Introduction to Treadmill Motor Controllers
A treadmill motor controller is an electronic device that regulates the speed and operation of the electric motor powering a treadmill. The motor controller circuitry ensures smooth acceleration and deceleration, maintains a constant speed under varying loads, and often includes safety features like automatic shut-off.
Understanding the circuit diagram of a treadmill motor controller can be valuable for treadmill owners, fitness equipment technicians, and electronics hobbyists. This guide aims to provide a comprehensive overview of treadmill motor controller circuit diagrams, their components, and their functioning.
Key Components of a Treadmill Motor Controller Circuit
The main components of a typical treadmill motor controller circuit include:
- Microcontroller or control circuitry
- Power supply
- Speed control potentiometer
- MOSFET or IGBT power transistors
- Driver IC for the power transistors
- Current sensing resistors
- Protection components (fuses, diodes, etc.)
- User interface elements (display, buttons, etc.)
Let’s take a closer look at each of these components and their roles in the motor controller circuit.
Microcontroller or Control Circuitry
The “brain” of the treadmill motor controller is either a dedicated microcontroller or a custom-designed control circuit. This component receives input from the user interface, reads sensors, and controls the power delivery to the motor.
In microcontroller-based designs, the firmware (embedded software) determines the controller’s functionality and features. Some common microcontrollers used in treadmill controllers include:
Microcontroller | Description |
---|---|
Arduino | Open-source, easy to program, suitable for DIY projects |
PIC | Versatile, wide range of models, popular in commercial products |
STM32 | High-performance, ARM Cortex-M based, feature-rich |
Custom control circuits, on the other hand, are designed specifically for the treadmill and often include dedicated ICs for functions like speed control and motor driving.
Power Supply
The power supply in a treadmill motor controller converts the AC mains voltage to the DC voltages required by the controller components and the motor. The power supply typically includes:
- Transformer for stepping down the AC voltage
- Rectifier bridge for converting AC to DC
- Filter capacitors for smoothing the DC voltage
- Voltage regulators for providing stable, lower DC voltages
The specific voltages required depend on the motor specifications and the controller design. Common DC voltages in treadmill controllers include:
Voltage | Purpose |
---|---|
12V | Powering control circuitry and user interface |
24V | Powering the motor in some lower-power treadmills |
90V | Powering the motor in high-power treadmills |
Speed Control Potentiometer
The speed control potentiometer allows the user to adjust the treadmill’s speed. It is typically connected to the microcontroller or control circuitry, which reads the potentiometer’s position and adjusts the motor speed accordingly.
The potentiometer is often mounted on the treadmill’s console, easily accessible to the user. Some treadmills may use digital controls instead, in which case the speed setting is communicated to the controller through a digital interface.
MOSFET or IGBT Power Transistors
The power transistors are responsible for switching the high current required by the motor. MOSFETs (Metal-Oxide-Semiconductor Field-Effect Transistors) and IGBTs (Insulated-Gate Bipolar Transistors) are the most common types used in treadmill motor controllers.
These transistors are controlled by the microcontroller or control circuitry, which rapidly switches them on and off to regulate the power delivered to the motor. The switching frequency and duty cycle determine the motor’s speed and torque.
The power transistors must be chosen based on the motor’s voltage and current requirements. Key specifications to consider include:
Specification | Description |
---|---|
Voltage rating | Must exceed the motor’s operating voltage |
Current rating | Must handle the motor’s peak current draw |
Power dissipation | Determines the transistor’s ability to dissipate heat |
Switching speed | Affects the controller’s efficiency and smoothness |
Driver IC for Power Transistors
The driver IC acts as an interface between the low-power control circuitry and the high-power transistors. It amplifies the control signals and ensures that the transistors are switched efficiently and reliably.
Common driver ICs used in treadmill motor controllers include:
Driver IC | Description |
---|---|
IR2110 | High-voltage, high-speed MOSFET/IGBT driver |
IR2183 | Half-bridge driver with built-in protection features |
MCP1404 | High-speed, dual-output MOSFET driver |
The choice of driver IC depends on the specific requirements of the motor controller, such as the switching frequency, voltage levels, and protection features needed.
Current Sensing Resistors
Current sensing resistors are used to measure the current flowing through the motor. This information is used by the controller for various purposes, including:
- Overcurrent protection: Shutting down the motor if the current exceeds a safe threshold
- Closed-loop speed control: Adjusting the motor speed based on the load to maintain a constant speed
- Torque limiting: Restricting the motor’s torque to prevent damage or ensure user safety
The current sensing resistors are typically low-value, high-power resistors placed in series with the motor. The voltage drop across the resistor is proportional to the current and can be measured by the controller using an analog-to-digital converter (ADC).
Protection Components
Treadmill motor controllers include various protection components to ensure safe and reliable operation. Some common protection features are:
-
Fuses: Protect against overcurrent conditions by interrupting the circuit if the current exceeds a specified limit.
