What is Surface Mount Technology (SMT)?
Surface-mount technology (SMT) is a method in which the electrical components are mounted directly onto the surface of a printed circuit board (PCB). An electrical component mounted in this manner is referred to as a surface-mount device (SMD). In industry, this approach has largely replaced the through-hole technology construction method of fitting components with wire leads into holes in the circuit board.
SMT components are usually smaller than their through-hole counterparts because they have either smaller leads or no leads at all. These compact components are designed to be soldered directly onto the PCB surface, rather than plugged into holes that go through the board. Surface mounting lends itself well to a high degree of automation, reducing labor costs and greatly increasing production rates.
Advantages of Surface Mount Technology
SMT offers several advantages over through-hole mounting:
-
Smaller components: Components can be one-quarter to one-tenth the size and weight of through-hole components, allowing much higher circuit densities.
-
Faster assembly: Placement of components on the board can be automated, and the components can be soldered to the board all at once. With through-hole mounting, each lead must be soldered individually.
-
Lower cost: The cost of SMT assembly is typically less than half that of through-hole assembly. Savings come from the use of smaller, cheaper components, and the increased automation of the assembly process.
-
Increased reliability: SMT provides stronger mechanical bonds than through-hole mounting, making the assembled boards more resistant to shake, vibration, and temperature changes.
-
Double-sided PCB assembly: SMT allows components to be placed on both sides of a circuit board. Through-hole mounting requires components to be inserted on one side and soldered on the other, limiting components to one side of the board.
SMT Manufacturing Process Overview
The SMT manufacturing process involves several steps:
-
Solder Paste Printing: Solder paste, a sticky mixture of tiny solder particles and flux, is applied to the PCB through a stainless steel stencil. The stencil has holes that correspond to the pads on the PCB where the components will be placed.
-
Component Placement: The components are placed onto the PCB, with their leads or terminations aligned with the pads. High-speed pick-and-place machines are used for this process, capable of placing thousands of components per hour.
-
Reflow Soldering: The PCB, with the components placed, goes through a reflow oven. The oven heats the board to a temperature high enough to melt the solder particles in the paste, but not so high as to damage the components. As the solder melts, it forms electrical and mechanical bonds between the component leads and the pads on the PCB.
-
Inspection: After soldering, the boards are inspected to ensure the components are properly placed and soldered. This is often done with automated optical inspection (AOI) systems.
-
Testing: Finally, the boards are tested to ensure they function as intended. This can involve in-circuit testing, functional testing, or both.
Here’s a table summarizing the SMT manufacturing process:
Step | Description |
---|---|
Solder Paste Printing | Solder paste is applied to the PCB through a stencil |
Component Placement | Components are placed onto the PCB, aligned with the pads |
Reflow Soldering | The PCB is heated to melt the solder, forming bonds between components and pads |
Inspection | Boards are inspected to ensure proper component placement and soldering |
Testing | Boards are tested for functionality |
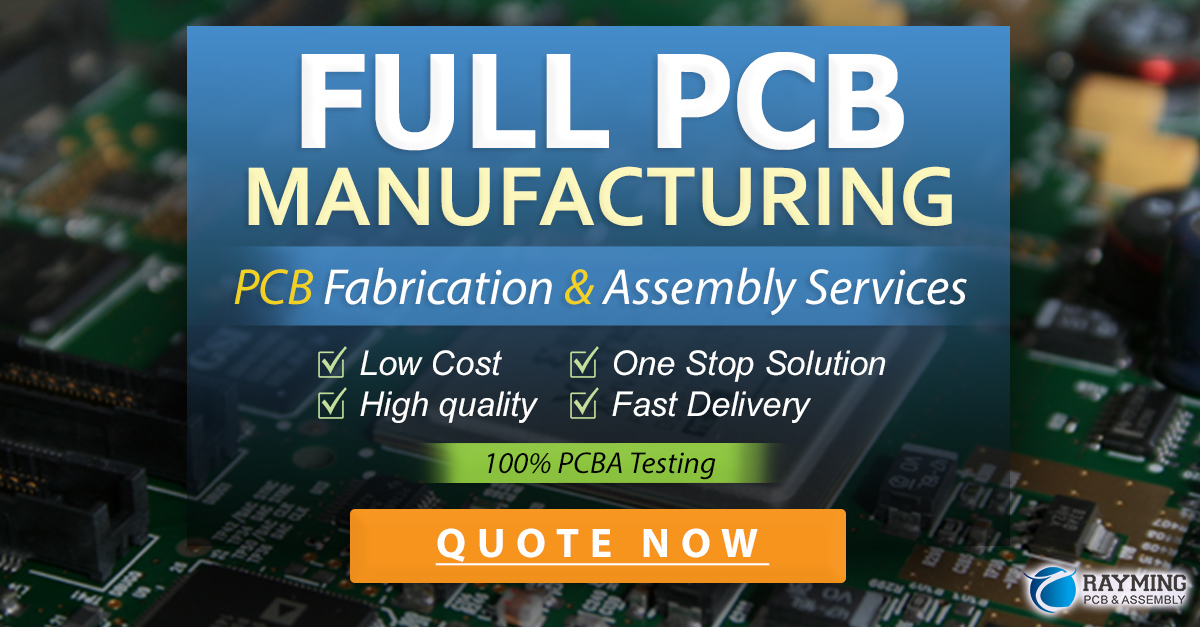
Types of SMT Components
SMT components come in various package types, each with its own characteristics and applications. Here are some of the most common types:
Resistors and Capacitors
-
Chip resistors and capacitors: These are simple, two-terminal devices in small rectangular packages. They are the most common SMT components.
