Understanding PCB Thermal Resistance
Printed Circuit Boards (PCBs) are essential components in modern electronic devices, serving as the foundation for mounting and interconnecting various electronic components. One crucial aspect of PCB design is its ability to dissipate heat generated by these components, which is quantified by the PCB’s thermal resistance. In this article, we will delve into the concept of PCB thermal resistance, its importance, factors influencing it, and strategies to optimize heat dissipation in PCB designs.
What is PCB Thermal Resistance?
PCB thermal resistance is a measure of a circuit board’s ability to transfer heat from its heat sources (electronic components) to the surrounding environment. It is expressed in units of degrees Celsius per watt (°C/W) and represents the temperature difference between the heat source and the ambient environment per unit of power dissipated.
A lower thermal resistance indicates that the PCB is more effective at dissipating heat, while a higher thermal resistance suggests that the PCB may struggle to remove heat efficiently, potentially leading to component overheating and reduced reliability.
The Importance of PCB Thermal Management
Effective thermal management is crucial for the proper functioning and longevity of electronic devices. When electronic components generate heat during operation, it must be efficiently dissipated to prevent overheating, which can lead to several issues:
- Component degradation: Excessive heat can cause components to deteriorate faster, reducing their lifespan and reliability.
- Performance degradation: Overheating can negatively impact the performance of electronic components, leading to reduced efficiency and potential malfunctions.
- Safety concerns: In extreme cases, overheating can pose safety risks, such as fire hazards or burns to users.
By minimizing the PCB’s thermal resistance and implementing proper thermal management techniques, designers can ensure that the electronic devices operate within their specified temperature ranges, enhancing reliability and performance.
Factors Influencing PCB Thermal Resistance
Several factors contribute to a PCB’s thermal resistance, including:
PCB Material Properties
The choice of PCB material significantly impacts its thermal resistance. Common PCB materials include:
- FR-4: A glass-reinforced epoxy laminate, FR-4 is the most widely used PCB material. It has a relatively high thermal resistance compared to other materials.
- Metal Core PCBs (MCPCBs): These PCBs feature a metal core, typically aluminum, which offers excellent thermal conductivity and helps dissipate heat more efficiently than FR-4.
- Ceramic PCBs: Ceramic materials, such as aluminum nitride (AlN) and alumina (Al2O3), provide excellent thermal conductivity and are suitable for high-temperature applications.
The thermal conductivity of the PCB material directly influences its ability to transfer heat from the heat sources to the environment. Higher thermal conductivity materials, like MCPCBs and ceramic PCBs, result in lower thermal resistance and improved heat dissipation.
Copper Thickness and Distribution
The thickness and distribution of copper on the PCB also play a vital role in thermal management. Copper is an excellent thermal conductor, and increasing its thickness can enhance heat spreading and reduce thermal resistance. Additionally, strategically placing copper layers or using copper pours in areas with high heat generation can further improve heat dissipation.
PCB Layer Stack-up
The number and arrangement of layers in a PCB stack-up can influence its thermal resistance. Multi-layer PCBs with dedicated ground planes and power planes can help spread heat more evenly across the board, reducing hot spots and improving overall thermal performance.
Component Placement and Density
The placement and density of components on a PCB can significantly impact its thermal resistance. Placing high-power components too close together can create localized hot spots, making it difficult for the PCB to dissipate heat effectively. Designers should consider the heat generation characteristics of each component and strategically place them to minimize thermal interactions and optimize heat dissipation.
Strategies for Optimizing PCB Thermal Resistance
To improve a PCB’s thermal performance and reduce its thermal resistance, designers can employ various strategies:
Thermal Vias
Thermal vias are small, plated holes drilled through the PCB to transfer heat from one layer to another. By strategically placing thermal vias near high-power components or hot spots, designers can create efficient heat conduction paths, allowing heat to be dissipated through the PCB’s layers and to the external environment.
Heat Sinks and Thermal Interface Materials
Heat sinks are passive cooling devices that can be attached to high-power components or mounted on the PCB to enhance heat dissipation. They work by increasing the surface area available for heat transfer and promoting convective cooling. Thermal interface materials (TIMs), such as thermal pads or thermal paste, are used to improve the thermal contact between components and heat sinks, minimizing air gaps and ensuring efficient heat transfer.
