Understanding the Basics of Temperature Control
Before we dive into the specifics of Temperature Controller circuits, let’s first understand the fundamental concepts of temperature control. Temperature control involves measuring the current temperature, comparing it to a desired setpoint, and adjusting the system’s heating or cooling elements accordingly. This closed-loop control system ensures that the temperature remains within a specified range, enabling optimal performance and preventing damage to sensitive components.
Closed-Loop Control System
A closed-loop control system, also known as a feedback control system, is the foundation of temperature control. It consists of the following key elements:
- Sensor: Measures the current temperature of the system.
- Controller: Compares the measured temperature with the desired setpoint and determines the necessary adjustments.
- Actuator: Implements the controller’s decisions by adjusting the heating or cooling elements.
- Process: The system or environment being controlled.
The closed-loop control system continuously monitors the temperature and makes adjustments based on the feedback received from the sensor. This iterative process allows for precise and stable temperature regulation.
Key Components of a Temperature Controller Circuit
A temperature controller circuit comprises several essential components that work together to achieve accurate temperature control. Let’s take a closer look at each of these components and their roles:
Temperature Sensor
The temperature sensor is responsible for measuring the current temperature of the system. There are various types of temperature sensors available, each with its own characteristics and advantages. Some common temperature sensors used in controller circuits include:
Sensor Type | Operating Range | Accuracy | Response Time |
---|---|---|---|
Thermistor | -50°C to 150°C | ±0.1°C | Fast |
RTD | -200°C to 850°C | ±0.1°C | Moderate |
Thermocouple | -200°C to 1750°C | ±1°C | Fast |
IC Sensor | -55°C to 150°C | ±0.5°C | Fast |
The choice of temperature sensor depends on factors such as the required temperature range, accuracy, response time, and environmental conditions.
Signal Conditioning Circuitry
The signal conditioning circuitry is responsible for processing the raw signal from the temperature sensor and converting it into a form suitable for the controller. This may involve amplification, filtering, linearization, or analog-to-digital conversion. The specific signal conditioning requirements depend on the type of sensor used and the desired output signal.
Controller
The controller is the brain of the temperature controller circuit. It receives the conditioned signal from the sensor and compares it with the desired setpoint. Based on this comparison, the controller determines the necessary adjustments to be made to the actuator. The controller can be implemented using various techniques, such as:
- On/Off Control: The simplest form of control, where the actuator is turned on or off based on a temperature threshold.
- Proportional Control: The actuator’s output is proportional to the difference between the measured temperature and the setpoint.
- PID Control: A more advanced control algorithm that combines proportional, integral, and derivative actions for precise and stable control.
The choice of control technique depends on the specific application requirements, such as accuracy, stability, and response time.
Actuator
The actuator is responsible for implementing the controller’s decisions by adjusting the heating or cooling elements of the system. Common types of actuators used in temperature controller circuits include:
- Relay: A switch that turns the heating or cooling element on or off based on the controller’s output.
- Solid-State Relay (SSR): Similar to a relay but uses solid-state components for faster switching and longer lifespan.
- Thyristor or TRIAC: Semiconductor devices that allow for variable power control of the heating or cooling element.
The selection of the actuator depends on factors such as the power rating, switching speed, and control precision required by the application.
Implementing a Temperature Controller Circuit
Now that we have covered the key components of a temperature controller circuit, let’s explore the steps involved in implementing one.
Step 1: Sensor Selection and Placement
The first step is to select an appropriate temperature sensor based on the application requirements. Consider factors such as the temperature range, accuracy, response time, and environmental conditions. Once the sensor is selected, it should be properly placed in the system to accurately measure the temperature of interest.
Step 2: Signal Conditioning
The raw signal from the temperature sensor needs to be conditioned to match the input requirements of the controller. This may involve amplification, filtering, linearization, or analog-to-digital conversion. The specific signal conditioning circuitry will depend on the type of sensor used and the desired output signal.
Step 3: Controller Design
The controller is the core of the temperature controller circuit. It receives the conditioned signal from the sensor and determines the necessary adjustments to be made to the actuator. The controller can be implemented using various techniques, such as on/off control, proportional control, or PID control. The choice of control technique depends on the specific application requirements.
Step 4: Actuator Selection and Integration
The actuator is responsible for adjusting the heating or cooling elements of the system based on the controller’s output. Select an appropriate actuator, such as a relay, solid-state relay, or thyristor, based on the power rating, switching speed, and control precision required by the application. Integrate the actuator with the heating or cooling elements and ensure proper electrical connections.
Step 5: Calibration and Testing
Once the temperature controller circuit is assembled, it is crucial to calibrate and test the system to ensure accurate and reliable operation. This involves setting the desired setpoint, monitoring the system’s response, and fine-tuning the controller parameters as necessary. Conduct thorough testing under various operating conditions to validate the performance of the temperature controller circuit.
