Introduction to Rigid-Flex PCBs and Flexible PCBs
Printed Circuit Boards (PCBs) have revolutionized the electronics industry by providing a reliable and efficient way to connect electronic components. As technology advances, the demand for more versatile and compact PCBs has led to the development of Rigid-Flex PCBs and Flexible PCBs. While both types of PCBs offer unique advantages, understanding the differences between them is crucial for choosing the right one for your specific application.
What is a Rigid-Flex PCB?
A Rigid-Flex PCB is a hybrid circuit board that combines the benefits of both rigid and flexible PCBs. It consists of multiple layers of flexible circuit substrates laminated together with rigid circuit boards. The flexible portions allow for bending and folding, while the rigid parts provide structural support and stability.
What is a Flexible PCB?
A Flexible PCB, also known as a flex circuit, is a type of PCB that is made from flexible materials such as polyimide or polyester. These materials allow the PCB to bend, twist, and conform to various shapes without damaging the circuit or components.
Advantages of Rigid-Flex PCBs
1. Space Savings and Miniaturization
One of the primary advantages of Rigid-Flex PCBs is their ability to save space and enable miniaturization. By combining rigid and flexible sections, designers can create compact and highly integrated electronic devices. This is particularly beneficial for applications where space is limited, such as wearable devices, medical implants, and aerospace systems.
2. Improved Reliability and Durability
Rigid-Flex PCBs offer enhanced reliability and durability compared to traditional PCBs. The flexible portions of the board can withstand repeated bending and flexing without compromising the integrity of the circuit. Additionally, the rigid sections provide structural support, reducing the risk of damage due to vibration or shock.
3. Reduced Assembly Time and Costs
Using Rigid-Flex PCBs can significantly reduce assembly time and costs. By eliminating the need for separate connectors and wires between rigid and flexible sections, the overall component count is reduced. This simplifies the assembly process, minimizes the risk of connection failures, and lowers manufacturing costs.
4. Enhanced Signal Integrity
Rigid-Flex PCBs offer improved signal integrity compared to traditional PCBs with separate connectors. The continuous copper traces between the rigid and flexible sections eliminate the need for connectors, reducing signal loss and reflections. This is particularly important for high-speed and high-frequency applications where signal integrity is critical.
Advantages of Flexible PCBs
1. Conformability and Flexibility
Flexible PCBs excel in applications that require conformability and flexibility. They can be bent, twisted, and shaped to fit into tight spaces or conform to irregular surfaces. This makes them ideal for applications such as wearable devices, medical equipment, and automotive electronics.
2. Lightweight and Thin Profile
Flexible PCBs are typically thinner and lighter than their rigid counterparts. This is due to the use of thin, flexible substrate materials such as polyimide. The lightweight and thin profile of flexible PCBs make them well-suited for applications where weight and size are critical factors, such as aerospace and portable devices.
3. Increased Vibration and Shock Resistance
Flexible PCBs offer excellent resistance to vibration and shock. The flexible nature of the board allows it to absorb and dissipate mechanical stresses, reducing the risk of damage to components and connections. This is particularly beneficial in applications that are subject to high levels of vibration or impact, such as automotive and aerospace systems.
4. Improved Thermal Management
Flexible PCBs can contribute to better thermal management in electronic devices. The thin and flexible nature of the board allows for better heat dissipation, as the heat can be spread more evenly across the surface. This can help prevent hotspots and reduce the risk of thermal-related failures.
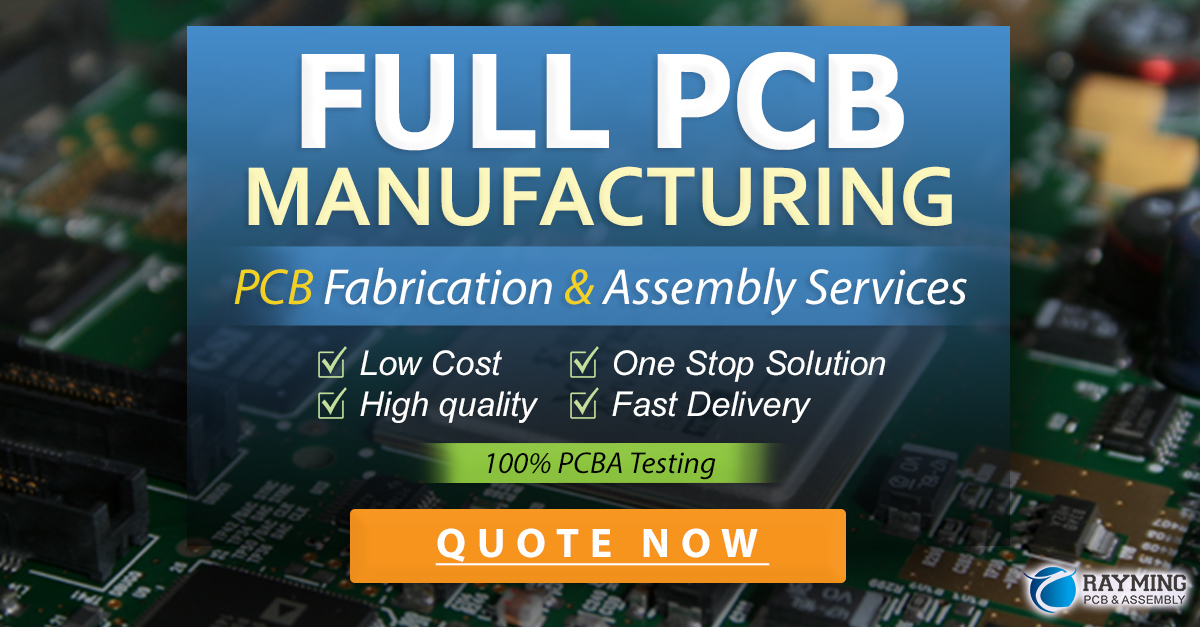
Comparison Table: Rigid-Flex PCBs vs. Flexible PCBs
Feature | Rigid-Flex PCBs | Flexible PCBs |
---|---|---|
Rigidity | High | Low |
Flexibility | Moderate | High |
Space Savings | High | Moderate |
Reliability | High | Moderate |
Assembly Complexity | Low | Moderate |
Signal Integrity | High | Moderate |
Conformability | Moderate | High |
Weight | Moderate | Low |
Vibration Resistance | High | High |
Thermal Management | Moderate | High |
Cost | High | Moderate |
Applications of Rigid-Flex PCBs
Rigid-Flex PCBs find applications in various industries where space savings, reliability, and high-performance are critical. Some common applications include:
