Introduction to PCB Hacks
Printed Circuit Boards (PCBs) are the backbone of modern electronics. They provide a platform for components to be mounted and connected, allowing for complex circuits to be designed and manufactured efficiently. However, designing and working with PCBs can be challenging, especially for beginners. In this article, we will explore some tips and tricks to help you improve your PCB design skills and overcome common obstacles. These #PCBHacks will cover various aspects of PCB design, from component placement to signal integrity, and will help you create more reliable and efficient PCBs.
Understanding the Basics of PCB Design
Before diving into specific #PCBHacks, it’s essential to understand the fundamentals of PCB design. A PCB consists of a non-conductive substrate, typically made of fiberglass or other composite materials, with conductive copper traces printed on one or both sides. Components are mounted on the PCB and connected through these traces, forming a complete circuit.
PCB Layers
PCBs can have multiple layers, depending on the complexity of the circuit and the space constraints. The most common PCB configurations are:
Layers | Description |
---|---|
Single-sided | Components and traces on one side only |
Double-sided | Components and traces on both sides |
Multi-layer | Additional conductive layers sandwiched between the top and bottom layers |
PCB Design Software
To design a PCB, you’ll need to use specialized software. Some popular PCB design software options include:
- KiCad (open-source)
- Eagle (free for non-commercial use)
- Altium Designer (paid)
- OrCAD (paid)
These software packages allow you to create schematic diagrams, design PCB layouts, and generate manufacturing files.
#PCBHacks for Component Placement
Proper component placement is crucial for ensuring the functionality, reliability, and manufacturability of your PCB. Here are some tips to help you optimize your component placement:
Keep Components Close Together
Minimizing the distance between related components can help reduce signal integrity issues and improve overall performance. When placing components, consider their logical connections and group them accordingly.
Use a Grid System
Aligning components to a grid can make your PCB layout more organized and easier to route. Most PCB design software allows you to set up a grid and snap components to it.
Consider Component Orientation
Orient components in a way that minimizes the crossing of traces and allows for efficient routing. For example, placing ICs with their pins facing the same direction can simplify trace routing.
Leave Space for Connectors
Ensure that there is adequate space around connectors for mating cables or plugs. Consult the connector’s datasheet for recommended clearances.
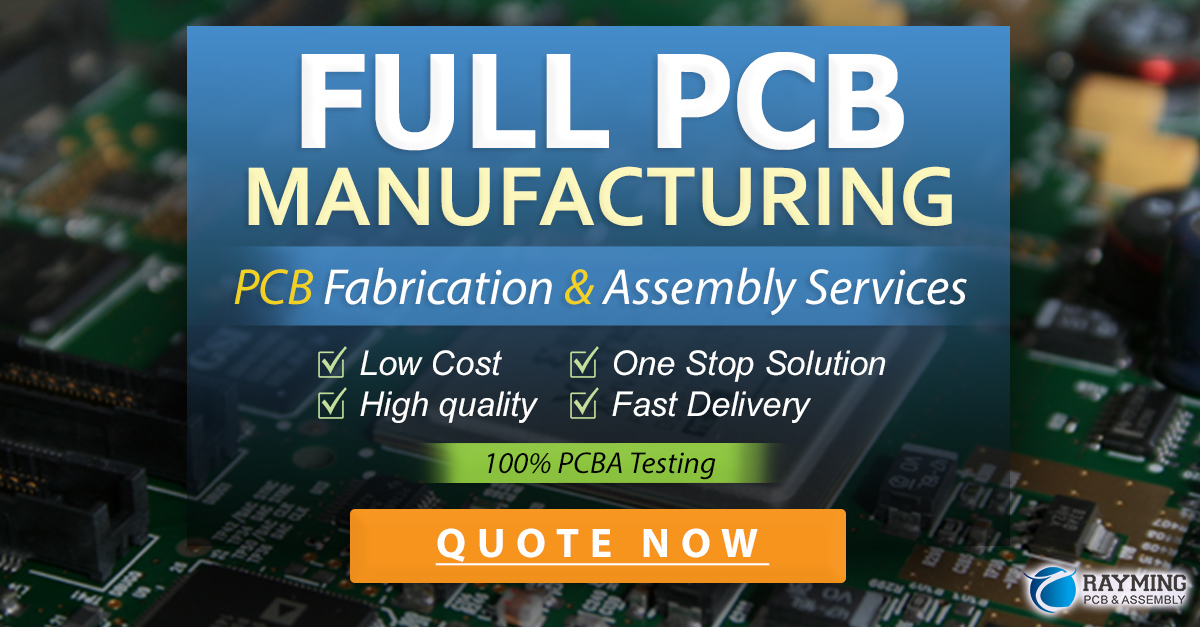
#PCBHacks for Trace Routing
Routing traces on a PCB can be a time-consuming and challenging task. These tips will help you create efficient and reliable trace routes:
Use Appropriate Trace Widths
The width of a trace determines its current-carrying capacity and resistance. Use wider traces for power lines and high-current signals, and narrower traces for low-current signals. Consult a trace width calculator or your PCB manufacturer’s specifications to determine the appropriate widths.
