Introduction to Strain Gauge Load Cells
Strain gauge load cells are essential components in various industries, including aerospace, automotive, and manufacturing. These devices are designed to accurately measure force, weight, and pressure by converting mechanical stress into electrical signals. In this comprehensive article, we will explore the usage, construction, working principles, and types of strain gauge load cells.
What is a Strain Gauge Load Cell?
A strain gauge load cell is a transducer that converts an applied force into an electrical signal. It consists of a metal body, typically made of aluminum or stainless steel, with one or more strain gauges bonded to its surface. When a force is applied to the load cell, the metal body deforms, causing the strain gauges to change their electrical resistance. This change in resistance is then converted into a measurable electrical signal, which can be used to determine the magnitude of the applied force.
Construction of a Strain Gauge Load Cell
The construction of a strain gauge load cell involves several key components:
-
Metal body: The metal body, also known as the spring element, is the main structural component of the load cell. It is designed to deform elastically when a force is applied.
-
Strain gauges: Strain gauges are thin, metallic foil patterns that are bonded to the surface of the metal body. They are typically arranged in a Wheatstone bridge configuration to maximize sensitivity and minimize the effects of temperature changes.
-
Wiring: The strain gauges are connected to wires that transmit the electrical signal to the measuring device.
-
Protective coating: A protective coating, such as polyurethane or silicone rubber, is applied over the strain gauges and wiring to shield them from environmental factors like moisture, dust, and mechanical damage.
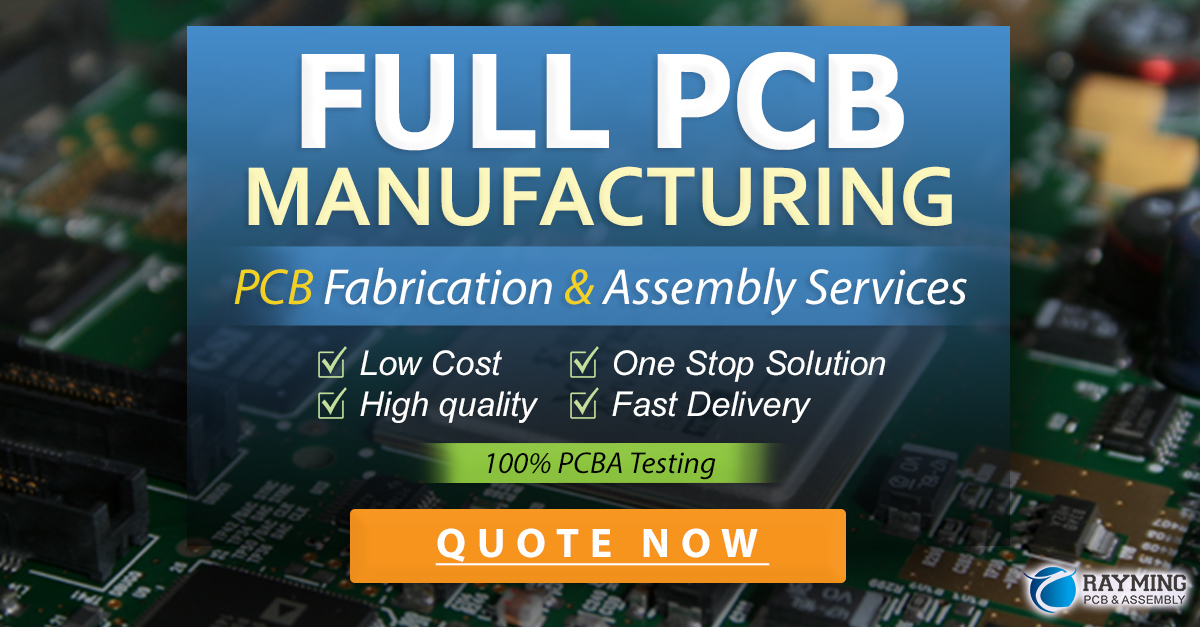
Working Principles of Strain Gauge Load Cells
The working principle of a strain gauge load cell is based on the piezoresistive effect, which is the change in electrical resistance of a material when it is subjected to mechanical stress. When a force is applied to the load cell, the metal body deforms, causing the bonded strain gauges to stretch or compress. This deformation alters the electrical resistance of the strain gauges, which is then measured using a Wheatstone bridge circuit.
The Wheatstone bridge is a simple electrical circuit that consists of four resistors arranged in a diamond-shaped configuration. In a strain gauge load cell, two of the resistors are active strain gauges, while the other two are passive resistors. When a force is applied, the resistance of the active strain gauges changes, causing an imbalance in the bridge circuit. This imbalance results in an output voltage that is proportional to the applied force.
