Introduction to PCB Topologies
Printed Circuit Board (PCB) design is a critical aspect of electronic product development. The layout and arrangement of components, traces, and planes on a PCB can significantly impact the performance, reliability, and electromagnetic compatibility (EMC) of the final product. One of the key considerations in PCB design is the management of return currents, which play a vital role in maintaining signal integrity and minimizing electromagnetic interference (EMI).
Return current topologies refer to the various ways in which return currents flow through a PCB. Understanding and optimizing these topologies is essential for achieving optimal performance and meeting EMC requirements. In this article, we will explore the different return current topologies commonly used in PCB design, their advantages and disadvantages, and best practices for implementing them effectively.
The Importance of Return Current Management
Before delving into specific return current topologies, it’s crucial to understand why managing return currents is so important in PCB design. Return currents are the counterpart to the signal currents flowing through a circuit. According to Kirchhoff’s Current Law, the sum of currents entering a node must equal the sum of currents leaving that node. This means that for every signal current flowing through a trace, there must be an equal and opposite return current flowing back to the source.
Proper management of return currents is essential for several reasons:
-
Signal Integrity: Return currents play a critical role in maintaining the integrity of signals transmitted through a PCB. If return currents are not properly managed, they can cause signal distortion, crosstalk, and other issues that degrade the quality of the signal.
-
Electromagnetic Compatibility (EMC): Poorly managed return currents can lead to increased electromagnetic emissions, which can interfere with other electronic devices and cause EMC compliance issues. By controlling the flow of return currents, designers can minimize EMI and ensure that the PCB meets relevant EMC standards.
-
Power Integrity: Return currents also impact the power delivery network (PDN) of a PCB. Inadequate return current paths can lead to voltage drops, ground bounces, and other power integrity issues that can affect the performance and reliability of the circuit.
Common Return Current Topologies
There are several return current topologies commonly used in PCB design, each with its own advantages and disadvantages. Let’s explore some of the most prevalent topologies:
1. Ground Plane
A ground plane is a large, continuous copper area on a PCB layer that serves as a low-impedance return path for currents. Ground planes are widely used in multi-layer PCBs due to their numerous benefits:
- Low impedance: Ground planes provide a low-impedance return path for currents, minimizing voltage drops and ensuring stable reference voltages.
- Reduced EMI: The continuous nature of a ground plane helps to contain electromagnetic fields and minimize EMI.
- Improved signal integrity: Ground planes provide a consistent reference for signals, reducing crosstalk and improving signal quality.
However, ground planes also have some drawbacks:
- Increased capacitance: The large surface area of a ground plane can increase the capacitance between signal traces and the plane, which can impact high-speed signals.
- Manufacturing complexity: Incorporating ground planes in a PCB design can increase the complexity and cost of manufacturing, especially for high-density designs.
Best practices for implementing ground planes include:
- Placing ground planes as close to the signal layers as possible to minimize loop areas and reduce inductance.
- Providing adequate clearance between signal traces and ground planes to control impedance and minimize capacitance.
- Using stitching vias to connect ground planes on different layers, ensuring a low-impedance return path.
2. Power Plane
Similar to a ground plane, a power plane is a continuous copper area on a PCB layer that provides a low-impedance distribution of power to components. Power planes offer several advantages:
- Low impedance: Power planes provide a low-impedance power distribution network, minimizing voltage drops and ensuring stable supply voltages.
- Reduced EMI: The continuous nature of a power plane helps to contain electromagnetic fields and minimize EMI.
- Improved power integrity: Power planes provide a consistent power supply to components, reducing power supply noise and improving overall power integrity.
However, power planes also have some limitations:
- Increased capacitance: Like ground planes, power planes can increase the capacitance between signal traces and the plane, which can impact high-speed signals.
- Manufacturing complexity: Incorporating power planes in a PCB design can increase the complexity and cost of manufacturing, especially for high-density designs.
Best practices for implementing power planes include:
- Placing power planes as close to the components as possible to minimize voltage drops and ensure stable power delivery.
- Providing adequate clearance between signal traces and power planes to control impedance and minimize capacitance.
- Using decoupling capacitors near power pins of components to provide local energy storage and reduce power supply noise.
