What is FR4 PCB?
FR4 PCB (Flame Retardant 4 Printed Circuit Board) is a type of PCB made from a composite material consisting of woven fiberglass cloth with an epoxy resin binder. The “FR” designation indicates flame retardant properties, while the “4” refers to the specific grade of the material. FR4 is the most widely used and versatile PCB substrate due to its excellent mechanical, electrical, and thermal properties.
Key Characteristics of FR4 PCB
- High strength and stiffness
- Excellent electrical insulation
- Good thermal stability
- Flame retardant
- Suitable for high-density designs
- Cost-effective
Advantages of Using FR4 PCB
1. Mechanical Strength
FR4 PCBs offer superior mechanical strength compared to other PCB materials. The woven fiberglass reinforcement provides high tensile strength and resistance to bending and twisting. This makes FR4 suitable for applications that require sturdy and durable PCBs.
2. Electrical Insulation
The epoxy resin used in FR4 PCBs provides excellent electrical insulation properties. This ensures minimal leakage currents and reduces the risk of short circuits between adjacent traces. FR4’s high dielectric strength allows for the use of thinner insulation layers, enabling higher-density PCB designs.
3. Thermal Stability
FR4 PCBs have good thermal stability, with a glass transition temperature (Tg) ranging from 130°C to 180°C depending on the specific grade. This means that FR4 can withstand high operating temperatures without significant degradation of its mechanical and electrical properties.
4. Flame Retardance
As the name suggests, FR4 PCBs are flame retardant. The material is designed to self-extinguish when exposed to a flame, minimizing the risk of fire hazards in electronic devices. This property is crucial for applications that require compliance with safety standards.
5. High-Density Capability
The mechanical strength and electrical insulation properties of FR4 allow for the design of high-density PCBs. Smaller trace widths and spacing can be achieved, enabling the integration of more components and functionalities within a given PCB area.
6. Cost-Effectiveness
FR4 is a widely available and cost-effective PCB material. Its popularity and large-scale production result in lower manufacturing costs compared to other specialized PCB substrates. This makes FR4 an attractive choice for a wide range of applications, from consumer electronics to industrial systems.
Applications of FR4 PCB
1. Consumer Electronics
FR4 PCBs are extensively used in consumer electronic devices such as smartphones, tablets, laptops, televisions, and home appliances. The versatility and cost-effectiveness of FR4 make it an ideal choice for mass-produced consumer products.
2. Industrial Equipment
Industrial equipment such as control systems, automation devices, and measurement instruments often rely on FR4 PCBs. The mechanical strength and thermal stability of FR4 ensure reliable performance in demanding industrial environments.
3. Automotive Electronics
FR4 PCBs are used in various automotive electronic systems, including engine control units, infotainment systems, and safety features. The flame retardant properties of FR4 are particularly important in automotive applications to ensure passenger safety.
4. Medical Devices
Medical devices such as patient monitors, diagnostic equipment, and implantable devices utilize FR4 PCBs. The high reliability and electrical insulation properties of FR4 are crucial for medical applications where patient safety is paramount.
5. Aerospace and Defense
FR4 PCBs are used in aerospace and defense applications such as avionics systems, radar equipment, and military communication devices. The mechanical strength and thermal stability of FR4 enable these systems to withstand harsh environmental conditions.
