Introduction to SolderMask
SolderMask, also known as solder resist or solder stop mask, is a thin layer of polymer that is applied to the copper traces of a printed circuit board (PCB). Its primary function is to prevent solder from bridging between conductors during the soldering process. SolderMask also provides protection against oxidation and contamination, improving the overall reliability and longevity of the PCB.
Over the years, SolderMask technology has undergone significant advancements, resulting in improved performance, durability, and aesthetics. This article will explore the progress made in SolderMask technology and its impact on the PCB industry.
Types of SolderMask
There are several types of SolderMask available, each with its own unique properties and applications. The most common types include:
Liquid Photoimageable SolderMask (LPISM)
LPISM is the most widely used type of SolderMask in the PCB industry. It is applied as a liquid and then exposed to UV light through a photomask, which hardens the exposed areas. The unexposed areas are then removed during the development process, leaving behind a precise and durable SolderMask layer.
Dry Film SolderMask (DFSM)
DFSM is a solid film that is laminated onto the PCB surface using heat and pressure. It is then exposed to UV light through a photomask, and the unexposed areas are removed during development. DFSM offers excellent thickness control and is suitable for high-volume production.
Liquid Photoimageable SolderMask (LPI) vs. Dry Film SolderMask (DFSM)
Property | LPI | DFSM |
---|---|---|
Application Method | Liquid, screen printed or sprayed | Solid film, laminated |
Thickness Control | Good | Excellent |
Resolution | High | Moderate |
Adhesion | Excellent | Good |
Chemical Resistance | Excellent | Good |
Cost | Moderate | High |
Advances in SolderMask Technology
High-Resolution SolderMask
As PCB designs become more complex and feature sizes continue to shrink, the demand for high-resolution SolderMask has increased. High-resolution SolderMask allows for the creation of smaller vias, pads, and traces, enabling denser PCB layouts and improved signal integrity.
Recent developments in SolderMask technology have led to the introduction of ultra-thin SolderMask materials, which can be applied in layers as thin as 5-10 microns. These ultra-thin SolderMasks offer excellent conformity to surface features and improved resolution, making them ideal for high-density PCB designs.
Flexible SolderMask
Flexible electronics have gained popularity in recent years, driving the need for SolderMask materials that can withstand bending and flexing without cracking or delaminating. Flexible SolderMask formulations have been developed to address this need, offering improved elongation and flexibility compared to traditional SolderMask materials.
These flexible SolderMasks are typically based on polyurethane or silicone chemistries and can accommodate bend radii as small as 1mm without compromising the integrity of the SolderMask layer.
Thermally Conductive SolderMask
With the increasing power densities of modern electronic devices, thermal management has become a critical concern in PCB design. Thermally conductive SolderMask materials have been developed to help dissipate heat more efficiently from the PCB surface.
These SolderMasks are formulated with thermally conductive fillers, such as ceramic or metal particles, which improve the thermal conductivity of the SolderMask layer. By facilitating better heat transfer from the components to the PCB substrate, thermally conductive SolderMasks can help reduce hot spots and improve overall system reliability.
Comparison of SolderMask Properties
Property | Standard SolderMask | High-Resolution SolderMask | Flexible SolderMask | Thermally Conductive SolderMask |
---|---|---|---|---|
Thickness | 15-50 microns | 5-10 microns | 15-50 microns | 15-50 microns |
Resolution | Moderate | High | Moderate | Moderate |
Flexibility | Low | Low | High | Low |
Thermal Conductivity | Low | Low | Low | High |
Applications | General purpose | High-density PCBs | Flexible electronics | High-power devices |
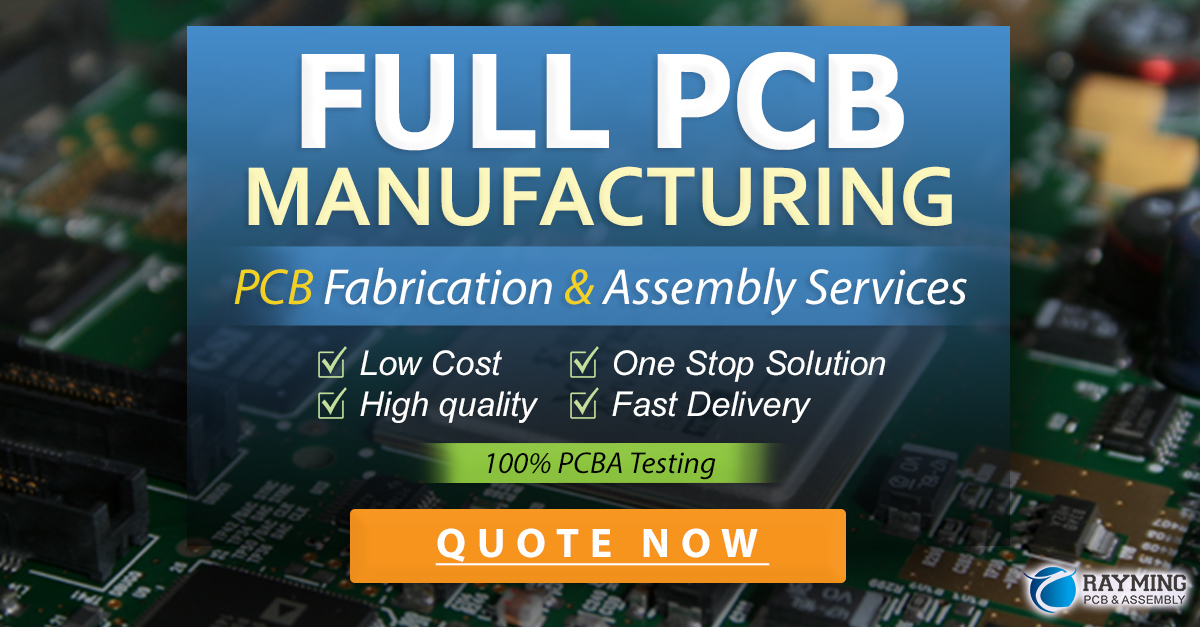
Benefits of Advanced SolderMask Technology
