Inadequate Planning and Documentation
One of the most significant PCB Pitfalls is inadequate planning and documentation. Before starting your design, it’s essential to have a clear understanding of the project requirements, constraints, and goals. This includes creating a detailed schematic, bill of materials (BOM), and layout plan.
Tips for Effective Planning and Documentation
- Create a comprehensive project brief that outlines the desired functionality, dimensions, and performance requirements of your PCB.
- Develop a detailed schematic that accurately represents the circuit design and component connections.
- Maintain an up-to-date BOM that includes all necessary components, their specifications, and quantities.
- Use version control software to track changes and revisions throughout the design process.
Incorrect Component Selection
Selecting the wrong components for your PCB can lead to a range of issues, including incompatibility, poor performance, and increased costs. It’s crucial to choose components that meet the specific requirements of your design and are readily available from reliable suppliers.
Tips for Selecting the Right Components
- Research and compare components from multiple manufacturers to ensure they meet your design specifications.
- Consider factors such as package size, power rating, and temperature range when selecting components.
- Verify component availability and lead times with suppliers to avoid delays in production.
- Use reputable component libraries and databases to ensure accurate footprints and specifications.
Signal Integrity Issues
Signal integrity problems can arise when high-speed signals are not properly managed on the PCB. This can lead to issues such as crosstalk, reflections, and electromagnetic interference (EMI), which can degrade the performance and reliability of your design.
Tips for Maintaining Signal Integrity
- Use controlled impedance traces and terminations to minimize reflections and ensure proper signal propagation.
- Implement proper grounding and shielding techniques to reduce EMI and crosstalk.
- Follow high-speed design guidelines for trace routing, spacing, and layer stackup.
- Simulate and analyze critical signals using signal integrity tools to identify and mitigate potential issues.
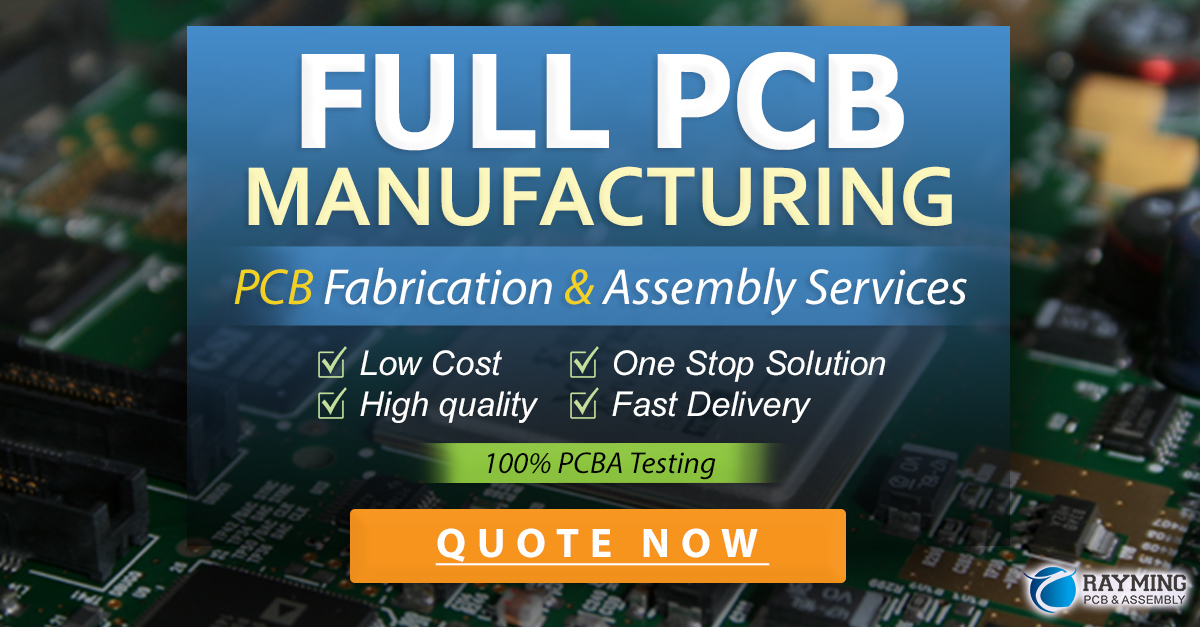
Thermal Management Challenges
Effective thermal management is essential for ensuring the long-term reliability and performance of your PCB. Overheating can lead to component failure, reduced lifespan, and decreased efficiency.
