What is PCB Programming?
PCB programming, also known as IC programming or device programming, is the process of loading firmware, software, or data onto programmable ICs on a PCB. This step is crucial for ensuring that the ICs function correctly and the PCB performs as designed. Programming can be done at various stages of the PCBA process, depending on the specific requirements and the chosen programming method.
Why is PCB Programming Important?
PCB programming is essential for several reasons:
-
Functionality: Programming the ICs with the correct firmware or software enables them to perform their intended functions within the PCB.
-
Customization: Programming allows for customization of the PCB’s functionality to suit specific applications or customer requirements.
-
Quality control: Proper programming ensures that the PCB functions as designed, reducing the risk of defects or failures in the final product.
-
Cost-effectiveness: Efficient programming methods can help reduce production time and costs in the PCBA process.
7 Methods of IC Programming in PCBA Processing
There are several methods used for programming ICs on PCBs during the assembly process. Each method has its advantages and disadvantages, and the choice depends on factors such as the type of IC, the complexity of the programming, and the production volume. Let’s explore seven common methods of IC programming in PCBA processing.
1. In-System Programming (ISP)
In-System Programming (ISP) is a method that allows ICs to be programmed while they are already soldered onto the PCB. This method utilizes a special programming interface, such as JTAG (Joint Test Action Group) or SPI (Serial Peripheral Interface), to communicate with the target IC.
Advantages of ISP:
– Programming can be done after the IC is soldered onto the PCB
– Allows for easy firmware updates or modifications
– Supports debugging and testing of the PCB
Disadvantages of ISP:
– Requires additional programming hardware and software
– May be slower than other methods for high-volume production
– Limited to ICs that support ISP interfaces
2. In-Circuit Programming (ICP)
In-Circuit Programming (ICP) involves programming the IC using a specialized socket or adapter that connects to the PCB. The socket or adapter provides a temporary connection between the programming hardware and the target IC.
Advantages of ICP:
– Allows for programming of ICs that do not support ISP
– Can be faster than ISP for high-volume production
– Supports a wide range of IC packages
Disadvantages of ICP:
– Requires specialized sockets or adapters for each IC package
– May require additional handling of the PCB during the programming process
– Sockets or adapters can wear out over time, requiring replacement
3. Off-Board Programming
Off-Board Programming involves removing the IC from the PCB and programming it using a standalone programmer. After programming, the IC is then soldered back onto the PCB.
Advantages of Off-Board Programming:
– Allows for programming of ICs before they are soldered onto the PCB
– Supports a wide range of IC packages
– Can be faster than ISP or ICP for high-volume production
Disadvantages of Off-Board Programming:
– Requires additional handling of the ICs, increasing the risk of damage
– Increases production time and costs due to the extra steps involved
– May not be suitable for ICs that are difficult to remove or replace
4. Boundary Scan (JTAG) Programming
Boundary Scan, also known as JTAG (Joint Test Action Group) programming, is a method that uses a special interface to access and program ICs on the PCB. JTAG is an industry-standard interface that allows for testing, debugging, and programming of ICs.
Advantages of Boundary Scan Programming:
– Supports a wide range of ICs that comply with the JTAG standard
– Allows for testing and debugging of the PCB
– Can program multiple ICs in a single operation
Disadvantages of Boundary Scan Programming:
– Requires additional hardware and software for the JTAG interface
– May be slower than other methods for high-volume production
– Limited to ICs that support the JTAG standard
5. Universal Serial Bus (USB) Programming
USB programming involves using a USB interface to program ICs on the PCB. This method requires the PCB to have a USB connector and the necessary circuitry to support USB communication.
Advantages of USB Programming:
– Utilizes a common and widely available interface (USB)
– Allows for easy firmware updates or modifications
– Supports high-speed data transfer
Disadvantages of USB Programming:
– Requires additional USB circuitry on the PCB
– May not be suitable for all types of ICs
– Limited to PCBs with USB connectivity
6. Automatic Programming
Automatic programming uses specialized equipment to program ICs automatically during the PCBA process. This method is suitable for high-volume production and can significantly reduce programming time and costs.
