What is the Production-Prototype Gap?
The production-prototype gap refers to the differences in quality, performance, and manufacturability between a prototype version of a product and the final production version intended for end users. Prototypes are early sample, model, or release of a product built to test a concept or process. The goal of a prototype is to test and validate ideas and product designs to enhance precision by system analysts and users. Due to differences in materials, processes, and scale, prototypes often differ significantly in quality from final production output.
Prototypes may be made with different manufacturing methods than the final product, use lower-grade materials, have looser tolerances, and go through less rigorous testing. This is acceptable for a prototype since the intent is to rapidly iterate designs and incorporate feedback, without investing in full production tooling.
However, when moving from prototype to production, companies need to bridge this gap in quality to deliver a product that meets all requirements and specifications. Failure to address the production-prototype gap can lead to delays, additional costs, unsatisfied customers, and potentially a product recall.
Key Differences Between Prototypes and Production Parts
Characteristic | Prototype | Production |
---|---|---|
Intent | Proof of concept, testing, validation | End use |
Materials | May use different materials than production | Uses final production materials |
Manufacturing processes | 3D printing, CNC Machining, hand assembly | Injection molding, casting, automated assembly |
Tolerances | Looser tolerances acceptable | Tight tolerances required for fit and function |
Quality control | Limited testing and QC | Rigorous testing and QC |
Lead time | Emphasis on speed | Emphasis on efficiency and cost |
Quantities | Low volume | High volume |
Materials
Prototypes are often built using materials that are easy to work with and iterate on, such as 3D printing filaments, soft tooling materials, or easily machined metals and plastics. The focus is on functionality over long-term durability.
In contrast, production parts use the final specified materials which are selected for their properties, cost, and compatibility with high volume manufacturing processes. For example, a plastic part may be 3D printed in ABS for prototyping but injection molded using a glass-filled nylon for production.
Manufacturing Processes
Building prototypes typically involves manual processes and general purpose equipment for flexibility, such as 3D printers, CNC machines, and hand assembly. Prototypes are often built by engineers or technicians.
Production parts are made using processes optimized for efficiency, consistency, and volume, such as injection molding, die casting, stamping, and automated assembly. Dedicated equipment and tooling is developed for each part and the parts are made by skilled operators.
Tolerances
Tolerances, or the allowable degree of variation in a part’s dimensions, are often loosened for prototypes. The intent is to verify form, fit, and function, but some deviation is acceptable.
Production parts need to have tight tolerances to ensure proper operation, performance, and the ability to be assembled consistently. There are usually specific tolerance callouts on the drawings for production parts.
Quality Control
Since prototypes are built to test and validate designs, they go through a less rigorous quality control process. Flaws or deviations are noted but may be acceptable at this stage.
Production parts go through extensive QC checks to ensure they meet all specifications and requirements. This may include automated vision systems, gauging, functional testing, and statistical process control. Any parts that fail QC are scrapped or reworked.
Lead Time and Cost
The emphasis for prototypes is on rapidly iterating and validating designs. Speed is prioritized over cost and some inefficiency is acceptable to get prototypes in the hands of stakeholders quickly for feedback. Prototype Costs are higher on a per-part basis but lower in absolute terms than production.
In production, the focus shifts to efficiency and cost reduction. More time is spent upfront to optimize designs for manufacturing and put cost-effective, repeatable processes in place. Lead times are longer but per-part costs are minimized through economies of scale. The high volumes amortize the upfront engineering and tooling costs.
Strategies for Bridging the Gap
Design for Manufacturing (DFM)
One of the most effective ways to bridge the production-prototype gap is to consider manufacturing early in the design process. Known as Design for Manufacturing (DFM), this approach involves designing parts with the production processes in mind from the start.
DFM principles include:
– Simplifying designs to reduce part count and complexity
– Avoiding unnecessary features, tight tolerances, and cosmetic finishes
– Designing parts to be easily fabricated and assembled with existing equipment and processes
– Standardizing materials, components, and fasteners
– Considering the capabilities and limitations of the intended manufacturing processes
By involving manufacturing engineers early and designing with production in mind, companies can smooth the transition from prototype to production and minimize redesign.
Rapid Prototyping with Production Intent
Another strategy is to use rapid prototyping techniques, but with as much production intent as possible. This means using the actual production materials and processes where feasible for prototypes.
For example, if a part will eventually be injection molded, try to 3D print it using the same material that will be used in production. Or machine it from the same plastic. This provides a more representative prototype and validates the material early.
Similarly, if a part will be CNC machined in production, use the same CAM program and tool paths for the prototype parts. This will identify any manufacturability issues and provide a better estimate of cycle times and costs.
The more the prototype can resemble the intended production part in material, process, and specification, the smaller the gap will be.
