Introduction to SMT Line
Surface Mount Technology (SMT) has revolutionized the printed circuit board (PCB) manufacturing industry since its introduction in the 1960s. SMT line, an essential component of PCB manufacturing, is a highly automated and efficient production process that involves placing surface mount devices (SMDs) onto a PCB. This technology has enabled the production of smaller, lighter, and more complex electronic devices, making it an indispensable part of modern electronics manufacturing.
What is an SMT Line?
An SMT line is a series of machines and processes that work together to assemble PCBs by placing SMDs onto the board’s surface. The line typically consists of several key components, including:
- Solder paste printer
- Pick-and-place machine
- Reflow oven
- Inspection systems
Each component plays a crucial role in ensuring the accuracy, reliability, and efficiency of the SMT process.
Advantages of SMT Line
SMT line offers numerous advantages over traditional through-hole technology (THT), making it the preferred choice for most PCB manufacturers. Some of the key benefits include:
- Increased component density
- Improved reliability
- Reduced production costs
- Faster assembly times
- Enhanced design flexibility
By leveraging these advantages, manufacturers can produce high-quality PCBs that meet the demanding requirements of modern electronics.
Key Components of an SMT Line
Solder Paste Printer
The solder paste printer is the first machine in the SMT line. Its primary function is to apply solder paste onto the PCB’s surface in a precise and controlled manner. The printer uses a stencil, which is a thin metal sheet with openings that correspond to the PCB’s solder pads. The solder paste is then squeezed through the stencil openings onto the PCB using a squeegee blade.
Types of Solder Paste Printers
There are two main types of solder paste printers:
- Manual printers
- Automated printers
Manual printers require an operator to align the stencil and PCB manually, while automated printers use vision systems and motorized controls to perform these tasks automatically. Automated printers offer higher accuracy, consistency, and throughput compared to manual printers.
Solder Paste Printing Process
The solder paste printing process involves the following steps:
- Stencil alignment
- Solder paste application
- Stencil cleaning
- Inspection
Proper control of the printing process is crucial for ensuring the quality and reliability of the assembled PCBs.
Pick-and-Place Machine
The pick-and-place (P&P) machine is responsible for picking up SMDs from component feeders and placing them onto the solder paste-printed PCB. Modern P&P machines are highly automated and can place thousands of components per hour with exceptional accuracy.
Types of Pick-and-Place Machines
P&P machines can be classified into three main categories based on their placement speed and accuracy:
- High-speed machines
- Medium-speed machines
- Low-speed machines
High-speed machines are capable of placing the smallest components at speeds of up to 100,000 components per hour (CPH), while medium-speed machines typically have a placement rate of 20,000 to 50,000 CPH. Low-speed machines are used for larger components and have placement rates below 20,000 CPH.
Pick-and-Place Process
The P&P process involves the following steps:
- Component pickup
- Vision inspection
- Component placement
- Post-placement inspection
Advanced P&P machines use vision systems to inspect components before and after placement to ensure accuracy and detect any defects.
Reflow Oven
After the SMDs are placed onto the PCB, the board enters the reflow oven, where the solder paste is melted and forms a permanent electrical and mechanical connection between the components and the PCB. Reflow ovens use a carefully controlled temperature profile to ensure proper solder joint formation without damaging the components.
Reflow Soldering Process
The reflow soldering process consists of four main stages:
- Preheat
- Soak
- Reflow
- Cooling
Each stage is critical for achieving a reliable solder joint and minimizing defects such as tombstoning, bridging, and solder balling.
Types of Reflow Ovens
There are two primary types of reflow ovens used in SMT lines:
- Convection ovens
- Infrared (IR) ovens
Convection ovens use hot air to heat the PCB and components, while IR ovens use infrared radiation. Some ovens combine both heating methods to achieve optimal results.
Inspection Systems
Inspection systems are used throughout the SMT line to ensure the quality and reliability of the assembled PCBs. There are several types of inspection systems, each focusing on different aspects of the assembly process.
Solder Paste Inspection (SPI)
SPI systems use 3D vision technology to inspect the solder paste deposit after the printing process. They measure the volume, height, and area of the solder paste to detect any defects such as insufficient or excess paste, bridging, or misalignment.
Automated Optical Inspection (AOI)
AOI systems use high-resolution cameras and advanced image processing algorithms to inspect the assembled PCB for defects such as missing or misaligned components, solder bridges, and insufficient or excess solder. AOI is typically performed after the reflow process.
X-Ray Inspection (AXI)
AXI systems use X-ray technology to inspect solder joints and components that are not visible from the surface, such as ball grid arrays (BGAs) and flip chips. AXI can detect defects such as voids, shorts, and opens in the solder joints.