The advancements in SolderMask technology have brought about numerous benefits for the PCB industry, including:
- Improved PCB reliability and longevity
- Enhanced signal integrity and reduced cross-talk
- Increased PCB density and miniaturization
- Better thermal management and reduced hot spots
- Expanded design possibilities for flexible electronics
These benefits have enabled the development of more advanced and sophisticated electronic devices, driving innovation across various industries, such as consumer electronics, automotive, aerospace, and medical devices.
Challenges and Future Developments
Despite the significant progress made in SolderMask technology, there are still challenges that need to be addressed. Some of these challenges include:
- Ensuring compatibility with new PCB materials and surface finishes
- Developing SolderMask formulations with improved environmental resistance
- Reducing the cost of advanced SolderMask materials
- Optimizing the application and processing of SolderMask for high-volume production
Researchers and manufacturers are continually working on overcoming these challenges and developing new SolderMask technologies to meet the evolving needs of the PCB industry. Some of the future developments in SolderMask technology may include:
- Self-healing SolderMask materials that can repair minor defects and damage
- Conductive SolderMask formulations for improved EMI shielding
- Biodegradable and eco-friendly SolderMask materials
- Integration of SolderMask with embedded components and 3D printing technologies
As the electronics industry continues to advance, it is clear that SolderMask technology will play a crucial role in enabling the development of next-generation PCBs and electronic devices.
Frequently Asked Questions (FAQ)
1. What is the purpose of SolderMask on a PCB?
SolderMask serves several purposes on a PCB, including:
– Preventing solder bridging between conductors during the soldering process
– Protecting the copper traces from oxidation and contamination
– Providing electrical insulation between adjacent traces
– Improving the aesthetic appearance of the PCB
2. What are the most common types of SolderMask?
The two most common types of SolderMask are Liquid Photoimageable SolderMask (LPISM) and Dry Film SolderMask (DFSM). LPISM is applied as a liquid and then exposed to UV light, while DFSM is a solid film that is laminated onto the PCB surface.
3. What are the advantages of high-resolution SolderMask?
High-resolution SolderMask allows for the creation of smaller vias, pads, and traces, enabling denser PCB layouts and improved signal integrity. It also offers excellent conformity to surface features and can be applied in ultra-thin layers, making it ideal for high-density PCB designs.
4. How does flexible SolderMask differ from traditional SolderMask?
Flexible SolderMask formulations are designed to withstand bending and flexing without cracking or delaminating. They are typically based on polyurethane or silicone chemistries and offer improved elongation and flexibility compared to traditional SolderMask materials.
5. What are the benefits of thermally conductive SolderMask?
Thermally conductive SolderMask materials are formulated with thermally conductive fillers, such as ceramic or metal particles, which improve the thermal conductivity of the SolderMask layer. By facilitating better heat transfer from the components to the PCB substrate, thermally conductive SolderMasks can help reduce hot spots and improve overall system reliability.
Conclusion
SolderMask technology has come a long way since its inception, with numerous advancements that have improved the performance, durability, and aesthetics of PCBs. From high-resolution and flexible SolderMasks to thermally conductive formulations, these developments have enabled the creation of more advanced and sophisticated electronic devices.
As the electronics industry continues to evolve, it is clear that SolderMask technology will play a vital role in shaping the future of PCB design and manufacturing. By staying at the forefront of SolderMask innovation, PCB manufacturers can ensure that they are well-equipped to meet the ever-increasing demands of the industry and deliver cutting-edge solutions to their customers.
Leave a Reply