Advantages of Automatic Programming:
– High-speed programming for high-volume production
– Reduces manual labor and human error
– Can support various IC packages and programming methods
Disadvantages of Automatic Programming:
– Requires significant investment in specialized equipment
– May have limited flexibility for customization or small-batch production
– Requires skilled operators and maintenance
7. Wireless Programming
Wireless programming involves programming ICs on the PCB using wireless communication technologies, such as Bluetooth, Wi-Fi, or NFC (Near Field Communication). This method allows for programming and firmware updates without the need for physical connections.
Advantages of Wireless Programming:
– Allows for remote programming and firmware updates
– Eliminates the need for physical programming interfaces
– Supports wireless debugging and testing
Disadvantages of Wireless Programming:
– Requires additional wireless circuitry on the PCB
– May have limited range and data transfer speeds
– Security concerns related to wireless data transmission
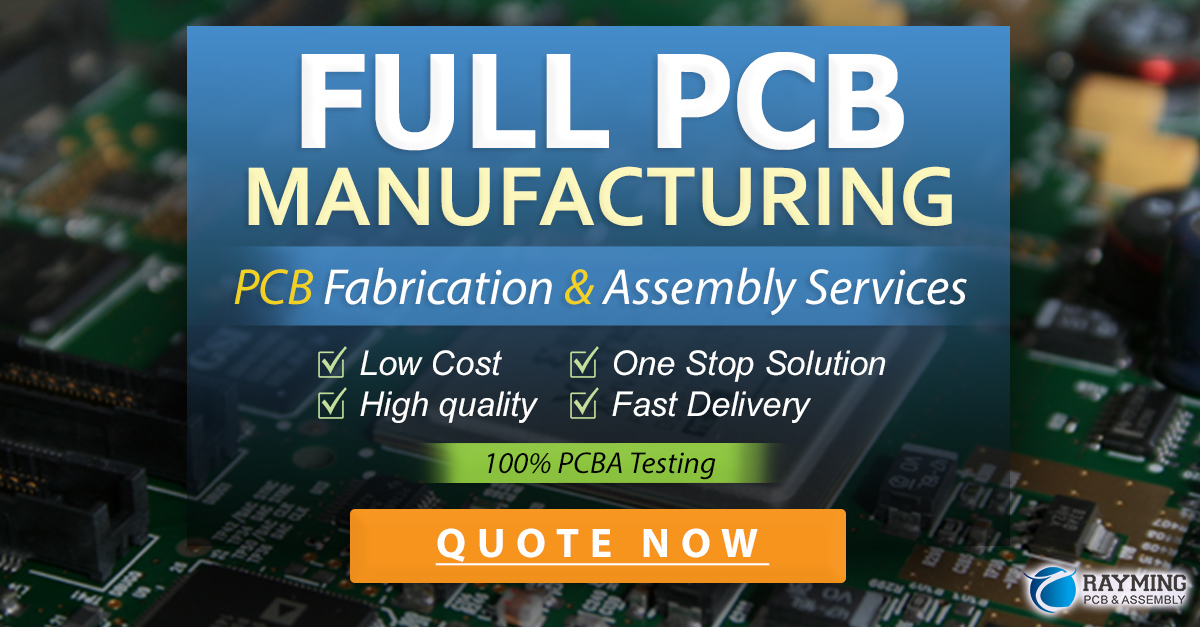
Comparison of IC Programming Methods
Method | Advantages | Disadvantages |
---|---|---|
In-System Programming | – Post-soldering programming – Firmware updates – Debugging support |
– Additional hardware and software – Slower for high-volume production – Limited to ISP-compatible ICs |
In-Circuit Programming | – Supports non-ISP ICs – Faster than ISP for high-volume – Wide range of IC packages |
– Requires specialized sockets or adapters – Additional handling of PCBs – Sockets/adapters wear out over time |
Off-Board Programming | – Pre-soldering programming – Supports various IC packages – Faster than ISP/ICP for high-volume |
– Additional IC handling (risk of damage) – Increases production time and costs – Not suitable for hard-to-remove ICs |
Boundary Scan (JTAG) | – Supports JTAG-compliant ICs – Testing and debugging – Multiple IC programming |
– Additional JTAG hardware and software – Slower for high-volume production – Limited to JTAG-compliant ICs |
USB Programming | – Common and widely available interface – Firmware updates – High-speed data transfer |
– Requires USB circuitry on the PCB – May not suit all IC types – Limited to USB-enabled PCBs |
Automatic Programming | – High-speed programming for high-volume – Reduces manual labor and errors – Supports various IC packages and methods |
– Significant investment in equipment – Limited flexibility for customization or small-batch – Requires skilled operators and maintenance |
Wireless Programming | – Remote programming and updates – No physical connections – Wireless debugging and testing |
– Requires wireless circuitry on the PCB – Limited range and data transfer speeds – Security concerns related to wireless transmission |
Factors to Consider When Choosing an IC Programming Method
When selecting an IC programming method for your PCBA process, consider the following factors:
-
IC type and package: Ensure that the chosen programming method is compatible with the specific ICs and packages used in your PCB design.
