Introduction to Printed and Flexible Electronics
Printed and flexible electronics, also known as Flexitronics, is an emerging field that combines the advantages of traditional electronics with the flexibility and affordability of printing technologies. This innovative approach to electronics manufacturing has the potential to revolutionize various industries, from consumer electronics to healthcare and beyond.
What are Printed and Flexible Electronics?
Printed and flexible electronics refer to electronic devices and circuits that are manufactured using printing technologies on flexible substrates, such as plastic, paper, or fabric. Unlike conventional rigid electronics, flexitronics can be bent, stretched, and twisted without losing their functionality. This unique property enables the development of a wide range of applications, including:
- Flexible displays
- Wearable devices
- Smart packaging
- Medical sensors
- Energy harvesting systems
Advantages of Flexitronics
Flexitronics offer several advantages over traditional rigid electronics:
- Flexibility: The ability to conform to various shapes and surfaces opens up new possibilities for product design and integration.
- Lightweight: Flexible substrates are typically lighter than rigid PCBs, making flexitronics ideal for portable and wearable devices.
- Cost-effective: Printing technologies enable high-volume, low-cost production of electronic devices and circuits.
- Sustainability: Many flexible substrates are recyclable or biodegradable, reducing electronic waste and environmental impact.
Printing Technologies for Flexitronics
Several printing technologies have been adapted for the manufacture of printed and flexible electronics, each with its own advantages and limitations.
Inkjet Printing
Inkjet printing is a digital printing method that deposits tiny droplets of conductive or semiconductive ink onto a flexible substrate. This technology offers high precision, low material waste, and the ability to print complex patterns. However, inkjet printing is limited by the available inks and the relatively slow printing speed.
Screen Printing
Screen printing is a versatile printing technique that uses a mesh screen to transfer ink onto a substrate. This method is well-suited for printing thick layers of conductive or dielectric materials, making it ideal for manufacturing printed batteries, capacitors, and resistors. Screen printing is also scalable for high-volume production, but it lacks the precision of inkjet printing.
Gravure Printing
Gravure printing is a high-speed, roll-to-roll printing process that uses an engraved cylinder to transfer ink onto a substrate. This technology is capable of producing high-quality, high-resolution prints at a low cost, making it attractive for large-scale production of flexitronics. However, gravure printing requires the fabrication of expensive engraved cylinders, which can be a barrier for low-volume or custom applications.
Comparison of Printing Technologies
Printing Technology | Advantages | Limitations |
---|---|---|
Inkjet Printing | High precision, low material waste, complex patterns | Limited inks, slow printing speed |
Screen Printing | Thick layers, scalable for high-volume production | Lower precision compared to inkjet |
Gravure Printing | High-speed, high-resolution, low-cost for large-scale production | Expensive engraved cylinders, not suitable for low-volume or custom applications |
Materials for Printed and Flexible Electronics
The development of new materials has been crucial to the advancement of printed and flexible electronics. These materials must be compatible with printing technologies, exhibit the desired electrical properties, and maintain their performance under mechanical stress.
Conductive Inks
Conductive inks are essential for printing electrical circuits and interconnects. These inks typically contain metal nanoparticles, such as silver, copper, or gold, dispersed in a liquid vehicle. Conductive polymers, such as PEDOT:PSS, are also used in some applications. The choice of conductive ink depends on the required conductivity, stability, and cost.
Semiconductive Inks
Semiconductive inks are used to print active electronic components, such as transistors and diodes. These inks often contain organic semiconductors, metal oxides, or carbon nanotubes. The performance of printed semiconductors is still lower than that of traditional silicon-based devices, but ongoing research aims to close this gap.
Dielectric and Insulating Materials
Dielectric and insulating materials are necessary for isolating conductive layers and creating capacitors and other passive components. Common materials include polymer dielectrics, such as PVP and PMMA, and inorganic dielectrics, such as BaTiO3 and Al2O3. The choice of dielectric material depends on the required dielectric constant, breakdown voltage, and compatibility with the printing process.
