Introduction
Printed circuit boards (PCBs) provide the foundation for almost all modern electronic devices. They allow components to be interconnected and packaged into functional products. For any new hardware, PCBs can either be bought off-the-shelf or custom designed for the particular application. Here we will examine the advantages and disadvantages of creating custom PCBs versus using standard premade boards.
Custom PCBs are designed specifically for a new product, tailored to its unique requirements. This gives high design flexibility but comes at a higher cost. Standard PCBs sacrifice customization for lower prices in high volumes. Weighing the trade-offs helps determine when to go custom.
Below we will look at factors like:
- Cost comparison
- Customization benefits
- Manufacturing considerations
- Quality and testing impact
- Time factors
- Complexity and scale
- Support and documentation
Understanding these pros and cons helps decide when investing in custom PCB development is worthwhile for a project.
The Benefits of Custom PCBs
1. Optimized for the Product’s Design Requirements
The primary advantage of custom PCBs is the ability to tailor the board completely to the needs of the product under development. This allows optimizing for critical criteria:
- Component placement and trace routing are designed for only the necessary parts, which minimizes board space needed.
- Circuit layout is designed specifically for signal and power integrity of the product, avoiding interference or noise issues.
- Board shape and dimensions are designed to fit the exact target enclosure or application space available.
- Locations of connectors, controls, and peripherals are placed specifically for integration with other product elements like the enclosure or interfaces.
- Thermal design including plane layers and component placement is optimized for the required heat dissipation.
With pre-made PCBs, you are limited to existing layouts which likely won’t align as well to the product. Custom boards provide full control over every design parameter.
2. Component Selection Flexibility
Since custom PCBs only need to support components used in the product design, there is flexibility to select optimal parts. All factors can be considered:
- Electrical performance parameters like voltage and current ratings, tolerance, frequency response, etc.
- Physical size, shape, and packaging to fit board space and layout.
- Integration of any unique component technologies needed by the product.
- Long term component lifecycle and availability.
- Cost, inventory, and sourcing factors.
Standard PCBs limit you to components and packages supported in their predefined layouts. A custom board allows picking parts tailored for the application.
3. Control of Board Materials and Construction
Custom PCB fabrication allows selecting ideal materials and construction methods for the product requirements:
- Choose core laminates like FR-4, Rogers, flexible circuits, etc. to suit dielectric, loss, and thermal needs.
- Specify layer count from simple 2 layer to complex 6+ layer stacks to optimize cost and layout capability.
- Define board thickness, copper weights, finishes, coatings, etc. based on the design needs.
- Determine fabrication process: subtractive, additive, semi-additive, or HDI.
- Specify unique board shapes, cutouts, silkscreen—not just standard rectangular boards.
Premade boards lock you into the predetermined materials and methods used, which may not be suitable for the electronics being designed.
4. Design Miniaturization
For products with tight space constraints like wearables or handheld devices, custom PCB capabilities can help minimize size. Approaches include:
- Using HDI fabrication for high density interconnect routing.
- Employing more compact components and chip-scale packages.
- Consolidating functionality into fewer parts.
- Designing complex multilayer boards to use vertical space.
- Using thinner, flexible PCB materials to save space.
These miniaturization approaches rely on custom board fabrication processes not supported on generic PCBs.
5. Performance Optimization
PCBs can be customized to provide specialized performance capabilities critical for the product:
- Controlled impedance traces for high frequency, RF, or analog signals.
- Low-noise ground and power planes.
- High-current power distribution design.
- Careful stackup and layer use for EMI control.
- Thermal vias, ground planes, and component placement for heating mitigation.
- Reliability enhancement with redundant traces or circuits.
For a pre-made PCB, you can’t fine tune to meet tight signal, thermal, or reliability specifications.
6. Cost and Inventory Reduction
With custom boards, you only produce what you need for your product build volume. No money is wasted on unused PCB inventory.
And smaller, more efficient designs use less materials lowering fabrication costs. These factors together reduce total cost compared to bulky pre-made boards bought in volume.
In summary, custom PCBs maximize design optimization, component integration, material selection, miniaturization, and performance for the target product. This gives them a significant advantage over rigid, generalized standard boards.
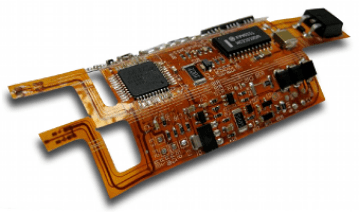
The Drawbacks of Custom PCBs
1. Higher Upfront Costs and Lead Times
The major tradeoff for complete design flexibility is that custom PCBs require high upfront investment and longer manufacturing times.
Each new custom design incurs engineering time for:
- Schematic capture and board layout requiring skilled PCB designers.
- More extensive simulations and verification due to new design.
- Creating manufacturing and test documentation.
- Prototyping iterations to refine the design.
This development cost is amortized over future production, but increases initial time and budget requirements.
In addition to development, initial fabrication lead times for a new custom design are higher:
- 4-6 weeks typically for first prototypes.
- 8-10 weeks for initial production.
Subsequent fabrication of an existing custom design is faster. But upfront cost and schedule impact should be planned for.
2. Potential Design Errors and Revisions
Given the greater complexity in creating a new custom PCB design, there is increased likelihood of design flaws slipping through versus a proven premade board. Potential issues include:
- Component footprints or pinouts defined incorrectly.
- Electrical connectivity errors in schematics or layout.
- Manufacturing rule violations making the board unbuildable.
- Signal integrity problems leading to glitches or noise.
- Power distribution problems creating transient spikes or brownsouts.
- Insufficient heat dissipation causing thermal shutdowns.
