What is Selective Soldering?
Selective soldering, also known as Selsoldering, is a process used in electronics manufacturing to solder specific components onto printed circuit boards (PCBs). Unlike wave soldering, which solders all components simultaneously, selective soldering targets individual components or groups of components, allowing for greater precision and flexibility in the assembly process.
Key Advantages of Selective Soldering
- Precision: Selsoldering enables the soldering of specific components without affecting nearby components or sensitive areas of the PCB.
- Flexibility: The process accommodates a wide range of component types, sizes, and configurations, making it suitable for complex PCB designs.
- Cost-effective: Selective soldering reduces the need for manual soldering, leading to increased efficiency and lower labor costs.
- Quality: The targeted approach minimizes the risk of thermal damage to components and the PCB, resulting in higher-quality solder joints.
The Selective Soldering Process
Step 1: PCB Preparation
Before the selective soldering process begins, the PCB undergoes a series of preparations:
- Solder paste application: Solder paste is applied to the PCB pads where components will be soldered.
- Component placement: Components are placed onto the PCB using pick-and-place machines or manual placement.
- Prebaking: The PCB is heated to activate the flux in the solder paste and remove any moisture.
Step 2: Selective Soldering Machine Setup
Selective soldering machines are configured according to the specific requirements of the PCB and components being soldered:
- Nozzle selection: The appropriate nozzle size and shape are chosen based on the component and pad dimensions.
- Solder pot preparation: The solder pot is filled with the appropriate solder alloy and heated to the required temperature.
- Nitrogen inerting: Nitrogen gas is used to create an inert atmosphere, preventing oxidation during the soldering process.
Step 3: Soldering Process
The selective soldering process involves the following steps:
- Positioning: The PCB is positioned in the machine, aligning the components to be soldered with the soldering nozzle.
- Preheating: The PCB is preheated to the appropriate temperature to minimize thermal shock during soldering.
- Fluxing: Liquid flux is applied to the solder joint area to improve solder wetting and prevent oxidation.
- Soldering: The soldering nozzle applies molten solder to the component leads and PCB pads, creating a solder joint.
- Cooling: The solder joint is cooled, typically with the aid of forced air or nitrogen, to solidify the connection.
Step 4: Inspection and Quality Control
After the selective soldering process, the PCB undergoes inspection and quality control:
- Visual inspection: The solder joints are visually inspected for defects such as bridging, insufficient solder, or poor wetting.
- Automated optical inspection (AOI): AOI systems use cameras and image processing software to detect soldering defects.
- X-ray inspection: X-ray systems may be used to inspect solder joints hidden under components or in multi-layer PCBs.
Factors Affecting Selective Soldering Quality
Several factors influence the quality of selective soldering:
Solder Alloy Selection
The choice of solder alloy depends on the specific requirements of the application, such as:
- Melting temperature
- Mechanical strength
- Electrical conductivity
- Compatibility with the PCB and component materials
Common solder alloys used in selective soldering include:
Alloy | Composition | Melting Temperature (°C) |
---|---|---|
Sn63/Pb37 | 63% tin, 37% lead | 183 |
SAC305 | 96.5% tin, 3% silver, 0.5% copper | 217-220 |
Sn99.3/Cu0.7 | 99.3% tin, 0.7% copper | 227 |
Flux Selection
Flux plays a crucial role in the selective soldering process by:
- Removing oxides from the solder joint surfaces
- Preventing oxidation during soldering
- Improving solder wetting and flow
Flux types commonly used in selective soldering include:
Flux Type | Activation Method | Residue | Cleaning Required |
---|---|---|---|
Rosin | Heat | Non-conductive, non-corrosive | Optional |
Water-soluble | Heat | Conductive, corrosive | Yes |
No-clean | Heat | Minimal, non-corrosive | No |
Soldering Temperature and Time
The soldering temperature and time must be carefully controlled to ensure optimal solder joint quality:
- Insufficient temperature or time may result in poor solder wetting and weak joints.
- Excessive temperature or time may cause thermal damage to components or the PCB.
Typical soldering temperatures and times for common solder alloys:
Alloy | Soldering Temperature (°C) | Dwell Time (seconds) |
---|---|---|
Sn63/Pb37 | 250-260 | 2-4 |
SAC305 | 270-280 | 3-5 |
Sn99.3/Cu0.7 | 280-290 | 3-5 |
Nozzle Design and Placement
The design and placement of the soldering nozzle significantly impact the quality of the solder joint:
- Nozzle size and shape should be matched to the component and pad dimensions to ensure adequate solder coverage.
- Nozzle placement must be precise to prevent solder bridging or insufficient solder on the joint.
Common nozzle types used in selective soldering include:
- Single-point nozzles: Used for soldering individual components or small groups of components.
- Multi-point nozzles: Used for soldering multiple components simultaneously, reducing cycle time.
- Jet nozzles: Used for soldering fine-pitch components or hard-to-reach areas of the PCB.