3. Split Planes
Split planes are a variation of ground or power planes where the continuous copper area is divided into separate sections, each serving a specific purpose. Split planes are commonly used in mixed-signal designs to isolate sensitive analog circuits from noisy digital circuits. Advantages of split planes include:
- Noise isolation: Split planes allow for the separation of noisy and sensitive circuits, reducing crosstalk and improving signal integrity.
- Flexibility: Split planes can be customized to meet the specific requirements of a design, such as separating different power domains or creating isolated ground regions.
However, split planes also have some drawbacks:
- Increased complexity: Designing and implementing split planes requires careful planning and attention to detail to ensure proper isolation and return current management.
- Potential EMI issues: If not properly designed, split planes can create discontinuities in the return current path, leading to increased EMI.
Best practices for implementing split planes include:
- Carefully planning the placement of components and the division of planes to ensure proper isolation and return current management.
- Using stitching capacitors or ferrite beads to provide a low-impedance connection between split plane sections at high frequencies.
- Minimizing the number of splits and ensuring that each split has a well-defined purpose.
4. Gridded Ground
A gridded ground topology consists of a network of interconnected ground traces or small ground areas, rather than a continuous ground plane. This topology is often used in high-speed designs or when a continuous ground plane is not feasible due to manufacturing constraints. Advantages of gridded ground include:
- Reduced capacitance: The smaller surface area of a gridded ground can reduce the capacitance between signal traces and the ground, which can be beneficial for high-speed signals.
- Flexibility: Gridded ground can be more easily incorporated into high-density designs where a continuous ground plane may not be practical.
However, gridded ground also has some limitations:
- Higher impedance: The interconnected nature of a gridded ground can result in higher impedance compared to a continuous ground plane, which can impact signal integrity and EMI.
- Complexity: Designing an effective gridded ground topology requires careful consideration of trace widths, spacing, and connectivity to ensure adequate return current paths.
Best practices for implementing gridded ground include:
- Using wide, low-impedance traces for the gridded ground network to minimize impedance and ensure adequate current carrying capacity.
- Providing sufficient connectivity between the gridded ground and components, using vias or traces as needed.
- Minimizing the spacing between gridded ground traces to reduce loop areas and improve return current management.
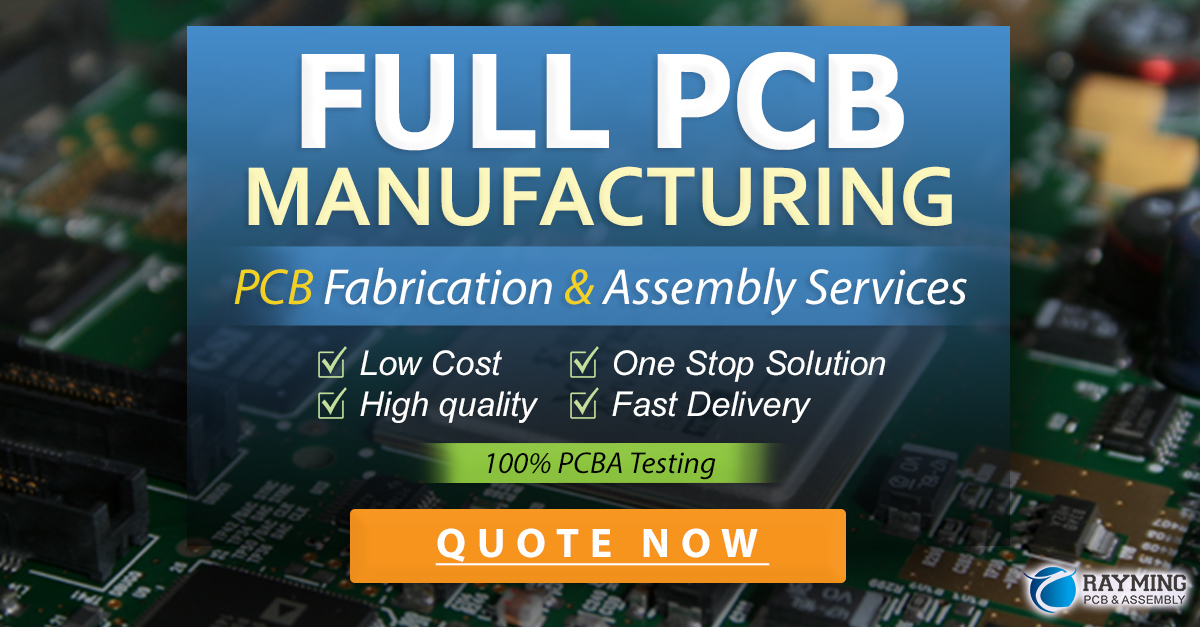
Selecting the Appropriate Return Current Topology
Choosing the appropriate return current topology for a PCB design depends on various factors, including:
- Signal speed and frequency: High-speed signals typically require low-impedance return paths, such as ground planes, to maintain signal integrity.
