Flexible printed circuit boards (flex PCBs) provide numerous advantages over traditional rigid PCBs, including improved reliability, dynamic flexing, and compact form factors. However, sourcing flex PCB prototypes and small batches can be challenging due to long lead times and high costs from fabricators. This guide covers strategies for obtaining quick turnaround on flex PCB orders ideal for prototyping and low volume production.
What are Flex PCBs?
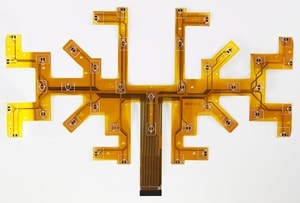
A flex PCB is a printed circuit board constructed using a flexible base material such as polyimide or polyester film. The circuits are photolithographically etched or printed onto the flexible substrate and components are soldered onto designated pads.
Compared to rigid PCBs, flex PCBs provide:
- Dynamic flexing and shape conforming abilities
- Improved shock/vibration resistance
- Compact, space saving form factors
- Enhanced reliability in stressful environments
- Design freedom for curving and folding
Common applications of flex PCBs include consumer electronics, automotive, aerospace, medical devices, wearables, IoT devices, and more. As circuits become more compact and devices more ergonomic, flex PCB usage continues to grow.
Benefits of Fast Turnaround Prototyping
For designers and engineers, having access to rapid flex PCB prototyping capabilities provides many advantages:
- Faster design iteration: Multiple design versions can be tested in parallel
- Accelerate development: Gets working models into designers hands faster
- Verify manufacturing: Confirm designs are manufacturable early
- Identify issues: Allows problems to be fixed sooner
- Stay on schedule: Avoids delays from long lead time boards
- Market faster: Enables bringing products to market quicker
For low volume end products, fast turnaround small batches are ideal for:
- Prototype devices: Units for demos, testing, qualifications, etc.
- Limited runs: Short production runs for niche products
- Bridge manufacturing: Fill the gap until higher volume production
- Service spares: Replacements for systems in the field
Challenges of Quick Turn Flex PCBs
Traditional flex PCB suppliers offer established capabilities but are geared towards higher volume production. Typical lead times range from 2-8 weeks depending on complexity. Rapid turnaround boards face some unique challenges:
- Front-loaded costs: High engineering and setup costs are absorbed over small volumes
- Panel utilization: Efficient panel space usage is harder with random small boards
- Inventory: Common materials must be stocked despite uncertain demand
- Testing: Full ICT test coverage requires selective test fixtures
- Logistics: Rush shipping or courier services often required
To overcome these barriers, some fabricators specialize in quick turnaround services. They optimize their processes and pricing strategies specifically for fast delivery of short run PCBs.
Quick Turn Flex PCB Manufacturing Process
The accelerated manufacturing process for fast turnaround flex PCBs focuses on streamlining steps and eliminating bottlenecks:
- Order Processing
- Simplified quoting and order system
- Automated DFM checks
- Identification of quick turn eligibility
- CAM and Tooling
- Front-loaded CAM team preparation
- Concurrent work on tooling files
- Direct communication for design clarification
- Materials Management
- Local specialized material inventory
- Kitting for each job
- Custom material sourcing if needed
- PCB Fabrication
- Small scale batch processing
- Flexible scheduling
- Additional shifts if required
- Testing
- Minimal test tooling for rapid start
- Parallel functional test
- ICT test if applicable
- Assembly
- Quick tooling made onsite
- Manual assembly and soldering
- Flexible staffing; Added shifts
- Final Testing and Inspection
- Comprehensive quality control
- Thorough visual inspection
- Spot checking of assemblies
- Logistics
- Local will-call pickup
- Rush domestic/intl shipping
- Individual tracking
Sourcing Quick Turn Flex PCBs
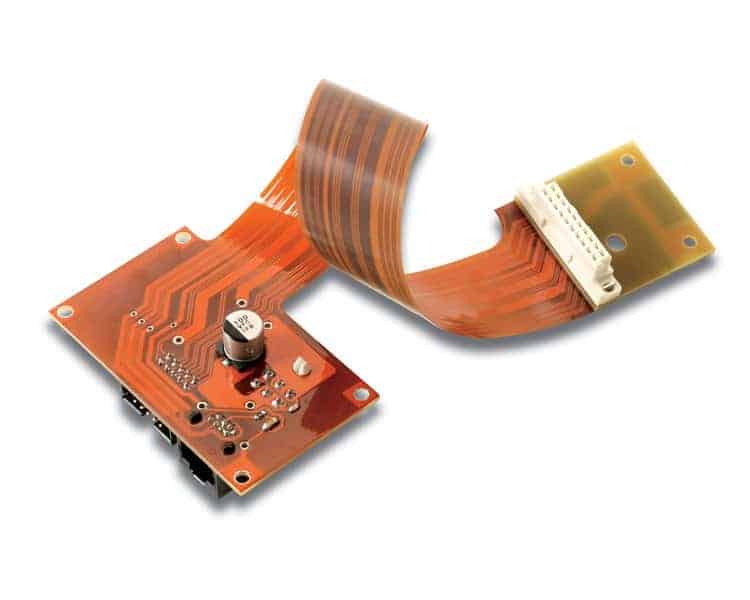
Domestic Specialists
A growing number of domestic PCB manufacturers cater specifically to fast turnaround prototyping and small batch assembly. Benefits include:
- Lead times as fast as 24 hours
- Lower minimum order quantities
- Reduced shipping time/cost
- IP protection/ITAR compliance
- Design for manufacturability guidance
- Dedicated engineering support
- Simple online ordering
Check reviews and talk to sales reps when selecting a quick turn supplier. Factors like responsiveness, attention to detail, manufacturing expertise and previous customer experiences should be carefully evaluated.
