What is a Polyimide PCB?
A Polyimide PCB, also known as a PI PCB or Kapton PCB, is a type of printed circuit board that uses polyimide as the base material instead of the more commonly used FR-4. Polyimide is a high-performance polymer that offers exceptional thermal, mechanical, and electrical properties, making it an ideal choice for demanding applications.
Polyimide was first developed by DuPont in the 1960s under the brand name Kapton. It quickly gained popularity in the aerospace and military industries due to its ability to withstand extreme temperatures and harsh environments. Today, polyimide PCBs are used in a wide range of applications, from consumer electronics to medical devices.
Key Properties of Polyimide
- High thermal stability: Polyimide can withstand temperatures up to 400°C without degrading.
- Excellent mechanical strength: Polyimide has a tensile strength of 231 MPa and a Young’s modulus of 2.5 GPa.
- Low dielectric constant: Polyimide has a dielectric constant of 3.4, which is lower than FR-4 (4.5).
- High resistance to chemicals: Polyimide is resistant to most solvents, acids, and oils.
- Lightweight and flexible: Polyimide PCBs can be made very thin (down to 25μm) and flexible.
Property | Polyimide | FR-4 |
---|---|---|
Maximum Operating Temperature | 400°C | 140°C |
Tensile Strength | 231 MPa | 415 MPa |
Dielectric Constant | 3.4 | 4.5 |
Density | 1.42 g/cm³ | 1.85 g/cm³ |
Types of Polyimide PCBs
There are several types of polyimide PCBs, each with its own unique features and benefits.
Standard Polyimide PCBs
Standard polyimide PCBs are made with a polyimide base material and copper traces. They can be single-sided, double-sided, or multilayer, depending on the complexity of the circuit design. Standard polyimide PCBs are often used in applications that require high temperature resistance, such as aerospace and automotive electronics.
Flexible Polyimide PCBs
Flexible polyimide PCBs, also known as flex PCBs or FPCBs, are made with a thin, flexible polyimide substrate. They can be bent, folded, or twisted without damaging the circuit, making them ideal for applications where space is limited or where the PCB needs to conform to a specific shape. Flexible polyimide PCBs are commonly used in wearable electronics, medical devices, and automotive applications.
Rigid-Flex Polyimide PCBs
Rigid-flex polyimide PCBs combine the benefits of standard and flexible polyimide PCBs. They consist of rigid PCB sections connected by flexible polyimide sections, allowing for complex 3D designs and reducing the need for connectors and cables. Rigid-flex polyimide PCBs are often used in aerospace, military, and medical applications.
High Density Interconnect (HDI) Polyimide PCBs
HDI polyimide PCBs are designed with very fine pitch traces and vias, allowing for higher component density and smaller form factors. They often use microvias (vias with a diameter of 150μm or less) and buried or blind vias to achieve higher connectivity. HDI polyimide PCBs are commonly used in smartphones, tablets, and other portable electronics.
Benefits of Polyimide PCBs
Polyimide PCBs offer several benefits over traditional FR-4 PCBs, making them the preferred choice for certain applications.
High Temperature Resistance
One of the main advantages of polyimide PCBs is their ability to withstand high temperatures. While FR-4 PCBs can only operate up to 140°C, polyimide PCBs can withstand temperatures up to 400°C. This makes them ideal for applications that generate a lot of heat, such as power electronics, aerospace systems, and automotive engines.
Lightweight and Flexible
Polyimide PCBs can be made very thin and lightweight, making them suitable for applications where weight and space are critical factors. Flexible polyimide PCBs can also conform to complex shapes and fit into tight spaces, reducing the need for connectors and cables.
High Reliability
Polyimide PCBs are highly resistant to chemicals, moisture, and other environmental factors that can degrade the performance of traditional PCBs. They also have excellent mechanical strength and dimensional stability, ensuring reliable performance over a long lifespan.
Low Dielectric Constant
Polyimide has a lower dielectric constant than FR-4, which means that it can support higher signal speeds and lower signal loss. This makes polyimide PCBs suitable for high-frequency applications, such as 5G wireless communication and radar systems.
Cost-Effective
Although polyimide PCBs are generally more expensive than FR-4 PCBs, they can be more cost-effective in the long run due to their high reliability and long lifespan. In applications where failure is not an option, such as medical devices and aerospace systems, the added cost of polyimide PCBs is justified by their superior performance.