- Circuit complexity: Complex designs with multiple power domains or mixed-signal requirements may benefit from split planes or gridded ground topologies.
- Manufacturing constraints: The choice of return current topology may be influenced by manufacturing limitations, such as the number of layers or the minimum trace width and spacing.
- EMC requirements: The selected topology should help meet the relevant EMC standards and minimize electromagnetic emissions.
When selecting a return current topology, designers should consider the trade-offs between performance, complexity, and manufacturability. In some cases, a combination of topologies may be used to achieve the desired results.
Best Practices for Return Current Management
Regardless of the specific return current topology used, there are several best practices that designers should follow to ensure optimal performance and EMC compliance:
-
Minimize loop areas: Keep signal traces and their corresponding return paths as close together as possible to minimize loop areas and reduce inductance.
-
Provide adequate return paths: Ensure that there are sufficient return paths for all signal currents, using ground planes, power planes, or gridded ground as appropriate.
-
Use stitching vias: When using multi-layer PCBs, use stitching vias to connect ground or power planes on different layers, providing a low-impedance return path.
-
Control impedance: Maintain consistent impedance for signal traces by controlling the width, spacing, and distance to reference planes.
-
Use decoupling capacitors: Place decoupling capacitors close to the power pins of components to provide local energy storage and reduce power supply noise.
-
Minimize discontinuities: Avoid abrupt changes in the return current path, such as slots or splits in planes, which can cause EMI and signal integrity issues.
-
Simulate and test: Use simulation tools to analyze the return current paths and identify potential issues early in the design process. Perform thorough testing to validate the performance and EMC compliance of the final design.
By following these best practices and selecting the appropriate return current topology, designers can create PCBs that deliver optimal performance, maintain signal integrity, and meet EMC requirements.
Frequently Asked Questions (FAQ)
-
What is the main purpose of managing return currents in PCB design?
Managing return currents is essential for maintaining signal integrity, minimizing electromagnetic interference (EMI), and ensuring power integrity in a PCB design. -
What are the most common return current topologies used in PCB design?
The most common return current topologies include ground planes, power planes, split planes, and gridded ground. -
What are the advantages of using a ground plane in a PCB design?
Ground planes provide a low-impedance return path for currents, reduce EMI, and improve signal integrity by providing a consistent reference for signals. -
When might a designer choose to use a split plane topology?
Split planes are often used in mixed-signal designs to isolate sensitive analog circuits from noisy digital circuits, reducing crosstalk and improving signal integrity. -
What are some best practices for managing return currents in PCB design?
Best practices include minimizing loop areas, providing adequate return paths, using stitching vias, controlling impedance, using decoupling capacitors, minimizing discontinuities, and performing simulations and thorough testing.
Conclusion
Return current management is a critical aspect of PCB design that directly impacts signal integrity, electromagnetic compatibility, and power integrity. By understanding the various return current topologies and their advantages and limitations, designers can make informed decisions when selecting the appropriate topology for their specific design requirements.
Ground planes, power planes, split planes, and gridded ground are among the most common return current topologies used in PCB design. Each topology has its own set of benefits and drawbacks, and the choice ultimately depends on factors such as signal speed, circuit complexity, manufacturing constraints, and EMC requirements.
To ensure optimal performance and EMC compliance, designers should follow best practices for return current management, such as minimizing loop areas, providing adequate return paths, controlling impedance, and using decoupling capacitors. Simulations and thorough testing are also essential for validating the design and identifying potential issues early in the development process.
By carefully considering return current topologies and adhering to best practices, PCB designers can create robust, high-performance electronic products that meet the ever-increasing demands of modern applications.
Leave a Reply