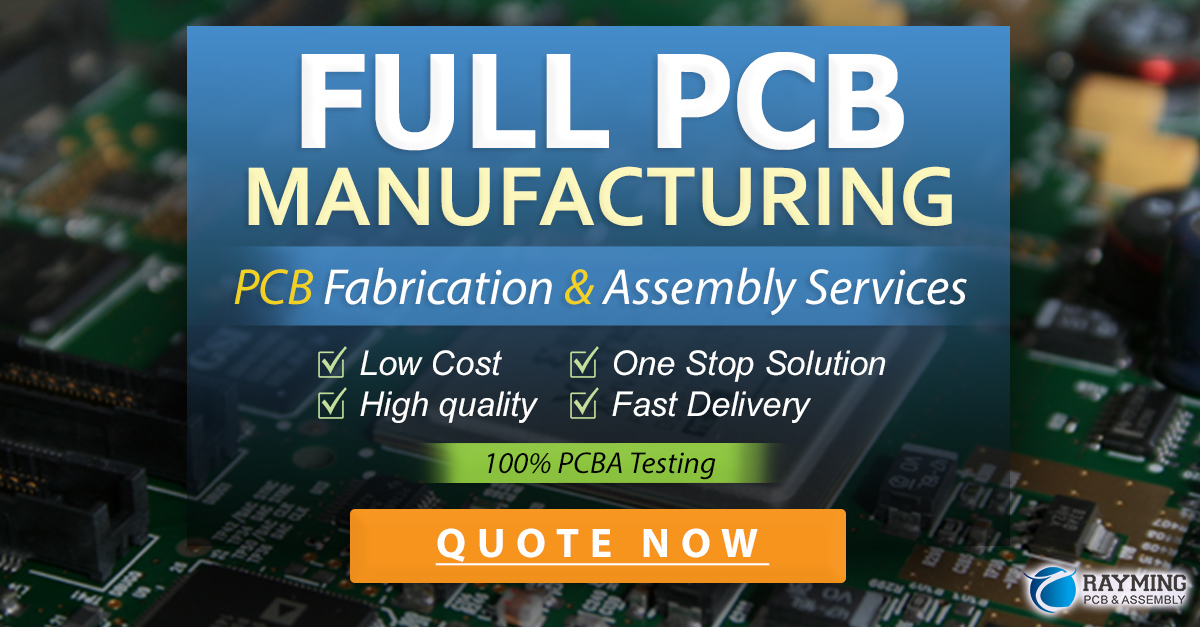
Design Considerations for Chamfered Holes
When designing components with chamfered holes, there are several key factors that need to be considered to ensure that the holes will perform as intended and meet the required specifications.
Chamfer Angle
The angle of the chamfer is one of the most important design considerations for chamfered holes. The most common chamfer angles are 45°, 60°, and 90°, although other angles may be used depending on the specific application and requirements. The choice of chamfer angle will depend on factors such as the material being worked, the size and depth of the hole, and the intended use of the component.
Chamfer Depth
The depth of the chamfer is another important design consideration for chamfered holes. The depth of the chamfer will determine the amount of material that is removed from the edge of the hole, and it will also affect the overall geometry and strength of the component. In general, deeper chamfers will provide greater benefits in terms of stress reduction and ease of insertion, but they may also require more material to be removed and may impact the overall structural integrity of the component.
Hole Diameter and Depth
The diameter and depth of the hole are also important design considerations for chamfered holes. The diameter of the hole will determine the size of the mating component that can be inserted, while the depth of the hole will determine the amount of engagement between the mating component and the hole. In general, larger diameter and deeper holes will provide greater strength and stability, but they may also require more material to be removed and may be more difficult to produce accurately.
Material Properties
The properties of the material being worked are another important design consideration for chamfered holes. Different materials will have different strengths, hardness, and machinability, which can affect the choice of chamfer angle, depth, and production method. For example, harder materials may require a shallower chamfer angle to prevent chipping or cracking, while softer materials may allow for deeper chamfers and more aggressive machining parameters.
Applications of Chamfered Holes
Chamfered holes are used in a wide range of applications across various industries, from automotive and aerospace to manufacturing and construction. Some of the most common applications of chamfered holes include:
Bolted Connections
Chamfered holes are commonly used in bolted connections, where they help to align the bolt with the hole and reduce the risk of cross-threading or damage to the threads. The chamfer also helps to distribute the load more evenly around the edge of the hole, reducing stress concentration and improving the overall strength and reliability of the connection.
