What is SMT-PCB Assembly?
SMT-PCB assembly is a process in which surface mount components are placed and soldered onto the surface of a printed circuit board. Unlike through-hole technology, SMT components have smaller leads or no leads at all, allowing for higher component density and smaller PCB sizes. The SMT assembly process typically involves three main steps: solder paste application, component placement, and soldering.
Advantages of SMT-PCB Assembly
SMT-PCB assembly offers several advantages over through-hole technology:
- Higher component density: SMT components are smaller, allowing for more components to be placed on a single PCB.
- Smaller PCB sizes: With higher component density, PCBs can be made smaller, leading to more compact electronic devices.
- Faster assembly: SMT assembly is highly automated, resulting in faster production times and lower labor costs.
- Improved reliability: SMT components have shorter leads, reducing the risk of component failure due to lead damage or vibration.
- Better high-frequency performance: SMT components have shorter leads, minimizing parasitic inductance and capacitance, leading to better high-frequency performance.
SMT-PCB Assembly Process
The SMT-PCB assembly process consists of three main steps:
- Solder paste application: A stencil is used to apply solder paste onto the PCB’s surface at specific locations where components will be placed.
- Component placement: Surface mount components are placed onto the solder paste using pick-and-place machines or manual methods.
- Soldering: The PCB is heated in a reflow oven, causing the solder paste to melt and form a strong bond between the components and the PCB.
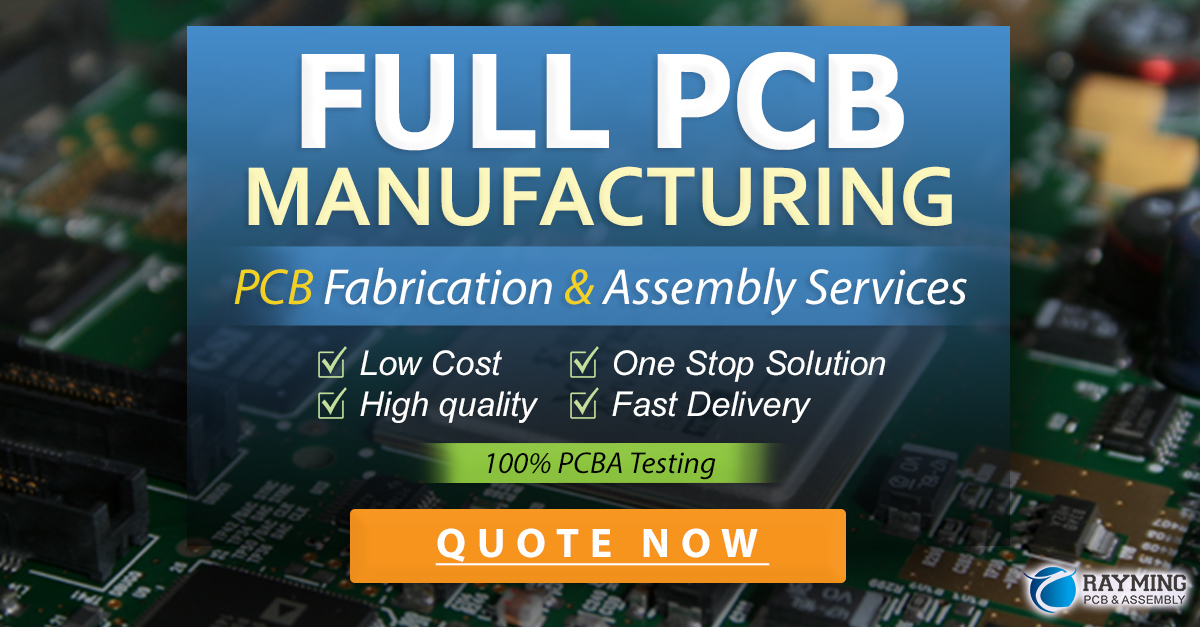
Types of SMT Components
There are various types of SMT components, each with different package styles and sizes. Some common types include:
- Chip components: Resistors, capacitors, and inductors in small, rectangular packages (e.g., 0201, 0402, 0603, 0805, 1206).
- SOT (Small Outline Transistor): Transistors and diodes in small, plastic packages with gull-wing leads.
- QFP (Quad Flat Pack): Integrated circuits with leads on all four sides of the package.
- BGA (Ball Grid Array): Integrated circuits with an array of solder balls underneath the package for connection to the PCB.
- CSP (Chip Scale Package): Integrated circuits with package sizes similar to the die size, often used in mobile devices.
Solder Paste and Stencils
Solder paste is a mixture of tiny solder particles suspended in a flux medium. It is applied to the PCB using a stencil, which is a thin metal sheet with apertures that correspond to the component pad locations on the PCB. The stencil is placed over the PCB, and solder paste is spread across the surface using a squeegee. When the stencil is removed, solder paste remains on the pads, ready for component placement.
