What is PCB Wiring?
PCB wiring refers to the process of connecting various components on a printed circuit board using thin strands of insulated wire or conductive traces. The goal is to create a functional electronic circuit that performs a specific task, such as powering a device, processing signals, or storing data. PCB wiring can be done manually or automatically, depending on the complexity of the board and the volume of production.
Tools and Materials Needed for PCB Wiring
To wire a PCB properly, you will need the following tools and materials:
Tool/Material | Description |
---|---|
Soldering iron | A tool used to melt solder and join electrical components to the PCB |
Solder | A metal alloy used to create electrical connections between components and the PCB |
Wire cutters | A tool used to cut wires to the desired length |
Wire strippers | A tool used to remove the insulation from the ends of wires |
Tweezers | A tool used to pick up and place small components on the PCB |
Magnifying glass | A tool used to inspect solder joints and trace continuity |
Multimeter | A tool used to measure voltage, current, and resistance in the circuit |
Insulated wires | Thin strands of copper wire with a non-conductive coating used to connect components |
Flux | A chemical agent used to promote the flow of solder and prevent oxidation |
Desoldering wick | A braided copper wire used to remove excess solder from joints |
PCB Holder | A device used to secure the PCB during the wiring process |
Step-by-Step Guide to PCB Wiring
Follow these steps to wire a PCB:
-
Design the PCB layout: Use PCB design software to create a schematic diagram and a physical layout of the components and traces on the board. Ensure that the design follows the best practices for PCB layout, such as minimizing trace lengths, avoiding sharp angles, and providing adequate clearance between components.
-
Gather the components: Collect all the necessary components for your PCB, such as resistors, capacitors, ICs, and connectors. Ensure that the components are compatible with the PCB design and the desired functionality of the circuit.
-
Place the components: Secure the PCB in a PCB holder or a vise. Using tweezers, place the components on the PCB according to the layout design. Ensure that the components are oriented correctly and seated firmly against the board.
-
Solder the components: Heat up the soldering iron to the appropriate temperature (usually 300-400°C). Apply a small amount of solder to the tip of the iron to promote heat transfer. Touch the tip of the iron to the pad on the PCB and the lead of the component simultaneously. Feed a small amount of solder into the joint and let it flow around the lead and pad. Remove the iron and let the joint cool for a few seconds. Repeat this process for all the components on the board.
-
Wire the components: Cut the insulated wires to the desired lengths using wire cutters. Strip about 1/4 inch of insulation from each end of the wire using wire strippers. Tin the exposed ends of the wires by applying a small amount of solder. Place the tinned end of the wire into the hole or pad on the PCB and solder it in place. Repeat this process for all the necessary connections between components.
-
Inspect the joints: Use a magnifying glass to visually inspect each solder joint for quality and continuity. Look for signs of cold joints, bridging, or insufficient solder. Use a multimeter to test for continuity between the components and ensure that there are no short circuits or open connections.
-
Clean the flux: Apply flux remover or isopropyl alcohol to a lint-free cloth and gently wipe the PCB to remove any residual flux or debris. Be careful not to dislodge any components or damage the board.