SMT Line Process Flow
The SMT line process flow consists of several sequential steps that transform a bare PCB into a fully assembled and functional board. The typical process flow includes:
- Solder paste printing
- Pick-and-place
- Reflow soldering
- Inspection
- Rework (if necessary)
- Final assembly and testing
Each step in the process flow is critical for ensuring the quality and reliability of the final product. Manufacturers must carefully control and monitor each step to minimize defects and maximize yield.
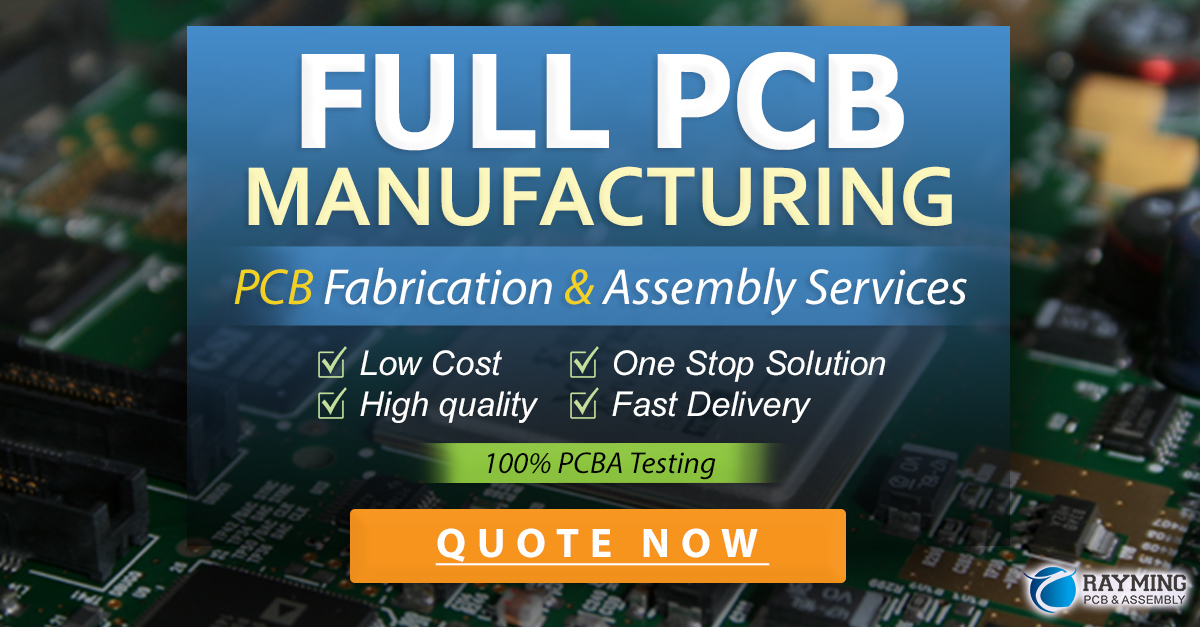
Advantages of SMT Line in PCB Manufacturing
SMT line offers numerous advantages over traditional through-hole technology (THT) in PCB manufacturing. Some of the key benefits include:
Increased Component Density
SMT allows for the use of smaller components and finer pitch sizes, enabling manufacturers to pack more functionality into a smaller PCB area. This increased component density is essential for modern electronics, which require compact and lightweight designs.
Improved Reliability
SMT components have shorter leads and are mounted directly onto the PCB surface, reducing the risk of mechanical stress and vibration-induced failures. Additionally, the SMT process allows for more precise control over solder joint formation, resulting in stronger and more reliable connections.
Reduced Production Costs
SMT line is highly automated, requiring fewer manual operations compared to THT. This automation leads to reduced labor costs and increased production efficiency. Moreover, SMT components are generally less expensive than their THT counterparts, contributing to overall cost savings.
Faster Assembly Times
The high-speed placement capabilities of modern P&P machines, combined with the efficiency of the reflow soldering process, enable manufacturers to assemble PCBs much faster than with THT. This increased throughput translates to shorter lead times and higher production volumes.
Enhanced Design Flexibility
SMT allows for greater design flexibility, as components can be placed on both sides of the PCB, enabling more complex and compact layouts. This flexibility is crucial for meeting the ever-increasing demands of modern electronics.
Challenges and Considerations in SMT Line Implementation
While SMT line offers numerous benefits, implementing and maintaining an efficient SMT process comes with its own set of challenges and considerations.
Equipment Investment
Setting up an SMT line requires significant capital investment in equipment such as solder paste printers, P&P machines, reflow ovens, and inspection systems. Manufacturers must carefully evaluate their production requirements and budget when selecting equipment to ensure a cost-effective solution.
Process Control and Optimization
Achieving a high-quality and reliable SMT process requires careful control and optimization of each step in the line. Manufacturers must establish and maintain strict process parameters, such as stencil design, solder paste viscosity, component placement accuracy, and reflow temperature profiles. Regular monitoring and adjustments are necessary to ensure consistent results.
