Introduction to RoHS 2 and Its Impact on PCB Manufacturing
The Restriction of Hazardous Substances Directive (RoHS) is an EU directive that aims to restrict the use of certain hazardous substances in electrical and electronic equipment (EEE). The original RoHS directive, also known as RoHS 1, was adopted in 2003 and came into effect in 2006. In 2011, the EU revised the directive, resulting in RoHS 2 (Directive 2011/65/EU), which became effective in 2013. RoHS 2 expands the scope of the original directive and introduces new obligations for EEE manufacturers, including those producing printed circuit boards (PCBs).
What is RoHS 2?
RoHS 2 is an updated version of the original RoHS directive that aims to further restrict the use of hazardous substances in EEE. The directive applies to all EEE placed on the EU market, including PCBs. RoHS 2 restricts the use of the following ten substances:
- Lead (Pb)
- Mercury (Hg)
- Cadmium (Cd)
- Hexavalent Chromium (Cr6+)
- Polybrominated Biphenyls (PBB)
- Polybrominated Diphenyl Ethers (PBDE)
- Bis(2-Ethylhexyl) phthalate (DEHP)
- Butyl benzyl phthalate (BBP)
- Dibutyl phthalate (DBP)
- Diisobutyl phthalate (DIBP)
The maximum concentration values for these substances are set at 0.1% by weight in homogeneous materials, except for cadmium, which has a limit of 0.01% by weight.
Impact on PCB Manufacturing
The implementation of RoHS 2 has had a significant impact on the PCB manufacturing industry. PCB manufacturers must ensure that their products comply with the directive by:
- Selecting RoHS-compliant materials
- Adapting their manufacturing processes
- Implementing strict quality control measures
- Providing proper documentation and labeling
Failure to comply with RoHS 2 can result in hefty fines and the restriction of market access in the EU.
Strategies for Producing RoHS 2 Compliant PCBs
To ensure compliance with RoHS 2, PCB manufacturers must adopt various strategies throughout the production process. These strategies involve careful material selection, process control, and documentation.
Material Selection
One of the most critical aspects of producing RoHS 2 compliant PCBs is selecting the right materials. PCB manufacturers must work closely with their suppliers to ensure that all materials used in the production process are RoHS-compliant. This includes:
- PCB Laminates
- Solder masks
- Inks and coatings
- Surface finishes
- Adhesives and sealants
Manufacturers should request RoHS compliance certificates from their suppliers and regularly audit their supply chain to ensure ongoing compliance.
Process Control
In addition to material selection, PCB manufacturers must also adapt their production processes to minimize the risk of contamination with restricted substances. This involves:
- Segregating RoHS-compliant and non-compliant materials
- Implementing strict cleaning and maintenance procedures for production equipment
- Training personnel on RoHS compliance requirements
- Regularly testing products for the presence of restricted substances
Manufacturers may also need to invest in new equipment or modify existing equipment to accommodate RoHS-compliant materials and processes.
Documentation and Labeling
Proper documentation and labeling are essential for demonstrating RoHS 2 compliance. PCB manufacturers must maintain detailed records of:
- Material specifications and supplier certifications
- Production processes and quality control measures
- Test results and compliance reports
Products must also be labeled with the CE marking and a RoHS compliance statement. Manufacturers should establish a system for tracking and documenting RoHS compliance throughout the supply chain.
Testing and Certification for RoHS 2 Compliance
To ensure that PCBs meet the requirements of RoHS 2, manufacturers must conduct thorough testing and obtain the necessary certifications.
Testing Methods
There are several testing methods available for determining the presence and concentration of restricted substances in PCBs. The most common methods include:
- X-Ray Fluorescence (XRF) Spectrometry
- Inductively Coupled Plasma (ICP) Spectrometry
- Ion Chromatography (IC)
- Gas Chromatography-Mass Spectrometry (GC-MS)
Method | Advantages | Disadvantages |
---|---|---|
XRF | Non-destructive, fast, and cost-effective | Limited to surface analysis, may require additional confirmation |
ICP | High accuracy and precision, can detect low concentrations | Destructive, requires sample preparation, more expensive |
IC | Can detect ionic species, high sensitivity | Limited to ionic species, requires sample preparation |
GC-MS | Can identify specific compounds, high sensitivity | Destructive, requires sample preparation, more expensive |
Manufacturers should choose the appropriate testing method based on their specific requirements and the nature of their products.
Certification and Compliance Marks
To demonstrate RoHS 2 compliance, PCB manufacturers must obtain the necessary certifications and display the appropriate compliance marks on their products. The most common certification and compliance marks include:
- CE Marking: Indicates that the product complies with all applicable EU directives, including RoHS 2.
- RoHS Compliance Statement: A statement declaring that the product meets the requirements of RoHS 2.
- Third-Party Certifications: Certifications from independent testing laboratories, such as UL or TÜV, can provide additional assurance of RoHS 2 compliance.
Manufacturers should work with accredited testing laboratories and certification bodies to obtain the necessary certifications and compliance marks.