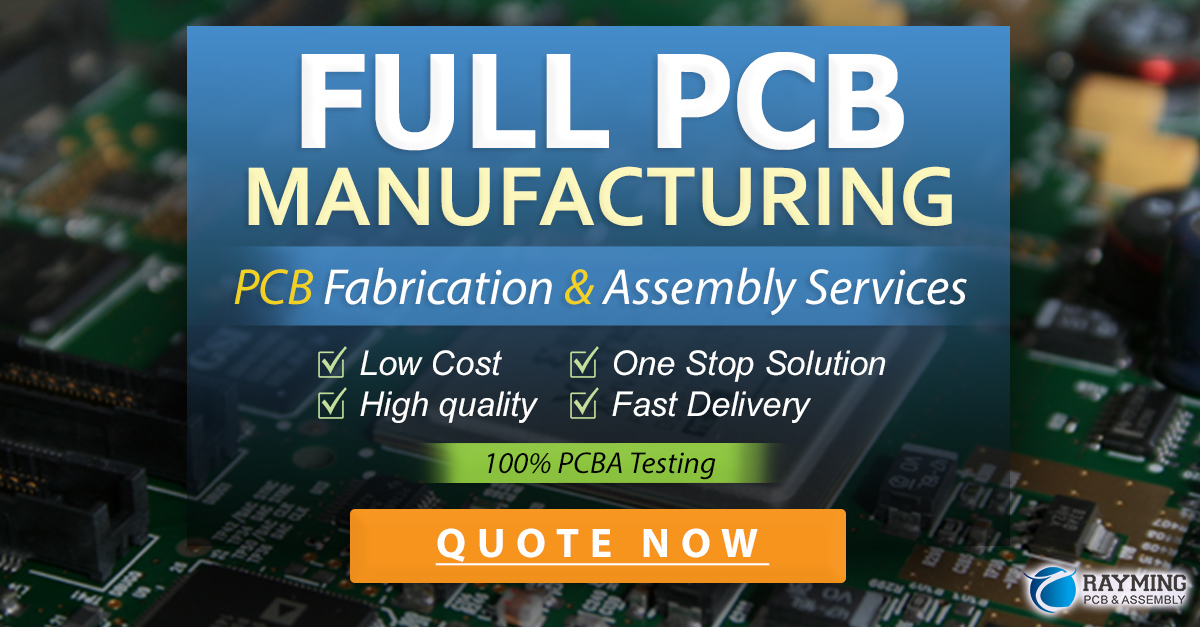
PCB Wiring Techniques
There are several techniques used in PCB wiring, depending on the type of components and the desired connection method. Here are some common PCB wiring techniques:
Through-Hole Wiring
Through-hole wiring involves inserting the leads of components into holes drilled in the PCB and soldering them in place. This technique is suitable for larger components with sturdy leads, such as resistors, capacitors, and connectors. Through-hole wiring provides a strong mechanical connection and is easier to inspect and repair than surface-mount wiring.
Surface-Mount Wiring
Surface-mount wiring involves soldering components directly onto pads on the surface of the PCB. This technique is suitable for smaller components with flat leads or terminations, such as chip resistors, chip capacitors, and SOICs. Surface-mount wiring allows for higher component density and faster assembly than through-hole wiring, but requires more precise soldering skills and equipment.
Wire Wrapping
Wire wrapping involves wrapping thin insulated wires around square posts on the PCB to create connections between components. This technique was popular in the early days of PCB manufacturing, but has largely been replaced by through-hole and surface-mount wiring. Wire wrapping is still used in some specialized applications, such as prototyping and high-reliability systems.
Point-to-Point Wiring
Point-to-point wiring involves soldering components and wires directly to each other without using a PCB. This technique is suitable for simple circuits with few components, or for repairs and modifications to existing PCBs. Point-to-point wiring is less reliable and more prone to errors than PCB wiring, but can be useful in certain situations.
Best Practices for PCB Wiring
To ensure the quality and reliability of your PCB wiring, follow these best practices:
-
Use the correct wire gauge: Choose the appropriate wire gauge for your PCB based on the current and voltage requirements of the circuit. Using a wire that is too thin can cause overheating and failure, while using a wire that is too thick can make the PCB bulky and difficult to assemble.
-
Keep wires short and neat: Minimize the length of wires between components to reduce resistance and inductance. Route the wires neatly and avoid crossing them wherever possible to prevent short circuits and interference.
-
Provide strain relief: Use cable ties, clamps, or adhesives to secure wires to the PCB and prevent them from pulling on the solder joints. This is especially important for wires that are subject to movement or vibration.
-
Use heat shrink tubing: Cover exposed wire connections with heat shrink tubing to provide insulation and protection from damage. Heat shrink tubing comes in various sizes and colors and can be easily shrunk using a heat gun or a lighter.