-
Production volume: Consider the expected production volume and choose a method that can efficiently handle the required throughput.
-
Programming complexity: Assess the complexity of the firmware or software to be programmed and select a method that can accommodate the necessary data size and structure.
-
Customization and updates: Determine if the PCB requires frequent firmware updates or customization and choose a method that allows for easy modifications.
-
Budget and resources: Evaluate the available budget and resources for programming equipment, software, and skilled personnel.
-
Reliability and quality: Select a programming method that ensures reliable and consistent programming results to maintain the quality of the final product.
Best Practices for Successful PCB Programming
To ensure successful PCB programming, follow these best practices:
-
Verify the programming files: Always verify the accuracy and compatibility of the firmware or software files before programming to avoid errors or failures.
-
Test the programmed PCBs: Conduct thorough testing of the programmed PCBs to ensure they function as intended and meet the required specifications.
-
Maintain programming equipment: Regularly maintain and calibrate the programming equipment to ensure optimal performance and minimize the risk of programming errors.
-
Train personnel: Provide adequate training to personnel involved in the programming process to ensure they follow the correct procedures and handle the equipment and PCBs properly.
-
Document the programming process: Maintain clear and detailed documentation of the programming process, including the equipment, software, and settings used, to ensure consistency and traceability.
Conclusion
PCB programming is a critical step in the PCBA process, ensuring that the assembled PCB functions as designed. The seven methods of IC programming discussed in this article – In-System Programming, In-Circuit Programming, Off-Board Programming, Boundary Scan Programming, USB Programming, Automatic Programming, and Wireless Programming – offer various advantages and disadvantages depending on the specific requirements of the PCB and the production environment.
By understanding the different programming methods and considering factors such as IC type, production volume, programming complexity, customization needs, budget, and reliability, you can select the most appropriate method for your PCBA process. Adhering to best practices and maintaining proper documentation will further ensure the success of your PCB programming endeavors.
Frequently Asked Questions (FAQ)
-
Q: What is the difference between In-System Programming (ISP) and In-Circuit Programming (ICP)?
A: In-System Programming (ISP) allows for programming of ICs while they are already soldered onto the PCB, using a special interface like JTAG or SPI. In-Circuit Programming (ICP) involves programming the IC using a specialized socket or adapter that connects to the PCB, providing a temporary connection between the programming hardware and the target IC. -
Q: Can all ICs be programmed using the same method?
A: No, not all ICs can be programmed using the same method. The choice of programming method depends on factors such as the IC type, package, programming interface, and compatibility with the selected method. It’s essential to ensure that the chosen programming method is suitable for the specific ICs used in your PCB design. -
Q: What are the advantages of Automatic Programming in PCBA processing?
A: Automatic Programming offers several advantages in PCBA processing, including high-speed programming for high-volume production, reduced manual labor and human error, and support for various IC packages and programming methods. It is particularly suitable for high-volume production environments where efficiency and consistency are critical. -
Q: How does Boundary Scan (JTAG) Programming differ from other methods?
A: Boundary Scan, or JTAG Programming, uses a special interface to access and program ICs on the PCB. It supports a wide range of ICs that comply with the JTAG standard and allows for testing and debugging of the PCB. JTAG Programming can also program multiple ICs in a single operation, making it efficient for certain applications. -
Q: What should I consider when choosing an IC programming method for my PCBA process?
A: When choosing an IC programming method, consider factors such as the IC type and package, production volume, programming complexity, customization and update requirements, available budget and resources, and the need for reliability and quality. Assess these factors in the context of your specific PCB design and production environment to select the most appropriate programming method.
Leave a Reply