Introduction
Printed Circuit Boards (PCBs) are the backbone of modern electronics, providing a platform for interconnecting various components and enabling complex circuitry. The copper layer on a PCB serves as the conductive pathway for electrical signals, but it is susceptible to oxidation and corrosion. To protect the copper layer and enhance the PCB’s performance, a surface finish is applied. One such surface finish is the Intermetallic Layer, which forms a protective barrier and improves the solderability of the PCB.
In this article, we will explore the concept of intermetallic layers in PCB surface finishes, their importance, and the various types of finishes available. We will also discuss the advantages and disadvantages of each surface finish and provide guidelines for selecting the appropriate finish for specific applications.
What is an Intermetallic Layer?
An intermetallic layer is a thin film that forms at the interface between two dissimilar metals when they are in contact and subjected to heat or pressure. In the context of PCB surface finishes, an intermetallic layer is created between the copper layer and the applied surface finish material. This layer serves several purposes:
-
Protection: The intermetallic layer acts as a barrier, preventing oxidation and corrosion of the underlying copper layer. It helps maintain the integrity of the copper traces and pads, ensuring reliable electrical connections.
-
Solderability: The intermetallic layer promotes better wetting and bonding of solder to the PCB surface. It enhances the ability of molten solder to flow and adhere to the copper, resulting in stronger and more reliable solder joints.
-
Durability: The intermetallic layer provides mechanical strength and stability to the PCB surface. It helps prevent wear and tear, especially during handling and assembly processes.
Types of PCB Surface Finishes
There are several types of PCB surface finishes available, each with its own characteristics and benefits. Let’s explore some of the most common surface finishes:
1. Hot Air Solder Leveling (HASL)
HASL is one of the oldest and most widely used surface finishes in the PCB industry. In this process, the PCB is dipped into a molten solder bath, and then hot air is used to level the solder on the surface. The solder forms an intermetallic layer with the copper, providing protection and improved solderability.
Advantages:
– Cost-effective
– Good solderability
– Suitable for through-hole components
Disadvantages:
– Uneven surface due to solder buildup
– Limited flatness, affecting fine-pitch components
– Thermal shock during the HASL process
2. Electroless Nickel Immersion Gold (ENIG)
ENIG is a popular choice for high-reliability applications. In this process, a layer of nickel is deposited on the copper surface through an electroless plating process, followed by a thin layer of gold. The nickel forms an intermetallic layer with the copper, while the gold provides oxidation resistance and enhanced solderability.
Advantages:
– Excellent flatness and coplanarity
– Good oxidation resistance
– Suitable for fine-pitch components
Disadvantages:
– Higher cost compared to HASL
– Potential for “black pad” defect due to nickel corrosion
– Shelf life limitations
3. Immersion Silver (ImAg)
Immersion silver is a cost-effective alternative to ENIG. In this process, a thin layer of silver is deposited directly on the copper surface through an immersion process. The silver forms an intermetallic layer with the copper, providing protection and good solderability.
Advantages:
– Cost-effective compared to ENIG
– Good solderability
– Suitable for fine-pitch components
Disadvantages:
– Limited shelf life due to silver tarnishing
– Potential for silver migration, causing short circuits
4. Organic Solderability Preservative (OSP)
OSP is a non-metallic surface finish that involves applying an organic compound to the copper surface. The organic layer acts as a protective barrier against oxidation and enhances solderability.
Advantages:
– Cost-effective
– Excellent solderability
– Suitable for fine-pitch components
– Environmentally friendly
Disadvantages:
– Limited shelf life
– Susceptible to handling damage
– Not suitable for multiple reflow cycles
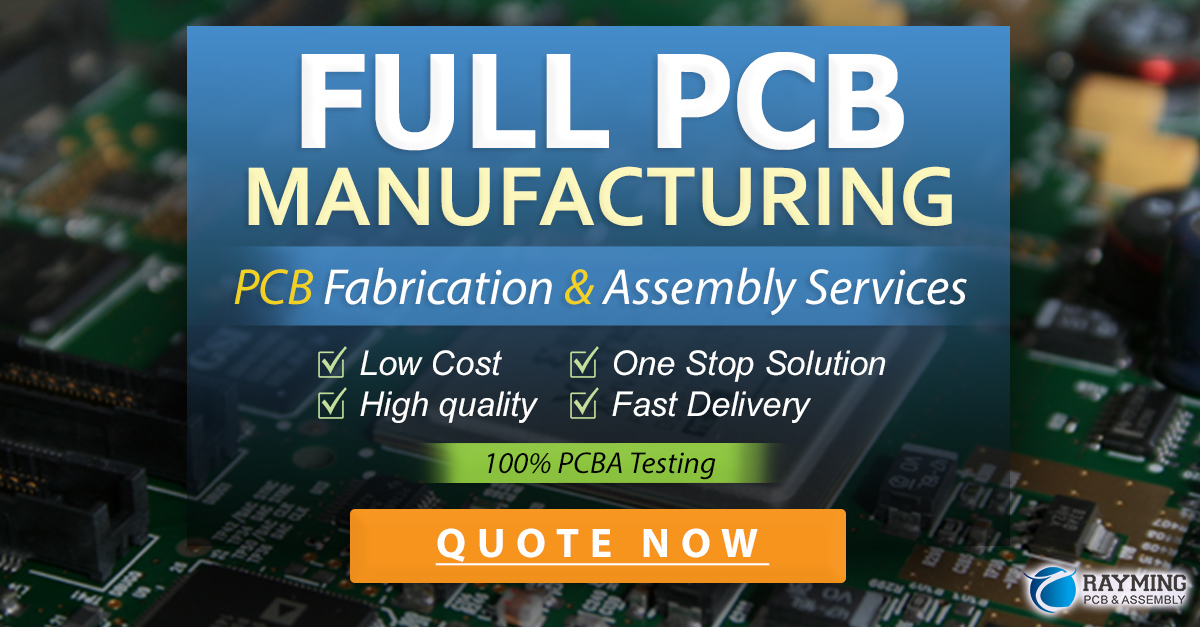
Comparison of Surface Finishes
Surface Finish | Advantages | Disadvantages |
---|---|---|