Bearing Housings
Chamfered holes are often used in bearing housings, where they help to facilitate the insertion and removal of the bearing and reduce the risk of damage to the bearing or the housing during assembly or maintenance. The chamfer also helps to distribute the load more evenly around the edge of the hole, reducing stress concentration and improving the overall performance and durability of the bearing.
Hydraulic and Pneumatic Fittings
Chamfered holes are commonly used in hydraulic and pneumatic fittings, where they help to facilitate the insertion and sealing of the fitting and reduce the risk of leaks or damage to the sealing surfaces. The chamfer also helps to guide the fitting into the hole and ensure proper alignment, improving the overall reliability and performance of the system.
Electrical Connectors
Chamfered holes are often used in electrical connectors, where they help to guide the pins or contacts into the holes and ensure proper alignment and contact pressure. The chamfer also helps to reduce the risk of damage to the pins or contacts during insertion or removal, improving the overall reliability and durability of the connector.
Chamfered Holes vs. Countersunk Holes
Chamfered holes are often confused with countersunk holes, which are another type of mechanical feature that is used to create a recessed or flush surface for the head of a fastener. While both chamfered and countersunk holes feature an angled transition at the entrance of the hole, there are some key differences between the two:
Geometry
The main difference between chamfered and countersunk holes is the geometry of the angled transition. Chamfered holes have a simple, straight angled cut at the entrance of the hole, while countersunk holes have a conical shape that is designed to match the angled underside of a countersunk fastener head.
Depth
Countersunk holes are typically deeper than chamfered holes, as they need to accommodate the entire head of the fastener and create a flush surface. Chamfered holes, on the other hand, are usually shallower and are used more for guidance and stress reduction than for creating a flush surface.
Application
Countersunk holes are primarily used in applications where a flush or recessed surface is required for aesthetic or functional reasons, such as in aerospace or automotive body panels. Chamfered holes, on the other hand, are used more for functional purposes, such as facilitating insertion, reducing stress concentration, and improving overall performance and reliability.
FAQ
What is the difference between a chamfer and a bevel?
A chamfer and a bevel are similar in that they both involve creating an angled transition between two surfaces. The main difference is that a chamfer is typically a flat, angled cut, while a bevel is a more gradual, curved transition. Chamfers are often used for functional purposes, such as reducing stress concentration or facilitating insertion, while bevels are often used for aesthetic purposes, such as creating a decorative edge on a piece of furniture.
Can chamfered holes be created in any material?
Chamfered holes can be created in most machinable materials, including metals, plastics, and composites. However, the choice of production method and chamfer geometry may vary depending on the specific material properties and requirements. For example, harder materials may require a shallower chamfer angle and more precise machining parameters to prevent chipping or cracking, while softer materials may allow for deeper chamfers and more aggressive machining.
How do I specify the size of a chamfered hole?
The size of a chamfered hole is typically specified by its diameter and depth, along with the angle and depth of the chamfer. For example, a chamfered hole may be specified as a 10mm diameter hole with a 45° chamfer that is 1mm deep. It is important to clearly communicate these dimensions and tolerances to ensure that the hole will meet the required specifications and perform as intended.
Can chamfered holes be created with 3D printing?
Yes, chamfered holes can be created with 3D printing, although the specific process and parameters may vary depending on the type of 3D printing technology being used. For example, in fused deposition modeling (FDM) 3D printing, chamfered holes can be created by adjusting the print settings to include a chamfer at the top of the hole. In stereolithography (SLA) 3D printing, chamfered holes can be created by designing the chamfer into the CAD model and using a high-resolution printer to accurately reproduce the geometry.
Summary
Chamfered holes are a versatile and widely used mechanical feature that offers a range of benefits in terms of ease of assembly, stress reduction, and overall performance and reliability. By creating an angled transition at the entrance of the hole, chamfered holes help to guide mating components, distribute loads more evenly, and improve the aesthetics of the finished product.
There are several methods that can be used to create chamfered holes, including drilling with chamfer drills, counterboring, reaming with chamfer reamers, and punching with chamfered punches. The choice of method will depend on factors such as the material being worked, the size and depth of the hole, and the required precision and surface finish.
When designing components with chamfered holes, it is important to consider factors such as the chamfer angle, depth, hole diameter and depth, and material properties to ensure that the holes will perform as intended and meet the required specifications. By carefully considering these design factors and selecting the appropriate production method, engineers and manufacturers can create high-quality, reliable components that meet the needs of a wide range of applications and industries.
Leave a Reply