-
Diodes: Suppress voltage spikes caused by the motor’s inductive load and protect the power transistors from reverse currents.
-
Optoisolators: Provide electrical isolation between the low-voltage control circuitry and the high-voltage power stage, enhancing safety and noise immunity.
-
Thermal sensors: Monitor the temperature of critical components, such as the power transistors and motor, and trigger a shutdown if the temperature exceeds safe limits.
These protection components are essential for preventing damage to the controller, motor, and the treadmill itself, as well as ensuring user safety.
User Interface Elements
The user interface of a treadmill motor controller typically includes:
-
Display: Shows information like speed, distance, time, and calories burned. May be a simple LED or LCD display or a more advanced touchscreen.
-
Buttons: Allow the user to start, stop, and adjust the treadmill’s settings. May include preset speed buttons and an emergency stop button.
-
Speed control: Either a potentiometer or digital controls for adjusting the treadmill’s speed.
-
Heart rate sensors: Some treadmills include handheld or chest strap heart rate sensors that communicate with the controller to display the user’s heart rate and adjust the workout intensity.
The user interface elements are connected to the microcontroller or control circuitry, which processes the user input and updates the display accordingly.
How a Treadmill Motor Controller Circuit Works
Now that we’ve covered the key components of a treadmill motor controller circuit, let’s look at how they work together to control the treadmill’s operation.
-
User input: The user sets the desired speed using the speed control potentiometer or digital controls and starts the treadmill using the start button.
-
Control circuitry: The microcontroller or control circuitry reads the user input and determines the appropriate motor speed and direction.
-
Power stage: The control circuitry sends signals to the driver IC, which switches the power transistors on and off rapidly to regulate the power delivered to the motor. The switching frequency and duty cycle determine the motor’s speed and torque.
-
Current sensing: The current sensing resistors provide feedback to the controller about the motor’s current draw. The controller uses this information for closed-loop speed control, overcurrent protection, and torque limiting.
-
Protection: The various protection components, such as fuses, diodes, and thermal sensors, continuously monitor the system for potential faults and take action to prevent damage or ensure user safety.
-
User feedback: The controller updates the display with relevant information, such as speed, distance, and calories burned, based on the motor’s performance and user input.
This process continues in real-time, with the controller constantly adjusting the motor’s speed and monitoring the system for faults or user input changes.
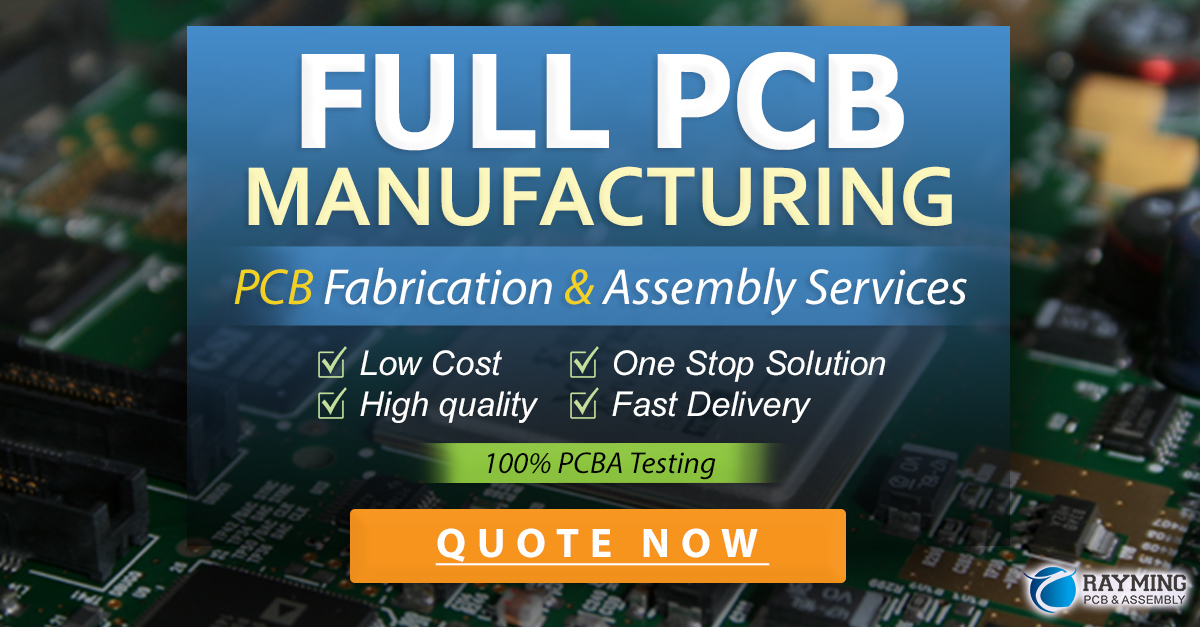
Treadmill Motor Controller Circuit Diagrams
Now, let’s look at some typical treadmill motor controller circuit diagrams to better understand how the components are interconnected.
