History of Carbon Contacts
The use of carbon contacts dates back to the early 20th century when they were first developed for use in telegraph systems. At the time, carbon was chosen as a contact material due to its high electrical conductivity and resistance to wear and oxidation. As technology advanced, carbon contacts found their way into various other applications, such as automotive electrical systems and industrial control systems.
In the 1950s, the development of silver-graphite contacts marked a significant milestone in the history of carbon contacts. These contacts, which consisted of a silver matrix with graphite particles dispersed throughout, offered improved performance compared to pure carbon contacts. They exhibited lower contact resistance, higher current-carrying capacity, and better resistance to wear and arc erosion.
Over the years, advancements in materials science have led to the development of new types of carbon contacts, such as those based on carbon nanotubes. These contacts offer even better performance than traditional silver-graphite contacts, with higher electrical conductivity, lower contact resistance, and improved mechanical properties.
Advantages of Carbon Contacts
Carbon contacts offer several advantages over other types of electrical contacts, making them the preferred choice for many applications. Some of the key benefits of carbon contacts include:
-
High electrical conductivity: Carbon contacts have excellent electrical conductivity, which allows them to carry high currents with minimal power loss. This is particularly important in applications where efficient power transfer is critical, such as in power distribution systems and electric motors.
-
Low contact resistance: The contact resistance of carbon contacts is typically lower than that of other contact materials, such as copper or brass. This means that less energy is lost due to resistance when current flows through the contacts, resulting in improved system efficiency and reduced heat generation.
-
High wear resistance: Carbon contacts are highly resistant to wear and tear, even under heavy use conditions. This is due to the hard and lubricating properties of the carbon material, which helps to reduce friction and prevent surface damage. As a result, carbon contacts have a longer service life compared to other contact materials.
-
Arc erosion resistance: When electrical contacts open and close, they can generate an electric arc that can cause damage to the contact surfaces. Carbon contacts are highly resistant to arc erosion, thanks to their ability to dissipate heat quickly and their high melting point. This helps to extend the life of the contacts and maintain their performance over time.
-
Temperature stability: Carbon contacts maintain their electrical and mechanical properties over a wide temperature range, making them suitable for use in environments with extreme temperatures. This is particularly important in applications such as aerospace and defense, where components may be exposed to high or low temperatures.
-
Cost-effectiveness: While carbon contacts may have a higher initial cost compared to other contact materials, their long service life and high performance make them a cost-effective choice in the long run. The reduced maintenance and replacement costs associated with carbon contacts can result in significant savings over the life of the system.
Applications of Carbon Contacts
Carbon contacts are used in a wide range of applications across various industries. Some of the most common applications include:
-
Automotive electrical systems: Carbon contacts are used in various components of automotive electrical systems, such as starter motors, alternators, and switches. They are particularly well-suited for these applications due to their high current-carrying capacity, resistance to wear and arc erosion, and ability to withstand high temperatures.
-
Industrial control systems: In industrial settings, carbon contacts are used in contactors, relays, and circuit breakers. These components are critical for controlling the flow of electricity in machinery and equipment, and the high reliability and long service life of carbon contacts make them an ideal choice for these applications.
-
Power distribution systems: Carbon contacts are used in switchgear and other components of power distribution systems, where they help to control and protect electrical equipment. Their high current-carrying capacity and resistance to arc erosion make them well-suited for handling the high voltages and currents present in these systems.
-
Aerospace and defense: In aerospace and defense applications, carbon contacts are used in various electrical and electronic systems, such as avionics, weapons systems, and communication equipment. Their ability to maintain their performance under extreme temperatures and their high reliability make them a critical component in these demanding environments.
-
Renewable energy: Carbon contacts are used in various components of renewable energy systems, such as wind turbines and solar inverters. Their high current-carrying capacity and resistance to wear and arc erosion make them well-suited for handling the variable and intermittent nature of renewable energy sources.