Tips for Effective Thermal Management
- Conduct thermal simulations to identify hot spots and optimize component placement and cooling strategies.
- Use thermal vias and heat sinks to dissipate heat from high-power components.
- Consider the use of thermal interface materials (TIMs) to improve heat transfer between components and heat sinks.
- Implement proper airflow and ventilation in the enclosure to prevent heat buildup.
Manufacturability and DFM Issues
Designing a PCB that is easy to manufacture and assemble is crucial for reducing costs and improving production yields. Design for Manufacturability (DFM) guidelines help ensure that your PCB can be efficiently fabricated and assembled without issues.
Tips for Improving Manufacturability and DFM
- Follow the manufacturer’s design rules and guidelines for minimum trace widths, spacings, and drill sizes.
- Use standard component packages and footprints to simplify assembly and reduce costs.
- Implement panelization techniques to maximize material utilization and minimize waste.
- Conduct DFM checks and reviews throughout the design process to identify and correct potential manufacturability issues.
Inadequate Power Distribution
Proper power distribution is essential for ensuring that all components on your PCB receive the necessary voltage and current to function correctly. Inadequate power distribution can lead to voltage drops, noise, and other issues that can affect the performance and reliability of your design.
Tips for Effective Power Distribution
- Use wide traces and copper pours to minimize resistance and improve current-carrying capacity.
- Implement proper decoupling and filtering techniques to reduce noise and ensure stable power delivery.
- Consider the use of separate power planes for analog and digital circuitry to minimize crosstalk and interference.
- Simulate and analyze the power distribution network to identify potential issues and optimize performance.
Electromagnetic Compatibility (EMC) Challenges
Ensuring that your PCB meets electromagnetic compatibility (EMC) requirements is essential for preventing interference with other electronic devices and complying with regulatory standards. EMC issues can arise from a variety of sources, including poor grounding, inadequate shielding, and improper component placement.
Tips for Improving EMC Performance
- Implement proper grounding and shielding techniques to reduce EMI and improve immunity to external interference.
- Follow best practices for component placement and routing to minimize coupling and crosstalk.
- Use EMI filters and suppressors to attenuate unwanted emissions and improve signal integrity.
- Conduct EMC testing and simulations to identify and mitigate potential issues early in the design process.
Insufficient Testing and Validation
Thorough testing and validation are essential for ensuring that your PCB meets the desired performance and reliability requirements. Insufficient testing can lead to undetected issues that may surface later in the product lifecycle, resulting in costly repairs or recalls.
Tips for Effective Testing and Validation
- Develop a comprehensive test plan that covers all critical aspects of the PCB, including functionality, performance, and reliability.
- Use automated test equipment (ATE) and test fixtures to streamline the testing process and ensure consistent results.
- Conduct environmental testing, such as thermal cycling and vibration testing, to validate the PCB’s robustness under real-world conditions.
- Implement a rigorous quality control process to identify and address any issues that arise during testing.
Inadequate Documentation and Version Control
Proper documentation and version control are essential for ensuring that your PCB design is accurate, up-to-date, and easily maintainable. Inadequate documentation can lead to confusion, errors, and delays in the design and manufacturing process.
Tips for Effective Documentation and Version Control
- Maintain a comprehensive design document that includes schematics, layouts, BOMs, and assembly instructions.
