What is Wave Soldering?
Wave soldering is a process that involves passing a PCB over a molten solder wave to create electrical connections between the components and the board. The process begins with applying flux to the bottom side of the PCB, which helps to remove oxides and improve solder wettability. The board is then placed on a conveyor belt that moves it over a preheating zone to gradually raise the temperature of the components and the board, preventing thermal shock.
As the PCB moves further along the conveyor, it passes over a molten solder wave. The solder adheres to the exposed metal surfaces, creating a strong electrical and mechanical bond between the components and the PCB. After the soldering process, the board undergoes a cleaning process to remove any excess flux or solder residue.
Advantages of Wave Soldering
-
Suitable for through-hole components: Wave soldering is an excellent choice for PCBs with through-hole components, as the solder can easily flow through the holes and create a strong connection.
-
High production speed: Wave soldering is a fast process, making it suitable for high-volume production runs. The conveyor system allows for continuous processing of boards, reducing the overall assembly time.
-
Cost-effective for large batches: Due to its high production speed, wave soldering is more cost-effective for large production runs compared to other methods.
Disadvantages of Wave Soldering
-
Limited compatibility with surface mount components: Wave soldering is not ideal for boards with a high number of surface mount components, as the solder wave may cause bridging or displacement of smaller components.
-
Thermal stress on components: The high temperature of the molten solder wave can cause thermal stress on sensitive components, potentially leading to damage or reduced lifespan.
-
Difficulty in controlling solder joint quality: Factors such as conveyor speed, solder temperature, and flux application can affect the quality of the solder joints, making it challenging to maintain consistent results.
What is Reflow Soldering?
Reflow soldering is a process that involves applying solder paste to the PCB pads, placing the components, and then heating the entire assembly in a reflow oven to melt the solder and create a bond between the components and the board. The solder paste consists of tiny solder spheres suspended in a flux medium, which helps to remove oxides and improve solder wettability.
The reflow soldering process begins with printing the solder paste onto the PCB pads using a stencil. The components are then placed on the pads, either manually or using an automated pick-and-place machine. The assembled board is then passed through a reflow oven, which heats the board according to a predefined temperature profile. The heat melts the solder paste, creating a strong electrical and mechanical bond between the components and the PCB.
Advantages of Reflow Soldering
-
Ideal for surface mount components: Reflow soldering is the preferred method for assembling PCBs with surface mount components, as it allows for precise control over the solder paste application and component placement.
-
Consistent solder joint quality: The controlled heating profile in a reflow oven ensures consistent solder joint quality across the entire board, reducing the risk of defects or failures.
-
Automation-friendly: Reflow soldering is highly compatible with automated assembly processes, such as pick-and-place machines and conveyor systems, making it suitable for high-volume production.
Disadvantages of Reflow Soldering
-
Limited compatibility with through-hole components: Reflow soldering is not suitable for boards with a high number of through-hole components, as the solder paste may not flow properly through the holes.
-
Higher initial investment: Setting up a reflow soldering process requires a higher initial investment in equipment, such as stencil printers, pick-and-place machines, and reflow ovens.
-
Sensitivity to solder paste quality: The performance of reflow soldering heavily depends on the quality and consistency of the solder paste. Improper storage, handling, or application of the solder paste can lead to defects or inconsistencies in the solder joints.
Comparing Wave Soldering and Reflow Soldering
Factor | Wave Soldering | Reflow Soldering |
---|---|---|
Component Compatibility | Ideal for through-hole components | Ideal for surface mount components |
Production Speed | High, suitable for large batches | Moderate, automation-friendly |
Solder Joint Quality | Can be inconsistent | Consistent and controlled |
Thermal Stress on Components | Higher risk of thermal stress | Lower risk of thermal stress |
Initial Investment | Lower | Higher |
Flexibility in PCB Design | Limited by solder wave access | High, allows for dense component placement |
