What is a Prototype and Why is it Important?
A prototype is an early sample, model, or release of a product built to test a concept or process. It is a crucial step in the product development process, as it allows companies to evaluate the feasibility, performance, and potential of a product before investing significant resources into full-scale production.
Prototypes serve several key purposes:
-
Proof of Concept: Prototypes help validate the basic principles and functionality of a product idea.
-
Design Refinement: Creating a physical prototype allows designers to identify and address any flaws or improvements in the product’s form, fit, and function.
-
User Feedback: Prototypes enable companies to gather valuable feedback from potential users, which can inform further product development and enhancements.
-
Manufacturability Assessment: By creating a prototype, companies can assess the feasibility and cost-effectiveness of manufacturing the product at scale.
-
Investor and Stakeholder Buy-in: A working prototype can be a powerful tool for demonstrating the potential of a product to investors, stakeholders, and decision-makers.
Factors Influencing Prototype Cost
The cost of creating a prototype can vary significantly depending on several factors:
Product Complexity
The complexity of the product is one of the primary drivers of prototype cost. More complex products, with numerous components, intricate designs, or advanced features, will typically require more time, resources, and specialized expertise to prototype, resulting in higher costs.
Material Selection
The choice of materials used in the prototype can greatly impact its cost. Some materials, such as plastics or lower-grade metals, may be less expensive than others, like high-performance alloys or advanced composites. The material selection will depend on the product’s intended function, performance requirements, and aesthetic considerations.
Prototyping Method
There are various methods for creating prototypes, each with its own associated costs:
Method | Description | Cost |
---|---|---|
3D Printing | Creating a physical model by depositing materials layer by layer | Low to Medium |
CNC Machining | Using computer-controlled machines to cut and shape materials | Medium to High |
Injection Molding | Injecting molten material into a mold to create parts | High |
Rapid Tooling | Creating molds or tooling quickly for short-run production | High |
The choice of prototyping method will depend on factors such as the required level of detail, material properties, and the intended purpose of the prototype.
Quantity
The number of prototypes required can also affect the overall cost. Producing a single prototype will generally be more expensive per unit than creating multiple prototypes, as the fixed costs associated with setup, tooling, and design can be spread across a larger number of units.
Design and Engineering
The time and expertise required for design and engineering can significantly contribute to prototype costs. More complex products may require the involvement of specialized engineers, designers, or consultants, which can increase expenses.
Strategies for Managing Prototype Costs
While prototype costs can be substantial, there are several strategies companies can employ to manage and optimize these expenses:
-
Start with a Minimum Viable Prototype: Begin by creating a basic prototype that focuses on the core functionality and features of the product. This approach allows for early validation and feedback while minimizing initial costs.
-
Leverage Digital Prototyping: Utilize computer-aided design (CAD) software and virtual simulations to create and test digital prototypes before investing in physical models. This can help identify potential issues and refine the design at a lower cost.
-
Use Off-the-Shelf Components: Where possible, incorporate readily available, standard components into the prototype design. This can reduce the need for custom parts and minimize the time and expense associated with procurement and production.
-
Collaborate with Suppliers and Partners: Engage with suppliers and partners early in the prototyping process to leverage their expertise, resources, and potential cost-saving opportunities. They may offer valuable insights into material selection, manufacturing methods, and design optimization.
-
Plan for Iterative Prototyping: Anticipate the need for multiple iterations of the prototype and budget accordingly. By planning for a phased approach, companies can allocate resources more effectively and incorporate learnings from each iteration into subsequent prototypes.