Substrates for Flexitronics
Flexible substrates are the foundation of printed and flexible electronics. The most common substrates are plastic films, such as PET, PEN, and PI, due to their flexibility, transparency, and low cost. Paper and fabrIC Substrates are also used in some applications, such as smart packaging and wearable electronics. The choice of substrate depends on the required mechanical, thermal, and chemical properties, as well as the compatibility with the printing process.
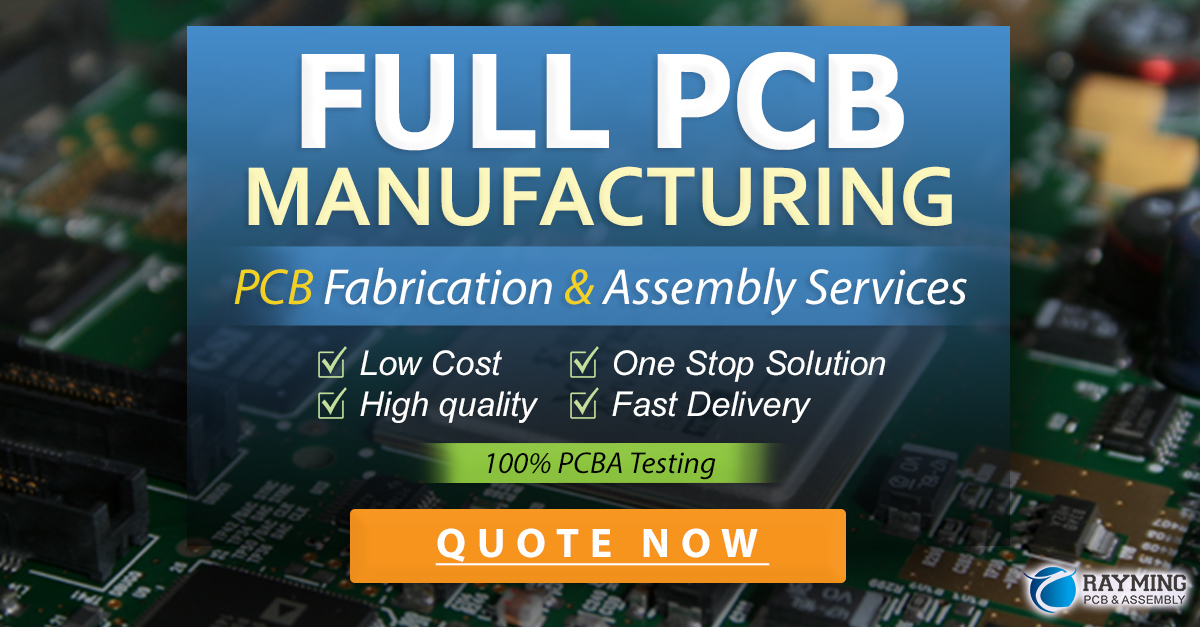
Applications of Printed and Flexible Electronics
Printed and flexible electronics have the potential to impact various industries and enable new applications that were previously not possible with rigid electronics.
Flexible Displays
Flexible displays are one of the most promising applications of flexitronics. These displays can be bent, rolled, or stretched, enabling new form factors for smartphones, tablets, and wearable devices. Flexible OLED displays are already commercially available in some high-end smartphones, and ongoing research aims to improve their performance and durability.
Wearable Electronics
Flexitronics are ideally suited for wearable electronics, as they can conform to the shape of the human body and withstand the stresses of daily wear. Printed sensors, such as strain gauges and Temperature Sensors, can be integrated into clothing or directly attached to the skin for health monitoring and sports performance tracking. Flexible batteries and energy harvesting devices can power these wearable systems, enabling long-term, continuous monitoring.
Medical Devices
Printed and flexible electronics have numerous applications in the medical field, from diagnostic devices to drug delivery systems. Flexible biosensors can be used to monitor vital signs, such as heart rate, blood pressure, and glucose levels, providing real-time data for personalized healthcare. Printed drug delivery patches can release medications at controlled rates, improving patient compliance and treatment outcomes.
Smart Packaging
Flexitronics can revolutionize the packaging industry by adding intelligent features to traditional packaging materials. Printed sensors can monitor the freshness and quality of food products, while printed displays can provide interactive information to consumers. Smart packaging can also incorporate anti-counterfeiting measures, such as printed RFID tags and unique graphic patterns, to ensure product authenticity and track supply chain logistics.
