Introduction to PCB Registration
Printed Circuit Board (PCB) registration is a crucial process in the manufacturing of electronic devices. It ensures that the various layers of a PCB align precisely with each other, resulting in proper electrical connections and optimal performance. PCB registration also plays a vital role in the application of solder paste using stencils. This article will delve into the details of registration systems for PCBs and stencils, covering the importance of accurate registration, different registration methods, and best practices for achieving high-quality results.
The Importance of Accurate PCB Registration
Accurate PCB registration is essential for several reasons:
-
Electrical Integrity: Proper alignment of PCB layers ensures that electrical connections are made correctly, minimizing the risk of short circuits, open circuits, or other defects that can compromise the functionality of the electronic device.
-
Component Placement: Precise registration allows for the accurate placement of components on the PCB surface. Misaligned layers can lead to component shifting, resulting in poor soldering and potential device failure.
-
Solder Paste Application: When using stencils to apply solder paste, accurate registration between the PCB and the stencil is critical. Misregistration can cause insufficient or excessive solder paste deposition, leading to soldering defects such as bridging, tombstoning, or poor joint formation.
-
Manufacturing Efficiency: Accurate registration reduces the need for rework and repairs, improving overall manufacturing efficiency and reducing costs associated with scrap and wasted materials.
PCB Registration Methods
There are several methods used to achieve accurate PCB registration during the manufacturing process:
1. Fiducial Markers
Fiducial markers are small, precise features added to the PCB design to serve as reference points for registration. These markers are typically copper pads or solder mask openings placed in specific locations on the PCB, such as the corners or along the edges. During the assembly process, machine vision systems detect these markers and use them to align the PCB layers and position components accurately.
Advantages of using fiducial markers include:
– High accuracy and repeatability
– Compatibility with automated assembly processes
– Relatively simple implementation
Disadvantages:
– Requires additional space on the PCB for marker placement
– May not be suitable for very small or densely populated PCBs
2. Edge Registration
Edge registration relies on the precise machining of the PCB edges to align the layers and components. This method involves creating a set of alignment holes or slots along the edges of the PCB, which are used as reference points for registration. Edge registration can be achieved using pins, rails, or other mechanical alignment features.
Advantages of edge registration:
– Does not require additional space on the PCB surface
– Suitable for small or densely populated PCBs
– Can be used in conjunction with fiducial markers for enhanced accuracy
Disadvantages:
– Requires precise machining of PCB edges, which can increase manufacturing costs
– May be more susceptible to wear and tear over time
3. Optical Registration
Optical registration uses camera-based systems to align PCB layers and components visually. This method relies on the recognition of specific patterns, such as artwork or unique features on the PCB surface. Optical registration systems employ advanced image processing algorithms to determine the correct alignment and make necessary adjustments.
Advantages of optical registration:
– Non-contact method, reducing the risk of damage to the PCB
– Highly flexible and adaptable to different PCB designs
– Can be used for both layer alignment and component placement
Disadvantages:
– Requires clean and clear PCB surfaces for accurate pattern recognition
– May be sensitive to variations in lighting conditions or surface finishes
– Higher initial investment in camera-based systems and software
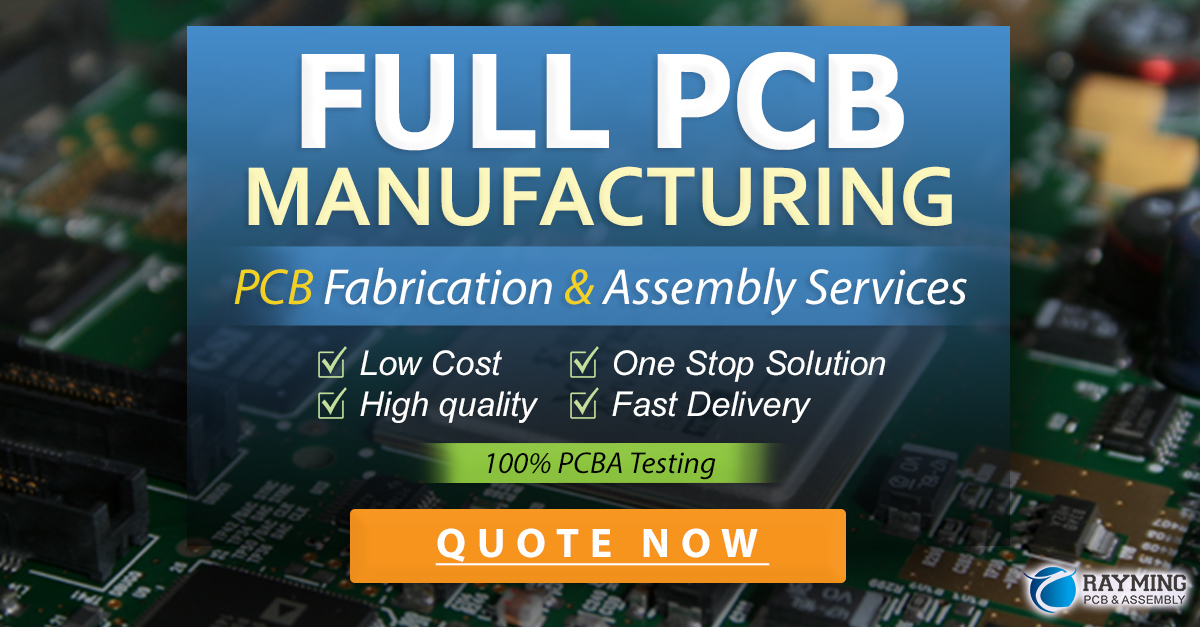
Stencil Registration
Stencil registration is the process of aligning a solder paste stencil with the PCB to ensure accurate solder paste deposition. Proper stencil registration is crucial for achieving high-quality solder joints and preventing defects such as bridging, insufficient solder, or poor wetting.