-
Label the wires: Use wire labels or color codes to identify the function and polarity of each wire. This will make it easier to troubleshoot and repair the PCB in the future.
-
Test and inspect: Always test the PCB for proper functionality and inspect the wiring for any defects or errors before putting it into use. Use a multimeter to check for continuity, voltage, and resistance, and use a magnifying glass to visually inspect the solder joints and traces.
Troubleshooting PCB Wiring Issues
Even with the best practices and techniques, PCB wiring issues can still occur. Here are some common PCB wiring issues and how to troubleshoot them:
Issue | Symptom | Possible Cause | Solution |
---|---|---|---|
Open circuit | No continuity between two points | Broken wire, cold solder joint, damaged trace | Visually inspect the wiring, reflow the solder joint, repair the trace with jumper wire |
Short circuit | Continuity between two points that should not be connected | Solder bridge, frayed wire, conductive debris | Visually inspect the wiring, remove the solder bridge with solder wick, insulate the frayed wire, clean the PCB |
Intermittent connection | Continuity that comes and goes | Loose wire, cracked solder joint, damaged component | Wiggle the wires and components to identify the loose connection, reflow the solder joint, replace the damaged component |
Overheating | Discoloration or melting of insulation, smoke or burning smell | Overcurrent, insufficient wire gauge, poor ventilation | Check the current draw of the circuit, replace the wire with a thicker gauge, provide adequate cooling and ventilation |
Interference | Unwanted noise or signal distortion | Crosstalk between wires, ground loops, EMI/RFI | Separate the wires, provide shielding, use twisted pair or coaxial cable, decouple the power supply |
FAQ
-
What is the difference between through-hole and surface-mount wiring?
Through-hole wiring involves inserting component leads into holes drilled in the PCB and soldering them in place, while surface-mount wiring involves soldering components directly onto pads on the surface of the PCB. Through-hole wiring is suitable for larger components and provides a stronger mechanical connection, while surface-mount wiring allows for higher component density and faster assembly. -
How do I choose the correct wire gauge for my PCB?
The choice of wire gauge depends on the current and voltage requirements of your circuit. As a general rule, use a wire gauge that can handle at least 25% more current than the maximum expected current in your circuit. Consult a wire gauge chart or calculator to determine the appropriate gauge based on the wire material, insulation type, and length. -
Can I mix through-hole and surface-mount components on the same PCB?
Yes, you can mix through-hole and surface-mount components on the same PCB, as long as you provide the appropriate pads and holes for each type of component. This is known as a hybrid PCB. However, mixing component types can make the assembly process more complex and time-consuming, so it is generally recommended to stick to one type of component whenever possible. -
How do I remove a soldered component from a PCB?
To remove a soldered component from a PCB, first heat up the solder joints with a soldering iron to melt the solder. Then, use a pair of tweezers or pliers to gently pull the component away from the board while keeping the heat on the joints. If the component is stuck, you can use a desoldering wick or a solder sucker to remove the excess solder before pulling the component. Be careful not to damage the PCB or the surrounding components during the removal process. -
What is the purpose of flux in PCB wiring?
Flux is a chemical agent used in PCB wiring to promote the flow of solder and prevent oxidation of the metals being soldered. Flux removes any dirt, grease, or oxidation from the surface of the metals and allows the solder to bond more easily and evenly. Flux comes in various forms, such as paste, liquid, or core, and can be applied manually or automatically. After soldering, any residual flux must be cleaned from the PCB to prevent corrosion and contamination.
Conclusion
PCB wiring is a critical skill for anyone involved in electronics design and manufacturing. By understanding the tools, techniques, best practices, and troubleshooting methods for PCB wiring, you can create reliable, high-quality PCBs that meet your specific needs and requirements. Whether you are a hobbyist or a professional, investing time and effort into learning and mastering PCB wiring will pay off in the long run and enable you to bring your electronic ideas to life. So grab your soldering iron and start wiring!
Leave a Reply