Offshore Volume Suppliers
Larger offshore manufacturers may be able to accommodate fast turnaround for small orders by opening up normally reserved quick turn production slots. Typical benefits are lower costs at higher volumes. Use caution to avoid:
- Lengthy communications and time zone difficulties
- Potential language barriers
- Hidden costs like expensive shipping
- Lack of design support
- Quality uncertainty
For best results, thoroughly discuss requirements upfront and get firm pricing commitments before proceeding.
In House Capability
For speed sensitive projects, building out internal rapid prototyping capabilities is an option. This requires investment in equipment like:
- Small scale etching/developing equipment
- Manual loading pick and place
- Reflow oven
- Used but capable test instrumentation
Labor costs are avoided but process know-how must be developed in house. This option only makes sense for companies with very frequent new product introductions.
Best Practices for Fast Flex PCB Delivery
To achieve the fastest possible turnaround, both the customer and manufacturer should adhere to some fundamental best practices:
For the Customer
- Provide clear specifications in fabrication/assembly drawings
- Use standard flex materials whenever possible
- Allow some flexibility in dimensions, solder mask, silkscreen, etc.
- Supply quality gerbers, ideally with placement/assembly files
- Make prompt decisions on quotations and design changes
- Pay expedited invoices as soon as possible
For the Manufacturer
- Optimize internal processes for rapid order fulfillment
- Maintain adequate quick turn material inventory
- Load balance work pipelines for maximum throughput
- Communicate proactively with customers on progress
- Ship as soon as product completes quality control
- Provide tracking info and receipts promptly
Cost Considerations
In general, expect to pay a premium for rush turnaround flex PCB orders compared to standard lead time production. Exact pricing is determined by factors like:
- Board size and layer count
- Design complexity
- Material requirements
- Lead time requested
- Order quantity
- Testing needs
- Assembly services
- Shipping requirements
Economies of scale allow longer lead time orders with larger quantities to benefit from volume discounts. For quick turn boards, smaller quantities plus the rush factors command higher per unit pricing.
However, the accelerated time to market often offsets the pricing premium. And being first to field a new design provides a competitive advantage that is hard to quantify.
Conclusion
Quick turnaround manufacturing enables flex PCB prototypes to be obtained in as little as 24-48 hours and short run production in 1 week or less. While traditional suppliers focus on high volume orders, specialized manufacturers offer rapid services catering to low and mid-volume requirements. With diligent sourcing and optimization on both sides, fast flex PCB delivery can give product development teams the speed advantage needed to stay ahead.
Frequently Asked Questions
Here are some common FAQs about quick turn flex PCB prototyping and production:
Q: What are typical lead times for fast turn flex PCBs?
A: Lead times can range from 24-48 hours for simple prototypes to 1 week for more complex designs. Small assembly batches generally take 1-2 weeks.
Q: What design factors affect the potential speed?
A: Board size and thickness, layer count, material selection, amount of stiffeners, and complexity of circuits and assemblies. Simpler is always faster.
Q: What is the typical cost per board for quick turn services?
A: Cost varies based on many factors, but expect to pay 2-4X the cost of standard lead time per board for rapid service.
Q: What are the limitations on smallest order quantities?
A: Some suppliers allow single piece prototype orders. Small batch assembly minimums are generally 10-25 pieces.
Q: What certifications should qualified suppliers have?
A: At minimum ISO 9001. Additional ones like IPC or ISO 13485 for medical devices are preferred.
Q: Can quick turn shops scale up to higher production volumes?
A: The focus is on fast prototyping and low volume batches. But some have capabilities up to a few thousand boards per month.
Leave a Reply