What is Through Hole Mounting?
Through hole mounting is the traditional method of attaching electronic components to a PCB. In this approach, the component leads are inserted into drilled holes on the PCB and soldered onto the opposite side. The holes are typically plated with a conductive material to create a secure electrical connection between the component leads and the copper traces on the PCB.
Advantages of Through Hole Mounting
- Strong mechanical bond: Through hole components are held securely in place by the soldered leads, providing excellent mechanical stability and durability.
- Easy manual assembly: Through hole components are easier to handle and solder manually compared to surface mount components, making them suitable for prototyping and low-volume production.
- Better heat dissipation: The leads of through hole components extend through the PCB, allowing for better heat dissipation compared to surface mount components.
- Compatibility with high-power components: Through hole mounting is often used for high-power components that generate significant heat, such as transformers and large capacitors.
Disadvantages of Through Hole Mounting
- Larger footprint: Through hole components require drilled holes and take up more space on the PCB compared to surface mount components.
- Increased manufacturing costs: Drilling holes and manually soldering through hole components is more time-consuming and labor-intensive, leading to higher manufacturing costs.
- Limited component density: The larger size of through hole components limits the achievable component density on the PCB.
- Reduced design flexibility: Through hole mounting restricts the placement of components to one side of the PCB, limiting design options.
What is Surface Mount Technology (SMT)?
Surface mount technology involves attaching electronic components directly onto the surface of the PCB without the need for drilled holes. SMT components have small metal pads or leads that are soldered directly to the copper pads on the PCB using a solder paste and a reflow oven.
Advantages of Surface Mount Technology
- Smaller footprint: SMT components are significantly smaller than through hole components, allowing for higher component density and more compact PCB designs.
- Increased design flexibility: Components can be placed on both sides of the PCB, enabling more complex and space-efficient designs.
- Automated assembly: SMT is well-suited for automated pick-and-place machines, enabling faster and more precise assembly compared to manual through hole soldering.
- Lower manufacturing costs: The automated assembly process and reduced PCB size lead to lower manufacturing costs, especially for high-volume production.
Disadvantages of Surface Mount Technology
- Challenging manual assembly: SMT components are small and require precise placement, making manual assembly more difficult and prone to errors.
- Sensitivity to thermal stress: SMT components are more susceptible to thermal stress due to their direct attachment to the PCB, which can lead to solder joint failures if not properly managed.
- Limited heat dissipation: The lack of leads extending through the PCB can limit the heat dissipation capabilities of SMT components.
- Higher setup costs: Implementing SMT requires specialized equipment and processes, which can result in higher initial setup costs compared to through hole mounting.
Comparing Through Hole and Surface Mount Methods
To better understand the differences between through hole and surface mount methods, let’s compare them side by side:
Characteristic | Through Hole | Surface Mount |
---|---|---|
Component Size | Larger | Smaller |
PCB Space | More | Less |
Assembly | Manual | Automated |
Manufacturing Cost | Higher | Lower |
Heat Dissipation | Better | Limited |
Design Flexibility | Limited | Higher |
Component Density | Lower | Higher |
Mechanical Strength | Strong | Moderate |
As evident from the comparison, surface mount technology offers several advantages over through hole mounting, particularly in terms of PCB space utilization, component density, and automated assembly. However, through hole mounting still has its place in certain applications where mechanical strength and heat dissipation are critical.
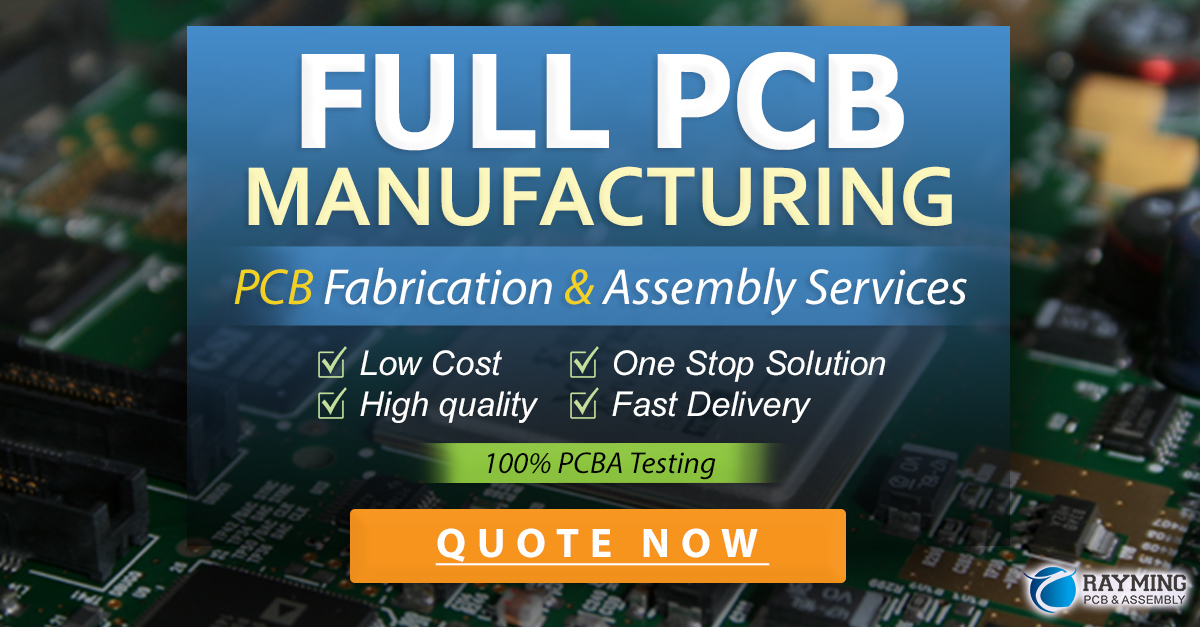
Factors to Consider When Choosing a Mounting Method
When deciding between through hole and surface mount methods for your PCB project, consider the following factors:
-
Production volume: For high-volume production, SMT is generally more cost-effective due to its automated assembly process. Through hole mounting may be more suitable for low-volume or prototype projects.