Each issue requires design revisions and another prototype fabrication round to resolve. This extends the development timeline and cost. Careful verification and simulation helps prevent errors.
3. Higher Risk of Obsolescence
If any custom components specified during the new PCB development become end-of-life or obsolete in the future, the design could require revisions. By contrast off-the-shelf boards may have longer lifecycles reducing risk of obsolescence.
4. Larger Minimum Order Quantities
For custom designs, PCB fabricators often impose higher minimum order quantities in the hundreds of boards. This ensures a reasonable production run cost. Smaller prototyping volumes typically cost more per board.
Standard published boards can be bought in lower quantities since fabrication setup is already covered.
So the minimum usable quantity should be evaluated when considering a new custom design. For lower volumes, standard boards may be more feasible.
5. Potential Vendor Lock-In
Once a custom PCB design is complete, you become reliant on that specific fabricator able to build those unique boards. This reduces flexibility to source from alternate suppliers, potentially leading to vendor lock-in.
Standard published boards offer more interchangeability between vendors.
Manufacturing and Testing Considerations
Fabricating and testing custom boards requires some unique processes. Here are considerations around manufacturability, assembly, and quality control.
Design for Manufacturing Guidelines
To ensure a smooth fabrication and assembly process for new PCB designs:
- Layouts should follow manufacturer design rules and capabilities. These cover trace spacing, hole sizes, annular rings, etc.
- Avoid unusually thick or thin boards. Stick to common 1.6mm thickness when possible.
- Use standard surface finishes and common lamination materials like FR-4.
- Utilize design features that aid manufacturability like chamfers, rounded pad corners, etc.
- Work with preferred component packages and lead styles suited to assembly methods.
- Provide sufficient test points for inspections and troubleshooting.
Qualification Testing
Since custom designs are unproven, additional qualification testing should be conducted:
- Simulation testing using thermal, power, and signal integrity analysis.
- Environmental stress testing for temperature, vibration, humidity, etc.
- Laboratory reliability testing like HALT/HASS, or accelerated lifetime testing.
- Sample functional testing under operational use conditions.
Premade published boards typically avoid extensive requalification testing since the design is already proven.
inspectability
Custom PCBs often require extra inspection steps:
- X-ray inspection to detect potential shorts, opens, and assembly flaws.
- High magnification inspection of trace spacing, hole annular rings, and etch quality.
- 0100 percentile in-circuit testing instead of just sampling.
Standard boards reused across programs have known good history and may just sample quality checks.
So custom boards demand increased front-end verification effort in order to certify the design.
Applications Suited for Each Approach
When is it best to use an off-the-shelf PCB versus developing a custom board? Here are typical scenarios suited for each approach.
Appropriate for Off-the-Shelf PCB Use
- Prototyping – Allows quick testing before custom design investment.
- Education/hobby – Quick start and lower skills needed.
- Low complexity circuits – Simpler I/O functions or breakout boards.
- Very high volume products – Amortizes down cost of pre-made boards.
- Resource limited projects – Faster and lower skill requirements.
- Applications with less critical PCB requirements.
Appropriate for Custom PCB Use
- Complex, dense circuits and multilayer boards.
- Size, space or shape constrained applications.
- Need for optimized electrical performance.
- RF, analog, power, or high speed digital circuits.
- Mission-critical reliability requirements.
- Medium/high mix volume production.
- Products where PCB is central to the functionality.
- Ability to amortize development costs over product lifetime.
In general, consider custom PCBs when the design demands or complexity are high, performance is critical, and volumes justify the investment. Premade boards excel at simplicity, low cost, and rapid prototyping.
Conclusion
In closing, developing custom tailored PCBs offers unparalleled design optimization at the expense of higher initial cost and lead time. The payoff comes from supporting innovative product functionality and industrialization. Off-the-shelf boards provide standardized, proven solutions at lower piece cost.
Engineers must weigh this trade-off between design flexibility and development risk/cost based on the specific product needs and constraints. Utilizing each approach where appropriate enables maximizing results.
With upfront planning and realistic budgeting, custom PCB development can successfully transform product concepts into fielded reality. Certain applications justify the extra effort to create boards that fully deliver features, performance and reliability.
Frequently Asked Questions
What are some tips for cost-optimizing custom PCB designs?
Some ways to reduce custom PCB costs include:
- Consolidating functionality to reduce component counts
- Eliminating unnecessary connectors or interfaces
- Using 2-4 layer boards instead of 6+ layers when possible
- Selecting larger package ICs over costly chip-scale parts
- Standardizing on common, high-volume lamination materials
- Allowing for moderate production tolerances
- Using a common PCB supplier to leverage panelization
What are the typical minimum order quantities for custom PCBs?
A sampling of minimum order volumes by fabrication stage:
- Prototyping: 10-25 boards
- Pre-production: 25-50 boards
- Initial production: 100-500 boards
- Mature production: 500-1000+ boards
Higher volumes give lower cost but require forecasts.
Should every new product design use a custom PCB?
Not necessarily – simpler or low complexity circuits may not require a full custom design. And very high volume commodity products favor existing published boards to reduce costs. Custom PCBs make sense when requirements warrant their capabilities.
How can I reduce risk on new custom PCB designs?
Strategies to reduce custom PCB development risk include:
- Thorough simulation, review, and early prototyping
- Qualification testing like HALT and environmental stress screening
- Incremental deployment and not overreaching on complexity
- Partnering with experienced, trusted PCB designers and fabricators
Why can custom PCBs enable miniaturization?
Techniques like HDI fabrication, thin cores, flexible boards, component embedding, and high density routing allow packing more functionality into less space – ideal for small product packaging.
Leave a Reply