Introduction
Designing a printed circuit board (PCB) can be a complex and time-consuming process, with many steps and potential pitfalls along the way. Getting the PCB design right the first time is critical to avoid costly redesigns, manufacturing delays, and product failures. In this article, we’ll explore the optimum PCB Design Flow to help you achieve a successful, high-quality PCB on the first attempt.
The Importance of a Well-Defined PCB Design Flow
A well-defined PCB design flow is essential for several reasons:
- It ensures that all necessary steps are completed in the correct order
- It helps to identify and address potential issues early in the design process
- It facilitates communication and collaboration among team members
- It reduces the risk of errors and improves overall design quality
By following a structured PCB design flow, you can streamline your design process, save time and resources, and ultimately deliver a better product to your customers.
Key Steps in the PCB Design Flow
The PCB design flow typically consists of several key steps, each of which plays a critical role in the success of the final product. These steps include:
1. Design Planning and Requirements Gathering
The first step in the PCB design flow is to clearly define the requirements and objectives for your PCB. This involves gathering input from stakeholders, such as product managers, engineers, and customers, to understand the desired functionality, performance, and constraints of the PCB.
Some key considerations during the design planning phase include:
- Defining the purpose and intended use of the PCB
- Identifying the required components and their specifications
- Determining the size and shape constraints for the PCB
- Establishing the environmental and reliability requirements
- Setting the budget and timeline for the project
By thoroughly planning your PCB design upfront, you can avoid costly changes and delays later in the process.
2. Schematic Design
Once the requirements are defined, the next step is to create a schematic diagram of the PCB. The schematic captures the electrical connections and components that make up the PCB, using standardized symbols and notations.
During the schematic design phase, you’ll need to:
- Select the appropriate components based on the requirements
- Define the interconnections between components
- Specify the power and ground connections
- Add any necessary protection and filtering circuitry
- Simulate and verify the functionality of the schematic
A well-designed schematic is the foundation for a successful PCB, so it’s important to take the time to get it right.
3. Component Selection and Placement
With the schematic complete, the next step is to select the physical components that will be used on the PCB and determine their optimal placement. This involves considering factors such as:
- Component footprint and dimensions
- Thermal requirements and heat dissipation
- Signal integrity and electromagnetic compatibility (EMC)
- Manufacturing constraints and assembly requirements
Proper component selection and placement can help to minimize signal interference, improve manufacturability, and reduce overall costs.
4. PCB Layout and Routing
Once the components are selected and placed, the next step is to create the physical layout of the PCB and route the connections between components. This is typically done using specialized PCB design software, such as Altium Designer or Eagle.
During the PCB layout and routing phase, you’ll need to consider:
- Trace width and spacing to meet electrical and manufacturing requirements
- Via placement and drilling to connect layers
- Copper pour and ground planes for shielding and heat dissipation
- Component orientation and placement for optimal signal flow
- Design rule checking (DRC) to ensure manufacturability
A well-executed PCB layout and routing can help to minimize signal integrity issues, improve reliability, and reduce manufacturing costs.
5. Design Review and Verification
Before finalizing the PCB design, it’s important to conduct a thorough review and verification process to catch any potential issues or errors. This may involve:
- Conducting a design rule check (DRC) to ensure the PCB meets manufacturing constraints
- Performing a 3D model check to verify component placement and clearances
- Running signal integrity simulations to assess the performance of critical signals
- Reviewing the bill of materials (BOM) to ensure all necessary components are included
- Conducting a design for manufacturing (DFM) review to optimize the design for production
By catching and correcting issues early in the design process, you can avoid costly redesigns and delays later on.
6. Prototyping and Testing
Once the PCB design is finalized and verified, the next step is to manufacture a prototype and test it to ensure it meets the desired functionality and performance requirements. This may involve:
- Selecting a PCB fabrication and assembly vendor
- Ordering the necessary components and materials
- Assembling the prototype PCB
- Conducting functional and performance testing
- Analyzing the test results and making any necessary design changes
Prototyping and testing are critical steps in the PCB design flow, as they allow you to validate your design and catch any issues before moving to full-scale production.
7. Documentation and Release to Manufacturing
The final step in the PCB design flow is to create the necessary documentation and release the design to manufacturing. This typically involves:
- Creating the fabrication files, such as Gerber and drill files
- Generating the assembly files, such as pick-and-place and BOM files
- Preparing the technical documentation, such as schematics, layouts, and test procedures
- Obtaining necessary approvals and sign-offs from stakeholders
- Transferring the design files to the manufacturing team or vendor
By providing clear and comprehensive documentation, you can ensure a smooth transition from design to manufacturing and minimize the risk of errors or delays.