- Use version control software to track changes and revisions throughout the design process.
- Implement a standardized naming convention for files and components to ensure consistency and clarity.
- Regularly review and update documentation to reflect any changes or modifications to the design.
Lack of Collaboration and Communication
Effective collaboration and communication among team members are crucial for the success of any PCB design project. Lack of collaboration can lead to misunderstandings, delays, and errors that can impact the quality and timeliness of the final product.
Tips for Improving Collaboration and Communication
- Use collaborative design tools and platforms to facilitate real-time communication and information sharing among team members.
- Establish clear roles and responsibilities for each team member to ensure accountability and minimize conflicts.
- Hold regular design reviews and progress meetings to keep everyone informed and aligned with project goals.
- Encourage open communication and feedback throughout the design process to identify and address issues early on.
Frequently Asked Questions (FAQ)
- What are the most common causes of signal integrity issues in PCB design?
-
Signal integrity issues can arise from a variety of factors, including improper trace routing, inadequate termination, poor grounding, and insufficient layer stackup design. High-speed signals are particularly susceptible to these issues, which can lead to reflections, crosstalk, and EMI.
-
How can I ensure that my PCB design is manufacturable and meets DFM guidelines?
-
To ensure manufacturability and compliance with DFM guidelines, it’s essential to work closely with your PCB manufacturer and follow their specific design rules and recommendations. This includes adhering to minimum trace widths, spacings, and drill sizes, using standard component packages and footprints, and implementing proper panelization techniques. Conducting regular DFM checks and reviews throughout the design process can also help identify and correct potential issues early on.
-
What are some effective strategies for managing thermal issues in PCB design?
-
Effective thermal management strategies include conducting thermal simulations to identify hot spots, optimizing component placement and cooling strategies, using thermal vias and heat sinks to dissipate heat, and implementing proper airflow and ventilation in the enclosure. The use of thermal interface materials (TIMs) can also help improve heat transfer between components and heat sinks.
-
How can I improve the EMC performance of my PCB design?
-
To improve the EMC performance of your PCB, it’s important to implement proper grounding and shielding techniques, follow best practices for component placement and routing, and use EMI filters and suppressors to attenuate unwanted emissions. Conducting EMC testing and simulations early in the design process can also help identify and mitigate potential issues.
-
What are some best practices for effective collaboration and communication in PCB design projects?
- Effective collaboration and communication in PCB design projects can be achieved by using collaborative design tools and platforms, establishing clear roles and responsibilities for each team member, holding regular design reviews and progress meetings, and encouraging open communication and feedback throughout the design process. By fostering a collaborative and transparent work environment, teams can identify and address issues early on, leading to better quality and more efficient PCB designs.
Problem | Solution |
---|---|
Inadequate Planning and Documentation | Create a comprehensive project brief, detailed schematic, up-to-date BOM, and use version control software |
Incorrect Component Selection | Research and compare components, consider package size, power rating, and temperature range, verify availability and lead times |
Signal Integrity Issues | Use controlled impedance traces and terminations, implement proper grounding and shielding, follow high-speed design guidelines, simulate and analyze critical signals |
Thermal Management Challenges | Conduct thermal simulations, use thermal vias and heat sinks, consider thermal interface materials, implement proper airflow and ventilation |
Manufacturability and DFM Issues | Follow manufacturer’s design rules and guidelines, use standard component packages and footprints, implement panelization techniques, conduct DFM checks and reviews |
By understanding and addressing these common PCB pitfalls, designers can create more efficient, reliable, and cost-effective PCBs that meet the desired performance and quality requirements. Effective planning, component selection, signal integrity management, thermal management, manufacturability, power distribution, EMC compliance, testing, documentation, and collaboration are all essential elements of successful PCB design. By following best practices and continuously improving their skills and knowledge, PCB designers can overcome these challenges and deliver high-quality products that meet the evolving needs of the electronics industry.
Leave a Reply