What is a Heavy Copper PCB?
A Heavy Copper PCB, also known as a Thick Copper PCB or Extreme Copper PCB, is a type of printed circuit board that uses thicker copper traces than standard PCBs. While a typical PCB might have copper traces ranging from 0.5 oz to 2 oz per square foot, heavy copper PCBs can have copper weights ranging from 3 oz to 20 oz per square foot or more.
The increased copper thickness provides several advantages, including:
- Improved current carrying capacity
- Better heat dissipation
- Enhanced mechanical strength
- Reduced resistance and voltage drop
These properties make heavy copper PCBs ideal for applications that require high power handling, such as power electronics, automotive systems, aerospace equipment, and industrial controls.
Why Use Heavy Copper PCBs?
There are several reasons why you might choose to use a heavy copper PCB in your design:
High Current Carrying Capacity
The primary benefit of using thicker copper traces is the ability to carry higher currents without overheating or experiencing voltage drop. The current carrying capacity of a trace is proportional to its cross-sectional area, which increases with copper thickness. By using heavy copper PCBs, you can design power electronics and other high-current applications with greater efficiency and reliability.
Improved Heat Dissipation
Thicker copper traces also provide better heat dissipation, helping to prevent thermal damage to components and extend the lifespan of the PCB. The increased thermal mass of the copper allows it to absorb and spread heat more effectively, reducing hot spots and thermal stress on the board.
Enhanced Mechanical Strength
Heavy copper PCBs offer greater mechanical strength and durability compared to standard PCBs. The thicker copper traces are less prone to damage from vibration, impact, and other mechanical stresses, making them suitable for use in harsh environments and applications subject to high levels of physical stress.
Lower Resistance and Voltage Drop
As copper thickness increases, the resistance of the traces decreases, leading to lower voltage drop and power loss. This is particularly important in high-current applications, where even small amounts of resistance can result in significant power dissipation and reduced efficiency.
Heavy Copper PCB Manufacturing Process
The manufacturing process for heavy copper PCBs is similar to that of standard PCBs, but with some additional steps and considerations to accommodate the thicker copper traces.
PCB Design and Layout
The first step in heavy copper PCB manufacturing is the design and layout of the board. The designer must take into account the specific requirements of the application, including the required current carrying capacity, heat dissipation, and mechanical strength. They must also consider the limitations of the manufacturing process, such as minimum trace widths and spacings, and the available copper weights.
Copper Foil Lamination
Once the design is finalized, the next step is to laminate the copper foil onto the base material, typically FR-4 or another high-temperature laminate. For heavy copper PCBs, the copper foil is usually pre-plated to the desired thickness before lamination. The lamination process involves applying heat and pressure to bond the copper foil to the base material.
Drilling and Plating
After lamination, the PCB is drilled to create holes for through-hole components and vias. The holes are then plated with copper to provide electrical connectivity between layers. For heavy copper PCBs, the plating process may need to be adjusted to ensure adequate coverage and adhesion of the thicker copper traces.
Etching and Resist Stripping
The next step is to etch away the unwanted copper to create the desired circuit pattern. This is typically done using a photolithographic process, where a photoresist is applied to the board, exposed to light through a mask, and developed to reveal the desired pattern. The exposed copper is then etched away using a chemical solution, leaving only the desired traces. After etching, the remaining photoresist is stripped away.
Solder Mask Application and Finishing
The final steps in the manufacturing process involve applying a solder mask to protect the copper traces and prevent short circuits, and applying a surface finish to the exposed copper to improve solderability and prevent oxidation. Common surface finishes for heavy copper PCBs include HASL (hot air solder leveling), ENIG (electroless nickel immersion gold), and OSP (organic solderability preservative).
