What is Front-End Data Optimization?
Front-end data optimization refers to the process of refining and optimizing the design data and manufacturing files used in PCB Assembly. This includes various aspects such as component placement, routing, design rule checks (DRC), and generating accurate manufacturing files like Gerber files, drill files, and bill of materials (BOM).
The primary goal of front-end data optimization is to ensure that the design data is accurate, complete, and compliant with the manufacturing capabilities and requirements. By optimizing the data upfront, manufacturers can minimize the chances of errors, delays, and rework during the assembly process.
Key Elements of Front-End Data Optimization
-
Design Rule Checks (DRC): DRC is a process of verifying the PCB design against a set of predefined rules and constraints. These rules ensure that the design meets the manufacturing capabilities and standards, such as minimum trace widths, clearances, and hole sizes. Running comprehensive DRC helps identify and resolve design issues early in the process, reducing the risk of manufacturing defects.
-
Component Placement Optimization: Component placement plays a significant role in the manufacturing efficiency and product quality. Front-end data optimization involves optimizing the component placement to minimize the assembly time, reduce the risk of defects, and improve the overall manufacturability. This includes considering factors such as component orientation, spacing, and thermal management.
-
Routing Optimization: Routing is the process of connecting the components on the PCB using conductive traces. Optimizing the routing is crucial for ensuring signal integrity, minimizing crosstalk, and reducing electromagnetic interference (EMI). Front-end data optimization techniques, such as using appropriate trace widths, lengths, and spacing, can significantly improve the routing quality and manufacturability.
-
Manufacturing File Generation: Once the PCB design is optimized, it is essential to generate accurate manufacturing files. These files include Gerber files (for the PCB layers), drill files (for the holes), and the bill of materials (BOM). Front-end data optimization ensures that these files are complete, accurate, and compliant with the manufacturing requirements. This reduces the chances of misinterpretation and errors during the assembly process.
Benefits of Front-End Data Optimization
Implementing front-end data optimization in PCB assembly offers several significant benefits, including:
-
Reduced Manufacturing Defects: By optimizing the design data and resolving issues upfront, manufacturers can minimize the occurrence of manufacturing defects. This leads to higher yield rates, lower rework costs, and improved product quality.
-
Faster Time-to-Market: Front-end data optimization streamlines the manufacturing process by reducing the need for design revisions and rework. This results in faster production cycles and shorter time-to-market for the final product.
-
Cost Savings: Optimizing the design data helps reduce material waste, minimize assembly time, and lower the chances of scrap and rework. This translates to significant cost savings for the manufacturer and the end customer.
-
Improved Product Reliability: By ensuring the design data is accurate and compliant with manufacturing standards, front-end data optimization contributes to the overall reliability and performance of the final product. This is particularly important for mission-critical applications where product failures can have severe consequences.
-
Enhanced Communication and Collaboration: Front-end data optimization promotes better communication and collaboration between the design and manufacturing teams. By establishing clear guidelines and standards for design data, both teams can work together more effectively to achieve the desired manufacturing outcomes.
Best Practices for Front-End Data Optimization
To effectively implement front-end data optimization in PCB assembly, consider the following best practices:
-
Establish Design Guidelines: Develop and maintain a set of comprehensive design guidelines that outline the manufacturing capabilities, constraints, and best practices. These guidelines should cover aspects such as component selection, placement, routing, and manufacturing file requirements.
-
Use Automated Design Rule Checks: Implement automated DRC tools to verify the design data against the established guidelines. These tools can quickly identify and flag potential issues, allowing designers to make necessary corrections early in the process.
-
Collaborate with Manufacturing Partners: Engage with your manufacturing partners early in the design process. Share your design data and seek their feedback on manufacturability, assembly requirements, and potential optimization opportunities. This collaboration can help identify and address issues before they impact the production process.
-
Invest in Training and Education: Provide training and education to your design and manufacturing teams on the importance of front-end data optimization and best practices. This ensures that everyone involved in the process understands the critical role they play in achieving optimal manufacturing outcomes.
-
Continuously Monitor and Improve: Establish metrics and key performance indicators (KPIs) to monitor the effectiveness of your front-end data optimization efforts. Regularly review and analyze these metrics to identify areas for improvement and implement necessary changes to enhance the overall process.
