Introduction to PCBs in Robotics
What are PCBs?
PCBs are thin boards made of insulating materials, such as fiberglass or plastic, with conductive pathways etched onto their surface. These conductive pathways, known as traces, connect various electronic components, such as microcontrollers, sensors, motors, and power supplies, to form a complete electronic circuit. PCBs provide a compact and organized way to assemble and connect these components, enabling the development of complex robotic systems.
The Role of PCBs in Robots
PCBs serve as the central nervous system of robots, facilitating communication and control between different subsystems. They allow for the integration of various sensors, actuators, and processing units, enabling robots to perceive their environment, make decisions, and execute actions. PCBs also provide a means for power distribution, ensuring that each component receives the appropriate voltage and current for optimal operation.
Types of PCBs used in Robotics
Single-sided PCBs
Single-sided PCBs have conductive traces on only one side of the board. They are the simplest and most cost-effective type of PCB, suitable for basic robotic applications with low complexity. Single-sided PCBs are commonly used in hobby robotics projects and educational kits.
Double-sided PCBs
Double-sided PCBs have conductive traces on both sides of the board, allowing for more complex circuit designs and higher component density. They offer better signal integrity and power distribution compared to single-sided PCBs. Double-sided PCBs are widely used in more advanced robotic systems, such as industrial robots and autonomous vehicles.
Multi-layer PCBs
Multi-layer PCBs consist of multiple layers of conductive traces sandwiched between insulating layers. They provide even greater circuit complexity and density than double-sided PCBs. Multi-layer PCBs are essential for high-performance robotic applications that require sophisticated signal routing, power management, and electromagnetic interference (EMI) shielding. They are commonly found in advanced robotics research and development.
Flexible PCBs
Flexible PCBs, also known as flex circuits, are made of thin, flexible materials that can bend and conform to various shapes. They are particularly useful in robotics applications where space is limited or where the PCB needs to fit into irregular spaces. Flexible PCBs are commonly used in wearable robots, soft robotics, and miniature robotic devices.
PCB Design Considerations for Robots
Component Selection
Choosing the right electronic components is crucial for the performance and reliability of robotic PCBs. Factors to consider include power requirements, operating voltages, current ratings, package sizes, and environmental factors such as temperature and vibration. It is important to select components that are compatible with each other and meet the specific requirements of the robotic application.
Signal Integrity
Ensuring signal integrity is critical in robotic PCBs to prevent signal distortion, crosstalk, and noise. Proper signal routing techniques, such as using appropriate trace widths, minimizing trace lengths, and implementing ground planes, help maintain signal quality. Additionally, techniques like impedance matching and termination can be employed to minimize reflections and ensure clean signal transmission.
Power Distribution
Efficient power distribution is essential for the stable operation of robotic systems. PCB designers must consider the power requirements of each component and design the power distribution network accordingly. This involves selecting appropriate Voltage Regulators, power management ICs, and decoupling capacitors to provide clean and stable power to all components. Proper grounding techniques, such as using star grounding or ground planes, help minimize ground loops and reduce noise.
Electromagnetic Compatibility (EMC)
Robotic PCBs must be designed with electromagnetic compatibility (EMC) in mind to ensure they do not interfere with other electronic devices and are not susceptible to external electromagnetic interference (EMI). EMC considerations include proper shielding, grounding, and filtering techniques. PCB designers may use techniques such as ground planes, shielded enclosures, and ferrite beads to mitigate EMI and ensure compliance with EMC standards.
Mechanical Considerations
PCBs in robots must be designed to withstand the mechanical stresses and vibrations encountered during operation. Proper mounting and support of components, as well as the use of strain relief techniques, help prevent component damage and ensure long-term reliability. Additionally, the PCB layout should consider the mechanical design of the robot, including the placement of connectors, switches, and sensors for optimal accessibility and functionality.
