Introduction to PCB Temperature
Printed circuit boards (PCBs) are essential components in most modern electronic devices. They provide the foundation for mounting and interconnecting various electronic components. However, one critical factor that can significantly impact the performance and reliability of PCBs is temperature. High temperatures can lead to a range of issues, such as component failure, reduced lifespan, and decreased overall system performance.
In this comprehensive guide, we will explore PCB temperature in depth. We will discuss the causes of high temperatures, the effects they can have on PCBs, and various strategies for managing and mitigating these issues. By understanding PCB temperature and implementing appropriate thermal management techniques, designers and engineers can ensure the optimal performance and longevity of their electronic devices.
Causes of High PCB Temperatures
Several factors can contribute to high temperatures on PCBs. Let’s examine some of the primary causes:
Power Dissipation
One of the main sources of heat generation on PCBs is power dissipation. As electronic components operate, they consume power and generate heat as a byproduct. The amount of heat generated depends on factors such as the component’s power rating, efficiency, and operating conditions. High-power components, such as processors, power regulators, and RF modules, are particularly prone to generating significant amounts of heat.
Current Density
Current density refers to the amount of electrical current flowing through a given cross-sectional area of a conductor, such as a PCB trace or via. When current density exceeds certain thresholds, it can lead to excessive heat generation due to the resistance of the conductor. This phenomenon is known as Joule heating. High current density can occur when traces are undersized, vias are inadequate, or when there is a high concentration of current-carrying traces in a specific area of the PCB.
Environmental Factors
The environment in which a PCB operates can also contribute to high temperatures. Factors such as ambient temperature, airflow, and enclosure design can all impact the thermal performance of a PCB. If a device is operating in a high-temperature environment or lacks proper ventilation, it can exacerbate the heat generation and accumulation on the PCB.
Component Placement
The placement of components on a PCB can significantly influence temperature distribution. When heat-generating components are placed close together or near thermally sensitive components, it can lead to localized hot spots and thermal challenges. Proper component placement and spacing are crucial for effective heat dissipation and temperature management.
Effects of High PCB Temperatures
High temperatures on PCBs can have various detrimental effects on the performance and reliability of electronic devices. Let’s explore some of the key consequences:
Component Failure
Excessive heat can cause components to fail prematurely. Many electronic components have specified operating temperature ranges, and exposure to temperatures beyond these limits can lead to degradation and failure. High temperatures can cause component packages to crack, solder joints to fail, and internal component structures to degrade. These failures can result in reduced reliability, intermittent operation, or complete device failure.
Reduced Lifespan
Even if components do not fail immediately due to high temperatures, prolonged exposure to elevated temperatures can significantly reduce their lifespan. The rate of chemical reactions and material degradation increases with temperature, leading to accelerated aging of components. This can result in shorter overall device lifespan and increased maintenance or replacement costs.
Performance Degradation
High temperatures can also impact the performance of electronic components. Many components, such as processors and power regulators, have temperature-dependent characteristics. As temperature increases, their efficiency, speed, and accuracy may degrade. This can lead to reduced system performance, increased power consumption, and potential instability.
PCB Material Degradation
PCBs themselves can also suffer from the effects of high temperatures. The materials used in PCB fabrication, such as the substrate, solder mask, and copper traces, have specific thermal tolerances. Exposure to excessive heat can cause delamination, warping, or degradation of the PCB materials. This can compromise the structural integrity of the PCB and lead to reliability issues.
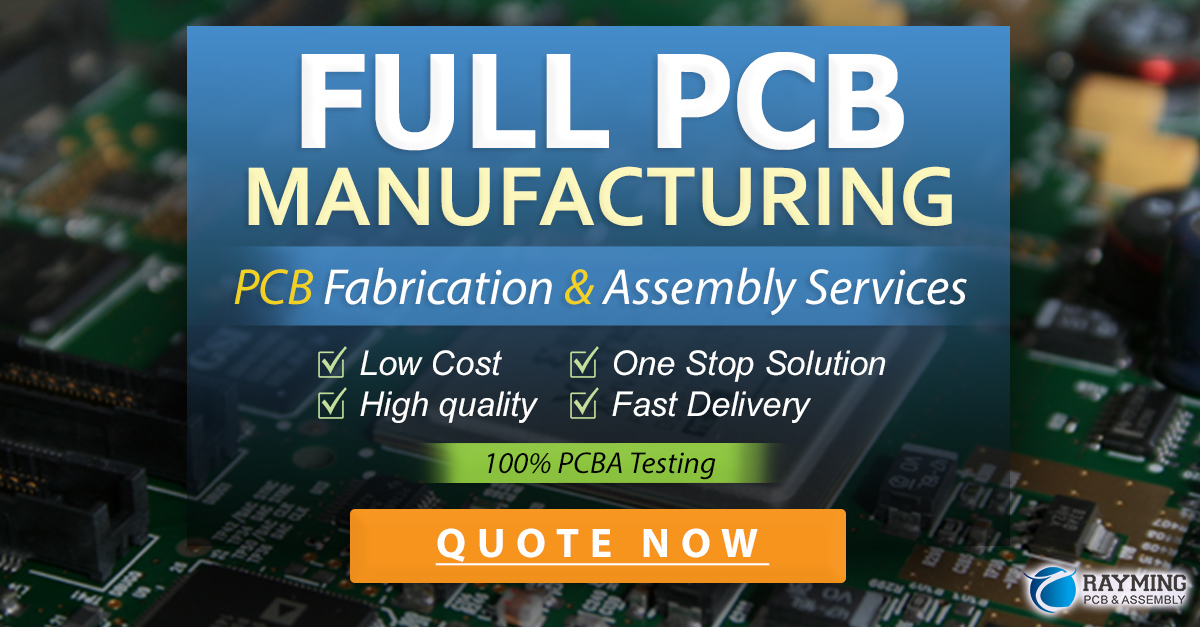
Thermal Management Techniques for PCBs
To mitigate the effects of high temperatures and ensure optimal performance of PCBs, various thermal management techniques can be employed. Let’s explore some effective strategies:
Proper Component Selection
