Introduction to Thermal Pads in PCB Design
In the world of printed circuit board (PCB) design, managing heat dissipation is a critical factor in ensuring the optimal performance and longevity of electronic components. One effective solution for minimizing heat loss is the use of thermal pads, specifically spoked copper pads, which provide an efficient pathway for heat transfer from components to the PCB substrate.
What are Thermal Pads?
Thermal pads, also known as thermal interface materials (TIMs), are conductive materials that facilitate the transfer of heat between two surfaces. In PCB design, thermal pads are typically made of copper and are placed beneath heat-generating components, such as power MOSFETs, voltage regulators, or high-power processors.
The Importance of Thermal Management in PCBs
Proper thermal management is crucial in PCB design for several reasons:
- Component reliability: Excessive heat can lead to component failure, reduced lifespan, and decreased reliability.
- Performance stability: High temperatures can cause components to operate outside their specified range, leading to performance fluctuations and instability.
- Safety: In extreme cases, inadequate heat dissipation can result in thermal runaway, potentially causing fire hazards or other safety issues.
By incorporating thermal pads into PCB designs, engineers can effectively manage heat dissipation, ensuring the reliable and safe operation of electronic devices.
Spoked Copper Pads: An Efficient Thermal Pad Design
What are Spoked Copper Pads?
Spoked copper pads are a specific type of thermal pad design that features a central pad connected to multiple “spokes” or traces that radiate outward. This unique design offers several advantages over traditional solid copper pads:
- Increased surface area: The spoked design allows for a greater surface area in contact with the PCB substrate, enhancing heat transfer efficiency.
- Improved mechanical stability: The spokes help to evenly distribute mechanical stress, reducing the risk of pad delamination or lifting.
- Better solder joint reliability: The spoked design promotes better solder wetting and reduces the likelihood of solder joint failures.
Designing Spoked Copper Pads
When designing spoked copper pads, several factors must be considered to ensure optimal performance:
- Pad size: The size of the central pad should be appropriate for the component’s thermal requirements and the available PCB space.
- Spoke width and spacing: The width and spacing of the spokes should be carefully calculated to maximize heat transfer while maintaining adequate electrical clearance.
- Number of spokes: The number of spokes can vary depending on the pad size and the desired heat dissipation performance.
- Copper thickness: Thicker copper layers provide better thermal conductivity but may increase manufacturing costs.
Here’s an example of a spoked copper pad design:
Parameter | Value |
---|---|
Central pad diameter | 5 mm |
Spoke width | 0.5 mm |
Spoke length | 3 mm |
Number of spokes | 8 |
Copper thickness | 2 oz (70 μm) |
Thermal Resistance Comparison
To demonstrate the effectiveness of spoked copper pads compared to solid pads, consider the following thermal resistance comparison:
Pad Type | Thermal Resistance (°C/W) |
---|---|
Solid copper pad (5 mm diameter) | 10 |
Spoked copper pad (5 mm diameter, 8 spokes) | 7 |
As shown in the table, the spoked copper pad offers a 30% reduction in thermal resistance compared to the solid pad, highlighting its superior heat dissipation capabilities.
Implementing Spoked Copper Pads in PCB Layouts
PCB Layer Stack-up Considerations
When incorporating spoked copper pads into a PCB design, it’s essential to consider the layer stack-up:
- Thermal vias: Placing thermal vias beneath the central pad can further enhance heat transfer to the inner layers and the opposite side of the PCB.
- Copper pour: Surrounding the spoked pad with a copper pour can help to distribute heat more evenly across the PCB surface.
- Solder mask: Ensuring adequate solder mask coverage around the spokes is crucial to prevent short circuits and maintain electrical integrity.
Component Placement and Routing
Proper component placement and routing are critical when using spoked copper pads:
- Component orientation: Orient components to align with the spoked pad design, ensuring optimal contact between the component and the pad.
- Trace routing: Route traces away from the spokes to avoid interference with heat transfer and maintain signal integrity.
- Thermal relief: Use thermal relief connections for traces attached to the central pad to minimize heat transfer to other parts of the circuit.
Thermal Simulation and Verification
Before finalizing a PCB design with spoked copper pads, it’s recommended to perform thermal simulations and verifications:
- Thermal modeling: Use thermal modeling software to predict the temperature distribution and identify potential hot spots.
- Prototype testing: Fabricate prototype PCBs and perform thermal testing under real-world conditions to validate the design’s performance.
- Iteration and optimization: Based on simulation and testing results, iterate and optimize the spoked pad design to achieve the desired thermal performance.
By carefully implementing spoked copper pads and considering factors such as layer stack-up, component placement, routing, and thermal simulation, PCB designers can effectively minimize heat loss and ensure the reliable operation of electronic devices.