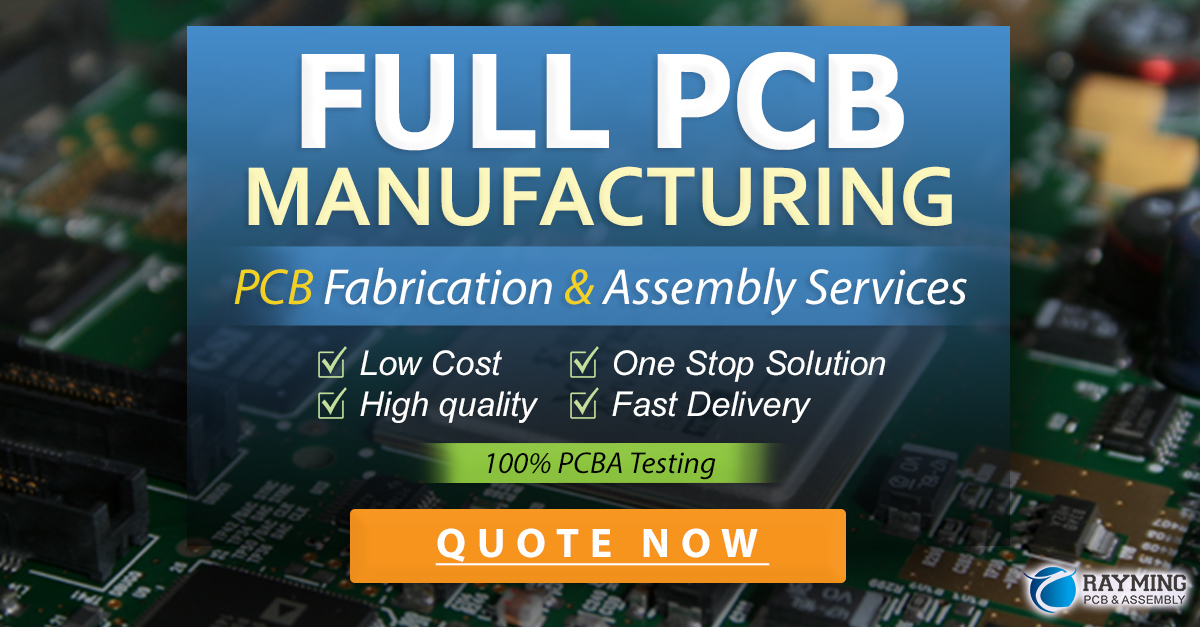
FR4 PCB Manufacturing Process
The manufacturing process of FR4 PCBs involves several steps to transform the raw materials into a functional printed circuit board. Here’s an overview of the key stages:
-
Material Preparation: The FR4 substrate is cut to the desired size, and the copper foil is laminated onto one or both sides of the substrate using heat and pressure.
-
Drilling: Holes are drilled through the FR4 substrate to accommodate through-hole components and provide interconnections between layers in multi-layer PCBs.
-
Patterning: The desired circuit pattern is transferred onto the copper foil using photolithography. A photoresist layer is applied, exposed to UV light through a photomask, and developed to create the desired pattern.
-
Etching: The exposed copper areas are etched away using a chemical solution, leaving only the desired circuit traces on the FR4 substrate.
-
Plating: Additional copper plating is applied to the holes and traces to improve conductivity and ensure reliable connections.
-
Solder Mask Application: A solder mask layer is applied to protect the circuit traces and prevent short circuits during soldering.
-
Silkscreen Printing: Text, logos, and component identifiers are printed onto the PCB surface using silkscreen printing.
-
Surface Finish: A surface finish, such as HASL (Hot Air Solder Leveling), ENIG (Electroless Nickel Immersion Gold), or OSP (Organic Solderability Preservative), is applied to protect the exposed copper and enhance solderability.
-
Electrical Testing: The manufactured FR4 PCB undergoes electrical testing to ensure proper functionality and adherence to design specifications.
-
Singulation: The panel containing multiple PCBs is cut into individual boards using a routing or punching process.
Advancements in FR4 PCB Technology
Over the years, FR4 PCB technology has evolved to meet the ever-increasing demands of modern electronics. Some notable advancements include:
1. High Tg FR4
High Tg (glass transition temperature) FR4 variants have been developed to offer improved thermal stability. These materials can withstand higher operating temperatures, making them suitable for applications with demanding thermal requirements.
2. Low-Loss FR4
Low-loss FR4 materials have been engineered to reduce dielectric losses and improve signal integrity at high frequencies. These materials are particularly beneficial for high-speed digital and RF applications.
3. Halogen-Free FR4
Halogen-free FR4 variants have been developed to address environmental concerns and comply with regulations such as RoHS (Restriction of Hazardous Substances). These materials achieve flame retardance without the use of halogenated compounds.
4. Embedded Components
Techniques for embedding components within the FR4 substrate have been developed to further increase PCB density and miniaturization. Embedded resistors, capacitors, and inductors can be integrated into the PCB, saving space and improving performance.
5. Advanced Manufacturing Processes
Advancements in PCB manufacturing processes, such as laser drilling, high-density interconnect (HDI), and micro-via technology, have enabled the production of more complex and high-density FR4 PCBs. These processes allow for finer feature sizes and improved reliability.
Choosing the Right FR4 PCB for Your Application
When selecting an FR4 PCB for your application, consider the following factors:
-
Thickness: FR4 PCBs are available in various thicknesses, typically ranging from 0.4 mm to 3.2 mm. Choose a thickness that provides the required mechanical strength and accommodates your components and design requirements.