Types of Strain Gauge Load Cells
There are several types of strain gauge load cells, each designed for specific applications and load ranges. Some of the most common types include:
-
Beam load cells: Beam load cells are the most basic type of load cell and are suitable for measuring small to medium loads. They consist of a metal beam with strain gauges bonded to its surface. Beam load cells are available in various configurations, such as single-point, bending beam, and shear beam.
-
S-beam load cells: S-beam load cells are named after their S-shaped metal body. They are designed to measure both tension and compression forces and are commonly used in weighing and force measurement applications.
-
Button load cells: Button load cells are compact, cylindrical-shaped devices that are ideal for measuring small loads in confined spaces. They are often used in medical devices, robotics, and industrial automation.
-
Pancake load cells: Pancake load cells have a flat, disc-shaped design and are typically used for measuring compression forces. They are commonly found in weighing systems, such as floor scales and tank weighing applications.
-
Multi-axis load cells: Multi-axis load cells are designed to measure forces and moments in multiple directions simultaneously. They are often used in advanced applications, such as aerospace testing and robotics.
Load Cell Type | Description | Typical Applications |
---|---|---|
Beam | Simple, versatile design for small to medium loads | Weighing scales, force measurement |
S-beam | S-shaped design for tension and compression | Weighing systems, force measurement |
Button | Compact, cylindrical design for small loads | Medical devices, robotics, industrial automation |
Pancake | Flat, disc-shaped design for compression forces | Floor scales, tank weighing |
Multi-axis | Measures forces and moments in multiple directions | Aerospace testing, robotics |
Advantages of Strain Gauge Load Cells
Strain gauge load cells offer several advantages over other force measurement technologies:
-
High accuracy: Strain gauge load cells can achieve accuracies of 0.03% to 0.25% of full scale, depending on the specific design and application.
-
Wide measuring range: Load cells are available in a wide range of capacities, from a few grams to hundreds of tons, making them suitable for a variety of applications.
-
Durability: With proper installation and maintenance, strain gauge load cells can withstand harsh environments and provide reliable measurements over an extended period.
-
Versatility: Strain gauge load cells can be used to measure various types of forces, including tension, compression, and shear.
-
Cost-effectiveness: Compared to other force measurement technologies, strain gauge load cells offer a cost-effective solution for many applications.
Applications of Strain Gauge Load Cells
Strain gauge load cells are used in a wide range of industries and applications, including:
-
Weighing systems: Load cells are the primary components in electronic weighing systems, such as scales, balances, and checkweighers.
-
Force measurement: Load cells are used to measure forces in various applications, such as material testing, product quality control, and process monitoring.
-
Aerospace and automotive testing: Multi-axis load cells are used to measure forces and moments in aircraft and vehicle components during testing and development.
-
Medical devices: Miniature load cells are used in medical devices, such as infusion pumps and surgical instruments, to monitor and control the applied forces.
-
Structural monitoring: Load cells are used to monitor the loads and stresses on bridges, buildings, and other structures to ensure their safety and integrity.
Frequently Asked Questions (FAQ)
-
What is the difference between a load cell and a force sensor?
A load cell is a type of force sensor that converts an applied force into an electrical signal. While all load cells are force sensors, not all force sensors are load cells. Other types of force sensors include piezoelectric sensors, capacitive sensors, and hydraulic sensors. -
How do I choose the right load cell for my application?
When selecting a load cell, consider factors such as the expected load range, the type of force being measured (tension, compression, or shear), the required accuracy, and the environmental conditions. Consult with a load cell manufacturer or supplier to determine the most suitable type and capacity for your specific application. -
How often should I calibrate my load cell?
The calibration frequency depends on the application, the load cell’s usage, and the required accuracy. In general, load cells should be calibrated at least once a year or according to the manufacturer’s recommendations. More frequent calibration may be necessary for critical applications or harsh environments. -
Can strain gauge load cells be used in hazardous environments?
Yes, certain load cells are designed for use in hazardous environments, such as those with explosive atmospheres or corrosive substances. These load cells are typically constructed with special materials and features, such as intrinsically safe circuits and explosion-proof enclosures, to ensure safe operation. -
How do I install a strain gauge load cell?
Proper installation is crucial for accurate and reliable load cell performance. The load cell should be mounted securely, with the force applied axially and centered on the load cell’s measuring axis. Avoid subjecting the load cell to off-axis loads, shock loads, or overloads. Follow the manufacturer’s installation guidelines and consider factors such as mounting surface, alignment, and cable management.
Conclusion
Strain gauge load cells are essential components in various industries, providing accurate and reliable force measurement solutions. By understanding their construction, working principles, and types, engineers and technicians can select the most suitable load cell for their specific applications. With proper installation, calibration, and maintenance, strain gauge load cells can deliver precise and consistent measurements, enabling better process control, quality assurance, and safety monitoring.
Leave a Reply