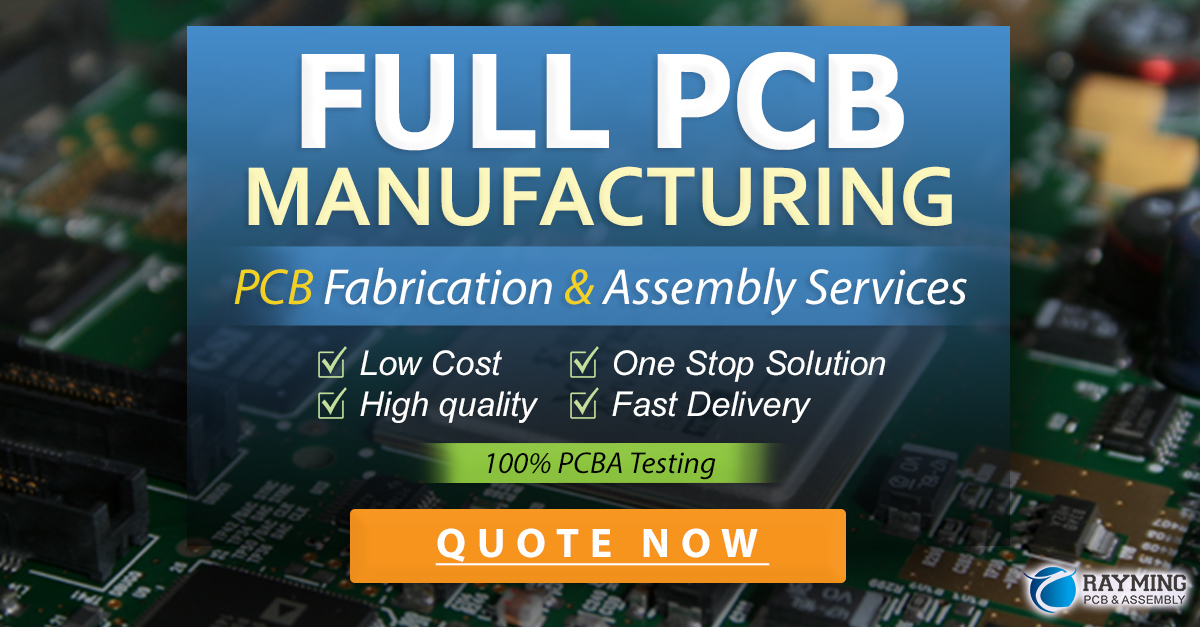
Choosing the Right Soldering Method
When deciding between wave soldering and reflow soldering for your PCB assembly, consider the following factors:
-
Component types: If your PCB primarily consists of through-hole components, wave soldering may be the better choice. For boards with mostly surface mount components, reflow soldering is the preferred method.
-
Production volume: Wave soldering is more cost-effective for large production runs, while reflow soldering is suitable for both small and large batches, especially when automated assembly processes are used.
-
PCB design complexity: Reflow soldering allows for more complex and dense PCB designs, as it can accommodate smaller components and tighter spacing. Wave soldering may limit the design flexibility due to the need for solder wave access.
-
Quality requirements: If consistent solder joint quality is a top priority, reflow soldering offers better control and repeatability compared to wave soldering.
-
Budget and resources: Consider your initial investment budget and the available resources when choosing between wave soldering and reflow soldering. Reflow soldering may require a higher upfront cost but can offer long-term benefits in terms of quality and automation.
Frequently Asked Questions (FAQ)
-
Can wave soldering and reflow soldering be used together on the same PCB?
Yes, it is possible to use both wave soldering and reflow soldering on the same PCB, especially when the board contains a mix of through-hole and surface mount components. In such cases, the surface mount components are typically reflow soldered first, followed by wave soldering for the through-hole components. -
What is selective soldering, and how does it differ from wave soldering?
Selective soldering is a process that uses a localized solder wave or iron to solder specific areas on a PCB. It differs from wave soldering in that it targets only the desired components or locations, rather than exposing the entire board to the solder wave. Selective soldering is useful for boards with a mix of through-hole and surface mount components, or when certain components are heat-sensitive and require special attention. -
How does the solder paste quality affect the reflow soldering process?
Solder paste quality is crucial for successful reflow soldering. The solder paste must have the correct composition, particle size, and viscosity to ensure proper solder joint formation. Poor quality solder paste can lead to issues such as solder balling, bridging, or insufficient solder coverage. It is essential to use high-quality solder paste from reputable suppliers and to store and handle the paste according to the manufacturer’s guidelines to maintain its performance. -
What are some common defects encountered in wave soldering, and how can they be prevented?
Common defects in wave soldering include bridging (solder shorts between adjacent pins), insufficient solder coverage, and solder flags (excess solder on component leads). These defects can be prevented by optimizing the wave soldering parameters, such as conveyor speed, solder temperature, and flux application. Proper PCB design, such as adequate pad spacing and solder mask application, can also help minimize the occurrence of these defects. -
How does the reflow temperature profile affect the solder joint quality in reflow soldering?
The reflow temperature profile is a critical factor in determining the solder joint quality in reflow soldering. The profile must be carefully designed to ensure that the solder paste reaches the correct peak temperature for the appropriate duration to allow for proper solder melting and wetting. An incorrect temperature profile can lead to issues such as cold solder joints, solder balling, or component damage. It is important to follow the solder paste manufacturer’s recommended temperature profile and to fine-tune the profile based on the specific PCB design and components used.
Conclusion
Wave soldering and reflow soldering are two essential methods for PCB assembly, each with its own advantages and disadvantages. Wave soldering is ideal for through-hole components and large production runs, while reflow soldering is the preferred choice for surface mount components and offers better control over solder joint quality.
When deciding between wave soldering and reflow soldering, consider factors such as component types, production volume, PCB design complexity, quality requirements, and available budget and resources. In some cases, a combination of both methods may be necessary to achieve the best results.
By understanding the differences between wave soldering and reflow soldering and carefully evaluating your specific PCB assembly needs, you can choose the most suitable method to ensure reliable and efficient production of your electronic devices.
Leave a Reply