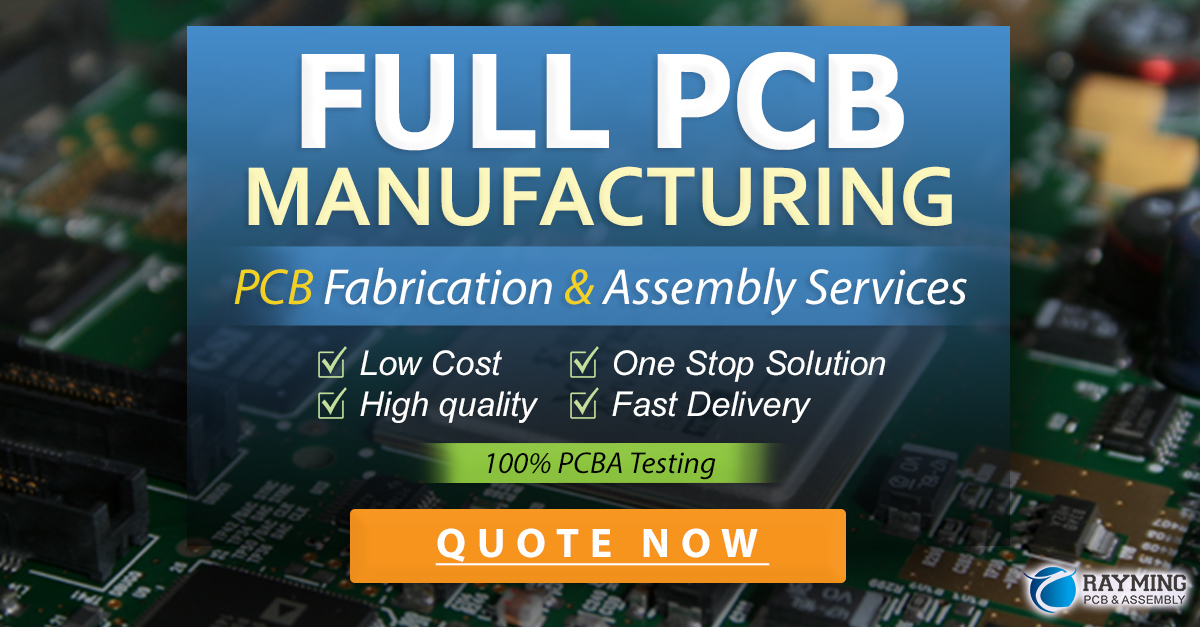
Applications of Polyimide PCBs
Polyimide PCBs are used in a wide range of industries and applications, including:
- Aerospace and Defense
- Satellites
- Missiles
- Avionics
- Automotive
- Engine control units
- Brake systems
- Electric vehicles
- Medical Devices
- Implantable devices
- Diagnostic equipment
- Wearable sensors
- Industrial
- Oil and gas drilling
- Power generation
- Robotics
- Consumer Electronics
- Smartphones
- Tablets
- Wearables
- Telecommunications
- 5G base stations
- Fiber optic networks
- Radar systems
FAQ
Q: What is the difference between polyimide and FR-4 PCBs?
A: Polyimide PCBs are made with a polyimide base material, while FR-4 PCBs are made with a fiberglass-reinforced epoxy resin. Polyimide offers higher temperature resistance, lower dielectric constant, and greater flexibility than FR-4, but is also more expensive.
Q: Can polyimide PCBs be used for all applications?
A: While polyimide PCBs offer many benefits, they are not necessary or cost-effective for all applications. FR-4 PCBs are still the most common choice for general-purpose electronics due to their lower cost and adequate performance for most use cases.
Q: How are flexible polyimide PCBs manufactured?
A: Flexible polyimide PCBs are manufactured using a similar process to standard PCBs, but with a thin polyimide film as the base material instead of rigid FR-4. The copper traces are etched onto the polyimide film, and the film is then covered with a protective coverlay. The PCB can then be cut and formed into the desired shape.
Q: What are the challenges of working with polyimide PCBs?
A: One of the main challenges of working with polyimide PCBs is their higher cost compared to FR-4 PCBs. Polyimide material is more expensive, and the manufacturing process is more complex, requiring specialized equipment and expertise. Another challenge is the difficulty of soldering components to polyimide PCBs due to their high temperature resistance.
Q: How can I choose the right type of polyimide PCB for my application?
A: Choosing the right type of polyimide PCB depends on the specific requirements of your application, such as temperature range, flexibility, and component density. Standard polyimide PCBs are suitable for high-temperature applications, while flexible polyimide PCBs are ideal for applications requiring conformity to complex shapes. HDI polyimide PCBs are best for applications requiring high component density and miniaturization. Consulting with a PCB manufacturer or design expert can help you make the best choice for your application.
Conclusion
Polyimide PCBs offer a range of benefits over traditional FR-4 PCBs, including high temperature resistance, flexibility, and reliability. With several types of polyimide PCBs available, including standard, flexible, rigid-flex, and HDI, designers can choose the best option for their specific application requirements.
While polyimide PCBs are more expensive than FR-4 PCBs, their superior performance and long lifespan can make them a cost-effective choice in the long run, particularly for demanding applications in industries such as aerospace, automotive, and medical devices.
As technology continues to advance and the demand for high-performance electronics grows, polyimide PCBs are likely to play an increasingly important role in enabling the next generation of products and systems.
Leave a Reply