Introduction to Soldermask and Nickel-Gold Surface Finish
Soldermask, also known as solder resist, is a thin layer of polymer applied to the copper traces of a printed circuit board (PCB) to prevent oxidation and provide protection against solder bridging during the assembly process. It also serves as an insulating layer, preventing short circuits between adjacent traces. In the case of via-holes, which are small holes drilled through the PCB to connect different layers, the application of soldermask can be crucial for ensuring the reliability and functionality of the board.
Nickel-Gold (ENIG) is a popular surface finish for PCBs, particularly in high-reliability applications such as aerospace, military, and medical devices. The ENIG process involves plating a thin layer of nickel onto the copper traces, followed by a thin layer of gold. The nickel layer provides a barrier against copper diffusion and improves the adhesion of the gold layer, while the gold layer offers excellent oxidation resistance and enhances the solderability of the board.
Advantages of Soldermask on Via-Holes
Applying soldermask on via-holes offers several advantages:
-
Protection against contamination: Soldermask prevents the ingress of contaminants, such as dust, moisture, and chemicals, into the via-holes, which can cause reliability issues.
-
Improved insulation: Soldermask provides an additional insulating layer, reducing the risk of short circuits between adjacent via-holes or traces.
-
Enhanced mechanical stability: Soldermask helps to reinforce the via-holes, improving the mechanical stability of the PCB and reducing the risk of via-hole cracking or delamination.
-
Better solder joint reliability: By preventing solder from wicking into the via-holes during the assembly process, soldermask promotes the formation of reliable solder joints on the surface of the board.
Challenges of Applying Soldermask on Via-Holes with ENIG Finish
While applying soldermask on via-holes offers numerous benefits, it can also present some challenges, particularly when used in conjunction with the ENIG surface finish:
-
Adhesion issues: The smooth, non-porous nature of the gold layer can make it difficult for the soldermask to adhere properly to the surface of the via-holes.
-
Compatibility concerns: Some soldermask materials may not be compatible with the chemicals used in the ENIG process, leading to potential delamination or degradation of the soldermask.
-
Inadequate coverage: If the soldermask application process is not optimized, it may result in incomplete or inconsistent coverage of the via-holes, leaving some areas exposed and vulnerable to contamination.
Optimizing Soldermask Application on Via-Holes with ENIG Finish
To overcome the challenges associated with applying soldermask on via-holes with ENIG finish, several strategies can be employed:
1. Surface Preparation
Proper surface preparation is essential for ensuring good adhesion between the soldermask and the ENIG-finished via-holes. This can involve:
- Cleaning: Thoroughly cleaning the surface of the PCB to remove any contaminants, such as oils, dust, or residues from previous processing steps.
- Roughening: Slightly roughening the surface of the gold layer using methods such as chemical etching or plasma treatment to improve the mechanical interlocking between the soldermask and the ENIG finish.
2. Soldermask Material Selection
Choosing the right soldermask material is crucial for achieving optimal performance and compatibility with the ENIG finish. Some key considerations include:
- Chemical compatibility: Select a soldermask material that is compatible with the chemicals used in the ENIG process to minimize the risk of delamination or degradation.
- Thermal stability: Ensure that the soldermask material can withstand the high temperatures encountered during the soldering process without degrading or losing adhesion.
- Flexibility: Opt for a soldermask material with good flexibility to accommodate any thermal or mechanical stresses that may arise during the PCB’s lifecycle.
3. Application Process Optimization
Optimizing the soldermask application process can help ensure consistent and reliable coverage of the via-holes. This may involve:
- Thickness control: Carefully controlling the thickness of the soldermask layer to ensure adequate coverage of the via-holes without causing excessive buildup or pooling.
- Multiple coats: Applying multiple thin coats of soldermask, rather than a single thick coat, can help improve the uniformity and consistency of the coverage.
- Curing conditions: Optimizing the curing conditions, such as temperature and duration, to ensure complete crosslinking of the soldermask material and maximize its adhesion and durability.
Testing and Qualification
To ensure the reliability and performance of soldermask on via-holes with ENIG finish, thorough testing and qualification procedures should be implemented. Some common tests include:
1. Adhesion Testing
Adhesion testing is performed to evaluate the bond strength between the soldermask and the ENIG-finished via-holes. Common methods include:
- Tape test: A piece of adhesive tape is applied to the soldermask surface and then peeled off. The amount of soldermask removed by the tape provides an indication of the adhesion strength.
- Cross-hatch test: A pattern of perpendicular cuts is made in the soldermask surface, and tape is applied and peeled off. The percentage of soldermask remaining on the surface is used to assess the adhesion.
2. Thermal Shock Testing
Thermal shock testing exposes the PCB to rapid changes in temperature to evaluate the soldermask’s ability to withstand thermal stresses without delaminating or cracking. The test typically involves cycling the PCB between extreme high and low temperatures for a specified number of cycles.
3. Moisture Resistance Testing
Moisture resistance testing assesses the soldermask’s ability to protect the via-holes from the ingress of moisture, which can lead to corrosion and other reliability issues. Common tests include:
- Pressure cooker test: The PCB is exposed to high-temperature, high-humidity conditions in a pressure cooker for a specified duration.
- Temperature-humidity bias (THB) test: The PCB is subjected to elevated temperature and humidity conditions while being electrically biased to simulate real-world operating conditions.
