Introduction to Rigid-flex PCBs
Rigid-flex PCBs are a unique type of printed circuit board that combines the benefits of both rigid and flexible substrates. This innovative design allows for enhanced reliability, improved electrical performance, and greater design flexibility compared to traditional rigid PCBs. Rigid-flex PCBs consist of rigid PCB sections connected by flexible PCB sections, enabling the board to be bent, folded, or twisted to fit into complex or compact spaces.
The demand for rigid-flex PCBs has been steadily increasing in recent years, driven by the growing need for miniaturization, high-density interconnects, and advanced packaging solutions in various industries, such as aerospace, automotive, medical, and consumer electronics. As a result, choosing the right rigid-flex PCB manufacturer is crucial to ensure the success of your project.
Advantages of Rigid-flex PCBs
- Space Savings: Rigid-flex PCBs allow for more compact designs by eliminating the need for connectors and cables between rigid sections.
- Increased Reliability: The elimination of connectors reduces the number of potential failure points, resulting in improved overall reliability.
- Enhanced Signal Integrity: Rigid-flex PCBs minimize signal loss and interference by reducing the distance signals must travel between components.
- Improved Durability: The flexible sections of rigid-flex PCBs can withstand repeated bending and flexing without compromising the board’s integrity.
- Design Flexibility: Rigid-flex PCBs enable designers to create complex, three-dimensional structures that would be impossible with traditional rigid PCBs.
Factors to Consider When Choosing a Rigid-flex PCB Manufacturer
1. Technical Capabilities
When selecting a rigid-flex PCB manufacturer, it is essential to assess their technical capabilities to ensure they can meet your project’s specific requirements. Some key factors to consider include:
- Layer Count: Ensure the manufacturer can produce boards with the required number of layers, both rigid and flexible.
- Material Selection: Check if the manufacturer has experience working with the specific materials needed for your application, such as high-frequency or high-temperature laminates.
- Feature Size: Verify that the manufacturer can achieve the desired feature sizes, such as minimum trace width and spacing, via diameter, and hole size.
- Controlled Impedance: If your design requires controlled impedance, make sure the manufacturer has the necessary expertise and equipment to meet your specifications.
2. Quality Control and Certifications
Quality control is critical in rigid-flex PCB manufacturing to ensure the boards meet the required performance and reliability standards. When evaluating potential manufacturers, consider the following:
- Quality Management System: Look for manufacturers with well-established quality management systems, such as ISO 9001, to ensure consistent and reliable production processes.
- Industry-Specific Certifications: Depending on your industry, you may require manufacturers to hold specific certifications, such as AS9100 for aerospace or ISO 13485 for medical devices.
- Testing and Inspection: Inquire about the manufacturer’s testing and inspection procedures, including in-process checks, electrical testing, and final visual inspection, to ensure the quality of the finished product.
3. Manufacturing Capabilities and Capacity
Assess the manufacturer’s production capabilities and capacity to determine if they can meet your project’s timeline and volume requirements:
- Production Volume: Ensure the manufacturer can accommodate your expected production volumes, whether you need prototypes, low-volume runs, or high-volume production.
- Lead Time: Discuss the manufacturer’s typical lead times for rigid-flex PCBs and whether they can meet your project’s timeline.
- Rapid Prototyping: If your project requires quick turnaround times for prototypes, look for manufacturers with in-house rapid prototyping capabilities.
4. Customer Support and Communication
Effective communication and responsive customer support are essential for a successful partnership with your rigid-flex PCB manufacturer:
- Technical Support: Look for manufacturers with knowledgeable technical support teams that can provide guidance and assistance throughout the design and manufacturing process.
- Project Management: Ensure the manufacturer assigns a dedicated project manager to oversee your project and serve as a single point of contact.
- Language and Cultural Barriers: If you are working with an offshore manufacturer, consider potential language and cultural barriers that may impact communication and project success.
5. Cost and Shipping
While cost is an important factor in selecting a rigid-flex PCB manufacturer, it should not be the sole deciding factor. Consider the following when evaluating costs:
- Price vs. Value: Balance the price of the PCBs with the overall value provided by the manufacturer, including quality, reliability, and support.
- Shipping Costs: Factor in shipping costs, especially if working with an offshore manufacturer, as they can significantly impact the total cost of your project.
- Tariffs and Duties: Be aware of any potential tariffs or duties that may apply when importing PCBs from foreign manufacturers.
Top Rigid-flex PCB Manufacturers
To help you start your search for the right rigid-flex PCB manufacturer, here are some top companies known for their expertise in this field:
Manufacturer | Location | Specialties | Certifications |
---|---|---|---|
Cirexx International | USA | Aerospace, Defense, Medical | AS9100, ISO 9001, ISO 13485 |
TTM Technologies | USA, China | Automotive, Medical, Industrial | AS9100, ISO 9001, ISO 13485 |
Eltek Ltd. | Israel | Defense, Medical, Telecom | AS9100, ISO 9001, ISO 13485 |
Printed Circuits, Inc. | USA | Military, Aerospace, Medical | AS9100, ISO 9001, ITAR |
Tech Etch | USA | Medical, Aerospace, Industrial | AS9100, ISO 9001, ISO 13485 |
Please note that this list is not exhaustive, and there are many other reputable rigid-flex PCB manufacturers worldwide. It is essential to conduct thorough research and due diligence when selecting a manufacturer for your specific project needs.
