Introduction to Thermocouple Sensors
A thermocouple sensor is a versatile and widely used temperature measurement device that consists of two dissimilar metal wires joined together at one end, forming a junction. When the junction is exposed to a temperature different from the reference temperature at the other end of the wires, a voltage is generated that can be correlated to the temperature difference. This phenomenon is known as the Seebeck effect, named after the German physicist Thomas Johann Seebeck who discovered it in 1821.
Thermocouple sensors are widely used in various industries, including automotive, aerospace, manufacturing, energy, and scientific research, due to their affordability, wide temperature range, fast response time, and durability in harsh environments.
How Thermocouple Sensors Work
The working principle of a thermocouple sensor is based on the Seebeck effect. When two dissimilar metals are joined together at one end (the measuring junction) and exposed to a temperature gradient, a voltage is generated at the other end (the reference junction). This voltage, known as the Seebeck voltage, is proportional to the temperature difference between the measuring and reference junctions.
The magnitude of the Seebeck voltage depends on the types of metals used in the thermocouple. Different combinations of metals produce different voltage outputs for the same temperature difference. The most common thermocouple types and their temperature ranges are:
Thermocouple Type | Positive Lead | Negative Lead | Temperature Range (°C) |
---|---|---|---|
Type K | Chromel | Alumel | -200 to 1250 |
Type J | Iron | Constantan | -40 to 750 |
Type T | Copper | Constantan | -250 to 350 |
Type E | Chromel | Constantan | -200 to 900 |
Type N | Nicrosil | Nisil | -200 to 1300 |
To measure the temperature using a thermocouple sensor, the reference junction temperature must be known. This is usually achieved by using a cold junction compensation (CJC) technique, which measures the temperature at the reference junction using another temperature sensor, such as a thermistor or an integrated circuit temperature sensor.
Advantages of Thermocouple Sensors
Thermocouple sensors offer several advantages over other temperature measurement devices:
-
Wide temperature range: Thermocouple sensors can measure temperatures from -200°C to 2000°C, depending on the type of thermocouple used. This wide temperature range makes them suitable for a variety of applications.
-
Affordable: Compared to other temperature sensors, such as resistance temperature detectors (RTDs) and thermistors, thermocouple sensors are relatively inexpensive, making them a cost-effective choice for many applications.
-
Fast response time: Thermocouple sensors have a fast response time, typically in the order of milliseconds, which makes them ideal for measuring rapidly changing temperatures.
-
Durability: Thermocouple sensors are rugged and can withstand harsh environments, such as high temperatures, vibrations, and shocks.
-
Interchangeability: Thermocouple sensors of the same type are interchangeable, which means they can be replaced without the need for recalibration.
Disadvantages of Thermocouple Sensors
Despite their many advantages, thermocouple sensors also have some limitations:
-
Lower accuracy: Compared to RTDs and thermistors, thermocouple sensors have lower accuracy, typically around ±1°C to ±2°C. However, for many applications, this level of accuracy is sufficient.
-
Reference junction compensation: To accurately measure the temperature, the reference junction temperature must be known and compensated for. This adds complexity to the measurement system.
-
Sensitivity to electromagnetic interference: Thermocouple sensors are susceptible to electromagnetic interference (EMI), which can cause measurement errors. Proper shielding and grounding techniques must be used to minimize the impact of EMI.
-
Sensitivity to mechanical stress: Thermocouple sensors can be affected by mechanical stress, such as bending or twisting of the wires, which can cause measurement errors.
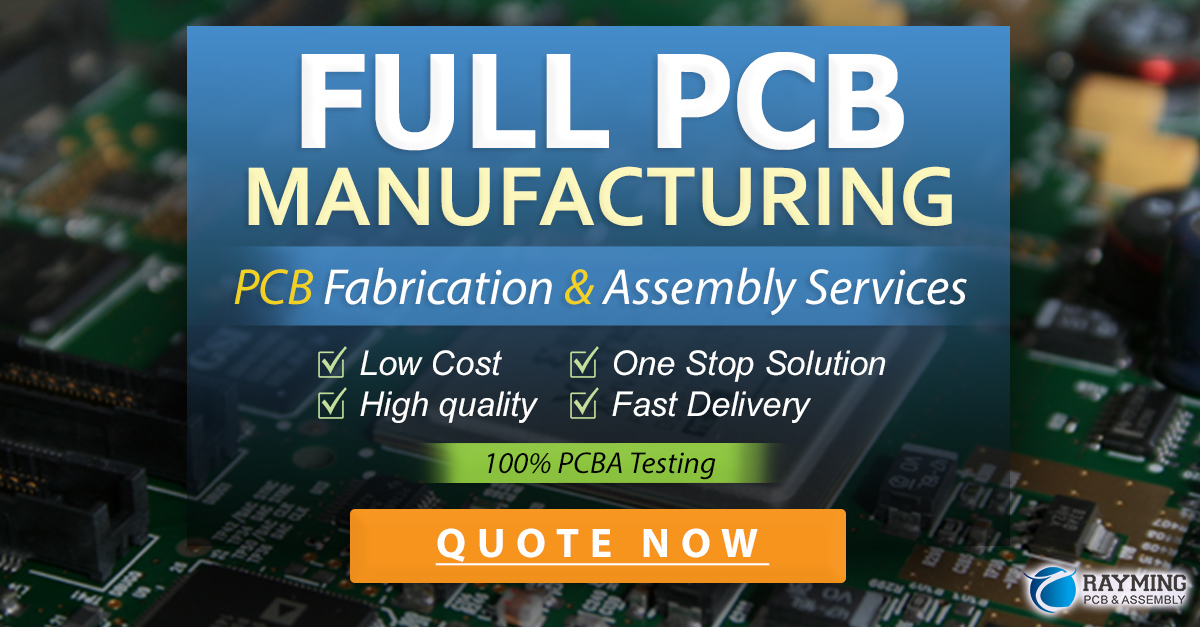
Applications of Thermocouple Sensors
Thermocouple sensors are used in a wide range of applications across various industries:
-
Automotive: In the automotive industry, thermocouple sensors are used to monitor exhaust gas temperatures, engine temperatures, and catalytic converter temperatures.
