What is PCB Tenting?
PCB tenting, also known as via tenting or tented vias, is a process used in the manufacturing of printed circuit boards (PCBs) where the drilled holes (vias) on the board are covered with a thin layer of solder mask material. This technique is used to protect the vias from contamination, improve the structural integrity of the board, and enhance its overall appearance.
Why is PCB Tenting Important?
PCB tenting plays a crucial role in the performance and longevity of a printed circuit board. Here are some of the key reasons why PCB tenting is essential:
-
Protection from Contamination: Tenting the vias prevents foreign particles, such as dust, dirt, and moisture, from entering the holes and causing short circuits or corrosion. This is particularly important in harsh industrial environments where PCBs are exposed to various contaminants.
-
Improved Structural Integrity: Covering the vias with solder mask material strengthens the board by providing additional support around the drilled holes. This reduces the risk of mechanical damage, such as cracks or breakages, especially during the assembly process or when the board is subjected to vibrations or shocks.
-
Enhanced Aesthetics: Tented vias create a cleaner and more uniform appearance on the surface of the PCB. This is particularly desirable for high-end electronic products where visual appeal is important.
-
Better Solderability: Tenting the vias prevents solder from flowing into the holes during the soldering process. This ensures that the components are properly soldered to the pads, reducing the risk of poor connections or solder bridges.
-
Increased Manufacturing Efficiency: PCB tenting simplifies the assembly process by eliminating the need for additional steps, such as plugging the vias or applying conformal coating. This saves time and reduces manufacturing costs.
Types of PCB Tenting
There are two main types of PCB tenting: full tenting and partial tenting.
Full Tenting
Full tenting, also known as complete tenting, involves covering the entire surface of the via with solder mask material. This provides maximum protection against contamination and enhances the structural integrity of the board. Full tenting is commonly used in applications where high reliability and durability are critical, such as in aerospace, military, and medical equipment.
Partial Tenting
Partial tenting, also referred to as semi-tenting or half-tenting, involves covering only a portion of the via with solder mask material. This is typically done by applying the solder mask to the top and bottom surfaces of the board, leaving the walls of the via exposed. Partial tenting is often used in applications where electrical testing or probing of the vias is required, such as in prototype development or debugging.
Here’s a table comparing the characteristics of full tenting and partial tenting:
Characteristic | Full Tenting | Partial Tenting |
---|---|---|
Protection | Maximum | Moderate |
Structural Integrity | High | Medium |
Aesthetics | Excellent | Good |
Solderability | Excellent | Good |
Manufacturing Efficiency | High | Medium |
Electrical Testing | Not Possible | Possible |
PCB Tenting Process
The PCB tenting process involves several steps, which are typically carried out during the solder mask application stage of PCB manufacturing. Here’s an overview of the process:
-
Via Drilling: The first step is to drill the vias into the PCB substrate according to the design specifications. The size and location of the vias are determined by the circuit layout and the components that will be mounted on the board.
-
Cleaning: After drilling, the board is cleaned to remove any debris or contaminants that may have accumulated during the drilling process. This is usually done using a chemical cleaning agent or a mechanical cleaning method, such as brushing or air blasting.
-
Solder Mask Application: The next step is to apply the solder mask material to the surface of the board. This is typically done using a screen printing or photoimaging process, depending on the desired level of precision and the type of solder mask being used.
-
Tenting: During the solder mask application process, the vias are tented by covering them with the solder mask material. This can be done either by fully covering the vias (full tenting) or by partially covering them (partial tenting), depending on the specific requirements of the application.
-
Curing: After the solder mask has been applied and the vias have been tented, the board is cured to harden the solder mask material. This is typically done using a combination of heat and ultraviolet (UV) light exposure, which causes the solder mask to polymerize and form a solid, protective layer over the surface of the board.
-
Inspection: Finally, the tented PCB is inspected to ensure that the vias have been properly covered and that there are no defects or irregularities in the solder mask coverage. This is usually done using automated optical inspection (AOI) equipment or manual visual inspection.