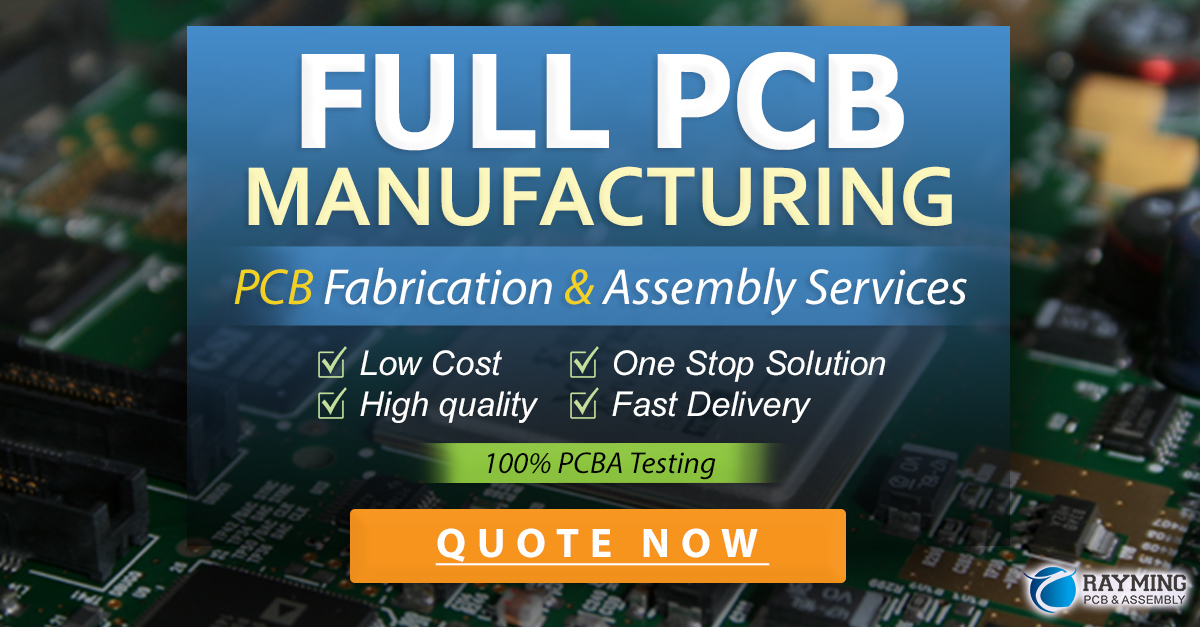
Rigid-flex PCB Design Considerations
To ensure the success of your rigid-flex PCB project, it is crucial to keep the following design considerations in mind:
- Bend Radius: Ensure that the bend radius of the flexible sections is within the manufacturer’s recommended guidelines to avoid stress and potential failure.
- Stiffener Placement: Strategically place stiffeners to support the rigid sections and prevent excessive flexing in the flexible sections.
- Coverlay Selection: Choose the appropriate coverlay material based on the application’s requirements, such as flexibility, durability, and environmental resistance.
- Copper Thickness: Consider the copper thickness in the flexible sections, as thinner copper can improve flexibility but may impact current-carrying capacity.
- Via Placement: Avoid placing vias in the flexible sections whenever possible, as they can reduce flexibility and increase the risk of failure.
By addressing these design considerations early in the development process, you can minimize potential issues and ensure a more seamless transition to manufacturing.
Frequently Asked Questions (FAQ)
- What is the typical lead time for rigid-flex PCBs?
-
Lead times for rigid-flex PCBs can vary depending on the manufacturer and the complexity of the design. Typically, lead times range from 2-8 weeks, with more complex designs and higher volumes requiring longer lead times.
-
Are rigid-flex PCBs more expensive than traditional rigid PCBs?
-
Yes, rigid-flex PCBs are generally more expensive than traditional rigid PCBs due to the additional materials, specialized manufacturing processes, and increased complexity involved in their production.
-
Can rigid-flex PCBs be used in high-temperature applications?
-
Yes, rigid-flex PCBs can be designed for high-temperature applications by selecting appropriate materials, such as polyimide or PTFE laminates, that can withstand elevated temperatures.
-
What is the minimum bend radius for a rigid-flex PCB?
-
The minimum bend radius depends on various factors, such as the thickness of the flexible substrate, copper thickness, and the number of layers. Manufacturers typically provide guidelines for minimum bend radii based on these factors.
-
How do I choose the right rigid-flex PCB manufacturer for my project?
- When selecting a rigid-flex PCB manufacturer, consider factors such as technical capabilities, quality control, certifications, manufacturing capacity, customer support, and cost. Researching and comparing multiple manufacturers based on these criteria can help you find the best fit for your project.
Conclusion
Choosing the right rigid-flex PCB manufacturer is essential for the success of your project. By considering factors such as technical capabilities, quality control, manufacturing capacity, customer support, and cost, you can select a manufacturer that meets your specific needs and ensures the production of high-quality, reliable rigid-flex PCBs.
When designing rigid-flex PCBs, it is crucial to keep in mind considerations such as bend radius, stiffener placement, coverlay selection, copper thickness, and via placement. By addressing these factors early in the design process, you can minimize potential issues and ensure a smoother transition to manufacturing.
As the demand for rigid-flex PCBs continues to grow across various industries, partnering with an experienced and reputable manufacturer can provide you with the expertise and support needed to bring your innovative designs to life.
Leave a Reply