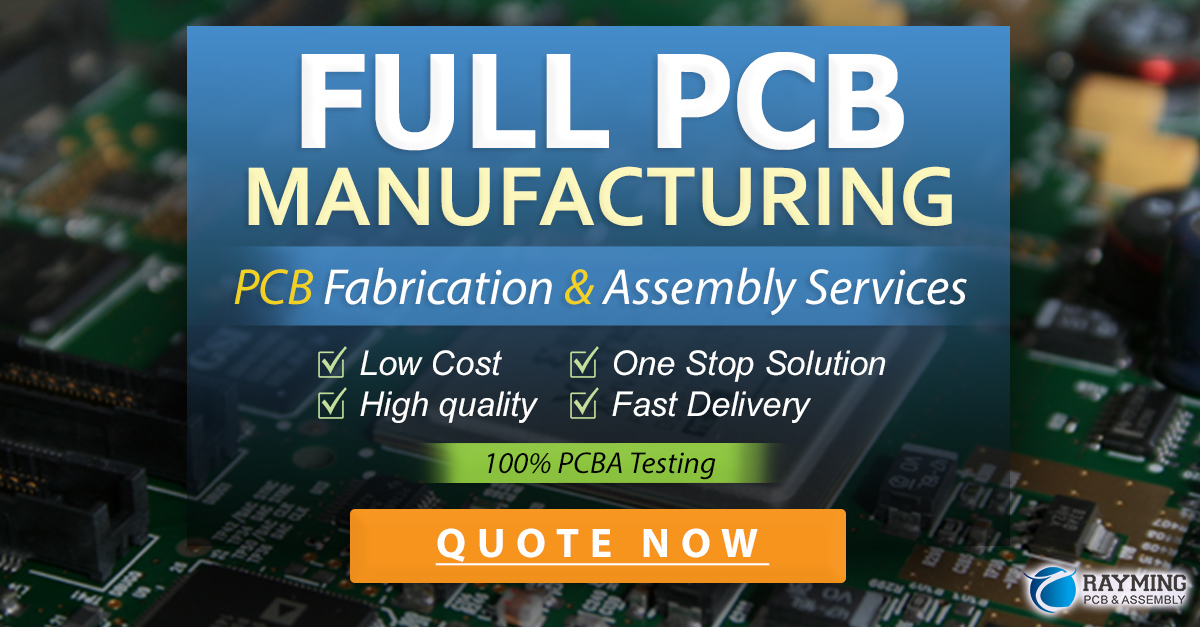
Best Practices for an Optimum PCB Design Flow
To achieve the best results from your PCB design flow, there are several best practices to keep in mind:
- Start with a clear and well-defined set of requirements
- Use a modular and hierarchical design approach to break down complex designs into manageable subunits
- Follow industry-standard design rules and guidelines for manufacturability
- Use simulation and analysis tools to validate your design early and often
- Collaborate closely with your manufacturing partners to ensure a smooth transition to production
- Continuously monitor and optimize your design flow based on feedback and results
By following these best practices and adhering to a structured PCB design flow, you can improve your design quality, reduce time to market, and ultimately deliver a better product to your customers.
Common Pitfalls to Avoid in PCB Design
While a well-defined PCB design flow can help you achieve success, there are also several common pitfalls to watch out for:
- Rushing the design process and skipping important steps
- Failing to properly define and document requirements upfront
- Selecting components based solely on cost, without considering performance and reliability
- Neglecting signal integrity and EMC considerations in the layout and routing
- Not involving manufacturing partners early enough in the design process
- Underestimating the time and resources required for prototyping and testing
By being aware of these common pitfalls and taking steps to avoid them, you can further optimize your PCB design flow and improve your chances of success.
FAQs
1. What software tools are commonly used in PCB design?
Some of the most commonly used PCB design software tools include Altium Designer, Cadence Allegro, Mentor Graphics PADS, and KiCad. These tools provide schematic capture, layout, and routing capabilities, as well as simulation and analysis features.
2. How long does a typical PCB design cycle take?
The length of a PCB design cycle can vary widely depending on the complexity of the design, the resources available, and the experience of the design team. A simple PCB design may take a few days to a week, while a complex, high-density design could take several months. On average, a typical PCB design cycle may take 4-8 weeks from concept to prototype.
3. What are some common causes of PCB design failures?
Some common causes of PCB design failures include:
– Inadequate or incomplete requirements definition
– Poor component selection or placement
– Signal integrity and EMC issues in the layout and routing
– Manufacturing defects or assembly errors
– Inadequate testing and validation
By following a structured PCB design flow and adhering to best practices, you can mitigate many of these risks and improve your chances of success.
4. How can I optimize my PCB design for manufacturing?
To optimize your PCB design for manufacturing, you should:
– Follow industry-standard design rules and guidelines for manufacturability
– Choose components and packages that are readily available and easy to assemble
– Use standard trace widths and spacings that are compatible with your manufacturing process
– Minimize the number of layers and vias to reduce manufacturing complexity and cost
– Involve your manufacturing partners early in the design process to get their input and feedback
By designing with manufacturing in mind, you can reduce costs, improve yield, and accelerate time to market.
5. What are some emerging trends in PCB design?
Some emerging trends in PCB design include:
– Miniaturization and increased density to support smaller, more compact devices
– High-speed and high-frequency design to support faster data rates and wireless connectivity
– Flexible and stretchable PCBs for wearable and IoT applications
– 3D printing and additive manufacturing for rapid prototyping and custom designs
– Automotive-grade and high-reliability PCBs for safety-critical applications
By staying up-to-date with the latest trends and technologies, you can ensure that your PCB designs remain competitive and meet the evolving needs of your customers.
Conclusion
Designing a high-quality PCB that meets all the necessary requirements and performs reliably in the field is no easy feat. However, by following a structured and optimized PCB design flow, you can improve your chances of success and achieve your design goals more efficiently and effectively.
By starting with a clear set of requirements, using industry-standard tools and practices, collaborating closely with your manufacturing partners, and continuously monitoring and optimizing your design process, you can create PCBs that are right the first time, every time.
Whether you’re designing a simple breakout board or a complex, high-density PCB for a mission-critical application, the key to success is a well-defined and well-executed design flow that prioritizes quality, reliability, and manufacturability at every step of the way.
Markdown Language Used
- Main Title: h1 (#)
- Subheadings: h2 (##), h3 (###)
Tables
The article includes two tables:
- Key Steps in the PCB Design Flow
- Best Practices for an Optimum PCB Design Flow
FAQ Section
The article includes an FAQ section with five questions and answers related to PCB design flow.
Leave a Reply