Understanding Power Requirements
Determining Voltage and Current Needs
The first step in power PCB Design is to understand the power requirements of your system. This involves determining the voltage and current needs of each component on the board. It is essential to consider the maximum power consumption of each component and the overall power budget of the system.
Selecting Appropriate Power Sources
Based on the power requirements, you need to select appropriate power sources such as batteries, power adapters, or voltage regulators. Consider factors such as input voltage range, output voltage stability, and current handling capacity when choosing power sources.
Calculating Power Dissipation
Power dissipation is the amount of power that is converted into heat during the operation of electronic components. It is crucial to calculate the power dissipation of each component and ensure that the PCB can effectively dissipate the generated heat to prevent overheating and component failure.
Choosing the Right Components
Power MOSFETs and Transistors
Power MOSFETs and transistors are commonly used in power PCB design for switching and regulating power. When selecting these components, consider parameters such as voltage rating, current rating, on-resistance, and switching speed. It is also important to choose components with appropriate packaging and heat dissipation capabilities.
Inductors and Transformers
Inductors and transformers play a vital role in power conversion and isolation. When selecting these components, consider factors such as inductance value, current rating, DC resistance, and saturation current. Pay attention to the core material and winding type to ensure optimal performance and efficiency.
Capacitors for Filtering and Decoupling
Capacitors are used in power PCBs for filtering and decoupling purposes. They help to reduce noise, smooth out voltage ripples, and provide a stable power supply to the components. When choosing capacitors, consider the capacitance value, voltage rating, equivalent series resistance (ESR), and temperature stability.
Proper Grounding and Shielding Techniques
Ground Plane Design
A well-designed ground plane is essential for power PCB design. It provides a low-impedance return path for currents and helps to minimize noise and EMI (Electromagnetic Interference). When designing the ground plane, consider factors such as copper thickness, ground plane splitting, and proper grounding of components.
Minimizing Ground Loops
Ground loops occur when there are multiple paths for current to flow between two points in a circuit. They can introduce noise and degrade the performance of the power system. To minimize ground loops, ensure that there is a single, low-impedance ground path and avoid creating multiple ground connections.
Shielding Sensitive Circuits
In power PCB design, it is important to shield sensitive circuits from sources of EMI. Techniques such as using shielding cans, grounded copper pours, and proper component placement can help to reduce the impact of EMI on the system. Consider the frequency range and intensity of the expected EMI when implementing shielding measures.
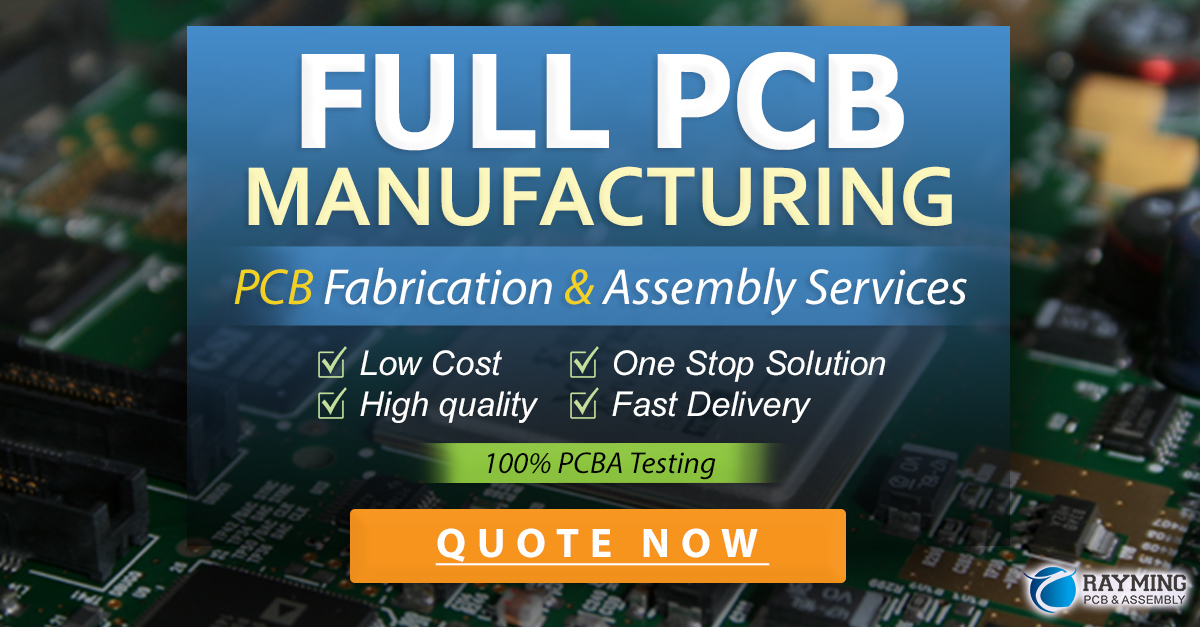
Thermal Management Considerations
Heat Sinking and Thermal Vias
Power components generate heat during operation, and it is crucial to dissipate this heat effectively to prevent overheating and component failure. Heat sinking involves attaching a heat sink to the component to increase its surface area and improve heat dissipation. Thermal vias are used to transfer heat from the component to the PCB’s ground plane or other heat-dissipating layers.