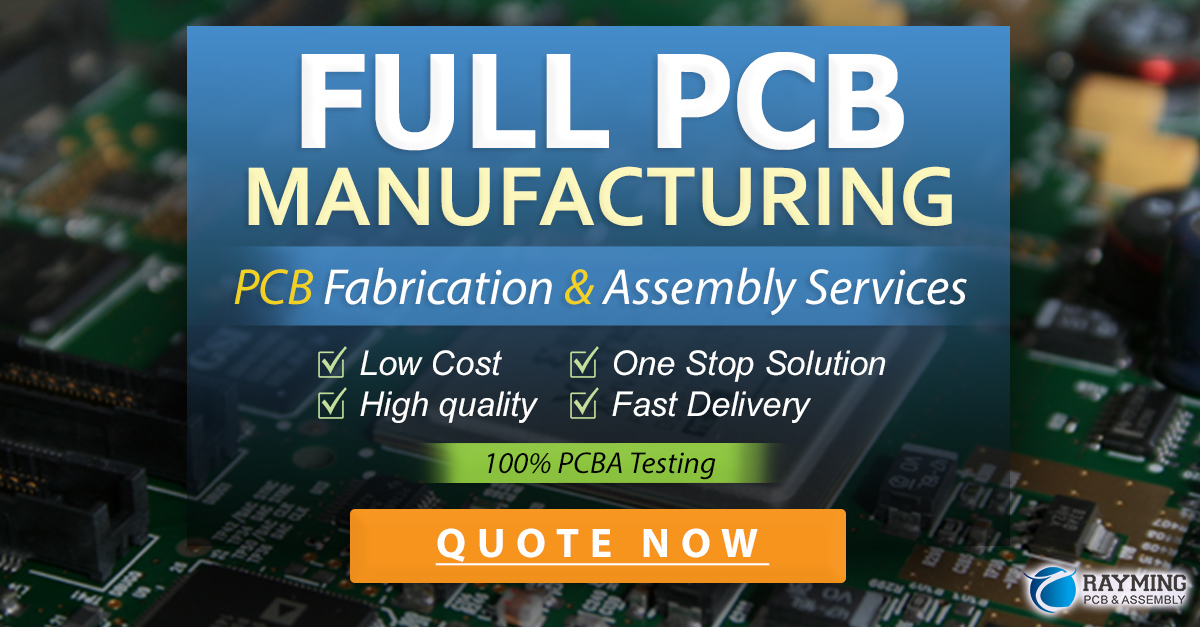
Types of Carbon Contacts
There are several types of carbon contacts available, each with its own unique properties and advantages. Some of the most common types include:
-
Silver-graphite contacts: These contacts consist of a silver matrix with graphite particles dispersed throughout. The silver provides excellent electrical conductivity, while the graphite improves the contact’s resistance to wear and arc erosion. Silver-graphite contacts are commonly used in applications with high current and frequent switching, such as in automotive electrical systems and industrial control systems.
-
Carbon-carbon contacts: These contacts are made entirely from carbon materials, such as graphite or carbon-carbon composites. They offer the highest resistance to arc erosion and are suitable for use in applications with extremely high temperatures, such as in aerospace and defense. However, they have lower electrical conductivity compared to silver-graphite contacts.
-
Carbon nanotube contacts: These contacts are based on carbon nanotubes, which are cylindrical carbon molecules with exceptional electrical and mechanical properties. Carbon nanotube contacts offer the highest electrical conductivity and the lowest contact resistance among carbon contacts. They are also highly resistant to wear and arc erosion, making them suitable for use in demanding applications, such as in high-speed switching and high-frequency power electronics.
-
Metal-graphite contacts: These contacts consist of a metal matrix, such as copper or aluminum, with graphite particles dispersed throughout. They offer a balance of electrical conductivity and wear resistance, making them suitable for use in a wide range of applications, such as in low-voltage switchgear and motor controls.
Factors to Consider When Choosing Carbon Contacts
When selecting carbon contacts for a particular application, several factors should be considered to ensure optimal performance and reliability. These factors include:
-
Current-carrying capacity: The current-carrying capacity of the contacts should be sufficient to handle the maximum expected current in the application. This is determined by the size and geometry of the contacts, as well as the properties of the carbon material used.
-
Contact resistance: The contact resistance should be as low as possible to minimize power losses and heat generation. This is particularly important in applications with high currents or frequent switching.
-
Switching frequency: The switching frequency of the application should be considered when selecting carbon contacts. Some types of contacts, such as silver-graphite, are better suited for applications with high switching frequencies, while others, such as carbon-carbon, may be more suitable for applications with lower switching frequencies.
-
Environmental conditions: The environmental conditions in which the contacts will be used should be taken into account. Factors such as temperature, humidity, and the presence of contaminants can affect the performance and reliability of the contacts. Some types of carbon contacts, such as those based on carbon nanotubes, are more resistant to environmental factors than others.
-
Cost: The cost of the contacts should be considered in relation to their performance and expected service life. While some types of carbon contacts, such as those based on carbon nanotubes, may have a higher initial cost, their superior performance and longer service life can make them a more cost-effective choice in the long run.