-
Copper Weight: The copper weight, measured in ounces per square foot (oz/ft²), determines the thickness of the copper foil laminated onto the FR4 substrate. Common copper weights include 0.5 oz/ft², 1 oz/ft², and 2 oz/ft². Higher copper weights offer better current carrying capacity but may increase manufacturing costs.
-
Number of Layers: FR4 PCBs can be single-sided, double-sided, or multi-layered. The number of layers depends on the complexity of your circuit design and the required interconnections. More layers provide greater design flexibility but also increase manufacturing costs.
-
Surface Finish: Choose a surface finish that suits your soldering requirements and provides adequate protection against oxidation and corrosion. Common surface finishes include HASL, ENIG, and OSP.
-
Special Requirements: Consider any special requirements your application may have, such as high temperature resistance, low dielectric loss, or halogen-free materials. Consult with your PCB manufacturer to select the appropriate FR4 variant that meets your specific needs.
FR4 PCB Design Considerations
When designing an FR4 PCB, keep the following considerations in mind:
-
Design Rules: Adhere to the design rules and guidelines provided by your PCB manufacturer. These rules specify minimum trace widths, spacings, hole sizes, and other parameters to ensure manufacturability and reliability.
-
Component Placement: Carefully plan the placement of components on your FR4 PCB to optimize signal routing, minimize noise, and ensure proper heat dissipation. Consider the mechanical constraints and assembly requirements when placing components.
-
Signal Integrity: Pay attention to signal integrity considerations, especially for high-speed designs. Use appropriate trace widths, impedance control techniques, and proper termination to minimize signal reflections and crosstalk.
-
Thermal Management: Ensure adequate thermal management by providing sufficient copper pour for heat dissipation, using thermal vias to transfer heat to other layers, and considering the use of thermal management techniques such as heatsinks or thermal interface materials.
-
Manufacturing Feasibility: Collaborate with your PCB manufacturer early in the design process to ensure the feasibility of your design. They can provide valuable feedback on design for manufacturability (DFM) and help you optimize your design for cost-effective production.
Frequently Asked Questions (FAQ)
1. What does FR4 stand for in PCB terminology?
FR4 stands for Flame Retardant 4. It refers to a specific grade of flame-retardant glass-reinforced epoxy laminate material used in PCB manufacturing.
2. Is FR4 suitable for high-frequency applications?
While standard FR4 materials have limitations at high frequencies due to dielectric losses, low-loss FR4 variants have been developed specifically for high-frequency applications. These materials offer improved signal integrity and reduced losses at higher frequencies.
3. Can FR4 PCBs be used in high-temperature environments?
Yes, FR4 PCBs can withstand relatively high temperatures. The glass transition temperature (Tg) of standard FR4 materials ranges from 130°C to 180°C. For even higher temperature requirements, high Tg FR4 variants are available.
4. Are FR4 PCBs environmentally friendly?
Standard FR4 materials contain halogenated flame retardants, which can have environmental concerns. However, halogen-free FR4 variants have been developed to address these concerns and comply with environmental regulations such as RoHS.
5. How do I choose the right thickness for my FR4 PCB?
The choice of FR4 PCB thickness depends on several factors, including the mechanical strength requirements, component sizes, and design constraints. Thicker PCBs offer greater mechanical stability but may increase manufacturing costs. Consult with your PCB manufacturer to determine the optimal thickness for your specific application.
Conclusion
FR4 PCB has been a staple in the electronics industry for decades, and its popularity continues to grow. With its excellent mechanical, electrical, and thermal properties, FR4 offers a versatile and cost-effective solution for a wide range of applications. As technology advances, FR4 PCB manufacturing processes and materials continue to evolve, enabling the development of more complex and high-performance electronic devices.
When designing and manufacturing FR4 PCBs, it is crucial to consider factors such as material selection, design rules, signal integrity, thermal management, and manufacturing feasibility. By collaborating with experienced PCB manufacturers and following best practices, you can ensure the success of your FR4 PCB projects.
As we look towards the future, FR4 PCB technology is poised to play a significant role in shaping the electronics landscape. With ongoing advancements in materials, manufacturing processes, and design techniques, FR4 PCBs will continue to meet the ever-increasing demands of modern electronics, driving innovation across various industries.
Leave a Reply