Energy Harvesting and Storage
Printed and flexible electronics can enable new energy harvesting and storage solutions. Flexible solar cells can be integrated into clothing, buildings, and vehicles to generate electricity from ambient light. Printed thermoelectric generators can convert waste heat into usable energy. Flexible supercapacitors and batteries can store the generated energy and power various electronic devices.
Challenges and Future Prospects
Despite the significant progress made in printed and flexible electronics, several challenges remain to be addressed before widespread adoption can occur.
Performance and Reliability
The performance of printed electronic devices is still lower than that of traditional silicon-based devices. Improving the mobility, stability, and reliability of printed semiconductors and other components is an ongoing research challenge. Additionally, the long-term durability of flexitronics under repeated mechanical stress needs to be further investigated and optimized.
Scalability and Manufacturing
Scaling up the production of printed and flexible electronics from lab-scale to industrial-scale manufacturing is another challenge. Ensuring consistent print quality, yield, and reliability across large areas and high volumes requires the development of advanced printing equipment and process control methods. Standardization of materials, processes, and testing methods is also necessary to facilitate the adoption of flexitronics by various industries.
Integration and Interconnects
Integrating printed and flexible electronics with conventional rigid electronics and other systems is crucial for many applications. Developing reliable and efficient interconnect technologies, such as printed conductive traces, conductive adhesives, and low-temperature soldering, is essential for seamless integration. Additionally, the development of hybrid systems that combine the strengths of both flexible and rigid electronics can open up new possibilities for product design and functionality.
Cost and Market Adoption
The cost of printed and flexible electronics is expected to decrease as manufacturing processes mature and economies of scale are achieved. However, the initial investment in equipment and materials can be a barrier for some companies. Demonstrating clear cost and performance advantages over traditional electronics will be crucial for driving market adoption. Additionally, educating consumers and businesses about the benefits and potential applications of flexitronics will be necessary to create demand and foster growth in this emerging field.
Frequently Asked Questions
- What is the difference between printed electronics and flexible electronics?
-
Printed electronics refer to electronic devices and circuits that are manufactured using printing technologies, while flexible electronics refer to devices that can be bent, stretched, or twisted without losing their functionality. Printed and flexible electronics are often combined to create devices that are both low-cost and mechanically flexible.
-
What are the most common printing technologies used for flexitronics?
-
The most common printing technologies used for flexitronics are inkjet printing, screen printing, and gravure printing. Each technology has its own advantages and limitations in terms of resolution, speed, and material compatibility.
-
What are the main challenges in the development of printed and flexible electronics?
-
The main challenges in the development of printed and flexible electronics include improving the performance and reliability of printed components, scaling up manufacturing processes, developing reliable interconnect technologies, and reducing costs to drive market adoption.
-
What are some of the most promising applications of printed and flexible electronics?
-
Some of the most promising applications of printed and flexible electronics include flexible displays, wearable devices, medical sensors, smart packaging, and energy harvesting and storage solutions.
-
How do printed and flexible electronics contribute to sustainability?
- Printed and flexible electronics can contribute to sustainability by reducing electronic waste and enabling new applications that promote energy efficiency and environmental monitoring. Many flexible substrates are recyclable or biodegradable, and printed electronics can be used to create low-cost, disposable sensors for environmental sensing and pollution monitoring.
Conclusion
Printed and flexible electronics, or flexitronics, represent a paradigm shift in the way we design, manufacture, and use electronic devices. By combining the advantages of printing technologies and flexible materials, flexitronics enable a wide range of new applications, from flexible displays and wearable devices to smart packaging and medical sensors. As research advances and manufacturing processes mature, the potential for printed and flexible electronics to transform various industries and improve our daily lives is immense. However, challenges related to performance, reliability, scalability, and cost must be addressed to fully realize the potential of this exciting field. With ongoing collaboration between academia, industry, and government, the future of flexitronics looks bright, and we can expect to see more innovative products and solutions in the years to come.
Leave a Reply