Rigorous Testing and Validation
A comprehensive testing and validation plan is essential for identifying and closing gaps between prototype and production quality. This should include:
- Material testing to ensure the selected materials meet all performance and durability requirements
- Dimensional validation using precise measurement equipment to verify that parts meet all specified tolerances
- Functional testing to simulate real-world use cases and environmental conditions
- Reliability testing to ensure the product will perform over its intended lifetime
- Manufacturability studies to validate that the designs can be consistently and efficiently produced at scale
Rigorous testing provides data to identify areas where the prototype deviates from the production intent and guide refinements to close those gaps.
Pilot Production Runs
Before ramping into full production, it’s often prudent to run smaller pilot production runs. These use the final production processes, materials, and equipment, but at a smaller scale.
Pilot runs serve several purposes:
– Validate that the production processes are capable of consistently delivering parts that meet all specifications
– Provide an opportunity for operators to get familiar with the new parts and processes
– Act as a trial run for the full QC and testing procedures
– Help identify any remaining issues or risks before full-scale commitment
Pilot runs provide a final check that the product is ready for primetime and that the production-prototype gap has been fully closed. They are an essential step for any critical or complex New Product Introduction.
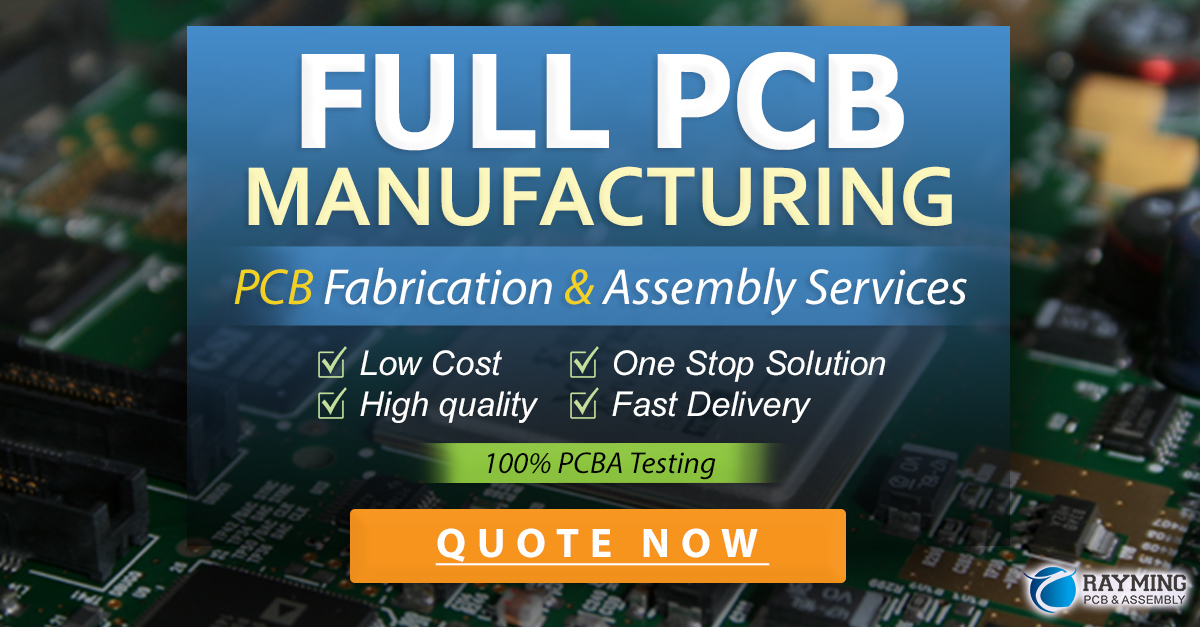
FAQ
What is the difference between a prototype and a production part?
A prototype is an early sample, model, or release of a product built to test a concept or process. It may be made with different materials and methods than the final production version. A production part is the final, finished good as it will be provided to the end customer. It uses the specified materials, is made with the production processes, and meets all quality requirements.
Why are prototypes often lower quality than production parts?
Prototypes are often lower quality because they are built quickly to validate designs, using easier to work with materials and more manual processes. The focus is on speed and flexibility over final quality and durability. Prototypes also go through less rigorous testing and quality control compared to production parts.
What problems can arise from the production-prototype gap?
If the gap between prototype and production quality is not addressed, several issues can arise:
– The final product may not meet performance or durability requirements
– Fit and interchangeability issues can occur, leading to assembly problems
– Higher than expected production costs or longer lead times
– Customers may receive inferior products, damaging brand reputation
– In extreme cases, a full product recall may be necessary
How can the production-prototype gap be minimized?
Strategies to minimize the gap include:
– Designing products with manufacturing in mind from the start (Design for Manufacturing)
– Using production materials and processes for prototype parts where possible
– Implementing rigorous testing and validation plans to identify and close gaps
– Running pilot production before full-scale ramp-up
At what stage should production considerations be incorporated into product development?
Production considerations should be incorporated as early as possible in the design process. The earlier manufacturing is involved, the more efficiently the product can be designed for production, minimizing late-stage redesign. Early collaboration between design and manufacturing engineers is key to a smooth transition from prototype to production.
Leave a Reply