-
MELF (Metal Electrode Leadless Face): Cylindrical components that offer better power handling and accuracy than chip components.
Integrated Circuits (ICs)
-
Small Outline Integrated Circuit (SOIC): A rectangular package with gull-wing leads extending from the two long sides.
-
Quad Flat Pack (QFP): A square or rectangular package with gull-wing leads extending from all four sides. Variations include Low Profile Quad Flat Pack (LQFP) and Thin Quad Flat Pack (TQFP).
-
Ball Grid Array (BGA): A square or rectangular package with a grid of solder balls on the bottom. BGA packages allow for a high density of interconnections.
Other Components
-
Small Outline Transistor (SOT): A small, usually three-lead transistor package.
-
Small Outline Diode (SOD): A small, usually two-lead diode package.
-
LED (Light Emitting Diode): SMT LEDs are available in various sizes and shapes.
SMT Design Considerations
When designing a PCB for SMT assembly, several factors need to be considered:
-
Component selection: Choose components that are suitable for SMT and available in the desired package types.
-
Footprint design: Create footprints (land patterns) for each component that match the component’s dimensions and provide adequate space for solder joints.
-
Placement: Place components to minimize the PCB size and trace lengths, while allowing for efficient assembly and soldering.
-
Routing: Route traces to minimize signal interference and provide proper power and ground connections.
-
Thermal management: Consider the thermal characteristics of the components and the PCB, and design for adequate heat dissipation.
-
Manufacturing constraints: Design the board to accommodate the capabilities and limitations of the SMT assembly process, such as minimum component spacing and maximum board size.
Frequently Asked Questions (FAQ)
- What is the difference between SMT and through-hole technology?
SMT components are mounted directly onto the surface of the PCB, while through-hole components have leads that are inserted into holes drilled in the PCB and soldered on the opposite side. SMT allows for smaller components, higher component density, and faster assembly compared to through-hole technology.
- Can SMT and through-hole components be used on the same PCB?
Yes, it is possible to use both SMT and through-hole components on the same PCB. This is often done for components that are not available in SMT packages or for components that require additional mechanical strength, such as connectors.
- What is solder paste, and how is it used in SMT assembly?
Solder paste is a mixture of tiny solder particles suspended in a flux paste. It is applied to the PCB pads through a stencil before the components are placed. During the reflow soldering process, the solder particles melt and form electrical and mechanical connections between the component leads and the PCB pads.
- What are the advantages of using SMT in PCB assembly?
SMT offers several advantages over through-hole technology, including smaller component sizes, higher component density, faster assembly, lower production costs, and increased reliability due to stronger mechanical bonds.
- What are some common SMT component package types?
Common SMT component package types include chip resistors and capacitors, Small Outline Integrated Circuits (SOIC), Quad Flat Packs (QFP), Ball Grid Arrays (BGA), Small Outline Transistors (SOT), and Light Emitting Diodes (LED).
Conclusion
Surface Mount Technology (SMT) has revolutionized the electronics manufacturing industry by enabling the production of smaller, denser, and more reliable electronic devices at lower costs and with faster assembly times compared to through-hole technology. By understanding the basics of SMT, including the manufacturing process, component types, and design considerations, engineers and technicians can effectively design and assemble high-quality electronic products that meet the demands of today’s market.
As electronic devices continue to become more compact and complex, SMT will likely remain the dominant PCB assembly method, driving innovation and shaping the future of the electronics industry.
Leave a Reply