HASL | – Cost-effective – Good solderability – Suitable for through-hole components |
– Uneven surface – Limited flatness – Thermal shock during process |
ENIG | – Excellent flatness and coplanarity – Good oxidation resistance – Suitable for fine-pitch components |
– Higher cost – Potential for “black pad” defect – Shelf life limitations |
ImAg | – Cost-effective compared to ENIG – Good solderability – Suitable for fine-pitch components |
– Limited shelf life – Potential for silver migration |
OSP | – Cost-effective – Excellent solderability – Suitable for fine-pitch components – Environmentally friendly |
– Limited shelf life – Susceptible to handling damage – Not suitable for multiple reflow cycles |
Selecting the Appropriate Surface Finish
When choosing a surface finish for a PCB, several factors should be considered:
-
Application requirements: Consider the specific needs of the application, such as environmental conditions, reliability expectations, and signal integrity requirements.
-
Component compatibility: Ensure that the selected surface finish is compatible with the components to be used, especially for fine-pitch and high-density components.
-
Manufacturing process: Take into account the manufacturing process, including the assembly methods, soldering techniques, and reflow cycles.
-
Cost: Evaluate the cost implications of each surface finish, considering both the initial cost and long-term reliability.
-
Shelf life: Consider the expected shelf life of the PCB and choose a surface finish that can withstand the required storage duration without significant degradation.
Frequently Asked Questions (FAQ)
1. What is the purpose of a surface finish on a PCB?
A surface finish on a PCB serves multiple purposes. It protects the copper layer from oxidation and corrosion, enhances solderability, and improves the durability of the PCB surface.
2. What is an intermetallic layer in the context of PCB surface finishes?
An intermetallic layer is a thin film that forms at the interface between the copper layer and the applied surface finish material. It acts as a protective barrier, preventing oxidation and corrosion of the copper while promoting better solder wetting and bonding.
3. What are the most common types of PCB surface finishes?
The most common types of PCB surface finishes include Hot Air Solder Leveling (HASL), Electroless Nickel Immersion Gold (ENIG), Immersion Silver (ImAg), and Organic Solderability Preservative (OSP).
4. What factors should be considered when selecting a surface finish for a PCB?
When selecting a surface finish for a PCB, consider factors such as application requirements, component compatibility, manufacturing process, cost, and shelf life. Evaluate each surface finish based on its advantages and disadvantages to determine the most suitable option.
5. Can multiple surface finishes be used on the same PCB?
Yes, it is possible to use multiple surface finishes on the same PCB. This is often done to achieve specific requirements for different areas of the board. For example, ENIG can be used for fine-pitch components, while HASL can be used for through-hole components on the same PCB.
Conclusion
PCB surface finishes play a crucial role in protecting the copper layer, enhancing solderability, and ensuring the overall reliability of the PCB. The intermetallic layer formed between the copper and the surface finish material acts as a protective barrier and promotes better solder wetting and bonding.
Various surface finishes are available, each with its own advantages and disadvantages. HASL, ENIG, ImAg, and OSP are among the most common choices, offering different levels of protection, solderability, and compatibility with specific applications.
When selecting a surface finish, it is essential to consider factors such as application requirements, component compatibility, manufacturing process, cost, and shelf life. By carefully evaluating these factors and understanding the characteristics of each surface finish, designers and manufacturers can make informed decisions to ensure the optimal performance and reliability of their PCBs.
As PCB technology continues to advance, new surface finishes and improvements to existing finishes may emerge. Staying up-to-date with the latest developments and industry standards is crucial for maintaining the quality and reliability of PCBs in various applications.
Leave a Reply