Introduction to Through-Hole Technology
Through-hole technology has been a fundamental part of printed circuit board (PCB) design for decades. Despite the rise of surface mount technology (SMT), through-hole components and techniques remain relevant in modern PCB designs. This article explores the importance of through-hole technology, its advantages, and its applications in various industries.
What is Through-Hole Technology?
Through-hole technology involves the use of components with long leads that are inserted into drilled holes on a PCB and soldered to pads on the opposite side. This creates a strong mechanical and electrical connection between the component and the board.
Advantages of Through-Hole Technology
- Mechanical Strength
- Through-hole components provide superior mechanical strength compared to surface mount components.
-
The leads passing through the board and being soldered on the opposite side create a robust connection.
-
Reliability
- Through-hole connections are less susceptible to vibrations and thermal stress.
-
The strong mechanical bond ensures reliable electrical connections over time.
-
Ease of Manual Assembly
- Through-hole components are easier to handle and manually solder than surface mount components.
-
This makes through-hole technology suitable for prototyping and low-volume production.
-
Visual Inspection
- Through-hole solder joints are visible on both sides of the PCB.
- This allows for easier visual inspection and troubleshooting.
Through-Hole Relevance in Modern PCB Designs
Power Electronics
In power electronics applications, through-hole technology remains prevalent due to its ability to handle high currents and voltages. Power components such as transformers, inductors, and large capacitors often utilize through-hole mounting for better heat dissipation and mechanical stability.
Component | Current Rating | Voltage Rating |
---|---|---|
Transformer | 10A – 100A | 100V – 1000V |
Inductor | 5A – 50A | 50V – 500V |
Large Capacitor | 1A – 10A | 100V – 500V |
High-Reliability Applications
Through-hole technology is preferred in high-reliability applications where failure is not an option. Industries such as aerospace, military, and medical equipment rely on through-hole components for their proven reliability and resistance to harsh environments.
Industry | Reliability Requirements |
---|---|
Aerospace | Withstand vibrations, temperature extremes |
Military | Rugged, resistant to shock and moisture |
Medical | Long-term reliability, biocompatibility |
Prototyping and Low-Volume Production
Through-hole technology remains relevant in prototyping and low-volume production scenarios. The ease of manual assembly and the ability to make modifications on the fly make through-hole components a preferred choice for initial designs and small batches.
Mixing Through-Hole and Surface Mount
Modern PCB designs often combine through-hole and surface mount technologies to leverage the benefits of both. Critical components that require high reliability or power handling are implemented using through-hole, while smaller and less critical components are surface mounted to save space and reduce costs.
Through-Hole Component Selection and Design Considerations
Component Selection
When selecting through-hole components, designers should consider factors such as:
- Package Size
-
Choose component packages that fit the available board space and hole sizes.
-
Power Rating
-
Ensure that the chosen components can handle the required power dissipation.
-
Availability
- Consider the availability and sourcing of through-hole components, especially for long-term production.
Design Considerations
Designers should keep the following considerations in mind when incorporating through-hole components in their PCB designs:
- Hole Size and Pad Diameter
- Ensure that the drilled holes and pad diameters are appropriate for the component leads.
-
Follow the manufacturer’s recommendations for hole and pad sizes.
-
Placement and Orientation
- Carefully plan the placement and orientation of through-hole components to optimize board space and minimize interference with other components.
-
Consider the component height and clearance requirements.
-
Soldering and Assembly
- Provide sufficient space around through-hole components for manual soldering and inspection.
- Consider the use of wave soldering or selective soldering for automated assembly.