Pick-and-Place Machines
Pick-and-place machines are automated systems that place SMT components onto the PCB with high precision and speed. These machines use vacuum nozzles to pick up components from feeders and place them onto the solder paste on the PCB. Modern pick-and-place machines can place thousands of components per hour, significantly reducing assembly time and costs.
Reflow Soldering
Reflow soldering is the process of heating the PCB assembly to melt the solder paste and form a strong bond between the components and the PCB. The reflow process typically involves four stages:
- Preheat: The PCB is gradually heated to activate the flux and remove moisture from the solder paste.
- Soak: The temperature is maintained to allow the components and PCB to reach a uniform temperature.
- Reflow: The temperature is increased above the solder’s melting point, causing the solder to melt and form a bond between the components and the PCB.
- Cooling: The PCB is cooled, allowing the solder to solidify and form a strong, reliable connection.
Inspection and Testing
After the SMT-PCB assembly process is complete, the PCB undergoes inspection and testing to ensure its quality and functionality. Common inspection methods include:
- Visual inspection: Manual or automated visual inspection to check for component placement accuracy, solder joint quality, and any visible defects.
- Automated Optical Inspection (AOI): Machine vision systems that compare the assembled PCB to a reference image to detect defects and placement errors.
- X-ray inspection: Used to inspect solder joints hidden under components, such as BGAs or CSPs.
- In-Circuit Testing (ICT): Electrical tests performed using a bed-of-nails fixture to verify the functionality of individual components and circuits.
- Functional testing: Testing the assembled PCB to ensure it performs as intended in its final application.
Design for Manufacturing (DFM)
To ensure successful SMT-PCB assembly, it is essential to consider Design for Manufacturing (DFM) principles during the PCB design stage. DFM guidelines help designers create PCBs that are easier to manufacture, more reliable, and cost-effective. Some key DFM considerations for SMT-PCB assembly include:
- Component selection: Choose components that are compatible with the SMT assembly process and available in tape-and-reel packaging for automated placement.
- Pad design: Ensure component pads are sized and spaced appropriately to accommodate solder paste application and prevent bridging.
- Clearances: Maintain sufficient clearances between components to allow for placement and inspection.
- Panelization: Design PCBs to be panelized for efficient manufacturing and to minimize handling damage.
- Fiducial marks: Include fiducial marks on the PCB to provide reference points for pick-and-place machines and inspection systems.
By following DFM guidelines, designers can minimize the risk of assembly issues and improve the overall quality and reliability of the final product.
Frequently Asked Questions (FAQ)
-
Q: What is the difference between SMT and through-hole technology?
A: SMT components are placed and soldered onto the surface of the PCB, while through-hole components have leads that are inserted through holes in the PCB and soldered on the opposite side. SMT allows for higher component density, smaller PCB sizes, and faster assembly compared to through-hole technology. -
Q: Can SMT and through-hole components be used on the same PCB?
A: Yes, it is possible to use both SMT and through-hole components on the same PCB. This is called a mixed-technology PCB assembly. However, it is essential to consider the assembly process and ensure that the through-hole components are compatible with the SMT assembly process. -
Q: What is the role of flux in solder paste?
A: Flux is a chemical compound that helps to remove oxides and impurities from the surfaces of the components and PCB pads during the soldering process. It also promotes the flow and wetting of the molten solder, ensuring a strong and reliable bond between the components and the PCB. -
Q: How do I select the right solder paste for my SMT-PCB assembly?
A: When selecting solder paste, consider factors such as the alloy composition, particle size, flux type, and viscosity. The solder paste should be compatible with the components, PCB surface finish, and reflow profile. Consult with your solder paste supplier or assembly service provider to choose the most suitable solder paste for your application. -
Q: What are some common defects in SMT-PCB assembly, and how can they be prevented?
A: Common defects in SMT-PCB assembly include component misalignment, solder bridging, tombstoning (component standing on end), and insufficient or excessive solder. These defects can be prevented by ensuring proper stencil design, solder paste application, component placement, and reflow profile optimization. Regular maintenance of assembly equipment and adherence to DFM guidelines can also help minimize the occurrence of defects.
In conclusion, SMT-PCB assembly is a critical process in the production of modern electronic devices. By understanding the basics of SMT technology, its advantages, the assembly process, and key considerations such as component types, solder paste, and inspection methods, designers and manufacturers can create high-quality, reliable, and cost-effective PCB assemblies. Adhering to DFM principles and working closely with experienced assembly service providers can help ensure the success of your SMT-PCB assembly projects.
Leave a Reply