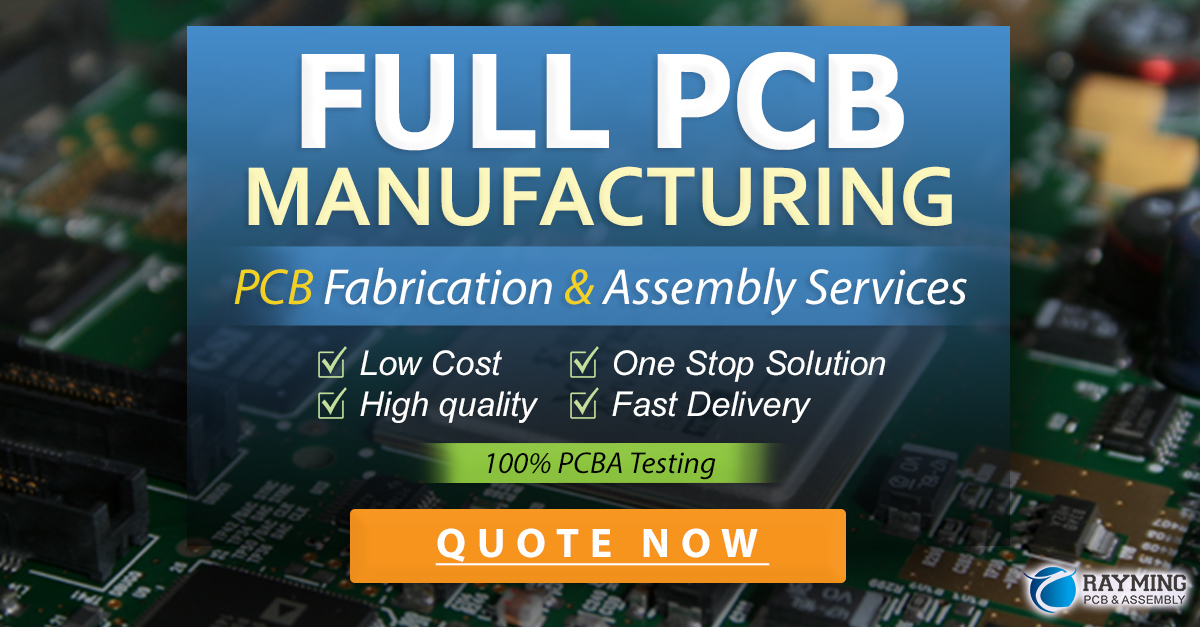
Best Practices for Designing with Spoked Copper Pads
Design for Manufacturability (DFM)
When designing spoked copper pads, it’s crucial to adhere to DFM guidelines to ensure the PCB can be reliably manufactured:
- Minimum feature size: Ensure that the spoke width and spacing comply with the PCB manufacturer’s minimum feature size requirements.
- Copper balance: Maintain proper copper balance across the PCB layers to prevent warping or other manufacturing defects.
- Solder mask alignment: Clearly communicate solder mask requirements to the manufacturer to ensure accurate alignment with the spoked pads.
Collaboration with Thermal Engineers
Collaborating with thermal engineers throughout the PCB design process can help to optimize the spoked copper pad design:
- Early involvement: Engage thermal engineers early in the design process to identify critical heat-generating components and discuss thermal management strategies.
- Iterative design: Work closely with thermal engineers to refine the spoked pad design based on simulation results and prototype testing feedback.
- Documentation: Clearly document the thermal requirements and design decisions to ensure a smooth handoff between the PCB design and thermal engineering teams.
Continuous Improvement and Learning
As with any aspect of PCB design, continuous improvement and learning are essential when working with spoked copper pads:
- Stay updated: Keep abreast of the latest advancements in thermal management techniques and materials.
- Attend conferences and workshops: Participate in industry conferences and workshops to learn from experts and share best practices with peers.
- Experiment and innovate: Don’t be afraid to experiment with new spoked pad designs or materials to push the boundaries of thermal performance.
By following best practices, collaborating with thermal engineers, and continuously improving their skills, PCB designers can effectively leverage spoked copper pads to minimize heat loss and create high-performance, reliable electronic devices.
Frequently Asked Questions (FAQ)
1. How do I determine the appropriate size and number of spokes for a thermal pad?
The size and number of spokes for a thermal pad depend on several factors, including the component’s heat generation, the available PCB space, and the desired thermal performance. As a general rule, larger pads with more spokes offer better heat dissipation, but this must be balanced against other design constraints. Thermal simulations and prototype testing can help to optimize the pad design for specific applications.
2. Can spoked copper pads be used on both the top and bottom layers of a PCB?
Yes, spoked copper pads can be used on both the top and bottom layers of a PCB. In fact, using thermal vias to connect spoked pads on both sides of the board can further enhance heat dissipation by providing a pathway for heat to transfer through the PCB substrate.
3. Are there any limitations or challenges when using spoked copper pads in high-density PCB designs?
In high-density PCB designs, the use of spoked copper pads may be limited by the available space and the proximity of other components and traces. In such cases, designers may need to prioritize the placement of spoked pads for the most critical heat-generating components and find alternative thermal management solutions for other parts of the circuit.
4. How do I ensure proper solder mask coverage for spoked copper pads?
To ensure proper solder mask coverage for spoked copper pads, it’s important to clearly communicate the design requirements to the PCB manufacturer. Provide detailed layer-by-layer artwork files that specify the solder mask openings for the spoked pads, and consider using solder mask expansion or contraction to account for any alignment tolerances.
5. Can spoked copper pads be used in conjunction with other thermal management techniques, such as heatsinks or thermal interface materials?
Yes, spoked copper pads can be used in conjunction with other thermal management techniques to further enhance heat dissipation. For example, placing a heatsink on top of a component mounted on a spoked copper pad can provide an additional pathway for heat to dissipate into the surrounding environment. Similarly, using thermal interface materials between the component and the spoked pad can improve thermal contact and reduce thermal resistance.
Conclusion
Thermal management is a critical aspect of PCB design, and the use of spoked copper pads offers an effective solution for minimizing heat loss and ensuring the reliable operation of electronic components. By understanding the principles of spoked pad design, implementing best practices, and collaborating with thermal engineers, PCB designers can create high-performance, thermally optimized circuits that meet the demands of today’s electronic devices.
As technology continues to advance and power densities increase, the importance of effective thermal management will only continue to grow. By staying at the forefront of thermal design techniques and continuously refining their skills, PCB designers can play a crucial role in driving innovation and creating the next generation of reliable, efficient electronic products.
Leave a Reply