-
Component availability: Some components may only be available in through hole or surface mount packages. Ensure that the required components are available in the desired package type.
-
PCB size and density: If space is limited and high component density is required, SMT is the preferred choice. Through hole components take up more space and limit the achievable density.
-
Mechanical requirements: If the PCB will be subjected to high mechanical stress or vibration, through hole mounting may provide better mechanical stability due to the stronger solder joint.
-
Heat dissipation: For components that generate significant heat, through hole mounting may be advantageous due to the leads extending through the PCB, which aid in heat dissipation.
-
Design complexity: SMT allows for more complex and compact PCB designs, with components placed on both sides of the board. Through hole mounting is more limited in terms of design flexibility.
-
Manufacturing capabilities: Consider the available manufacturing capabilities and equipment. SMT requires specialized pick-and-place machines and reflow ovens, while through hole mounting can be done with simpler soldering tools.
Mixed Assembly: Combining Through Hole and SMT
In some cases, a combination of through hole and surface mount methods, known as mixed assembly, may be the best approach. Mixed assembly allows designers to take advantage of the strengths of both methods while mitigating their weaknesses.
For example, a PCB may use SMT for the majority of the components to achieve high density and automated assembly, while using through hole mounting for large or high-power components that require better mechanical stability or heat dissipation.
Mixed assembly can also be useful when incorporating legacy through hole components into a primarily surface mount design or when dealing with components that are only available in one package type.
FAQ
-
Q: Can through hole and surface mount components be used on the same PCB?
A: Yes, it is possible to use both through hole and surface mount components on the same PCB in a mixed assembly approach. This allows designers to take advantage of the strengths of both methods. -
Q: Is surface mount technology always better than through hole mounting?
A: While surface mount technology offers several advantages, such as smaller footprint, higher component density, and automated assembly, through hole mounting still has its place in certain applications. The choice between the two methods depends on various factors, including production volume, mechanical requirements, and heat dissipation needs. -
Q: Can surface mount components be soldered manually?
A: Yes, surface mount components can be soldered manually using soldering irons and tweezers. However, manual assembly of SMT components is more challenging and prone to errors compared to through hole components due to their small size and precise placement requirements. -
Q: Are through hole components becoming obsolete?
A: While surface mount technology has become increasingly popular, through hole components are still widely used in certain applications, particularly where mechanical strength and heat dissipation are critical. Some components may only be available in through hole packages, ensuring their continued relevance. -
Q: How do I choose between through hole and surface mount methods for my PCB project?
A: When choosing between through hole and surface mount methods, consider factors such as production volume, component availability, PCB size and density, mechanical requirements, heat dissipation needs, design complexity, and available manufacturing capabilities. Evaluate your project requirements and constraints to determine the most suitable mounting method.
Conclusion
Selecting the appropriate PCB mounting method is a crucial decision in the PCB design process. Through hole and surface mount technologies each have their own advantages and disadvantages, and the choice between them depends on various project-specific factors.
Through hole mounting offers strong mechanical bonds, easier manual assembly, and better heat dissipation, making it suitable for applications that require high mechanical stability or involve high-power components. On the other hand, surface mount technology enables smaller footprints, higher component density, automated assembly, and lower manufacturing costs, making it the preferred choice for most modern PCB designs.
In some cases, a mixed assembly approach combining both through hole and surface mount methods may be the best solution, allowing designers to leverage the strengths of both technologies.
When deciding between through hole and surface mount methods, carefully consider your project requirements, including production volume, component availability, PCB size and density, mechanical and thermal needs, design complexity, and manufacturing capabilities. By weighing these factors and understanding the characteristics of each mounting method, you can make an informed decision that ensures the optimal performance, reliability, and cost-effectiveness of your PCB design.
Leave a Reply