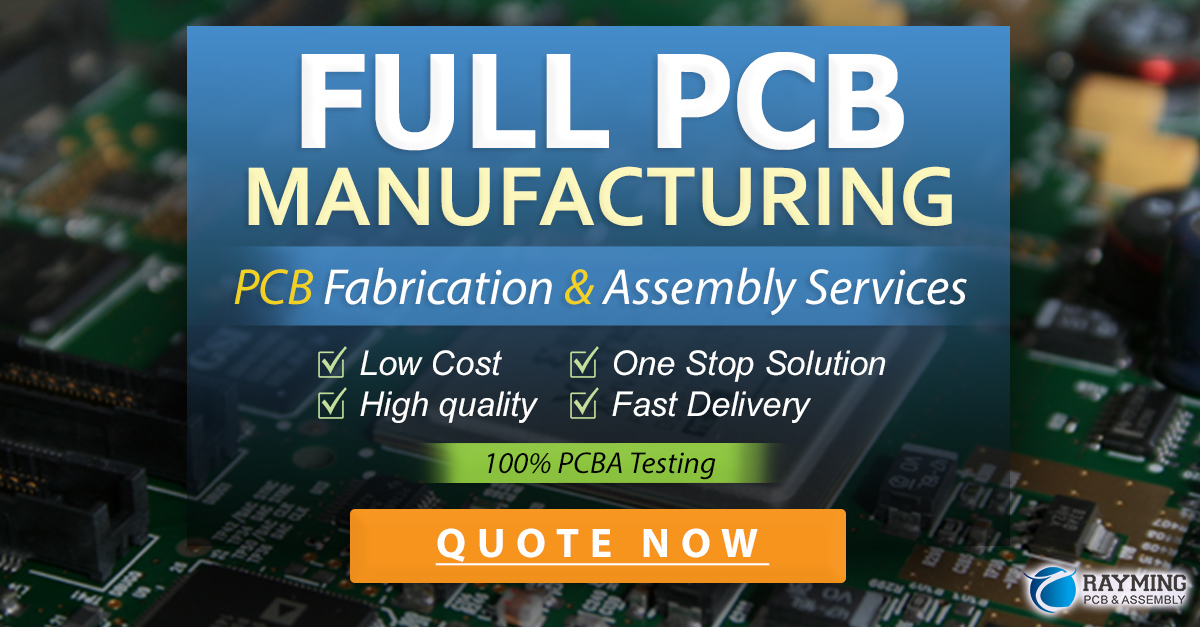
PCB Manufacturing Process for Robots
PCB Fabrication
The PCB fabrication process involves several steps to transform the PCB design into a physical board. It begins with the creation of a PCB layout file, which contains the information about the component placement, trace routing, and layer stackup. The layout file is used to generate gerber files, which are the industry-standard format for PCB manufacturing.
The gerber files are then sent to a PCB fabrication facility, where the actual manufacturing process takes place. The process typically involves the following steps:
-
Substrate preparation: The PCB substrate, usually made of fiberglass or other insulating materials, is cut to the desired size and shape.
-
Copper lamination: Thin layers of copper foil are laminated onto the substrate using heat and pressure.
-
Photoresist application: A light-sensitive photoresist is applied to the copper layers.
-
Exposure and development: The photoresist is exposed to UV light through a photomask, which contains the PCB pattern. The exposed areas of the photoresist are then removed during the development process.
-
Etching: The exposed copper areas are etched away using a chemical solution, leaving behind the desired conductive traces.
-
Drill holes: Holes are drilled through the PCB for component mounting and inter-layer connections.
-
Plating: The drilled holes are plated with copper to establish electrical connections between layers.
-
Solder mask application: A protective solder mask is applied to the PCB surface, leaving only the exposed pads for component soldering.
-
Silkscreen printing: Text, symbols, and component designators are printed onto the PCB surface using silkscreen printing.
-
Surface finish: A surface finish, such as HASL (Hot Air Solder Leveling) or ENIG (Electroless Nickel Immersion Gold), is applied to the exposed pads to prevent oxidation and enhance solderability.
PCB Assembly
Once the PCB fabrication is complete, the next step is PCB assembly, where electronic components are mounted onto the board. The assembly process can be done manually for small-scale or prototype production, but automated assembly methods are more common for larger volumes.
The most common automated assembly method is surface mount technology (SMT), which involves the following steps:
-
Solder paste application: Solder paste, a mixture of tiny solder balls and flux, is applied to the component pads using a stencil or screen printing process.
-
Component placement: SMT components are picked and placed onto the solder paste-covered pads using automated pick-and-place machines.
-
Reflow soldering: The PCB with the placed components is passed through a reflow oven, where the solder paste melts and forms a permanent electrical and mechanical connection between the components and the PCB.
-
Inspection: The assembled PCB undergoes visual and automated optical inspection (AOI) to ensure proper component placement and solder joint quality.