- Aerospace and Defense
- Medical Devices and Implants
- Wearable Technology
- Industrial Automation and Robotics
- Automotive Electronics
Applications of Flexible PCBs
Flexible PCBs are widely used in applications that require conformability, lightweight design, and resistance to vibration and shock. Some common applications include:
- Consumer Electronics
- Wearable Devices
- Medical Equipment
- Automotive Electronics
- Aerospace and Defense
Design Considerations for Rigid-Flex PCBs and Flexible PCBs
When designing Rigid-Flex PCBs or Flexible PCBs, several factors need to be considered to ensure optimal performance and reliability. These include:
- Material Selection: Choosing the right substrate materials based on the application requirements, such as flexibility, temperature resistance, and dielectric properties.
- Bend Radius: Determining the appropriate bend radius to prevent excessive stress on the flexible portions of the board.
- Copper Thickness: Selecting the appropriate copper thickness to balance flexibility and current-carrying capacity.
- Coverlay and Stiffeners: Incorporating coverlay and stiffeners to protect the flexible portions and provide additional support.
- Manufacturing Process: Understanding the specific manufacturing processes and design rules for Rigid-Flex PCBs and Flexible PCBs.
Frequently Asked Questions (FAQ)
1. Can Rigid-Flex PCBs be used in high-temperature applications?
Yes, Rigid-Flex PCBs can be designed to withstand high temperatures by selecting appropriate materials and following specific design guidelines. High-temperature materials such as polyimide can be used for the flexible portions, while the rigid sections can be made from temperature-resistant substrates like FR-4 or ceramic.
2. How does the cost of Rigid-Flex PCBs compare to traditional PCBs?
Rigid-Flex PCBs are generally more expensive than traditional rigid PCBs due to the complex manufacturing process and the use of specialized materials. However, the overall cost savings achieved through reduced assembly time, fewer connectors, and improved reliability can offset the initial higher cost in many applications.
3. What is the typical lifespan of a Flexible PCB?
The lifespan of a Flexible PCB depends on various factors, including the materials used, the application environment, and the level of stress and flexing the board undergoes. With proper design and material selection, Flexible PCBs can have a lifespan of several years or even decades in some cases.
4. Can Flexible PCBs be used in high-speed applications?
Yes, Flexible PCBs can be used in high-speed applications, but careful design considerations are necessary. Factors such as impedance control, signal integrity, and EMI shielding need to be addressed to ensure optimal performance. Using high-speed materials and following best design practices can help mitigate signal integrity issues in Flexible PCBs.
5. Are there any limitations to the number of layers in Rigid-Flex PCBs?
The number of layers in a Rigid-Flex PCB is limited by the manufacturing capabilities and the specific design requirements. Typically, Rigid-Flex PCBs can have up to 30 layers or more, depending on the complexity of the design and the manufacturing process used. However, as the number of layers increases, the manufacturing complexity and cost also increase.
Conclusion
Rigid-Flex PCBs and Flexible PCBs offer unique advantages and are suitable for different applications. Rigid-Flex PCBs excel in space savings, reliability, and high-performance, making them ideal for applications such as aerospace, medical devices, and wearable technology. On the other hand, Flexible PCBs offer exceptional conformability, lightweight design, and resistance to vibration and shock, making them well-suited for consumer electronics, medical equipment, and automotive electronics.
When choosing between Rigid-Flex PCBs and Flexible PCBs, it is essential to consider the specific requirements of your application, such as space constraints, flexibility needs, environmental factors, and performance criteria. By understanding the advantages and limitations of each type of PCB and following best design practices, you can select the most suitable option for your project and ensure optimal performance and reliability.
As technology continues to advance, the demand for Rigid-Flex PCBs and Flexible PCBs is expected to grow, driven by the increasing need for miniaturization, flexibility, and high-performance in various industries. By staying informed about the latest developments and design techniques, engineers and designers can leverage the benefits of these advanced PCB technologies to create innovative and reliable electronic devices.
Leave a Reply