Basic DC Motor Controller Circuit
This simple circuit demonstrates the core components of a DC motor controller:
+12V
|
|
+-+
| |
| | MOSFET
| | IRF540
+-+
|
|
+-----+
| |
| |
PWM Signal | | Motor
from MCU | |
-----------+ +-----+
| | |
+-+ +-+ +-+
| | | | | |
| | | | | |
+-+ +-+ +-+
| | |
GND GND GND
In this circuit, a microcontroller (MCU) generates a pulse-width modulated (PWM) signal that controls the MOSFET, which in turn regulates the power delivered to the motor. The motor’s speed is determined by the PWM signal’s duty cycle.
Treadmill Motor Controller with Speed Control and Current Sensing
This more advanced circuit includes speed control and current sensing features:
+24V
|
+-+
| |
| | Fuse
| |
+-+
|
|
Speed Control +-+
Potentiometer | |
-------------+ | | MOSFET
| | | IRFP460
| | |
+--+-+
| |
| |
PWM Signal | | Motor
from MCU | |
-----------+ | +------+
| | | |
+-+ | | |
| | | | |
Current | | | | |
Sensing +-+ | | |
Resistor | | | |
+--+ +------+
| |
GND GND
In this circuit, the speed control potentiometer provides an analog input to the microcontroller, which adjusts the PWM signal accordingly. The current sensing resistor allows the microcontroller to monitor the motor’s current draw and implement protective features or closed-loop speed control.
Treadmill Motor Controller with Driver IC and Protection Features
This advanced circuit includes a driver IC for efficient switching of the power transistors and additional protection features:
+90V
|
+-+
| |
| | Fuse
| |
+-+
|
|
Speed Control +-+
Potentiometer | |
-------------+ | | IGBT
| | | IRGP50B60PD1
| | |
+--+-+
| |
| |
PWM Signal | | Motor
from MCU | |
-----------+ | +------+
| | | |
+-+ | | |
| | | | |
Current | | | | |
Sensing +-+ | | |
Resistor | | | |
+--+ +------+
| |
IR2183 +-+ +-+
Driver IC | | | |
-----------+| | | | Thermal
+-+ | | Sensor
| | |
| +-+
| |
GND GND
In this circuit, the IR2183 driver IC provides efficient and reliable driving of the high-power IGBT. The thermal sensor monitors the temperature of the power transistor and triggers a shutdown if the temperature exceeds a safe limit.
FAQ
-
What is the purpose of a treadmill motor controller?
A treadmill motor controller regulates the speed and operation of the electric motor powering a treadmill, ensuring smooth acceleration, deceleration, and maintaining a constant speed under varying loads. -
What are the main components of a treadmill motor controller circuit?
The main components include a microcontroller or control circuitry, power supply, speed control potentiometer, MOSFET or IGBT power transistors, driver IC, current sensing resistors, protection components, and user interface elements. -
How does a treadmill motor controller adjust the motor’s speed?
The controller adjusts the motor’s speed by rapidly switching the power transistors on and off using pulse-width modulation (PWM). The PWM signal’s duty cycle determines the power delivered to the motor and, consequently, its speed. -
What safety features are typically included in a treadmill motor controller?
Treadmill motor controllers often include safety features such as overcurrent protection (fuses), voltage spike suppression (diodes), electrical isolation (optoisolators), and thermal protection (thermal sensors) to prevent damage and ensure user safety. -
Can I build my own treadmill motor controller?
Building a treadmill motor controller requires knowledge of electronic circuits and safety considerations. While it is possible for experienced hobbyists to design and build a controller, it is generally recommended to use a commercially available controller for reliability and safety reasons.
Conclusion
Treadmill motor controllers play a crucial role in ensuring the smooth and safe operation of treadmills. By understanding the components and functioning of these controllers, treadmill owners and technicians can better troubleshoot and maintain their equipment, while electronics enthusiasts can gain insights into motor control techniques.
This guide has provided a comprehensive overview of treadmill motor controller circuit diagrams, including the key components, their roles, and how they work together to control the treadmill’s motor. The example circuit diagrams illustrate the progression from a basic DC motor controller to a more advanced treadmill motor controller with speed control, current sensing, and protection features.
When designing or working with treadmill motor controllers, it is essential to prioritize safety and reliability. Always ensure that the components are rated for the required voltages and currents, and include appropriate protection features to prevent damage and ensure user safety.
By following best practices and understanding the principles behind treadmill motor controller circuits, you can ensure that your treadmill operates smoothly and safely, providing an enjoyable and effective fitness experience.
Leave a Reply