Selecting components with appropriate thermal characteristics is crucial for managing PCB temperature. When choosing components, consider their power dissipation, thermal resistance, and maximum operating temperature. Opt for components with lower power dissipation and higher thermal efficiency whenever possible. Additionally, consider using components with enhanced thermal packages, such as those with exposed pads or heat spreaders, to facilitate heat dissipation.
Optimized PCB Layout
The layout of a PCB plays a significant role in thermal management. When designing the PCB, consider the following layout techniques:
- Provide adequate spacing between high-power components to reduce thermal coupling and allow for better heat dissipation.
- Use wide and thick traces for high-current paths to minimize current density and reduce Joule heating.
- Incorporate sufficient copper pour and ground planes to distribute heat evenly across the PCB.
- Place temperature-sensitive components away from heat-generating components to minimize thermal impact.
- Utilize thermal vias to transfer heat from components to other layers or to a heatsink.
Heatsinks and Thermal Interface Materials
Heatsinks are effective tools for dissipating heat away from components and the PCB. They work by providing a large surface area for heat to be conducted away from the heat source and then dissipated into the surrounding environment. When using heatsinks, ensure proper thermal contact between the component and the heatsink using thermal interface materials (TIMs) such as thermal pads, pastes, or adhesives. TIMs fill the microscopic gaps between the surfaces, enhancing heat transfer efficiency.
Fans and Active Cooling
In some cases, passive cooling through heatsinks may not be sufficient, and active cooling methods like fans may be necessary. Fans create airflow over the PCB and components, enhancing convective heat transfer and reducing overall temperatures. When incorporating fans, consider factors such as fan size, placement, and airflow direction to optimize cooling performance. Additionally, ensure that the enclosure design allows for proper airflow and ventilation.
Thermal Simulation and Analysis
Thermal simulation and analysis tools can be valuable in predicting and optimizing the thermal performance of PCBs. These tools allow designers to model the heat distribution, identify potential hot spots, and evaluate the effectiveness of various thermal management strategies. By performing thermal simulations early in the design process, designers can make informed decisions and iterate on the design to achieve optimal thermal performance.
PCB Temperature Monitoring and Control
Monitoring and controlling PCB temperature is essential for ensuring reliable operation and preventing thermal-related issues. Let’s explore some techniques for temperature monitoring and control:
Temperature Sensors
Incorporating temperature sensors on the PCB allows for real-time monitoring of temperatures at critical locations. Common types of temperature sensors include thermistors, resistance temperature detectors (RTDs), and digital temperature sensors. Place sensors near high-power components, thermally sensitive areas, or any locations where temperature monitoring is crucial. The sensor data can be used for thermal management, fault detection, or triggering cooling mechanisms.
Thermal Throttling
Thermal throttling is a technique used to dynamically adjust the performance of components based on their temperature. When a component reaches a certain temperature threshold, its operating frequency or power consumption can be reduced to prevent overheating. This is commonly used in processors and power management ICs. Implementing thermal throttling requires a combination of temperature sensing, control algorithms, and communication between the component and the system.
Thermal Shutdown
In extreme cases where temperatures exceed safe limits, thermal shutdown mechanisms can be implemented to protect the PCB and components from damage. Thermal shutdown circuits monitor the temperature and trigger a shutdown or power-off sequence when a critical temperature threshold is reached. This prevents catastrophic failures and ensures the safety of the device and its users.
PCB Temperature Testing and Validation
Proper testing and validation of PCB temperature performance are essential to ensure the reliability and longevity of electronic devices. Let’s discuss some key aspects of temperature testing:
Thermal Chamber Testing
Thermal chamber testing involves subjecting the PCB and device to controlled temperature and humidity conditions. By placing the device in a thermal chamber, designers can evaluate its performance and reliability under various environmental conditions. Thermal chambers can simulate extreme temperatures, temperature cycling, and humidity levels to assess the device’s ability to withstand these conditions.
