What is AOI Inspection?
AOI (Automated Optical Inspection) is a critical process in the manufacturing of printed circuit boards (PCBs) and other electronic components. It involves using specialized cameras and image processing software to automatically inspect the quality of manufactured products for defects, such as missing components, incorrect component placement, or soldering issues. AOI inspection ensures that products meet the required quality standards before they are shipped to customers, reducing the risk of defective products reaching the market.
Key Benefits of AOI Inspection
- Increased Efficiency: AOI systems can inspect products much faster than manual inspection, allowing for higher throughput and reduced production time.
- Improved Accuracy: Automated inspection eliminates human error and ensures consistent, reliable results.
- Cost Savings: By catching defects early in the manufacturing process, AOI inspection reduces the cost of rework and scrap.
- Enhanced Quality: AOI inspection helps maintain high product quality standards, improving customer satisfaction and brand reputation.
How Does AOI Inspection Work?
AOI inspection systems typically consist of the following components:
- Cameras: High-resolution cameras capture images of the product from various angles.
- Lighting: Proper lighting is essential for capturing clear, detailed images of the product.
- Image Processing Software: Sophisticated algorithms analyze the captured images and compare them to a reference model to identify defects.
- Conveyor System: A conveyor moves the products through the inspection area, ensuring consistent positioning and smooth operation.
The AOI Inspection Process
- Product Placement: The product is placed on the conveyor and moved into the inspection area.
- Image Capture: Cameras capture high-resolution images of the product from multiple angles.
- Image Analysis: The image processing software analyzes the captured images, comparing them to a reference model to identify any defects or irregularities.
- Defect Classification: If defects are detected, the software classifies them according to predefined categories, such as missing components, incorrect placement, or soldering issues.
- Reporting: The system generates a report detailing the inspection results, including the type and location of any defects found.
Types of AOI Inspection Systems
There are two main types of AOI inspection systems:
-
2D AOI Systems: These systems use conventional 2D cameras to capture images of the product from a top-down view. They are suitable for inspecting flat, planar surfaces and are commonly used for PCB inspection.
-
3D AOI Systems: These systems use specialized 3D cameras or multiple 2D cameras to capture images from different angles, allowing for the inspection of three-dimensional features such as component height and solder joint quality. 3D AOI systems are becoming increasingly popular due to their ability to detect a wider range of defects.
Comparison of 2D and 3D AOI Systems
Feature | 2D AOI Systems | 3D AOI Systems |
---|---|---|
Inspection Capability | Planar surfaces | Planar and three-dimensional features |
Defect Detection | Limited to 2D defects | Can detect 2D and 3D defects |
Cost | Generally lower cost | Higher cost due to more advanced technology |
Complexity | Simpler setup and operation | More complex setup and operation |
Suitability | PCB inspection, flat surfaces | PCB inspection, component height, solder joint quality |
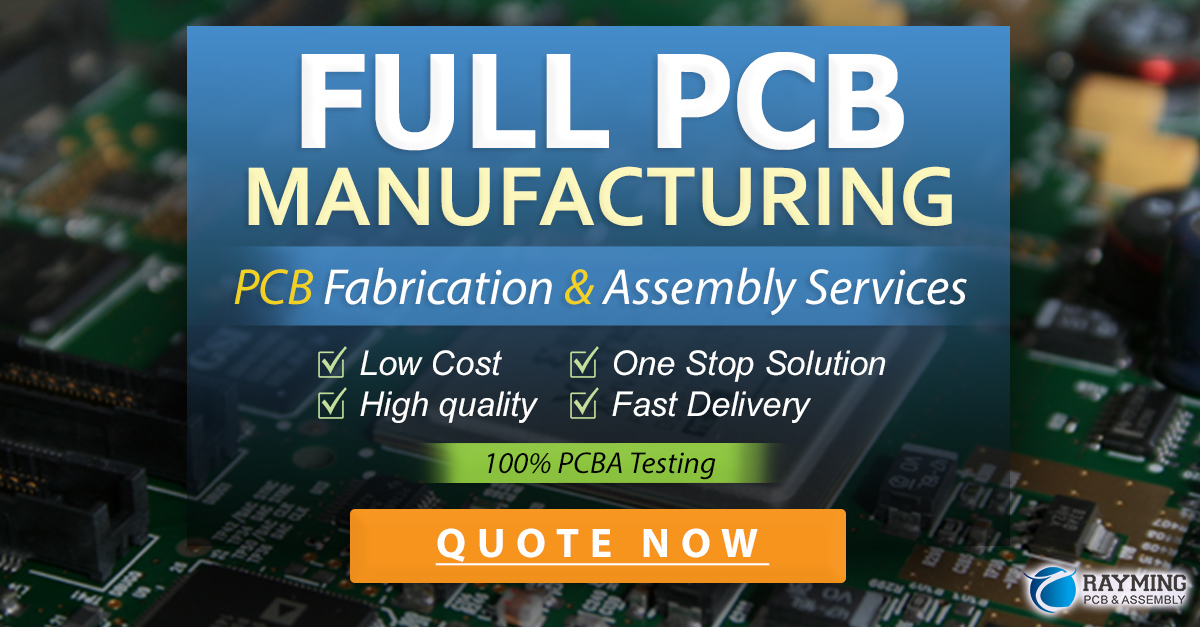
Implementing AOI Inspection in Your Manufacturing Process
To successfully implement AOI inspection in your manufacturing process, consider the following steps:
- Define Inspection Requirements: Determine the specific quality standards and defect types that need to be inspected.