-
Aerospace: Thermocouple sensors are used in aircraft engines to monitor the temperature of the exhaust gas, turbine blades, and other critical components.
-
Manufacturing: In manufacturing processes, thermocouple sensors are used to monitor the temperature of molten metals, furnaces, and other high-temperature processes.
-
Energy: In power plants, thermocouple sensors are used to monitor the temperature of boilers, steam turbines, and other critical components.
-
Scientific research: Thermocouple sensors are used in scientific research to measure temperatures in experiments involving high temperatures, such as in material science and chemistry.
Selecting the Right Thermocouple Sensor
When selecting a thermocouple sensor for a specific application, several factors must be considered:
-
Temperature range: Choose a thermocouple type that covers the expected temperature range of the application.
-
Accuracy: Consider the required accuracy of the temperature measurement and select a thermocouple type that meets the accuracy requirements.
-
Environment: Consider the environment in which the thermocouple sensor will be used, such as the presence of corrosive chemicals, high pressures, or mechanical stress, and select a thermocouple type and protection tube material that can withstand these conditions.
-
Response time: Consider the required response time of the temperature measurement and select a thermocouple sensor with an appropriate size and construction to meet the response time requirements.
-
Cost: Consider the cost of the thermocouple sensor and the associated instrumentation, and select a solution that meets the budget constraints of the application.
Installing and Maintaining Thermocouple Sensors
To ensure accurate and reliable temperature measurements, proper installation and maintenance of thermocouple sensors are essential:
-
Proper installation: Thermocouple sensors must be installed correctly to ensure good thermal contact with the measured object and to minimize the impact of environmental factors, such as air currents and radiation.
-
Shielding and grounding: To minimize the impact of electromagnetic interference, thermocouple sensors must be properly shielded and grounded.
-
Regular calibration: Thermocouple sensors should be calibrated regularly to ensure accurate temperature measurements. The calibration frequency depends on the application and the required accuracy.
-
Replacement: Thermocouple sensors have a limited lifespan and should be replaced when they show signs of degradation, such as increased measurement drift or physical damage.
FAQ
-
What is the difference between a thermocouple sensor and an RTD?
A thermocouple sensor consists of two dissimilar metal wires joined together at one end, while an RTD (Resistance Temperature Detector) is a temperature sensor that measures the change in electrical resistance of a metal wire or film as a function of temperature. Thermocouple sensors have a wider temperature range and faster response time, while RTDs have higher accuracy and stability. -
Can thermocouple sensors be used in liquids?
Yes, thermocouple sensors can be used to measure the temperature of liquids, provided they are properly protected from the liquid using a suitable protection tube or sheath. -
How often should thermocouple sensors be calibrated?
The calibration frequency of thermocouple sensors depends on the application and the required accuracy. In general, thermocouple sensors should be calibrated at least once a year, but more frequent calibration may be necessary for critical applications or harsh environments. -
What is cold junction compensation, and why is it necessary?
Cold junction compensation (CJC) is a technique used to measure the temperature at the reference junction of a thermocouple sensor and compensate for its effect on the measured voltage. CJC is necessary to accurately measure the temperature at the measuring junction, as the voltage generated by the thermocouple sensor depends on the temperature difference between the measuring and reference junctions. -
Can thermocouple sensors be used in hazardous areas?
Yes, thermocouple sensors can be used in hazardous areas, such as those with explosive atmospheres, provided they are properly designed and certified for use in such environments. Special protection measures, such as explosion-proof enclosures or intrinsically safe barriers, may be necessary to ensure safe operation.
Conclusion
Thermocouple sensors are a versatile and widely used temperature measurement solution, offering a wide temperature range, fast response time, and affordability. By understanding the working principle, advantages, and limitations of thermocouple sensors, and by following proper installation and maintenance practices, users can ensure accurate and reliable temperature measurements in a variety of applications.
As technology advances, new developments in thermocouple sensor design and materials are expected to further improve their performance and expand their range of applications. For example, research is ongoing to develop high-temperature thermocouple sensors using advanced materials, such as ceramics and refractory metals, which can withstand temperatures up to 2500°C.
In conclusion, thermocouple sensors remain an essential tool for temperature measurement in various industries, and their importance is likely to continue in the future as the demand for accurate and reliable temperature monitoring grows in an increasingly technology-driven world.
Leave a Reply