Introduction to Flex PCB Soldering
Flex PCB Soldering is the process of attaching electronic components to a flexible printed circuit board using a conductive material, typically solder. The goal is to create a reliable electrical and mechanical connection between the components and the PCB. Soldering Flex PCBs requires special considerations compared to traditional rigid PCBs due to their flexibility, thinness, and material properties.
Challenges in Flex PCB Soldering
- Thermal management: Flex PCBs have limited heat dissipation capabilities, making them prone to damage during soldering.
- Material compatibility: The choice of solder and flux must be compatible with the Flex PCB materials to avoid delamination or degradation.
- Mechanical stress: Flexing and bending of the PCB during soldering can cause component misalignment or solder joint failures.
- Accessibility: The compact and dense nature of Flex PCBs can make it difficult to access certain areas for soldering.
1. Hand Soldering
Hand soldering is a manual soldering technique commonly used for small-scale production, prototyping, or rework. It involves using a soldering iron to apply heat and solder to the component leads and PCB pads.
Techniques for Hand Soldering Flex PCBs
- Use a temperature-controlled soldering iron with a fine tip to minimize heat exposure to the Flex PCB.
- Apply flux to the component leads and PCB pads to improve solder wetting and prevent oxidation.
- Pre-tin the component leads and PCB pads to ensure a quick and efficient soldering process.
- Use a light touch and minimize the soldering time to avoid overheating the Flex PCB.
Advantages and Disadvantages of Hand Soldering
Advantages:
– Flexibility in soldering different component types and sizes
– Suitable for small-scale production or rework
– Low initial equipment cost
Disadvantages:
– Time-consuming and labor-intensive
– Inconsistent solder joint quality
– Requires skilled operators
2. Reflow Soldering
Reflow soldering is an automated soldering process that uses a reflow oven to melt and solidify solder paste applied to the PCB and components. It is widely used for surface mount technology (SMT) components on Flex PCBs.
Reflow Soldering Process
- Solder paste application: Solder paste, a mixture of solder alloy and flux, is applied to the PCB pads using stencil printing or dispensing methods.
- Component placement: SMT components are placed onto the solder paste using pick-and-place machines or manual placement.
- Reflow: The Flex PCB with components is passed through a reflow oven, where it is subjected to a controlled temperature profile. The solder paste melts, wets the component leads and PCB pads, and solidifies to form solder joints.
Reflow Soldering Considerations for Flex PCBs
- Use a low-temperature solder paste to minimize thermal stress on the Flex PCB.
- Adjust the reflow temperature profile to accommodate the thermal limitations of the Flex PCB materials.
- Use a nitrogen atmosphere in the reflow oven to reduce oxidation and improve solder joint quality.
- Implement proper support and fixturing to prevent Flex PCB warpage during reflow.
Advantages and Disadvantages of Reflow Soldering
Advantages:
– High-speed and automated process
– Consistent and reliable solder joint quality
– Suitable for high-volume production
Disadvantages:
– Higher initial equipment cost
– Limited flexibility in soldering different component types and sizes
– Requires careful process control and optimization
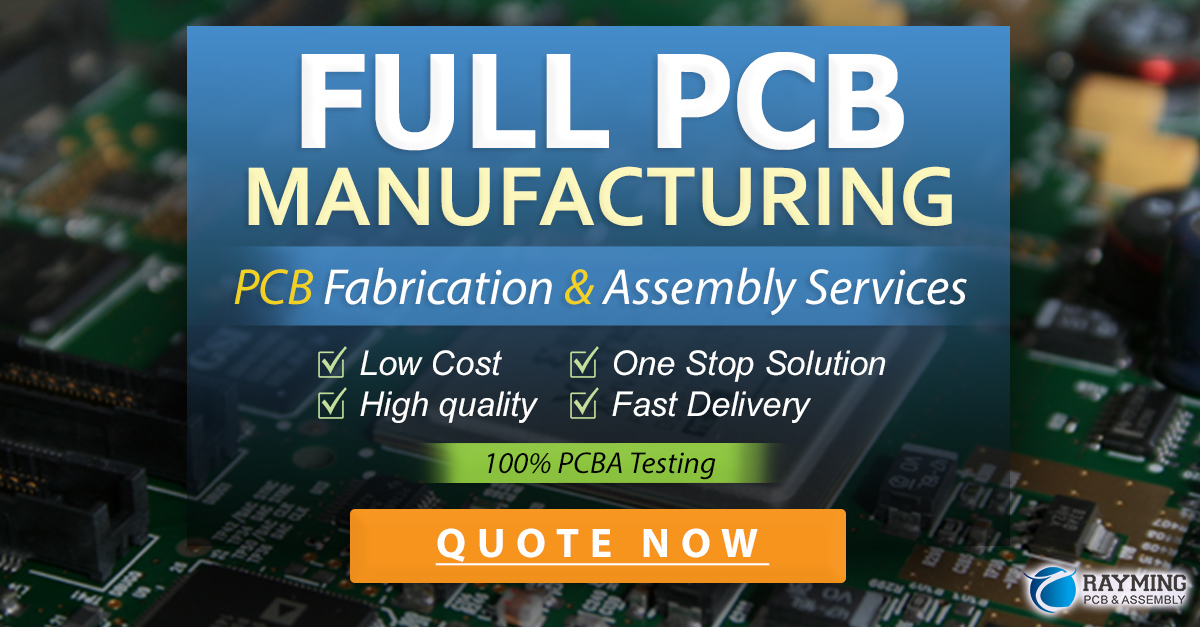
3. Wave Soldering
Wave soldering is an automated soldering process primarily used for through-hole components on Flex PCBs. It involves passing the PCB over a molten solder wave, which wets the component leads and PCB holes to form solder joints.
Wave Soldering Process
- Flux application: Liquid flux is applied to the bottom side of the Flex PCB to improve solder wetting and prevent oxidation.
- Preheating: The Flex PCB is preheated to activate the flux and minimize thermal shock during soldering.
- Solder wave contact: The Flex PCB is passed over a molten solder wave, which wets the component leads and PCB holes.
- Cooling: The soldered Flex PCB is cooled to allow the solder joints to solidify.
Wave Soldering Considerations for Flex PCBs
- Use a low-temperature solder alloy to reduce thermal stress on the Flex PCB.
- Adjust the solder wave height and contact time to prevent excessive solder buildup or bridging.
- Implement proper Flex PCB support and conveyor systems to minimize warpage and ensure consistent solder joint formation.
- Use a nitrogen atmosphere in the wave soldering machine to reduce oxidation and improve solder joint quality.
Advantages and Disadvantages of Wave Soldering
Advantages:
– Fast and automated process
– Suitable for through-hole components
– Efficient for high-volume production
Disadvantages:
– Limited flexibility in soldering different component types and sizes
– Potential for solder bridging or insufficient hole fill
– Requires careful process control and optimization
4. Selective Soldering
Selective soldering is a targeted soldering process that combines the advantages of hand soldering and automated soldering. It uses a miniature solder wave or laser to apply solder to specific areas on the Flex PCB.
Selective Soldering Techniques
- Mini-wave soldering: A small solder wave is directed towards the specific areas to be soldered, such as through-hole components or connectors.
- Laser soldering: A focused laser beam is used to heat and melt solder on specific areas of the Flex PCB, providing precise control and minimal thermal impact.
Selective Soldering Considerations for Flex PCBs
- Use a low-temperature solder alloy to minimize thermal stress on the Flex PCB.
- Optimize the solder wave or laser parameters to achieve consistent solder joint formation.
- Implement proper Flex PCB fixturing and masking to protect sensitive areas from unintended solder exposure.
- Use a nitrogen atmosphere to reduce oxidation and improve solder joint quality.
Advantages and Disadvantages of Selective Soldering
Advantages:
– Targeted soldering approach
– Suitable for mixed component types and sizes
– Reduced thermal impact on the Flex PCB
– Increased flexibility compared to wave soldering
Disadvantages:
– Higher equipment cost compared to hand soldering
– Slower process compared to reflow or wave soldering
– Requires precise fixturing and masking
5. Vapour Phase Soldering
Vapour phase soldering is an advanced soldering technique that uses a heated vapour to transfer heat to the Flex PCB and components. It provides a uniform and controlled soldering environment, minimizing thermal stress and oxidation.