Minimize Trace Lengths
Shorter traces have lower resistance and are less susceptible to noise and interference. When routing traces, take the most direct path possible between components.
Avoid Sharp Angles
Sharp angles in traces can cause signal reflections and increase electromagnetic interference (EMI). Use 45-degree angles or curved traces instead of 90-degree angles.
Use Vias Strategically
Vias are used to connect traces on different layers of a multi-layer PCB. Place vias strategically to minimize their impact on signal integrity and to avoid blocking other traces.
#PCBHacks for Signal Integrity
Signal integrity is essential for ensuring that your PCB functions as intended. Poor signal integrity can lead to issues such as crosstalk, electromagnetic interference, and signal distortion. Here are some tips to help you maintain good signal integrity:
Use Ground Planes
A ground plane is a large area of copper on a PCB layer that is connected to the ground. Ground planes help to reduce EMI and provide a low-impedance return path for signals. They also help to distribute heat and improve mechanical stability.
Decouple Power Lines
Decoupling capacitors help to smooth out voltage fluctuations on power lines and reduce high-frequency noise. Place decoupling capacitors close to the power pins of ICs and other components.
Separate Analog and Digital Signals
Analog and digital signals have different requirements for signal integrity. Keep analog and digital signals separated on your PCB to minimize interference. Use separate ground planes for analog and digital sections if possible.
Terminate High-Speed Signals
High-speed signals, such as those used in communication protocols like USB or Ethernet, require proper termination to prevent reflections and maintain signal integrity. Use appropriate termination resistors or other techniques as specified in the relevant standards.
#PCBHacks for Manufacturing
Designing a PCB that can be manufactured efficiently and reliably is just as important as creating a functional circuit. These tips will help you optimize your PCB design for manufacturing:
Follow Design Rules
PCB manufacturers have specific design rules that dictate minimum trace widths, clearances, and other parameters. Familiarize yourself with these rules and ensure that your PCB design adheres to them.
Use Standard Components
Using standard, readily-available components can help reduce manufacturing costs and lead times. Avoid using obscure or custom components unless absolutely necessary.
Provide Clear Silkscreen Labels
Silkscreen labels help to identify components and provide assembly instructions. Ensure that your silkscreen labels are clear, legible, and do not overlap with pads or other features.
Include Fiducial Marks
Fiducial marks are small, circular pads used by automated assembly machines to align the PCB and place components accurately. Include at least three fiducial marks on your PCB, preferably near the corners.
Frequently Asked Questions (FAQ)
- What is the difference between a schematic and a PCB layout?
-
A schematic is a symbolic representation of a circuit, showing the components and their connections. A PCB layout is the physical design of the PCB, showing the actual placement of components and routing of traces.
-
How do I choose the right PCB thickness?
-
The choice of PCB thickness depends on factors such as the number of layers, the size and weight of components, and the mechanical requirements of the application. Common PCB thicknesses range from 0.8mm to 1.6mm. Consult with your PCB manufacturer for guidance on selecting the appropriate thickness for your design.
-
What is the difference between through-hole and surface-mount components?
-
Through-hole components have leads that are inserted into holes drilled in the PCB and soldered on the opposite side. Surface-mount components are mounted directly on the surface of the PCB and soldered in place. Surface-mount components are generally smaller and allow for higher component density, while through-hole components are more robust and easier to hand-solder.
-
How do I select the right copper weight for my PCB?
-
Copper weight refers to the thickness of the copper layer on a PCB, typically measured in ounces per square foot (oz/ft²). Higher copper weights can carry more current and provide better heat dissipation, but they also increase the cost and weight of the PCB. Common copper weights are 1oz/ft² and 2oz/ft². Choose the copper weight based on the current requirements and thermal considerations of your design.
-
What are the advantages of using a four-layer PCB over a two-layer PCB?
- Four-layer PCBs have two additional conductive layers compared to two-layer PCBs. The main advantages of using a four-layer PCB include better signal integrity, reduced EMI, and improved power distribution. Four-layer PCBs also allow for more complex routing and higher component density. However, they are more expensive to manufacture than two-layer PCBs.
Conclusion
Designing and working with PCBs can be a challenging but rewarding experience. By applying the #PCBHacks discussed in this article, you can improve your PCB design skills, create more reliable and efficient circuits, and optimize your designs for manufacturing. Remember to keep learning and experimenting, as there is always room for improvement in the world of PCB design.
Leave a Reply