There are two main methods for stencil registration:
-
Frame Mounting: In this method, the stencil is mounted onto a rigid frame that aligns with the PCB using pins, rails, or other mechanical features. Frame mounting provides a stable and repeatable registration, but it may require additional setup time and can be less flexible when accommodating different PCB designs.
-
Vision Alignment: Vision alignment systems use cameras to align the stencil with the PCB optically. These systems identify specific patterns or features on the PCB and stencil, then make precise adjustments to ensure proper registration. Vision alignment offers greater flexibility and can accommodate a wider range of PCB designs, but it may require a higher initial investment in equipment and software.
Factors that influence stencil registration accuracy include:
– Stencil material and thickness
– PCB and stencil cleanliness
– Solder paste properties (viscosity, particle size, etc.)
– Printing parameters (pressure, speed, separation distance)
Parameter | Typical Range |
---|---|
Stencil Thickness | 0.1 – 0.2 mm |
Solder Paste Viscosity | 150 – 300 kcps |
Printing Pressure | 5 – 10 kg |
Printing Speed | 20 – 50 mm/s |
Separation Distance | 0.5 – 2.0 mm |
Table 1: Typical Stencil Printing Parameters
Best Practices for PCB and Stencil Registration
To achieve optimal registration results, consider the following best practices:
-
Design for Manufacturing (DFM): Incorporate registration-friendly features into the PCB design, such as fiducial markers or edge alignment features. Collaborate with your manufacturing partners to ensure that the design is compatible with their registration systems and processes.
-
Material Selection: Choose high-quality PCB substrates and stencil materials that provide dimensional stability and resist warping or deformation. Consider factors such as thermal expansion coefficients and moisture absorption when selecting materials.
-
Process Control: Implement strict process controls to maintain consistent registration accuracy. This includes regular calibration of registration systems, monitoring of environmental conditions (temperature, humidity), and adherence to standard operating procedures.
-
Cleanliness: Maintain a clean manufacturing environment to prevent contamination of PCBs and stencils. Use appropriate cleaning methods and materials to remove dirt, dust, or residues that can interfere with registration accuracy.
-
Inspection and Feedback: Regularly inspect PCBs and stencils for registration accuracy using visual inspection, automated optical inspection (AOI), or solder paste inspection (SPI) systems. Use the feedback from these inspections to identify and correct any registration issues promptly.
Frequently Asked Questions (FAQ)
-
What is the typical accuracy of PCB registration systems?
Modern PCB registration systems can achieve accuracies of ±25 microns or better, depending on the specific method and equipment used. Fiducial markers and vision alignment systems generally offer the highest accuracy, while edge registration may have slightly lower accuracy due to potential wear and tear of mechanical features. -
Can I use multiple registration methods on the same PCB?
Yes, it is possible to use a combination of registration methods on a single PCB. For example, you can use fiducial markers for overall layer alignment and edge registration for component placement. The choice of registration methods depends on the specific PCB design, manufacturing requirements, and available equipment. -
How often should I calibrate my registration systems?
The frequency of calibration depends on factors such as the type of registration system, the volume of production, and the required accuracy. As a general guideline, it is recommended to calibrate registration systems at least once per shift or every 8 hours of continuous operation. However, more frequent calibration may be necessary for high-precision applications or if there are significant changes in environmental conditions. -
What are the most common causes of registration errors?
Common causes of registration errors include: - Poor PCB or stencil quality (warping, dimensional instability)
- Contamination or debris on the PCB or stencil surface
- Incorrect setup or calibration of registration systems
- Wear and tear of mechanical registration features
-
Environmental factors (temperature, humidity) affecting material dimensions
-
How can I troubleshoot registration issues in my manufacturing process?
If you encounter registration issues, follow these troubleshooting steps: - Verify that the PCB and stencil designs are compatible with your registration systems and meet the necessary DFM guidelines.
- Check for any visible contamination, damage, or defects on the PCB or stencil surfaces. Clean or replace components as needed.
- Review the setup and calibration of your registration systems, ensuring that all parameters are within the specified ranges.
- Inspect the mechanical registration features (pins, rails, etc.) for wear or damage, and replace them if necessary.
- Monitor environmental conditions and make adjustments to maintain a stable manufacturing environment.
- Conduct a thorough analysis of the registration errors, using inspection data and statistical process control (SPC) tools to identify patterns or trends.
- Collaborate with your equipment suppliers, material providers, and PCB design team to develop and implement corrective actions.
Conclusion
PCB and stencil registration is a critical aspect of electronic device manufacturing, ensuring the proper alignment of layers, components, and solder paste deposition. Accurate registration is essential for maintaining electrical integrity, component placement accuracy, and manufacturing efficiency. By understanding the various registration methods, best practices, and troubleshooting techniques, manufacturers can optimize their processes and produce high-quality PCBs consistently.
As technology advances and device complexity increases, the importance of precise registration will only continue to grow. Investing in robust registration systems, maintaining strict process controls, and staying up-to-date with industry best practices will be key to success in the competitive world of PCB manufacturing.
Leave a Reply