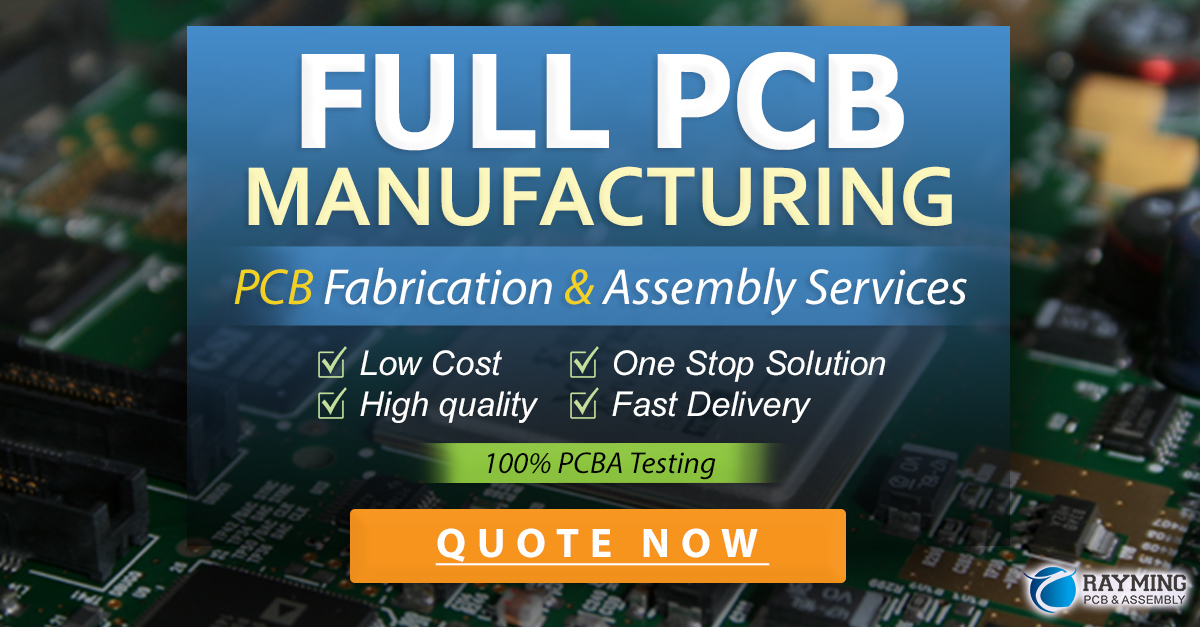
Challenges in Heavy Copper PCB Manufacturing
While heavy copper PCBs offer many benefits, they also present some unique challenges in manufacturing that must be addressed to ensure reliable and cost-effective production.
Copper Thickness Limitations
One of the main challenges in heavy copper PCB manufacturing is the limitation on the maximum copper thickness that can be achieved. While copper weights up to 20 oz/ft² or more are possible, the thickness of the copper can impact the ability to create fine pitch features and maintain tight tolerances. As the copper thickness increases, the minimum trace width and spacing also increase, which can limit the routing density and overall functionality of the board.
Increased Manufacturing Costs
Another challenge is the increased cost of manufacturing heavy copper PCBs compared to standard PCBs. The thicker copper foils and additional processing steps required can add significant expense to the manufacturing process. Additionally, the increased weight of the copper can impact shipping and handling costs.
Thermal Management
While the improved heat dissipation of heavy copper PCBs is a benefit in many applications, it can also present challenges in manufacturing. The increased thermal mass of the copper can make it more difficult to control the temperature during the lamination and soldering processes, which can lead to issues with bonding and reliability.
Plating Challenges
The plating process for heavy copper PCBs can also be more challenging than for standard PCBs. The thicker copper traces require more time and material to plate, and there is a greater risk of voids or other defects in the plating that can impact the reliability of the board. Special attention must be paid to the plating process to ensure adequate coverage and adhesion of the copper.
Applications of Heavy Copper PCBs
Heavy copper PCBs are used in a wide range of applications that require high power handling, improved heat dissipation, and enhanced mechanical strength. Some of the most common applications include:
Power Electronics
Power electronics, such as motor drives, power supplies, and inverters, are one of the primary applications for heavy copper PCBs. The high current carrying capacity and improved heat dissipation of heavy copper PCBs make them ideal for handling the high power levels and thermal stresses encountered in these applications.
