Introduction to Circuit Board Types
A circuit board, also known as a printed circuit board (PCB), is the backbone of modern electronic devices. It is a flat board made of insulating material, such as fiberglass or plastic, with conductive tracks, pads, and other features etched from copper sheets laminated onto the board. Circuit boards are used in virtually all electronic devices, from simple calculators to complex computers and smartphones.
There are several types of circuit boards, each with its own unique characteristics and applications. In this article, we will explore the different types of circuit boards in detail, their manufacturing processes, and their uses in various industries.
Types of Circuit Boards
1. Single-Sided PCB
What is a Single-Sided PCB?
A single-sided PCB, also known as a single-layer PCB, is the simplest type of circuit board. It consists of a single layer of conductive material, usually copper, on one side of the insulating substrate. The components are mounted on the same side as the conductive tracks.
Manufacturing Process of Single-Sided PCBs
The manufacturing process of single-sided PCBs involves the following steps:
- Designing the circuit layout using PCB design software
- Printing the circuit layout onto a transparent film
- Coating the copper-clad board with a photoresist layer
- Exposing the photoresist layer to UV light through the transparent film
- Developing the photoresist layer to remove the unexposed areas
- Etching the copper layer to remove the unwanted copper
- Drilling holes for through-hole components
- Applying a solder mask and silkscreen layer for protection and labeling
Applications of Single-Sided PCBs
Single-sided PCBs are commonly used in simple electronic devices, such as:
- Calculators
- Radios
- Toys
- Low-power amplifiers
- Power supplies
2. Double-Sided PCB
What is a Double-Sided PCB?
A double-sided PCB, also known as a two-layer PCB, has conductive material on both sides of the insulating substrate. The two layers are connected through plated through-holes (PTHs), which are small holes drilled through the board and plated with conductive material.
Manufacturing Process of Double-Sided PCBs
The manufacturing process of double-sided PCBs is similar to that of single-sided PCBs, with a few additional steps:
- Designing the circuit layout using PCB design software
- Printing the circuit layout onto two transparent films, one for each side
- Coating both sides of the copper-clad board with a photoresist layer
- Exposing both sides of the photoresist layer to UV light through the transparent films
- Developing the photoresist layer to remove the unexposed areas
- Etching the copper layer on both sides to remove the unwanted copper
- Drilling holes for through-hole components and PTHs
- Plating the PTHs with conductive material
- Applying a solder mask and silkscreen layer for protection and labeling
Applications of Double-Sided PCBs
Double-sided PCBs are used in more complex electronic devices, such as:
- Mobile phones
- Laptops
- Televisions
- Automotive electronics
- Industrial control systems
3. Multi-Layer PCB
What is a Multi-Layer PCB?
A multi-layer PCB has more than two layers of conductive material, with insulating layers sandwiched between them. The layers are connected through PTHs and blind or buried vias, which are small holes drilled through only a portion of the board’s thickness.
Manufacturing Process of Multi-Layer PCBs
The manufacturing process of multi-layer PCBs is more complex than that of single-sided or double-sided PCBs:
- Designing the circuit layout using PCB design software
- Printing the circuit layout onto multiple transparent films, one for each layer
- Laminating the inner layers with insulating material and copper foil
- Drilling holes for PTHs and vias
- Plating the holes with conductive material
- Etching the outer layers to remove the unwanted copper
- Laminating the outer layers with the inner layers
- Drilling additional holes for through-hole components
- Applying a solder mask and silkscreen layer for protection and labeling
Applications of Multi-Layer PCBs
Multi-layer PCBs are used in high-density electronic devices that require a large number of components and connections, such as:
- Servers and data centers
- Aerospace and defense systems
- Medical equipment
- High-performance computing systems
- Telecommunications equipment
4. Flexible PCB
What is a Flexible PCB?
A flexible PCB, also known as a flex PCB or FPC, is a circuit board made of flexible insulating material, such as polyimide or polyester. The conductive tracks are printed on the flexible substrate, allowing the board to bend and flex without breaking.
Manufacturing Process of Flexible PCBs
The manufacturing process of flexible PCBs is similar to that of rigid PCBs, with a few modifications:
- Designing the circuit layout using PCB design software
- Printing the circuit layout onto a flexible copper-clad substrate
- Etching the copper layer to remove the unwanted copper
- Applying a coverlay or solder mask for protection
- Cutting the board to the desired shape and size
Applications of Flexible PCBs
Flexible PCBs are used in applications that require the board to bend or flex, such as:
- Wearable electronics
- Medical implants
- Automotive electronics
- Aerospace and defense systems
- Consumer electronics (e.g., smartphones, smartwatches)
5. Rigid-Flex PCB
What is a Rigid-Flex PCB?
A rigid-flex PCB is a hybrid circuit board that combines the features of both rigid and flexible PCBs. It consists of rigid PCB sections connected by flexible PCB sections, allowing for three-dimensional packaging and improved reliability.