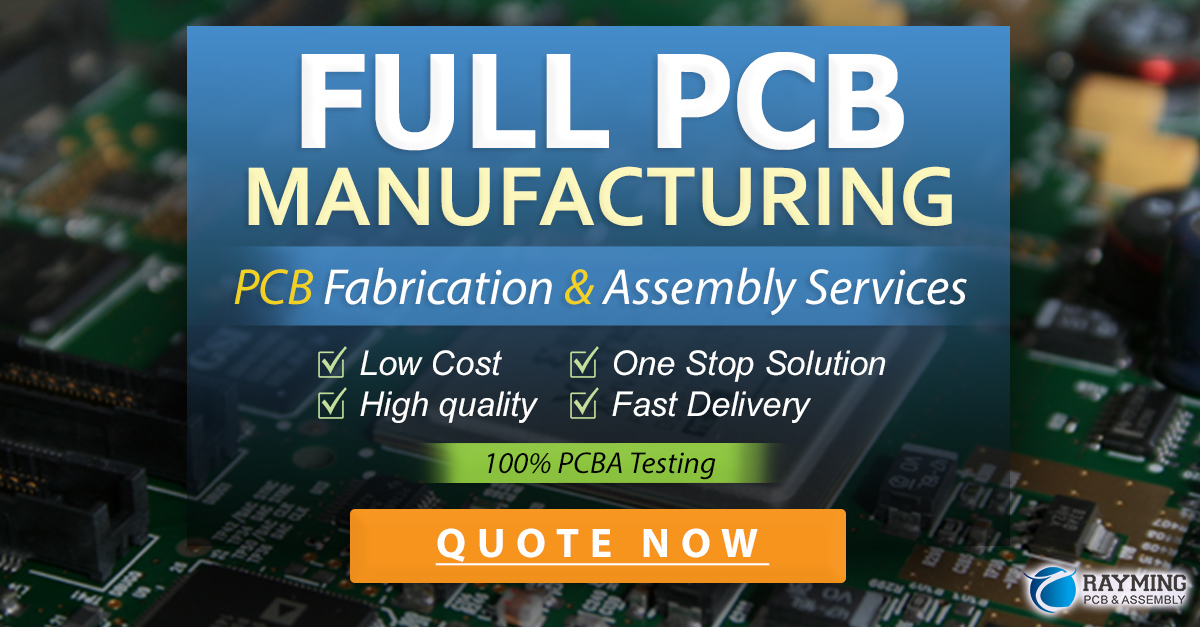
Best Practices for Maintaining RoHS 2 Compliance
Achieving RoHS 2 compliance is an ongoing process that requires continuous monitoring and improvement. PCB manufacturers should adopt the following best practices to maintain compliance:
- Regularly review and update material specifications and supplier certifications
- Conduct periodic audits of the supply chain to ensure ongoing compliance
- Implement a robust quality management system (QMS) that includes RoHS 2 compliance requirements
- Provide regular training and education for personnel on RoHS 2 compliance
- Stay informed about updates and changes to the RoHS directive and related regulations
By adopting these best practices, PCB manufacturers can minimize the risk of non-compliance and ensure the long-term sustainability of their products.
Frequently Asked Questions (FAQ)
- What is the difference between RoHS 1 and RoHS 2?
-
RoHS 2 is an updated version of the original RoHS directive that expands the scope of the regulation and introduces new obligations for EEE manufacturers. RoHS 2 also adds four new restricted substances (DEHP, BBP, DBP, and DIBP) to the list of six substances already restricted under RoHS 1.
-
Do all PCBs need to be RoHS 2 compliant?
-
PCBs intended for use in EEE placed on the EU market must be RoHS 2 compliant. However, some exemptions apply for certain applications, such as medical devices and military equipment. PCB manufacturers should consult the directive and related regulations to determine if their products are subject to RoHS 2 requirements.
-
How can PCB manufacturers ensure that their suppliers provide RoHS-compliant materials?
-
PCB manufacturers should request RoHS compliance certificates from their suppliers and regularly audit their supply chain to ensure ongoing compliance. They should also establish clear material specifications and communicate RoHS requirements to their suppliers.
-
What are the consequences of non-compliance with RoHS 2?
-
Non-compliance with RoHS 2 can result in hefty fines and the restriction of market access in the EU. In some cases, non-compliant products may need to be recalled or disposed of, leading to significant financial losses and damage to the manufacturer’s reputation.
-
How often should PCB manufacturers test their products for RoHS 2 compliance?
- The frequency of testing depends on various factors, such as the risk level of the materials used, the complexity of the supply chain, and the manufacturer’s quality control procedures. In general, manufacturers should conduct testing at least once per year or whenever there are significant changes to materials or suppliers. Regular testing helps ensure ongoing compliance and minimizes the risk of non-compliance.
Conclusion
Producing RoHS 2 compliant PCBs is a complex and ongoing process that requires careful planning, execution, and monitoring. By adopting the strategies and best practices outlined in this article, PCB manufacturers can ensure that their products meet the requirements of the directive and maintain access to the EU market.
Key elements of a successful RoHS 2 compliance program include:
- Careful selection of RoHS-compliant materials
- Adaptation of manufacturing processes to minimize contamination risk
- Implementation of strict quality control measures and testing procedures
- Proper documentation and labeling of products
- Continuous monitoring and improvement of compliance efforts
As the regulatory landscape continues to evolve, PCB manufacturers must stay informed about updates and changes to the RoHS directive and related regulations. By prioritizing RoHS 2 compliance, manufacturers can not only meet their legal obligations but also demonstrate their commitment to environmental sustainability and consumer safety.
Leave a Reply