Automotive Electronics
Heavy copper PCBs are also used extensively in automotive electronics, particularly in high-power applications such as electric vehicle battery management systems, motor controllers, and charging systems. The enhanced mechanical strength and durability of heavy copper PCBs make them well-suited for the harsh operating environments encountered in automotive applications.
Industrial Controls
Industrial control systems, such as programmable logic controllers (PLCs), motor drives, and power distribution systems, often require heavy copper PCBs to handle the high currents and power levels involved. The improved reliability and thermal management of heavy copper PCBs can help to ensure the long-term performance and stability of these critical systems.
Aerospace and Defense
Heavy copper PCBs are also used in aerospace and defense applications, where high reliability and performance are essential. Applications such as radar systems, avionics, and satellite communications often require the enhanced current carrying capacity and heat dissipation of heavy copper PCBs to ensure reliable operation in harsh environments.
Frequently Asked Questions (FAQ)
1. What is the difference between heavy copper PCBs and standard PCBs?
Heavy copper PCBs use thicker copper traces than standard PCBs, typically ranging from 3 oz to 20 oz per square foot or more, compared to 0.5 oz to 2 oz per square foot for standard PCBs. The thicker copper provides improved current carrying capacity, better heat dissipation, enhanced mechanical strength, and reduced resistance and voltage drop.
2. What are the advantages of using heavy copper PCBs?
The main advantages of using heavy copper PCBs include:
– Higher current carrying capacity for handling high power levels
– Improved heat dissipation for better thermal management
– Enhanced mechanical strength and durability for use in harsh environments
– Lower resistance and voltage drop for improved efficiency and performance
3. What are some common applications for heavy copper PCBs?
Heavy copper PCBs are commonly used in applications that require high power handling and improved thermal management, such as:
– Power electronics (e.g., motor drives, power supplies, inverters)
– Automotive electronics (e.g., electric vehicle battery management systems, motor controllers, charging systems)
– Industrial controls (e.g., PLCs, motor drives, power distribution systems)
– Aerospace and defense (e.g., radar systems, avionics, satellite communications)
4. What are the challenges in manufacturing heavy copper PCBs?
Some of the main challenges in manufacturing heavy copper PCBs include:
– Limitations on the maximum copper thickness that can be achieved while maintaining fine pitch features and tight tolerances
– Increased manufacturing costs due to thicker copper foils and additional processing steps
– Thermal management challenges due to the increased thermal mass of the copper
– Plating challenges to ensure adequate coverage and adhesion of the thicker copper traces
5. How do I choose the right copper thickness for my heavy copper PCB design?
The choice of copper thickness for a heavy copper PCB design depends on several factors, including the required current carrying capacity, heat dissipation needs, mechanical strength requirements, and cost constraints. It’s important to work with an experienced PCB manufacturer to determine the optimal copper thickness for your specific application, taking into account the design requirements and manufacturing capabilities. In general, higher copper weights will provide greater benefits in terms of current carrying capacity and thermal management, but may also increase costs and limit the ability to create fine pitch features.
Conclusion
Heavy copper PCBs offer numerous advantages over standard PCBs, including improved current carrying capacity, better heat dissipation, enhanced mechanical strength, and reduced resistance and voltage drop. These properties make them ideal for use in high-power applications such as power electronics, automotive systems, industrial controls, and aerospace and defense.
However, the manufacturing process for heavy copper PCBs also presents some unique challenges, such as limitations on copper thickness, increased manufacturing costs, thermal management issues, and plating difficulties. By understanding these challenges and working with an experienced PCB manufacturer, designers can successfully incorporate heavy copper PCBs into their products to achieve the desired performance and reliability.
As the demand for high-power electronics continues to grow across a wide range of industries, heavy copper PCBs will play an increasingly important role in enabling the next generation of advanced technologies. By staying up-to-date with the latest developments in heavy copper PCB manufacturing and design, engineers and product developers can stay ahead of the curve and create products that meet the evolving needs of their customers.
Leave a Reply