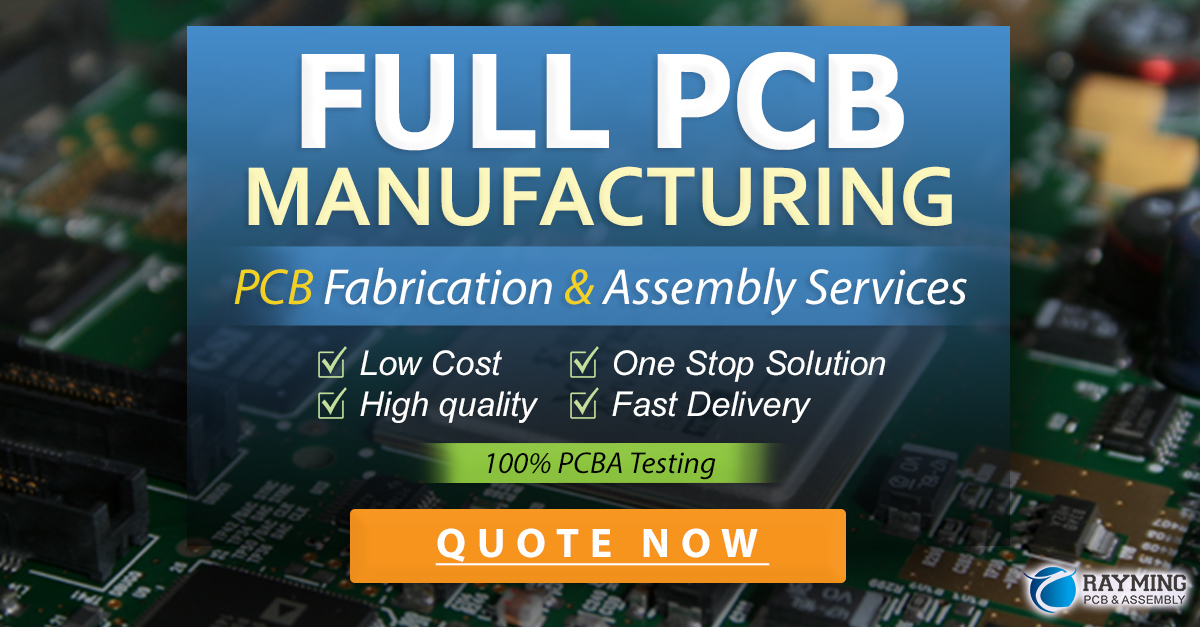
Case Studies and Real-World Applications
The use of soldermask on via-holes with ENIG finish has been successfully employed in various industries and applications. Some notable examples include:
1. Aerospace
In the aerospace industry, PCBs are subject to harsh environmental conditions, including extreme temperatures, vibration, and exposure to moisture and chemicals. The combination of soldermask and ENIG finish on via-holes has been used to enhance the reliability and durability of PCBs in avionics systems, satellite communications, and other critical applications.
2. Medical Devices
Medical devices often require high-reliability PCBs that can withstand repeated sterilization cycles and exposure to bodily fluids. Soldermask on via-holes with ENIG finish has been used in the manufacture of PCBs for implantable devices, diagnostic equipment, and other medical applications to ensure long-term reliability and patient safety.
3. Automotive Electronics
The automotive industry has increasingly adopted PCBs with soldermask on via-holes and ENIG finish for use in engine control units, infotainment systems, and advanced driver assistance systems (ADAS). The enhanced protection against contamination and improved solder joint reliability offered by this combination have helped to improve the performance and longevity of automotive electronics.
Frequently Asked Questions (FAQ)
-
What is the purpose of applying soldermask on via-holes?
Soldermask on via-holes serves to protect the via-holes from contamination, improve insulation, enhance mechanical stability, and promote reliable solder joint formation. -
Why is the ENIG surface finish commonly used in combination with soldermask on via-holes?
The ENIG surface finish offers excellent oxidation resistance and enhances the solderability of the PCB, making it an ideal choice for use with soldermask on via-holes in high-reliability applications. -
What challenges can arise when applying soldermask on via-holes with ENIG finish?
Challenges include potential adhesion issues between the soldermask and the smooth gold surface, compatibility concerns between the soldermask material and ENIG process chemicals, and the risk of inadequate or inconsistent coverage of the via-holes. -
How can the adhesion of soldermask to ENIG-finished via-holes be improved?
Adhesion can be improved through proper surface preparation, such as cleaning and roughening the gold surface, as well as by selecting a soldermask material that is compatible with the ENIG process and has good flexibility. -
What testing methods are used to qualify the reliability of soldermask on via-holes with ENIG finish?
Common testing methods include adhesion testing (tape test and cross-hatch test), thermal shock testing, and moisture resistance testing (pressure cooker test and temperature-humidity bias test).
Conclusion
The application of soldermask on via-holes in combination with the ENIG surface finish offers numerous benefits for PCBs in high-reliability applications. By providing protection against contamination, improving insulation, enhancing mechanical stability, and promoting reliable solder joint formation, this approach can significantly enhance the performance and longevity of PCBs in demanding environments.
However, achieving optimal results requires careful consideration of surface preparation, soldermask material selection, and application process optimization. Additionally, thorough testing and qualification procedures are essential for ensuring the reliability and performance of soldermask on via-holes with ENIG finish.
As the electronics industry continues to evolve and push the boundaries of performance and reliability, the use of soldermask on via-holes with ENIG finish is likely to remain a key strategy for meeting the challenges of today and tomorrow.
Leave a Reply