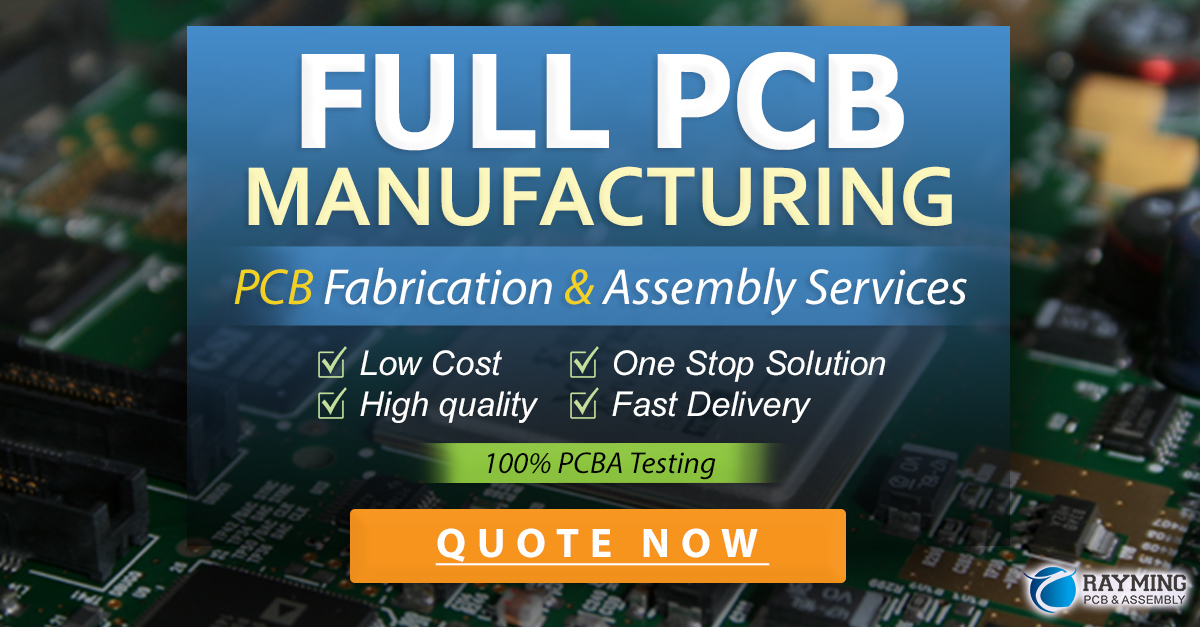
Frequently Asked Questions (FAQ)
1. Is through-hole technology becoming obsolete?
No, through-hole technology is not becoming obsolete. While surface mount technology has gained popularity, through-hole components still have their place in modern PCB designs. They offer superior mechanical strength, reliability, and power handling capabilities.
2. Can through-hole and surface mount components be used together on the same PCB?
Yes, it is common to mix through-hole and surface mount components on the same PCB. This approach allows designers to leverage the benefits of both technologies. Critical components that require high reliability or power handling can be implemented using through-hole, while smaller and less critical components can be surface mounted to save space.
3. What are the limitations of through-hole technology?
The main limitations of through-hole technology include:
– Larger component size compared to surface mount components.
– Higher assembly costs for high-volume production.
– Increased board space requirements due to the need for drilled holes and larger pads.
4. Are through-hole components suitable for high-frequency applications?
Through-hole components can be used in high-frequency applications, but designers need to consider the parasitic effects introduced by the component leads. Proper layout techniques, such as minimizing lead lengths and providing proper grounding, can help mitigate these effects. In some cases, surface mount components may be preferred for high-frequency designs.
5. Can through-hole components be used for automated assembly?
Yes, through-hole components can be used in automated assembly processes. Wave soldering and selective soldering techniques are commonly used for automated through-hole assembly. However, the assembly process is generally slower and more complex compared to surface mount assembly.
Conclusion
Through-hole technology remains a relevant and essential part of PCB design, despite the widespread adoption of surface mount technology. Its superior mechanical strength, reliability, and power handling capabilities make it indispensable in industries such as power electronics, high-reliability applications, and prototyping.
By understanding the advantages and design considerations of through-hole technology, PCB designers can make informed decisions when incorporating through-hole components into their designs. Mixing through-hole and surface mount components allows for the best of both worlds, enabling designers to create robust and efficient PCBs that meet the specific requirements of their applications.
As technology continues to evolve, through-hole technology will likely coexist with surface mount technology, each serving its unique purpose in the realm of PCB design. By leveraging the strengths of both technologies, designers can create innovative and reliable electronic products that push the boundaries of performance and functionality.
Leave a Reply