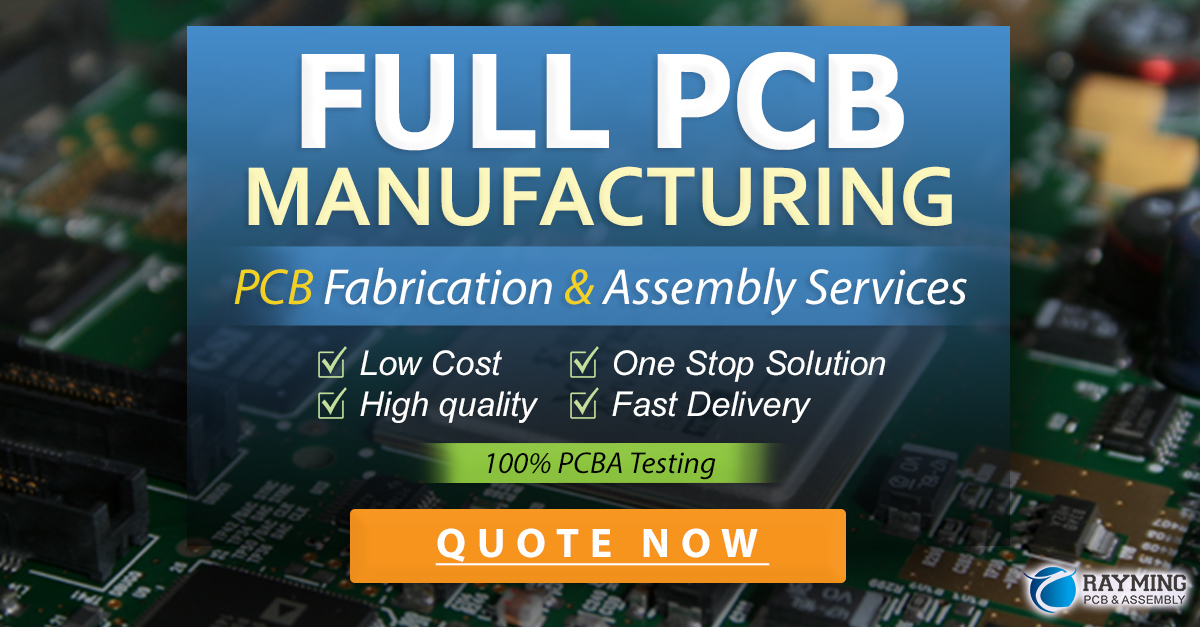
Advantages of PCB Tenting
PCB tenting offers several advantages over non-tented PCBs, including:
-
Improved Reliability: By protecting the vias from contamination and strengthening the board, PCB tenting enhances the overall reliability of the circuit. This is particularly important in critical applications where failure is not an option, such as in medical devices or aerospace systems.
-
Reduced Manufacturing Costs: Tenting the vias eliminates the need for additional manufacturing steps, such as plugging the vias or applying conformal coating. This streamlines the assembly process and reduces overall manufacturing costs.
-
Better Signal Integrity: Tented vias provide a smooth, uninterrupted surface for the flow of electrical signals, which can improve signal integrity and reduce noise or interference. This is especially important in high-speed or high-frequency applications.
-
Enhanced Durability: The added structural support provided by tented vias makes the PCB more resistant to mechanical stress and damage, such as cracking or delamination. This improves the long-term durability of the board and reduces the risk of premature failure.
-
Improved Aesthetics: Tented vias create a clean, uniform appearance on the surface of the PCB, which can be important for high-end electronic products where visual appeal is a key consideration.
Disadvantages of PCB Tenting
While PCB tenting offers many benefits, there are also some potential disadvantages to consider:
-
Limited Electrical Testing: Fully tented vias cannot be probed or tested electrically, which can make debugging or troubleshooting more difficult. This is why partial tenting is sometimes used in applications where electrical testing is required.
-
Increased Design Complexity: Tenting the vias adds an extra layer of complexity to the PCB design process, as the size and location of the vias must be carefully planned to ensure proper solder mask coverage. This can increase design time and costs.
-
Potential for Trapped Contaminants: If the vias are not properly cleaned before tenting, there is a risk that contaminants or debris could become trapped under the solder mask material. This can lead to reliability issues or even failure of the circuit over time.
-
Limited Repairability: Tented vias can make it more difficult to repair or rework the PCB, as the solder mask material must be removed to access the underlying vias. This can increase repair time and costs.
FAQ
1. What is the difference between tented and non-tented vias?
Tented vias are covered with a layer of solder mask material, while non-tented vias are left exposed. Tented vias offer better protection against contamination, improved structural integrity, and enhanced aesthetics, while non-tented vias allow for easier electrical testing and probing.
2. Can tented vias be used in all PCB applications?
Tented vias can be used in most PCB applications, but they may not be suitable for all situations. In applications where electrical testing or probing of the vias is required, partial tenting or non-tented vias may be preferred. The specific requirements of the application should be carefully considered when deciding whether to use tented vias.
3. How does PCB tenting affect the manufacturing process?
PCB tenting adds an extra step to the manufacturing process, as the solder mask material must be applied to the vias during the solder mask application stage. However, tenting the vias can also streamline the assembly process by eliminating the need for additional steps, such as plugging the vias or applying conformal coating.
4. What are the most common materials used for PCB tenting?
The most common materials used for PCB tenting are liquid photoimageable solder masks (LPI) and dry film solder masks. LPI solder masks are applied as a liquid and then cured using UV light, while dry film solder masks are applied as a solid film and then laminated onto the surface of the board.
5. Can tented vias be used in high-reliability applications?
Yes, tented vias are often used in high-reliability applications, such as aerospace, military, and medical equipment. The added protection and structural support provided by tented vias can help to ensure the long-term reliability and durability of the circuit, even in harsh operating environments.
Conclusion
PCB tenting is a critical process in the manufacturing of printed circuit boards that offers numerous benefits, including improved reliability, reduced manufacturing costs, better signal integrity, enhanced durability, and improved aesthetics. While there are some potential disadvantages to consider, such as limited electrical testing and increased design complexity, the overall benefits of PCB tenting make it a widely used technique in the electronics industry.
When deciding whether to use tented vias in a particular application, it is important to carefully consider the specific requirements and constraints of the project, as well as the trade-offs between the various advantages and disadvantages of PCB tenting. By understanding the principles and best practices of PCB tenting, designers and manufacturers can create high-quality, reliable PCBs that meet the needs of even the most demanding applications.
Leave a Reply