PCB Layer Stackup for Heat Dissipation
The PCB layer stackup plays a significant role in thermal management. By strategically placing copper layers and using thicker copper for power and ground planes, you can improve heat dissipation and reduce thermal resistance. Consider the thermal conductivity of the PCB material and the placement of components when designing the layer stackup.
Airflow and Cooling Techniques
In addition to heat sinking and thermal vias, airflow and cooling techniques can be employed to manage heat in power PCBs. This includes using fans, heatsinks with fins, and proper component placement to allow for adequate airflow. In some cases, liquid cooling or other advanced cooling techniques may be necessary for high-power applications.
Safety and Compliance Considerations
Isolation and Creepage Distance
Isolation and creepage distance are critical safety considerations in power PCB design. Isolation refers to the separation between different voltage domains, while creepage distance is the shortest path between two conductive parts. Proper isolation and creepage distance help to prevent electrical shock and ensure the safety of users.
Fuse and Over-Current Protection
Incorporating fuses and over-current protection devices is essential to protect the power system and users from potential hazards. Fuses are designed to interrupt the flow of current when it exceeds a predetermined level, preventing damage to components and reducing the risk of fire. Over-current protection devices, such as resettable fuses or circuit breakers, provide similar protection and can be reset once the fault condition is cleared.
Regulatory Compliance and Certifications
Power PCBs must comply with various regulatory standards and certifications depending on the application and target market. Some common standards include UL (Underwriters Laboratories), IEC (International Electrotechnical Commission), and FCC (Federal Communications Commission). It is important to understand the applicable regulations and design the PCB to meet the required specifications and safety standards.
Frequently Asked Questions (FAQ)
1. What is the importance of power plane in PCB design?
A power plane in PCB design serves as a low-impedance source of power for the components on the board. It provides a stable and uniform voltage distribution, minimizes voltage drops, and reduces noise and EMI. The power plane also acts as a heat dissipation layer, helping to spread heat evenly across the PCB.
2. How do I select the appropriate voltage regulator for my power PCB?
When selecting a voltage regulator for your power PCB, consider factors such as input voltage range, output voltage, current rating, efficiency, and package type. Also, take into account the noise performance, transient response, and protection features such as over-voltage and over-current protection. It is important to choose a voltage regulator that meets your specific power requirements and design constraints.
3. What are the benefits of using a four-layer PCB for power design?
Using a four-layer PCB for power design offers several benefits. It allows for dedicated power and ground planes, which provide low-impedance paths for power distribution and reduce noise and EMI. The additional layers also provide more routing space for signal traces and improve heat dissipation. Four-layer PCBs offer better signal integrity and can handle higher power densities compared to two-layer PCBs.
4. How do I minimize EMI in my power PCB design?
To minimize EMI in your power PCB design, consider the following techniques:
– Use proper grounding and shielding techniques, such as ground planes and shielding cans.
– Keep power and signal traces as short as possible and avoid running them parallel to each other.
– Use decoupling capacitors close to power pins of components to reduce high-frequency noise.
– Implement proper filtering techniques, such as using ferrite beads or LC filters.
– Follow good PCB layout practices, such as avoiding sharp bends in traces and maintaining proper trace spacing.
5. What are the safety considerations when designing a high-voltage power PCB?
When designing a high-voltage power PCB, safety is of utmost importance. Some key safety considerations include:
– Ensuring proper isolation and creepage distance between high-voltage and low-voltage areas.
– Using appropriate insulation materials and spacing to prevent electrical breakdown.
– Incorporating fuses and over-current protection devices to prevent damage and reduce fire hazards.
– Following relevant safety standards and obtaining necessary certifications for the specific application.
– Providing clear labeling and warnings for high-voltage areas on the PCB.
Conclusion
Designing power PCBs requires careful consideration of various factors to ensure optimal performance, reliability, and safety. As a beginner, understanding power requirements, selecting the right components, implementing proper grounding and shielding techniques, managing thermal aspects, and adhering to safety and compliance standards are crucial. By keeping these five major things in mind and continuously learning and refining your skills, you can create robust and efficient power PCB designs.
Remember, power PCB design is an iterative process that involves simulation, prototyping, and testing. Don’t hesitate to seek guidance from experienced designers, refer to industry guidelines and standards, and leverage the wealth of resources available online. With practice and perseverance, you can master the art of power PCB design and create innovative electronic products.
Leave a Reply