Thermal Imaging
Thermal imaging, also known as infrared imaging, is a non-contact method for visualizing the temperature distribution on a PCB. Thermal cameras capture the infrared radiation emitted by the PCB and create a temperature map of the surface. This allows designers to identify hot spots, thermal gradients, and areas of concern. Thermal imaging is particularly useful for locating hidden thermal issues and optimizing component placement and cooling strategies.
Accelerated Life Testing
Accelerated life testing involves subjecting the PCB and components to elevated temperatures and stress conditions to simulate the effects of long-term aging and degradation. By exposing the device to accelerated conditions, designers can predict the expected lifespan and identify potential failure modes. This helps in assessing the reliability and durability of the device under real-world operating conditions.
FAQ
What is the optimal operating temperature range for PCBs?
The optimal operating temperature range for PCBs depends on various factors, including the specific components used, the PCB material, and the application requirements. Generally, most PCBs and components are designed to operate reliably within a temperature range of -40°C to +85°C. However, some specialized components and applications may have different temperature ranges. It’s essential to refer to the manufacturer’s specifications and datasheets for the specific temperature ratings of the components and PCB materials used.
How can I identify potential thermal issues on my PCB?
There are several methods to identify potential thermal issues on a PCB:
- Thermal simulation: Use thermal simulation software to model the heat distribution and identify hot spots during the design phase.
- Thermal imaging: Perform thermal imaging of the PCB under operating conditions to visualize the temperature distribution and locate areas of concern.
- Temperature monitoring: Place temperature sensors at critical locations on the PCB to monitor temperatures during operation and detect any abnormal temperature rises.
- Visual inspection: Visually inspect the PCB for signs of overheating, such as discoloration, charring, or component damage.
What are some common causes of component overheating on PCBs?
Common causes of component overheating on PCBs include:
- Insufficient heat dissipation: Lack of proper heatsinks, thermal interface materials, or cooling mechanisms can lead to heat buildup.
- High power dissipation: Components with high power consumption generate more heat and require adequate thermal management.
- Overcurrent or overvoltage conditions: Excessive current or voltage applied to components can cause increased heat generation.
- Poor PCB layout: Improper component placement, insufficient spacing, or inadequate trace sizing can contribute to localized heating.
- Environmental factors: High ambient temperatures, lack of airflow, or inadequate ventilation can exacerbate component overheating.
How often should I perform temperature testing on my PCBs?
The frequency of temperature testing depends on the specific application, reliability requirements, and development stage of the PCB. Generally, it is recommended to perform temperature testing at various stages:
- During the prototype phase: Conduct thorough temperature testing to validate the thermal design and identify any issues early on.
- Before mass production: Perform temperature testing on pre-production samples to ensure the PCB meets the specified thermal requirements.
- During qualification testing: Include temperature testing as part of the overall qualification process to assess the PCB’s reliability and durability.
- Periodic testing during production: Implement periodic temperature testing on a sample basis to monitor the consistency and quality of the manufactured PCBs.
Can high PCB temperatures cause safety hazards?
Yes, high PCB temperatures can potentially cause safety hazards. Excessive temperatures can lead to several risks:
- Fire hazard: If temperatures exceed the ignition point of materials or cause components to fail catastrophically, it can result in a fire hazard.
- Burns and injury: Touching or handling a PCB with excessively high temperatures can cause burns or injuries to users or technicians.
- Exploding batteries: In devices with batteries, high temperatures can cause the batteries to overheat, swell, or even explode, posing a significant safety risk.
- Emission of toxic fumes: Overheated PCBs or components can release toxic fumes or gases, which can be harmful if inhaled.
It is crucial to implement proper thermal management techniques, safety features, and adhere to relevant safety standards to mitigate these risks and ensure the safe operation of electronic devices.
Conclusion
Managing PCB temperature is a critical aspect of designing and manufacturing reliable and high-performance electronic devices. High temperatures can lead to component failure, reduced lifespan, and decreased system performance. By understanding the causes and effects of high PCB temperatures, designers can employ various thermal management techniques to mitigate these issues.
From proper component selection and optimized PCB layout to the use of heatsinks, fans, and active cooling, there are numerous strategies available to manage PCB temperature effectively. Additionally, incorporating temperature monitoring and control mechanisms, such as sensors, thermal throttling, and shutdown, further enhances the thermal reliability of the system.
Thorough testing and validation, including thermal chamber testing, thermal imaging, and accelerated life testing, are essential to ensure the PCB meets the desired temperature specifications and can withstand real-world operating conditions.
By following the guidelines and best practices outlined in this guide, designers and engineers can effectively manage PCB temperature, improving the reliability, performance, and longevity of their electronic devices. As technology advances and power densities continue to increase, thermal management will remain a critical consideration in PCB design and manufacturing.
Leave a Reply