Thermal Planes
Thermal planes are dedicated copper layers within the PCB stack-up that are designed to spread heat evenly across the board. These planes can be connected to thermal vias and heat sinks to provide a low-resistance path for heat dissipation. By incorporating thermal planes, designers can effectively distribute heat and reduce hot spots on the PCB.
Airflow and Cooling Solutions
Adequate airflow is essential for effective heat dissipation. Designers should consider the enclosure design and ensure that there are sufficient ventilation openings to allow air to circulate freely around the PCB. In some cases, active cooling solutions, such as fans or heat pipes, may be necessary to maintain proper operating temperatures.
Thermal Simulation and Analysis
Thermal simulation and analysis tools can help designers predict and optimize the thermal performance of PCBs before fabrication. These tools use computational fluid dynamics (CFD) and finite element analysis (FEA) to model heat transfer and identify potential thermal issues. By conducting thermal simulations, designers can iterate on their designs, evaluate different materials and layouts, and make informed decisions to minimize thermal resistance.
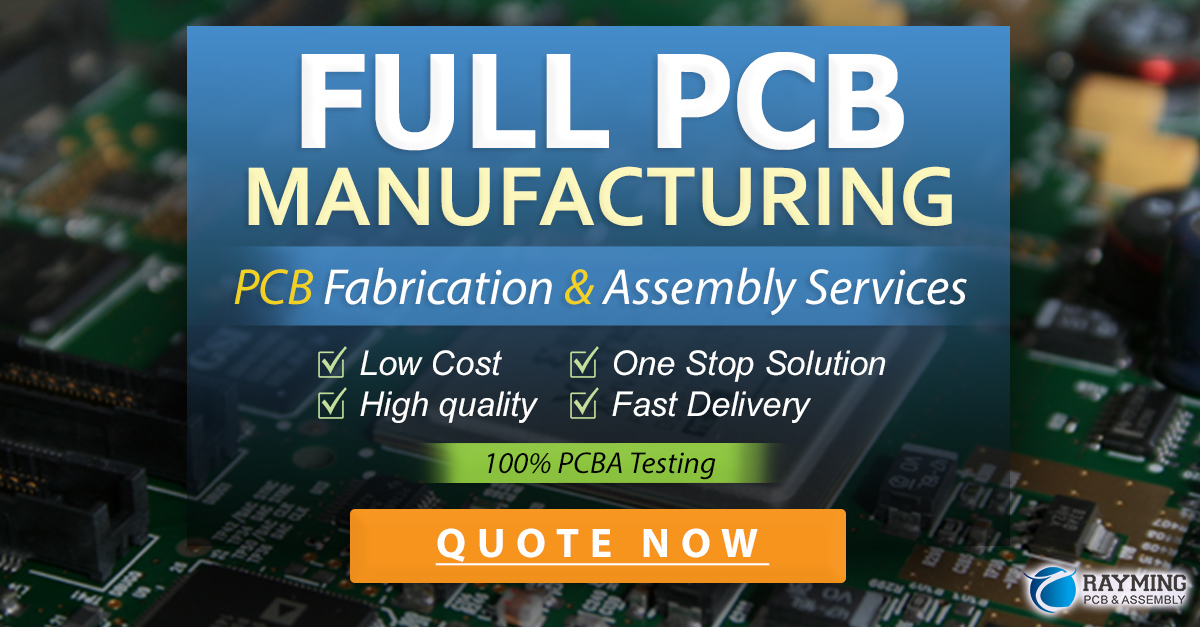
PCB Thermal Resistance Measurement Techniques
Measuring the thermal resistance of a PCB is crucial for validating the effectiveness of thermal management strategies and ensuring that the board operates within its specified temperature limits. Several techniques can be used to measure PCB thermal resistance:
Thermocouples
Thermocouples are temperature sensors that consist of two dissimilar metals joined together at one end. By attaching thermocouples to specific locations on the PCB and measuring the temperature difference between the hot spot and the ambient environment, designers can calculate the thermal resistance using the following formula:
Thermal Resistance = (Thot spot - Tambient) / Power Dissipated
Infrared Thermography
Infrared (IR) thermography is a non-contact method that uses an IR camera to capture thermal images of the PCB. These images provide a visual representation of the temperature distribution across the board, allowing designers to identify hot spots and assess the effectiveness of thermal management solutions. IR thermography is particularly useful for detecting localized heating issues and evaluating the overall thermal performance of the PCB.