Manufacturing Process of Rigid-Flex PCBs
The manufacturing process of rigid-flex PCBs involves a combination of rigid and flexible PCB manufacturing techniques:
- Designing the circuit layout using PCB design software
- Fabricating the rigid and flexible PCB sections separately
- Laminating the rigid and flexible sections together
- Drilling holes for through-hole components and PTHs
- Plating the holes with conductive material
- Applying a solder mask and silkscreen layer for protection and labeling
Applications of Rigid-Flex PCBs
Rigid-flex PCBs are used in applications that require high reliability, compact packaging, and three-dimensional design, such as:
- Aerospace and defense systems
- Medical equipment
- Industrial control systems
- Automotive electronics
- High-performance computing systems
Comparison of Circuit Board Types
Circuit Board Type | Layers | Flexibility | Density | Cost |
---|---|---|---|---|
Single-Sided PCB | 1 | Rigid | Low | Low |
Double-Sided PCB | 2 | Rigid | Medium | Medium |
Multi-Layer PCB | 3+ | Rigid | High | High |
Flexible PCB | 1-2 | Flexible | Low | Medium |
Rigid-Flex PCB | 2+ | Both | High | High |
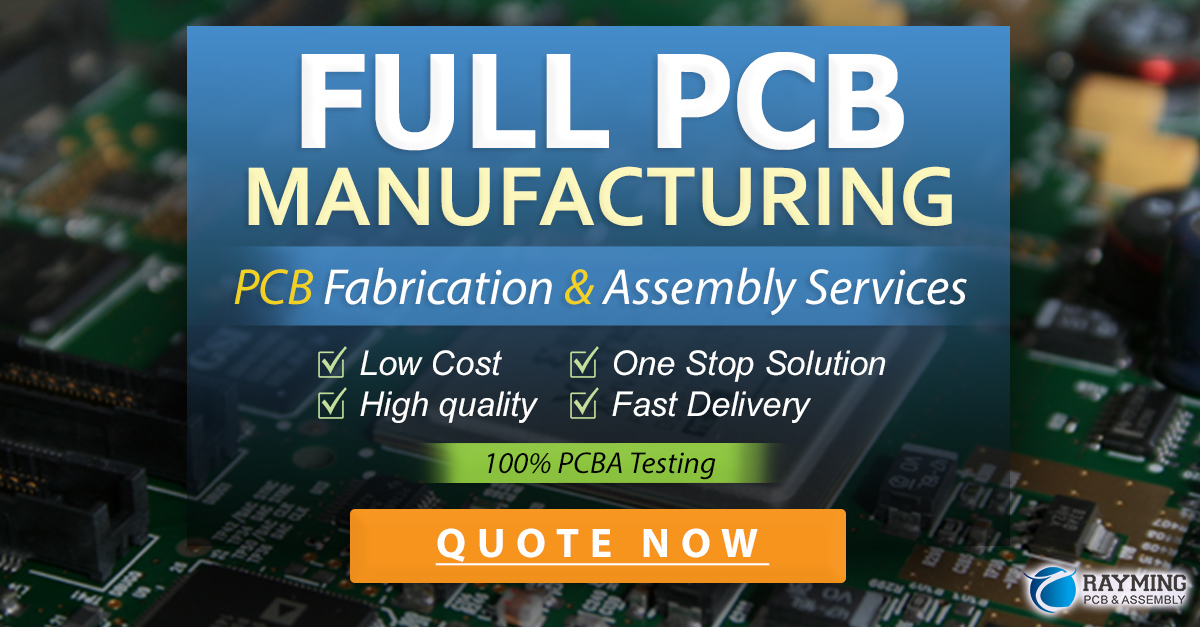
Frequently Asked Questions (FAQ)
1. What is the difference between a single-sided and double-sided PCB?
A single-sided PCB has conductive material on only one side of the insulating substrate, while a double-sided PCB has conductive material on both sides. Double-sided PCBs can accommodate more components and connections than single-sided PCBs.
2. What are the advantages of using a multi-layer PCB?
Multi-layer PCBs offer several advantages, including:
- Higher component density
- Improved signal integrity
- Reduced electromagnetic interference (EMI)
- Better heat dissipation
- Compact packaging
3. When should I use a flexible PCB?
Flexible PCBs are ideal for applications that require the board to bend or flex, such as wearable electronics, medical implants, and automotive electronics. They offer improved reliability and durability compared to rigid PCBs in these applications.
4. What is the purpose of a rigid-flex PCB?
Rigid-flex PCBs combine the benefits of both rigid and flexible PCBs, allowing for three-dimensional packaging and improved reliability. They are commonly used in aerospace, defense, medical, and industrial applications that require high performance and compact design.
5. How do I choose the right type of circuit board for my project?
When choosing a circuit board type for your project, consider factors such as:
- The complexity of the circuit design
- The number of components and connections required
- The space constraints and packaging requirements
- The operating environment and reliability needs
- The budget and production volume
Consult with a PCB manufacturer or design expert to determine the best circuit board type for your specific application.
Conclusion
Circuit boards are essential components in modern electronics, providing the foundation for the functionality and performance of countless devices. Understanding the different types of circuit boards, their manufacturing processes, and their applications is crucial for anyone involved in electronic design and production.
Single-sided, double-sided, multi-layer, flexible, and rigid-flex PCBs each have their own unique characteristics and benefits, making them suitable for different applications and industries. By selecting the appropriate circuit board type and working with experienced PCB manufacturers, designers can ensure the success and reliability of their electronic products.
As technology continues to advance, the demand for high-performance, compact, and reliable circuit boards will only increase. Staying informed about the latest developments in circuit board design and manufacturing will be essential for businesses and individuals looking to stay competitive in the rapidly evolving world of electronics.
Leave a Reply