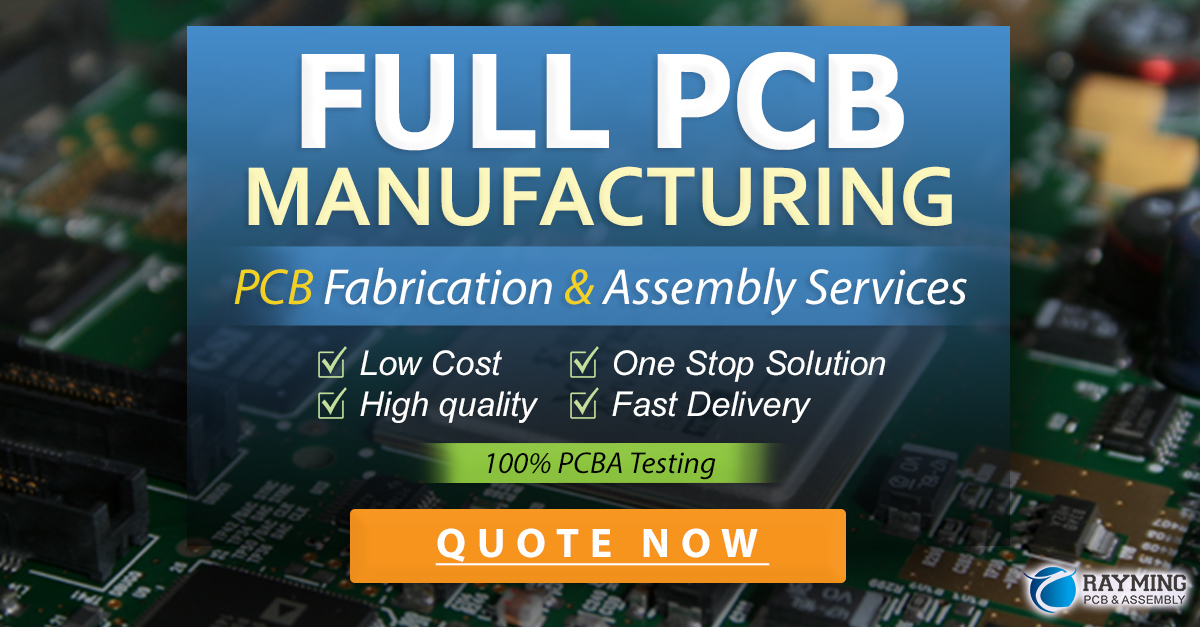
Troubleshooting Common Selective Soldering Defects
Despite careful process control, defects can occur in selective soldering. Some common defects and their causes include:
Solder Bridging
Solder bridging occurs when excess solder connects adjacent pads or component leads, creating a short circuit.
Causes:
– Excessive solder volume
– Incorrect nozzle placement
– Insufficient spacing between pads or leads
Solutions:
– Adjust solder volume
– Improve nozzle placement accuracy
– Increase spacing between pads or leads in PCB design
Insufficient Solder
Insufficient solder refers to a lack of solder on the joint, resulting in a weak or open connection.
Causes:
– Inadequate solder volume
– Poor solder wetting due to contamination or oxidation
– Incorrect soldering temperature or time
Solutions:
– Increase solder volume
– Ensure proper cleaning and fluxing of the solder joint area
– Optimize soldering temperature and time
Tombstoning
Tombstoning occurs when a surface-mount component stands up on one end due to uneven solder solidification.
Causes:
– Uneven heating of the component leads
– Difference in pad sizes or solder volume on either end of the component
– Rapid cooling of the solder joint
Solutions:
– Ensure even heating of the component leads
– Match pad sizes and solder volume on both ends of the component
– Control cooling rate to allow for even solder solidification
Frequently Asked Questions (FAQ)
- What types of components can be soldered using selective soldering?
Selective soldering can accommodate a wide range of through-hole and surface-mount components, including: - Connectors
- Transformers
- Switches
- Large integrated circuits (ICs)
-
Capacitors and resistors
-
How does selective soldering compare to wave soldering in terms of efficiency and quality?
Selective soldering offers several advantages over wave soldering: - Higher precision, as only specific components are soldered
- Reduced thermal stress on components and the PCB
- Flexibility to accommodate a wider range of component types and sizes
-
Lower energy consumption and operating costs
-
Can selective soldering be used for double-sided PCBs?
Yes, selective soldering can be used for double-sided PCBs. The process typically involves: - Soldering the bottom side components first
- Flipping the PCB and soldering the top side components
-
Using specialized fixtures to hold components in place during the flipping process
-
What is the role of nitrogen in the selective soldering process?
Nitrogen is used in selective soldering to create an inert atmosphere, which: - Prevents oxidation of the solder joint surfaces
- Improves solder wetting and flow
-
Reduces the formation of solder balls and other defects
-
How can I optimize my PCB design for selective soldering?
To optimize your PCB design for selective soldering, consider the following: - Ensure adequate spacing between pads and components to prevent solder bridging
- Use uniform pad sizes and shapes to promote even solder distribution
- Avoid placing sensitive components near areas that will be selectively soldered
- Consider the accessibility of components for the soldering nozzle
In conclusion, selective soldering is a versatile and precise method for soldering specific components onto PCBs. By understanding the process, factors affecting solder joint quality, and common defects, manufacturers can optimize their selective soldering operations to produce high-quality, reliable electronic assemblies.
As the electronics industry continues to evolve, with increasingly complex PCB designs and diverse component types, selective soldering will remain an essential tool for efficient and cost-effective manufacturing. By staying up-to-date with the latest selective soldering technologies and best practices, manufacturers can ensure their products meet the highest standards of quality and performance.
Leave a Reply