Thermal Test Vehicles (TTVs)
Thermal test vehicles (TTVs) are specially designed PCBs that mimic the thermal characteristics of the actual product. TTVs are populated with components that generate heat similar to the final application, and they are equipped with temperature sensors to measure the thermal resistance. By testing TTVs under various operating conditions, designers can validate the thermal performance of the PCB design and make necessary adjustments before finalizing the product.
PCB Thermal Resistance Standards and Guidelines
To ensure the reliability and performance of electronic devices, several standards and guidelines have been established to address PCB thermal resistance and thermal management:
- IPC-2221: Generic Standard on Printed Board Design
- Provides guidelines for PCB design, including thermal management considerations.
- IPC-2152: Standard for Determining Current-Carrying Capacity in Printed Board Design
- Offers guidance on calculating current-carrying capacity and managing thermal issues in PCBs.
- JEDEC JC-15: Thermal Standards
- Defines standards for thermal characterization, measurement, and reporting of semiconductor packages and PCBs.
By adhering to these standards and guidelines, designers can ensure that their PCB designs meet industry best practices for thermal management and reliability.
Frequently Asked Questions (FAQ)
-
Q: What is the difference between thermal conductivity and thermal resistance?
A: Thermal conductivity is a material property that measures a substance’s ability to conduct heat, while thermal resistance is a measure of a system’s (e.g., a PCB’s) ability to resist heat flow. Thermal conductivity is an intrinsic property of the material, whereas thermal resistance depends on the material properties, geometry, and heat transfer mechanisms of the system. -
Q: How does PCB thickness affect thermal resistance?
A: In general, thicker PCBs have lower thermal resistance compared to thinner PCBs. This is because a thicker PCB provides more cross-sectional area for heat conduction, allowing heat to spread more easily through the layers. However, increasing PCB thickness also increases the overall weight and cost of the board, so designers must find a balance between thermal performance and other design constraints. -
Q: Can solder mask color affect PCB thermal resistance?
A: Yes, the color of the solder mask can have a minor effect on the PCB’s thermal resistance. Darker colors, such as black or dark green, have a higher emissivity, which means they are better at radiating heat compared to lighter colors. However, the impact of solder mask color on thermal resistance is relatively small compared to other factors like PCB material, copper thickness, and thermal management techniques. -
Q: What is the role of thermal interface materials (TIMs) in reducing PCB thermal resistance?
A: Thermal interface materials (TIMs) are used to fill the air gaps between components and heat sinks or between a PCB and its enclosure. By eliminating these air gaps, TIMs improve the thermal contact and facilitate better heat transfer from the heat source to the heat sink or enclosure. This, in turn, helps reduce the overall thermal resistance of the PCB assembly. -
Q: How can designers address thermal issues in high-density PCB layouts?
A: In high-density PCB layouts, designers can address thermal issues by: - Using thermal vias to transfer heat through the layers
- Increasing copper thickness in high-power areas
- Strategically placing components to minimize thermal interactions
- Incorporating thermal planes to spread heat evenly
- Using advanced PCB materials with higher thermal conductivity
- Implementing active cooling solutions, such as fans or heat pipes, when necessary
Conclusion
PCB thermal resistance is a critical aspect of electronic design, as it directly impacts the reliability, performance, and safety of electronic devices. By understanding the factors that influence thermal resistance and employing appropriate thermal management strategies, designers can create PCBs that effectively dissipate heat and maintain optimal operating temperatures.
Through careful material selection, strategic component placement, and the use of thermal vias, heat sinks, and thermal planes, designers can minimize thermal resistance and ensure the long-term reliability of their products. Additionally, thermal simulation and analysis tools, along with adherence to industry standards and guidelines, can help validate and optimize PCB designs for optimal thermal performance.
As electronic devices continue to become more compact and powerful, effective thermal management will remain a key challenge for PCB designers. By staying up-to-date with the latest techniques and technologies in PCB thermal management, designers can create robust, reliable, and thermally efficient electronic products that meet the demands of today’s increasingly complex applications.
Leave a Reply