Vapour Phase Soldering Process
- Solder paste application: Solder paste is applied to the PCB pads using stencil printing or dispensing methods.
- Component placement: SMT components are placed onto the solder paste using pick-and-place machines or manual placement.
- Vapour phase soldering: The Flex PCB with components is placed inside a vapour phase soldering machine. A heated vapour, typically generated from a perfluoropolyether (PFPE) liquid, envelops the PCB and transfers heat to the solder paste, causing it to melt and form solder joints.
Vapour Phase Soldering Considerations for Flex PCBs
- Use a low-temperature solder paste compatible with the vapour phase soldering process.
- Adjust the vapour temperature and exposure time to accommodate the thermal limitations of the Flex PCB materials.
- Implement proper Flex PCB support and fixturing to prevent warpage during soldering.
- Ensure adequate ventilation and safety measures when handling PFPE liquid and vapours.
Advantages and Disadvantages of Vapour Phase Soldering
Advantages:
– Uniform and controlled soldering environment
– Minimal thermal stress on the Flex PCB
– Reduced oxidation and improved solder joint quality
– Suitable for high-density and fine-pitch components
Disadvantages:
– Higher equipment cost compared to other soldering methods
– Limited throughput compared to reflow soldering
– Requires specialized equipment and facilities
Frequently Asked Questions (FAQ)
-
Q: What is the most suitable soldering method for prototyping or small-scale production of Flex PCBs?
A: Hand soldering is often the most suitable method for prototyping or small-scale production of Flex PCBs. It offers flexibility in soldering different component types and sizes and has a low initial equipment cost. -
Q: How can I minimize thermal stress on Flex PCBs during soldering?
A: To minimize thermal stress on Flex PCBs during soldering, use low-temperature solder alloys, adjust the soldering temperature profiles, and minimize the soldering time. Implementing proper Flex PCB support and fixturing can also help prevent warpage and reduce thermal stress. -
Q: What are the advantages of using reflow soldering for Flex PCBs?
A: Reflow soldering offers several advantages for Flex PCBs, including high-speed and automated processing, consistent and reliable solder joint quality, and suitability for high-volume production. It is particularly effective for surface mount technology (SMT) components. -
Q: Can selective soldering be used for both through-hole and surface mount components on Flex PCBs?
A: Yes, selective soldering can be used for both through-hole and surface mount components on Flex PCBs. It provides a targeted soldering approach, allowing for flexibility in soldering different component types and sizes while minimizing thermal impact on the Flex PCB. -
Q: What safety precautions should be taken when using vapour phase soldering for Flex PCBs?
A: When using vapour phase soldering for Flex PCBs, it is crucial to ensure adequate ventilation and implement proper safety measures when handling perfluoropolyether (PFPE) liquid and vapours. Follow the manufacturer’s guidelines and wear appropriate personal protective equipment (PPE) to minimize exposure risks.
Conclusion
Soldering Flex PCBs requires careful consideration of the unique properties and challenges associated with flexible substrates. The five common Flex PCB soldering technologies discussed in this article – hand soldering, reflow soldering, wave soldering, selective soldering, and vapour phase soldering – offer different approaches to achieve reliable solder joints.
Choosing the most suitable soldering method depends on factors such as production volume, component types and sizes, thermal limitations of the Flex PCB materials, and available resources. By understanding the advantages and disadvantages of each soldering technology and implementing appropriate techniques and considerations, manufacturers can ensure the successful assembly of Flex PCBs for various applications.
As Flex PCB technology continues to evolve, it is essential for engineers and manufacturers to stay updated with the latest soldering advancements and best practices. Investing in the right equipment, training, and process optimization can lead to improved product quality, reliability, and manufacturing efficiency in the dynamic world of Flex PCBs.
Leave a Reply