Maintenance and Replacement of Carbon Contacts
To ensure the reliable and efficient operation of systems using carbon contacts, regular maintenance and timely replacement of the contacts are essential. Some key considerations for the maintenance and replacement of carbon contacts include:
-
Regular inspection: Carbon contacts should be regularly inspected for signs of wear, damage, or contamination. This can be done through visual inspection or by measuring the contact resistance using specialized equipment. Any contacts that show signs of excessive wear or damage should be replaced promptly to prevent system failures or performance degradation.
-
Cleaning and lubrication: In some cases, carbon contacts may become contaminated with dirt, dust, or other debris, which can increase contact resistance and lead to overheating or arcing. Regular cleaning of the contacts using approved solvents or methods can help to maintain their performance. In some applications, the use of lubricants specifically designed for electrical contacts can also help to reduce friction and wear.
-
Replacement intervals: The replacement interval for carbon contacts will depend on various factors, such as the application, the switching frequency, and the environmental conditions. Manufacturers typically provide guidelines for the expected service life of their contacts under different operating conditions. It is important to follow these guidelines and replace the contacts as recommended to ensure optimal system performance and reliability.
-
Proper installation: When replacing carbon contacts, it is crucial to ensure that they are installed correctly and securely. Improper installation can lead to poor contact, increased resistance, and premature failure. It is recommended to follow the manufacturer’s installation instructions and to use the specified torque values when tightening the contacts.
Future Developments in Carbon Contact Technology
As technology continues to advance, new developments in carbon contact technology are expected to emerge. Some of the areas where future developments may occur include:
-
Improved carbon materials: Researchers are continually working on developing new carbon materials with enhanced electrical and mechanical properties. For example, the use of graphene, a single layer of carbon atoms arranged in a hexagonal lattice, has shown promise in creating contacts with extremely high electrical conductivity and mechanical strength.
-
Nanostructured contacts: The incorporation of nanostructures, such as carbon nanotubes or metal nanoparticles, into carbon contacts can lead to improved performance. These nanostructures can enhance the electrical conductivity, thermal conductivity, and mechanical properties of the contacts, enabling their use in even more demanding applications.
-
Self-lubricating contacts: The development of self-lubricating carbon contacts, which contain solid lubricants such as molybdenum disulfide or graphite, can help to reduce friction and wear even further. These contacts would require less frequent maintenance and replacement, leading to reduced system downtime and maintenance costs.
-
Smart contacts: The integration of sensors and monitoring systems into carbon contacts could enable real-time monitoring of contact performance and condition. This would allow for predictive maintenance, where contacts are replaced before they fail, based on data from the monitoring system. Smart contacts could also provide valuable data for optimizing system performance and efficiency.
Frequently Asked Questions (FAQ)
-
Q: What are the main advantages of carbon contacts over other contact materials?
A: Carbon contacts offer several advantages, including high electrical conductivity, low contact resistance, high wear resistance, arc erosion resistance, temperature stability, and cost-effectiveness. -
Q: In what industries are carbon contacts commonly used?
A: Carbon contacts are used in various industries, such as automotive, industrial control systems, power distribution, aerospace and defense, and renewable energy. -
Q: What are the different types of carbon contacts available?
A: The main types of carbon contacts include silver-graphite contacts, carbon-carbon contacts, carbon nanotube contacts, and metal-graphite contacts. -
Q: How often should carbon contacts be replaced?
A: The replacement interval for carbon contacts depends on factors such as the application, switching frequency, and environmental conditions. It is important to follow the manufacturer’s guidelines and replace the contacts as recommended. -
Q: What future developments can be expected in carbon contact technology?
A: Future developments in carbon contact technology may include improved carbon materials, nanostructured contacts, self-lubricating contacts, and smart contacts with integrated sensors and monitoring systems.
Conclusion
Carbon contacts are a critical component in a wide range of electrical and electronic systems, offering superior performance and reliability compared to other contact materials. Their high electrical conductivity, low contact resistance, wear resistance, and arc erosion resistance make them an ideal choice for applications in industries such as automotive, industrial control, power distribution, aerospace, and renewable energy.
As technology continues to advance, new developments in carbon contact technology are expected to emerge, leading to even better performance and new possibilities for their use. By understanding the properties, advantages, and applications of carbon contacts, engineers and system designers can make informed decisions when selecting contact materials for their projects, ensuring optimal system performance and reliability.
Leave a Reply