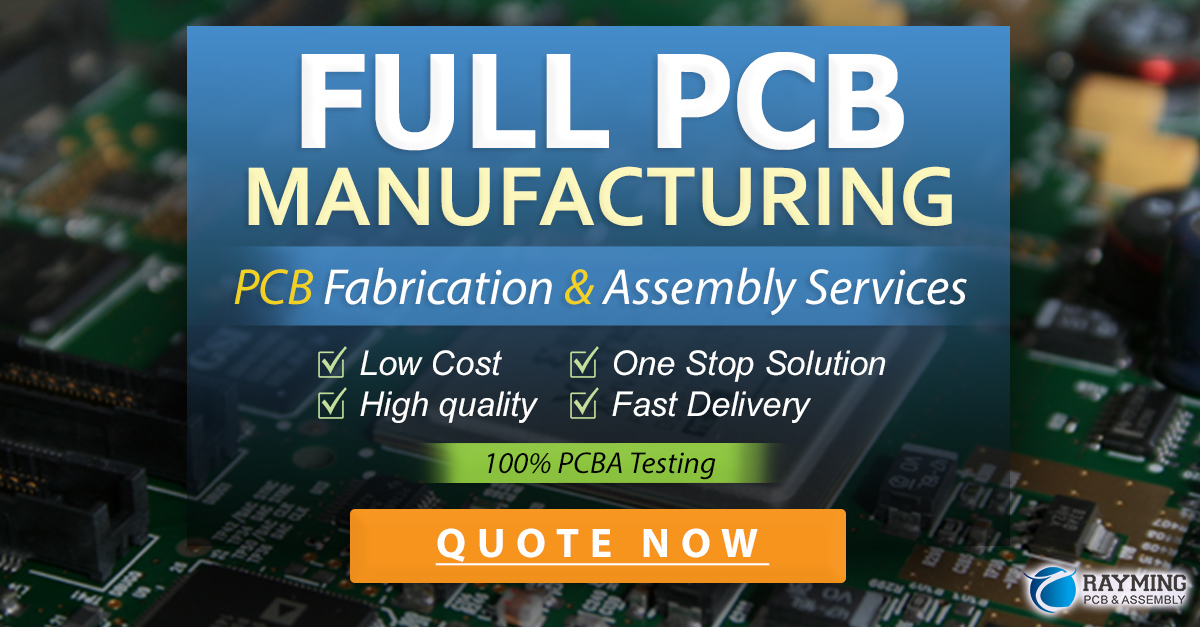
FAQs
-
What is the difference between front-end data optimization and back-end optimization in PCB assembly?
Front-end data optimization focuses on optimizing the design data and manufacturing files before the actual assembly process begins. It involves tasks such as design rule checks, component placement optimization, and generating accurate manufacturing files. On the other hand, back-end optimization deals with optimizing the actual assembly process, including machine setup, process control, and quality inspection. -
How does front-end data optimization impact the cost of PCB assembly?
Front-end data optimization can significantly reduce the cost of PCB assembly by minimizing the chances of defects, rework, and scrap. By ensuring the design data is accurate and optimized for manufacturability, manufacturers can reduce material waste, assembly time, and the need for costly rework. This translates to lower production costs and improved profitability. -
What are the key challenges in implementing front-end data optimization?
Some of the key challenges in implementing front-end data optimization include: - Lack of standardized design guidelines and best practices
- Insufficient collaboration between design and manufacturing teams
- Limited resources and expertise in data optimization techniques
- Resistance to change and adopting new processes and tools
-
Balancing optimization efforts with time-to-market pressures
-
How can manufacturers measure the effectiveness of their front-end data optimization efforts?
Manufacturers can measure the effectiveness of their front-end data optimization efforts by tracking various metrics and KPIs, such as: - First-pass yield rates
- Defect rates and rework costs
- Cycle time and time-to-market
- Material utilization and waste reduction
-
Customer satisfaction and product quality feedback
-
What role does automation play in front-end data optimization?
Automation plays a crucial role in front-end data optimization by streamlining and accelerating various tasks. Automated design rule checks, component placement algorithms, and manufacturing file generation tools can significantly reduce the time and effort required for data optimization. Automation also helps minimize human errors and ensures consistency in the optimization process.
Conclusion
Front-end data optimization is a critical aspect of PCB assembly that directly impacts the quality, reliability, and cost-effectiveness of the final product. By optimizing the design data and manufacturing files upfront, manufacturers can minimize defects, reduce production time, and achieve significant cost savings.
To successfully implement front-end data optimization, it is essential to establish clear design guidelines, collaborate with manufacturing partners, invest in training and education, and continuously monitor and improve the process. By adopting best practices and leveraging automation tools, manufacturers can streamline their front-end data optimization efforts and gain a competitive edge in the market.
As the electronics industry continues to evolve and demand for high-quality, cost-effective PCBs grows, front-end data optimization will remain a key focus area for manufacturers. By prioritizing this critical aspect of PCB assembly, companies can deliver superior products, enhance customer satisfaction, and drive long-term success in the dynamic world of electronics manufacturing.
PCB Assembly Stage | Key Elements |
---|---|
Design Rule Checks (DRC) | – Verifying design against manufacturing constraints – Identifying and resolving design issues early |
Component Placement Optimization | – Minimizing assembly time and defects – Considering component orientation, spacing, and thermal management |
Routing Optimization | – Ensuring signal integrity and minimizing crosstalk – Using appropriate trace widths, lengths, and spacing |
Manufacturing File Generation | – Generating accurate Gerber files, drill files, and BOM – Ensuring compliance with manufacturing requirements |
Leave a Reply