- Choose the Right AOI System: Select an AOI system that meets your inspection requirements and budget, considering factors such as 2D vs. 3D capabilities, speed, and accuracy.
- Develop Inspection Programs: Create inspection programs that define the reference model, defect categories, and acceptance criteria for each product.
- Integrate with Existing Processes: Integrate the AOI system into your existing manufacturing process, ensuring smooth material flow and minimal disruption.
- Train Operators: Provide training to operators on the proper use and maintenance of the AOI system.
- Monitor and Optimize: Continuously monitor the performance of the AOI system and optimize inspection programs as needed to improve defect detection and reduce false positives.
Advantages of AOI Inspection Over Manual Inspection
AOI inspection offers several advantages over traditional manual inspection methods:
- Consistency: AOI systems provide consistent, reliable results, eliminating the variability associated with human inspectors.
- Speed: AOI systems can inspect products much faster than human inspectors, enabling higher production throughput.
- 24/7 Operation: AOI systems can operate continuously, allowing for inspection during off-hours and reducing the need for manual labor.
- Objective Results: AOI inspection provides objective, quantifiable results, making it easier to track quality trends and identify areas for improvement.
Comparison of AOI and Manual Inspection
Factor | AOI Inspection | Manual Inspection |
---|---|---|
Speed | High | Low |
Consistency | High | Low |
Accuracy | High | Moderate |
Cost | Higher initial investment | Lower initial investment |
Scalability | Easily scalable | Limited by available labor |
Subjectivity | Objective results | Subjective results |
Common Defects Detected by AOI Inspection
AOI inspection can detect a wide range of defects, including:
- Missing Components: Components that are absent from the product.
- Incorrect Components: Components that are the wrong type or value.
- Misaligned Components: Components that are not placed correctly on the board.
- Solder Defects: Issues with solder joints, such as bridging, insufficient solder, or cold joints.
- Polarity Defects: Components that are installed with the incorrect polarity.
- Dimensional Defects: Issues with the size or shape of components or features.
Examples of Defects and Their Potential Impact
Defect | Potential Impact |
---|---|
Missing Component | Product malfunction, reduced reliability |
Incorrect Component | Unexpected behavior, product failure |
Misaligned Component | Short circuits, interference with other components |
Solder Bridge | Short circuits, product malfunction |
Insufficient Solder | Poor electrical connection, reduced reliability |
Reversed Polarity | Product malfunction, damage to components |
Limitations of AOI Inspection
While AOI inspection is a powerful tool for quality control, it does have some limitations:
- Limited Subsurface Inspection: AOI systems cannot inspect features below the surface of the product, such as internal layers of a PCB.
- False Positives and False Negatives: AOI systems may occasionally identify defects that are not actually present (false positives) or miss defects that are present (false negatives).
- Reflective Surfaces: Highly reflective surfaces can be challenging for AOI systems to inspect accurately.
- Dependence on Reference Model: AOI inspection relies on a reference model for comparison, so any errors in the reference model can lead to incorrect results.
The Future of AOI Inspection
As technology continues to advance, AOI inspection systems are becoming more sophisticated and capable. Some of the emerging trends in AOI inspection include:
- Machine Learning and AI: The integration of machine learning and artificial intelligence algorithms is enabling AOI systems to learn and adapt, improving defect detection and reducing false positives.
- Inline vs. Offline Inspection: Inline AOI systems, which inspect products directly on the production line, are becoming more common, providing real-time feedback and reducing the need for offline inspection.
- Integration with Other Technologies: AOI inspection is being combined with other quality control technologies, such as X-ray inspection and electrical testing, to provide a more comprehensive view of product quality.
Frequently Asked Questions (FAQ)
-
Q: What is the difference between AOI and visual inspection?
A: AOI (Automated Optical Inspection) uses cameras and image processing software to automatically inspect products, while visual inspection relies on human inspectors to manually examine products for defects. -
Q: Can AOI inspection completely replace manual inspection?
A: While AOI inspection can significantly reduce the need for manual inspection, it may not completely replace it in all cases. Some products may require additional manual inspection for certain defect types or to verify the results of the AOI system. -
Q: How much does an AOI inspection system cost?
A: The cost of an AOI inspection system can vary widely depending on factors such as the type of system (2D or 3D), the size and complexity of the products being inspected, and the level of automation required. Entry-level systems can start at around $50,000, while more advanced systems can cost several hundred thousand dollars. -
Q: How long does it take to set up an AOI inspection system?
A: The time required to set up an AOI inspection system depends on the complexity of the system and the products being inspected. Simple systems may be set up in a few days, while more complex systems can take several weeks to fully integrate into the production process. -
Q: Can AOI inspection be used for products other than PCBs?
A: Yes, AOI inspection can be used for a wide range of products, including semiconductors, automotive parts, medical devices, and consumer electronics. The specific application will determine the type of AOI system and inspection requirements needed.
Leave a Reply