-
Through-hole assembly: If the PCB contains through-hole components, they are manually inserted and soldered onto the board after the SMT process.
-
Testing: The assembled PCB undergoes various functional and quality control tests to verify its performance and reliability.
Challenges and Future Trends in Robotic PCBs
Miniaturization
As robots become smaller and more compact, there is a growing demand for miniaturized PCBs that can fit into tight spaces. This requires advanced PCB design techniques, such as high-density interconnect (HDI) and embedded components, to achieve higher component density and smaller form factors. Miniaturized PCBs also pose challenges in terms of signal integrity, power management, and thermal dissipation, requiring careful design considerations.
Flexibility and Stretchability
The emergence of soft robotics and wearable robots has led to the development of flexible and stretchable PCBs. These PCBs can conform to non-planar surfaces and withstand repeated bending and stretching without losing functionality. Flexible and stretchable PCBs are made using special materials, such as polyimide or elastomeric substrates, and employ novel fabrication techniques like inkjet printing or screen printing of conductive inks.
Integration of Sensors and Actuators
As robots become more autonomous and intelligent, there is a growing trend towards the integration of sensors and actuators directly onto PCBs. This allows for more compact and efficient robotic systems, reducing the need for external wiring and connectors. Techniques such as printed electronics and MEMS (Microelectromechanical Systems) technology enable the fabrication of sensors and actuators directly on PCBs, leading to highly integrated and intelligent robotic modules.
Advanced Materials
Researchers are exploring the use of advanced materials in robotic PCBs to enhance their performance and functionality. For example, the use of carbon nanotubes or graphene-based conductive inks can improve the electrical and thermal properties of PCBs. Additionally, the incorporation of smart materials, such as shape memory alloys or piezoelectric polymers, can enable the development of self-reconfigurable or self-healing PCBs for robots operating in challenging environments.
Frequently Asked Questions (FAQ)
-
Q: What is the difference between a single-sided and double-sided PCB in robotics?
A: Single-sided PCBs have conductive traces on only one side of the board, while double-sided PCBs have traces on both sides. Double-sided PCBs offer more complex circuit designs, better signal integrity, and higher component density compared to single-sided PCBs. They are commonly used in more advanced robotic systems. -
Q: Why are flexible PCBs important in robotics?
A: Flexible PCBs are important in robotics because they can bend and conform to various shapes, making them suitable for applications where space is limited or where the PCB needs to fit into irregular spaces. They are commonly used in wearable robots, soft robotics, and miniature robotic devices. -
Q: What are some key considerations when designing PCBs for robots?
A: When designing PCBs for robots, some key considerations include component selection, signal integrity, power distribution, electromagnetic compatibility (EMC), and mechanical factors. Designers must choose compatible components, ensure proper signal routing, provide stable power, mitigate EMI, and consider the mechanical stresses and vibrations the PCB will encounter during operation. -
Q: What is the role of solder paste in the PCB assembly process?
A: Solder paste, a mixture of tiny solder balls and flux, is applied to the component pads during the PCB assembly process. It serves as a temporary adhesive to hold the components in place and forms a permanent electrical and mechanical connection between the components and the PCB when heated during the reflow soldering process. -
Q: What are some future trends in robotic PCBs?
A: Some future trends in robotic PCBs include miniaturization, flexibility and stretchability, integration of sensors and actuators directly onto PCBs, and the use of advanced materials such as carbon nanotubes or graphene-based conductive inks. These trends aim to enhance the performance, functionality, and adaptability of robotic systems.
Conclusion
PCBs play a vital role in the development and functionality of robots, serving as the backbone of their electronic systems. From single-sided to multi-layer and flexible PCBs, various types of PCBs are employed in robotics based on the specific requirements of the application. Designing PCBs for robots involves careful consideration of component selection, signal integrity, power distribution, EMC, and mechanical factors to ensure optimal performance and reliability.
The PCB manufacturing process, including fabrication and assembly, is a critical step in bringing robotic designs to life. As robots continue to evolve and become more advanced, PCB technologies are also advancing to meet the demands of miniaturization, flexibility, sensor integration, and the use of advanced materials.
By understanding the significance of PCBs in robotics and staying updated with the latest trends and technologies, engineers and researchers can push the boundaries of what is possible in the field of robotics. The continued development of innovative PCB solutions will undoubtedly shape the future of robotics, enabling the creation of more intelligent, efficient, and adaptable robotic systems.
Leave a Reply