What is Wave Soldering?
Wave soldering is a soldering process that involves passing a PCB over a molten solder wave to create electrical connections between the components and the board. The process follows these steps:
-
PCB Preparation: The PCB is designed with through-hole components and solder pads. A solder mask is applied to the board to prevent solder from adhering to unwanted areas.
-
Flux Application: A thin layer of flux is applied to the bottom side of the PCB to help the molten solder flow and adhere to the component leads and solder pads.
-
Preheating: The PCB is preheated to activate the flux and prevent thermal shock when it comes into contact with the molten solder wave.
-
Wave Soldering: The PCB is passed over a molten solder wave, which is typically a mixture of tin, lead, and other alloys. The solder adheres to the exposed metal surfaces, creating electrical connections between the components and the PCB.
-
Cooling and Cleaning: After wave soldering, the PCB is cooled, and any excess flux or solder is cleaned off the board.
Advantages of Wave Soldering
- Suitable for high-volume production
- Ideal for through-hole components
- Faster than manual soldering
- Consistent solder joints
- Cost-effective for large batches
Disadvantages of Wave Soldering
- Limited to through-hole components
- Not suitable for surface mount devices (SMDs)
- Requires more setup time and equipment maintenance
- May cause thermal stress on components
- Difficult to control solder joint quality for complex PCBs
What is Reflow Soldering?
Reflow soldering is a process that involves applying solder paste to the PCB pads, placing components onto the paste, and then heating the entire assembly in a reflow oven to melt the solder and create electrical connections. The process follows these steps:
-
PCB Preparation: The PCB is designed with surface mount pads and a solder mask.
-
Solder Paste Application: Solder paste, a mixture of tiny solder spheres and flux, is applied to the PCB pads using a stencil or solder paste printer.
-
Component Placement: Surface mount components are placed onto the solder paste using a pick-and-place machine or by hand.
-
Reflow Soldering: The PCB assembly is passed through a reflow oven, which heats the board according to a specific temperature profile. The solder paste melts, creating electrical and mechanical connections between the components and the PCB pads.
-
Cooling and Inspection: The PCB is cooled, and the solder joints are inspected for quality and defects.
Advantages of Reflow Soldering
- Ideal for surface mount devices (SMDs)
- Suitable for high-density PCB layouts
- Faster than wave soldering for SMD-dominant boards
- More precise component placement
- Better control over solder joint quality
- Fewer thermal stresses on components
Disadvantages of Reflow Soldering
- Not suitable for through-hole components
- Requires specialized equipment (reflow oven, pick-and-place machine)
- Higher initial setup costs
- Solder paste has a limited shelf life
- Requires careful temperature profile management
Comparing Wave Soldering and Reflow Soldering
To better understand the differences between wave soldering and reflow soldering, let’s compare them side-by-side:
Aspect | Wave Soldering | Reflow Soldering |
---|---|---|
Component Types | Through-hole components | Surface mount devices (SMDs) |
PCB Layout | Simpler, less dense | High-density, complex |
Process Speed | Faster for through-hole dominant PCBs | Faster for SMD-dominant PCBs |
Equipment Required | Wave soldering machine, fluxer | Reflow oven, pick-and-place machine, stencil |
Solder Application | Molten solder wave | Solder paste |
Thermal Stress | Higher, due to direct solder contact | Lower, due to controlled heating |
Solder Joint Quality | Consistent, but harder to control | More precise and controllable |
Cost-effectiveness | Better for high-volume through-hole | Better for high-volume SMD |
Flexibility | Limited to through-hole components | Accommodates a wide range of SMDs |
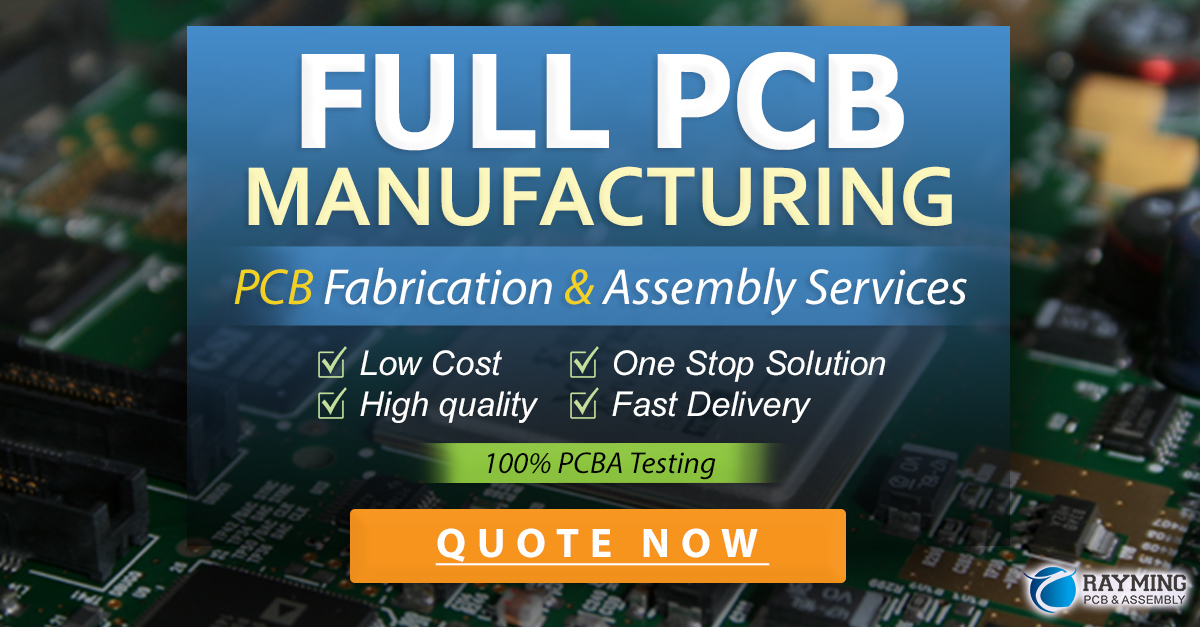
Choosing Between Wave Soldering and Reflow Soldering
When deciding between wave soldering and reflow soldering for your PCB assembly project, consider the following factors:
-
Component Types: If your PCB primarily uses through-hole components, wave soldering is the better choice. If your PCB is dominated by surface mount devices, reflow soldering is the way to go.
-
PCB Layout: Wave soldering is more suitable for simpler, less dense PCB layouts, while reflow soldering can accommodate high-density, complex designs.
-
Production Volume: Both methods are suitable for high-volume production, but wave soldering is more cost-effective for large batches of through-hole dominant PCBs, while reflow soldering is more efficient for SMD-dominant boards.
-
Available Equipment: Consider the equipment you have access to or are willing to invest in. Wave soldering requires a wave soldering machine and a fluxer, while reflow soldering needs a reflow oven, pick-and-place machine, and solder paste stencil.
-
Solder Joint Quality: Reflow soldering offers better control over solder joint quality and is more precise, while wave soldering provides consistent joints but may be harder to control for complex PCBs.
-
Mixed Technology PCBs: If your PCB contains both through-hole and surface mount components, you may need to use a combination of wave soldering and reflow soldering techniques, such as selective soldering or pin-in-paste reflow soldering.
FAQ
-
Q: Can wave soldering be used for surface mount devices (SMDs)?
A: Wave soldering is not suitable for most SMDs, as the molten solder wave can cause the components to dislodge or short-circuit. However, some special SMDs, such as bottom-terminated components, can be wave soldered with proper precautions. -
Q: Is reflow soldering compatible with through-hole components?
A: Reflow soldering is not ideal for through-hole components, as the solder paste may not flow adequately into the component holes, resulting in weak or incomplete solder joints. However, a technique called pin-in-paste reflow soldering can be used for certain through-hole components in combination with SMDs. -
Q: What is selective soldering, and when is it used?
A: Selective soldering is a specialized soldering process that combines aspects of wave soldering and reflow soldering. It is used for mixed technology PCBs that contain both through-hole and surface mount components. Selective soldering machines apply solder to specific areas of the PCB, allowing for precise control over the soldering process. -
Q: How does the cost of wave soldering compare to reflow soldering?
A: The cost comparison between wave soldering and reflow soldering depends on various factors, such as the PCB design, component types, and production volume. Generally, wave soldering has lower initial setup costs but may be more expensive for SMD-dominant boards. Reflow soldering has higher initial equipment costs but can be more cost-effective for high-volume SMD assembly. -
Q: Can reflow soldering be done without a pick-and-place machine?
A: Yes, reflow soldering can be done manually without a pick-and-place machine, especially for low-volume or prototype PCBs. In this case, solder paste is applied using a stencil or dispensed manually, and components are placed by hand. However, for high-volume production and consistent results, a pick-and-place machine is highly recommended.
Conclusion
Wave soldering and reflow soldering are two essential techniques used in the electronics manufacturing industry for creating reliable electrical connections between components and PCBs. While wave soldering is ideal for through-hole components and simpler PCB layouts, reflow soldering is the preferred method for surface mount devices and high-density designs.
When choosing between wave soldering and reflow soldering, consider factors such as component types, PCB layout, production volume, available equipment, and desired solder joint quality. In some cases, a combination of both techniques may be necessary for mixed technology PCBs.
By understanding the differences, advantages, and disadvantages of wave soldering and reflow soldering, you can make an informed decision on which method is best suited for your PCB assembly needs, ensuring a reliable and cost-effective manufacturing process.
Leave a Reply