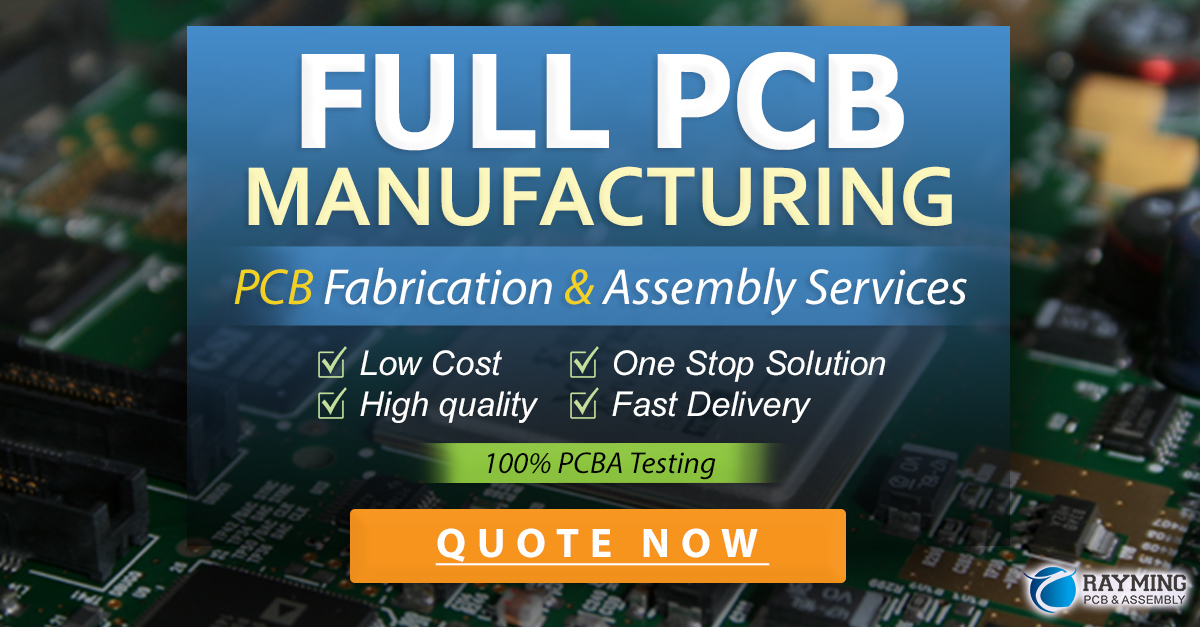
Case Studies
To illustrate the impact of prototype costs and the strategies employed to manage them, let’s examine two case studies:
Case Study 1: Medical Device Startup
A medical device startup was developing a new wearable device for monitoring patient vitals. Given the complex nature of the product and the stringent regulatory requirements, the company knew that prototyping costs could quickly escalate.
To manage these costs, the startup employed several strategies:
-
They began with a basic functional prototype, focusing on the core sensor technology and data transmission capabilities.
-
The company leveraged 3D printing to create initial housing designs, allowing for rapid iteration and refinement at a lower cost compared to traditional tooling methods.
-
They collaborated with a contract manufacturer specializing in medical devices to optimize the design for manufacturability and identify cost-saving opportunities in material selection and component sourcing.
By implementing these strategies, the startup was able to create a functional prototype within their budget and secure the necessary funding to proceed with further development and testing.
Case Study 2: Consumer Electronics Manufacturer
A large consumer electronics manufacturer was developing a new smartphone with advanced camera capabilities. With a tight timeline and a highly competitive market, the company needed to balance prototype costs with the need for rapid iteration and refinement.
To achieve this, the manufacturer employed the following strategies:
-
They leveraged their in-house design and engineering teams to create detailed digital prototypes, minimizing the need for physical models in the early stages.
-
The company utilized rapid prototyping methods, such as 3D printing and CNC machining, to quickly create physical models for testing and validation.
-
They collaborated closely with their existing suppliers to source components and materials, leveraging economies of scale and established relationships to secure favorable pricing.
By employing these strategies, the manufacturer was able to create multiple iterations of the prototype within their allocated budget, ultimately leading to a successful product launch.
FAQ
-
Q: How much does it typically cost to create a prototype?
A: The cost of creating a prototype can vary widely, ranging from a few hundred dollars to several hundred thousand dollars, depending on factors such as product complexity, materials, prototyping method, and required quantity. -
Q: What is the most cost-effective prototyping method?
A: The most cost-effective prototyping method will depend on the specific product and its requirements. However, methods like 3D printing and rapid prototyping tend to be more affordable compared to traditional tooling and molding methods, particularly for low-volume prototypes. -
Q: How can I reduce the cost of prototyping?
A: Strategies for reducing prototype costs include starting with a minimum viable prototype, leveraging digital prototyping, using off-the-shelf components, collaborating with suppliers and partners, and planning for iterative prototyping. -
Q: Is it worth investing in expensive prototypes?
A: The decision to invest in expensive prototypes should be based on the potential benefits and risks associated with the product. In some cases, higher prototype costs may be justified if they lead to a more refined, successful final product or help secure necessary funding and support. -
Q: How many prototype iterations should I plan for?
A: The number of prototype iterations required will vary depending on the complexity of the product and the specific development goals. However, it’s generally advisable to plan for at least 2-3 iterations to allow for design refinements, testing, and incorporation of user feedback.
Conclusion
Prototype cost is a critical consideration in the product development process, as it can significantly impact a company’s budget, timeline, and overall success. By understanding the factors that influence prototype costs and employing strategies to manage and optimize these expenses, companies can effectively navigate the prototyping phase and create successful, market-ready products.
Effective prototype cost management involves a combination of careful planning, strategic decision-making, and collaboration with key partners and stakeholders. By leveraging the right mix of prototyping methods, materials, and resources, companies can strike a balance between controlling costs and creating high-quality, functional prototypes that pave the way for successful product launches.
Leave a Reply