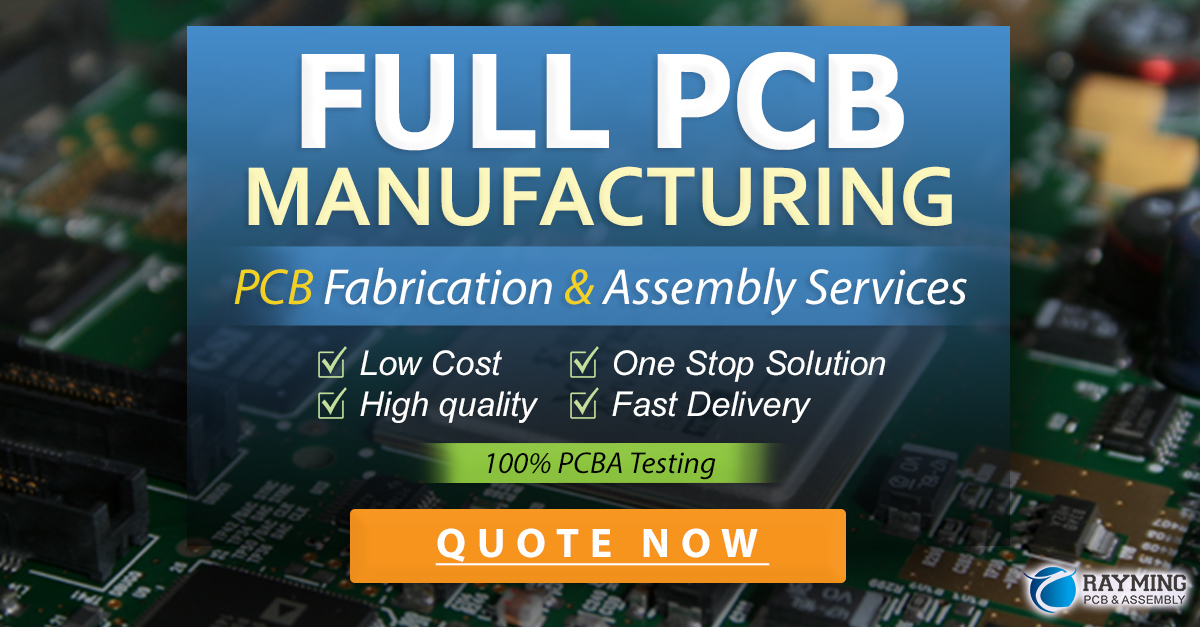
Applications of Temperature Controller Circuits
Temperature controller circuits find applications in a wide range of industries and devices. Some common applications include:
- HVAC Systems: Temperature controller circuits are used in heating, ventilation, and air conditioning systems to maintain a comfortable indoor environment.
- Industrial Processes: Many industrial processes, such as chemical reactions, require precise temperature control to ensure product quality and safety.
- Medical Equipment: Temperature controller circuits are used in medical devices, such as incubators and sterilizers, to maintain optimal operating conditions.
- Automotive Systems: Temperature control is essential in automotive systems, such as engine cooling and cabin climate control.
- Consumer Appliances: Household appliances, such as ovens, refrigerators, and water heaters, rely on temperature controller circuits for accurate temperature regulation.
Frequently Asked Questions (FAQ)
1. What is the difference between a thermistor and an RTD?
A thermistor is a temperature-sensitive resistor whose resistance changes nonlinearly with temperature. It offers fast response times and high sensitivity but has a limited temperature range. An RTD (Resistance Temperature Detector) is a temperature sensor whose resistance changes linearly with temperature. It provides high accuracy and a wide temperature range but has a slower response time compared to thermistors.
2. What is PID control, and when is it used?
PID (Proportional-Integral-Derivative) control is an advanced control algorithm that combines proportional, integral, and derivative actions to achieve precise and stable temperature control. The proportional action adjusts the actuator’s output based on the current error, the integral action eliminates steady-state errors, and the derivative action improves the system’s response to rapid changes. PID control is used in applications that require high accuracy, stability, and fast response times.
3. Can a temperature controller circuit be used for both heating and cooling?
Yes, a temperature controller circuit can be designed to control both heating and cooling elements. In such cases, the controller’s output is connected to both heating and cooling actuators, and the control algorithm determines which actuator to activate based on the measured temperature and the desired setpoint.
4. What is the importance of calibration in a temperature controller circuit?
Calibration is crucial in a temperature controller circuit to ensure accurate and reliable temperature measurement and control. It involves comparing the sensor’s output with a known reference temperature and adjusting the controller’s parameters accordingly. Regular calibration helps compensate for sensor drift, environmental changes, and other factors that may affect the system’s accuracy over time.
5. How do I select the appropriate temperature sensor for my application?
Selecting the appropriate temperature sensor depends on several factors, including the required temperature range, accuracy, response time, and environmental conditions. Consider the specific requirements of your application and evaluate the characteristics of different Sensor Types, such as thermistors, RTDs, thermocouples, and IC sensors. Consult sensor datasheets and application notes to determine the most suitable sensor for your needs.
Conclusion
Temperature controller circuits play a vital role in maintaining optimal operating conditions in various electronic devices and systems. By understanding the key components, functionalities, and applications of these circuits, engineers and technicians can design and implement effective temperature control solutions.
From selecting the appropriate temperature sensor to designing the controller and integrating the actuator, each step in the implementation process requires careful consideration and attention to detail. Regular calibration and testing ensure the accuracy and reliability of the temperature controller circuit over time.
As technology advances, temperature controller circuits continue to evolve, offering improved accuracy, faster response times, and enhanced functionality. By staying up-to-date with the latest developments in temperature control techniques and components, engineers can design more efficient and reliable systems that meet the ever-growing demands of various industries.
In conclusion, temperature controller circuits are essential building blocks in the world of electronics, enabling precise and stable temperature regulation in a wide range of applications. By understanding the inner workings of these circuits and following best practices in their design and implementation, we can harness the power of temperature control to optimize performance, ensure safety, and drive innovation across industries.
Leave a Reply