Training and Skill Development
Operating and maintaining an SMT line requires specialized skills and knowledge. Manufacturers must invest in training their personnel to ensure they can effectively operate, troubleshoot, and maintain the equipment. Continual skill development is essential to keep pace with advances in technology and best practices.
Supply Chain Management
Ensuring a smooth and uninterrupted SMT process requires effective supply chain management. Manufacturers must establish reliable sources for components, solder paste, and other consumables, as well as maintain adequate inventory levels to avoid production delays. Close collaboration with suppliers is crucial for managing lead times and ensuring quality.
Quality Control and Traceability
Implementing a robust quality control system is essential for identifying and addressing defects in the SMT process. Manufacturers must establish clear quality metrics and use inspection systems to monitor and verify the quality of the assembled PCBs. Traceability is also critical for identifying the root cause of defects and implementing corrective actions.
Future Trends and Developments in SMT Line Technology
As the electronics industry continues to evolve, SMT line technology must adapt to meet the changing requirements of PCB manufacturing. Some of the key trends and developments shaping the future of SMT include:
Miniaturization and Advanced Packaging
The demand for smaller, more complex electronic devices is driving the need for even greater component density and finer pitch sizes. Advancements in SMT equipment, such as high-resolution solder paste printers and ultra-high-speed P&P machines, will enable manufacturers to assemble PCBs with increasingly miniaturized components and advanced packaging technologies.
Industry 4.0 and Smart Factory Integration
The integration of Industry 4.0 technologies, such as the Internet of Things (IoT), big data analytics, and artificial intelligence (AI), will transform SMT lines into smart, connected systems. These technologies will enable real-time monitoring, predictive maintenance, and autonomous process optimization, leading to increased efficiency, quality, and flexibility.
Sustainable and Eco-Friendly Practices
As environmental concerns continue to grow, manufacturers will need to adopt more sustainable and eco-friendly practices in their SMT processes. This includes the use of lead-free solder alloys, low-VOC (volatile organic compound) solder pastes, and energy-efficient equipment. Additionally, manufacturers will need to focus on reducing waste and implementing recycling programs for end-of-life PCBs.
Flexible and Agile Manufacturing
The increasing demand for customization and shorter product life cycles will require SMT lines to be more flexible and agile. Manufacturers will need to invest in modular, reconfigurable equipment and develop strategies for quick changeovers and mixed-model production. Agile manufacturing practices, such as lean and six sigma, will be critical for optimizing efficiency and responsiveness.
Conclusion
SMT line has revolutionized the PCB manufacturing industry, enabling the production of smaller, more complex, and more reliable electronic devices. By leveraging the advantages of SMT technology, manufacturers can achieve increased component density, improved reliability, reduced production costs, faster assembly times, and enhanced design flexibility.
However, implementing and maintaining an efficient SMT process requires careful consideration of equipment investment, process control, skill development, supply chain management, and quality control. As the electronics industry continues to evolve, SMT line technology must adapt to meet the challenges of miniaturization, advanced packaging, Industry 4.0 integration, sustainable practices, and agile manufacturing.
By staying at the forefront of these trends and developments, PCB manufacturers can ensure their SMT lines remain efficient, cost-effective, and competitive in the dynamic landscape of electronics manufacturing.
Frequently Asked Questions (FAQ)
1. What is the difference between SMT and through-hole technology (THT)?
SMT involves placing components directly onto the surface of the PCB, while THT requires components to be inserted through holes in the board and soldered on the opposite side. SMT allows for smaller components, higher density, and faster assembly compared to THT.
2. What are the main components of an SMT line?
The main components of an SMT line include:
1. Solder paste printer
2. Pick-and-place machine
3. Reflow oven
4. Inspection systems
Each component plays a crucial role in the SMT assembly process, from applying solder paste and placing components to soldering and inspecting the assembled PCBs.
3. How does the reflow soldering process work in an SMT line?
The reflow soldering process involves passing the PCB with placed components through a reflow oven, which uses a carefully controlled temperature profile to melt the solder paste and form a permanent connection between the components and the board. The process consists of four main stages: preheat, soak, reflow, and cooling.
4. What types of inspection systems are used in an SMT line?
There are three main types of inspection systems used in an SMT line:
1. Solder Paste Inspection (SPI)
2. Automated Optical Inspection (AOI)
3. X-Ray Inspection (AXI)
Each system focuses on different aspects of the assembly process, from inspecting solder paste deposits to verifying component placement and solder joint quality.
5. What are some of the key challenges in implementing and maintaining an efficient SMT line?
Some of the key challenges in implementing and maintaining an efficient SMT line include:
1. Equipment investment
2. Process control and optimization
3. Training and skill development
4. Supply chain management
5. Quality control and traceability
Manufacturers must carefully address these challenges to ensure a cost-effective, high-quality, and reliable SMT assembly process.
Leave a Reply