Introduction to PCB Lay-up
PCB (Printed Circuit Board) lay-up is a crucial step in the multi-layer PCB fabrication process. It involves stacking and aligning multiple layers of the PCB, including the core, prepreg, and copper foil, to create a compact and functional circuit board. The lay-up process ensures that the layers are correctly positioned and oriented before the bonding stage.
The Importance of PCB Lay-up
Proper PCB lay-up is essential for several reasons:
- Signal Integrity: Accurate alignment of the layers ensures that the electrical signals travel through the intended paths without interference or crosstalk.
- Mechanical Stability: Correct lay-up provides structural integrity to the PCB, preventing delamination and other mechanical issues.
- Reliability: A well-executed lay-up process contributes to the overall reliability and longevity of the PCB.
PCB Lay-up Process
The PCB lay-up process typically involves the following steps:
1. Material Preparation
Before starting the lay-up process, all the necessary materials must be prepared and inspected for quality. This includes:
- Core: The base material of the PCB, usually made of FR-4 or other dielectric materials.
- Prepreg: Pre-impregnated glass fiber sheets used as insulating layers between the core and copper foil.
- Copper Foil: Thin sheets of copper that form the conductive layers of the PCB.
2. Layer Stacking
The prepared materials are then stacked in the desired order to form the multi-layer PCB. The stacking sequence depends on the specific design requirements and the number of layers in the PCB.
A typical stacking sequence for a 4-layer PCB might look like this:
Layer | Material |
---|---|
Top | Copper Foil |
Prepreg | |
Inner 1 | Copper Foil |
Core | |
Inner 2 | Copper Foil |
Prepreg | |
Bottom | Copper Foil |
3. Alignment and Registration
Once the layers are stacked, they need to be accurately aligned and registered. This is done using registration pins or holes that ensure the layers are positioned correctly relative to each other.
Proper alignment is crucial for maintaining the desired electrical connections and preventing short circuits or open connections.
4. Lay-up Pressing
After alignment, the stacked layers are placed in a lay-up press. The press applies pressure and heat to the stack, causing the prepreg to melt and flow, bonding the layers together.
The pressing process typically involves the following parameters:
- Temperature: The press is heated to a specific temperature, usually between 180°C and 200°C, depending on the prepreg material used.
- Pressure: A uniform pressure, typically between 200 and 400 PSI, is applied to the stack to ensure proper bonding.
- Time: The stack is held under pressure and heat for a specific duration, usually between 1 and 2 hours, to allow the prepreg to fully cure.
5. Cooling and Inspection
After the pressing cycle, the bonded PCB stack is cooled down to room temperature. The cooled PCB is then inspected for any visible defects, such as delamination, blistering, or uneven thickness.
If the inspection passes, the bonded PCB proceeds to the next stages of fabrication, such as drilling, plating, and etching.
Factors Affecting PCB Lay-up Quality
Several factors can influence the quality of the PCB lay-up process:
-
Material Selection: Choosing the right materials, such as the core, prepreg, and copper foil, with compatible thermal expansion coefficients and bonding properties is essential for a successful lay-up.
-
Environmental Control: The lay-up process should be carried out in a controlled environment with proper temperature, humidity, and cleanliness to prevent contamination and ensure consistent results.
-
Press Parameters: Optimal press temperature, pressure, and time settings are crucial for achieving proper bonding without causing defects like delamination or excessive resin flow.
-
Operator Skill: Skilled and experienced operators are essential for ensuring accurate layer stacking, alignment, and handling of the materials during the lay-up process.
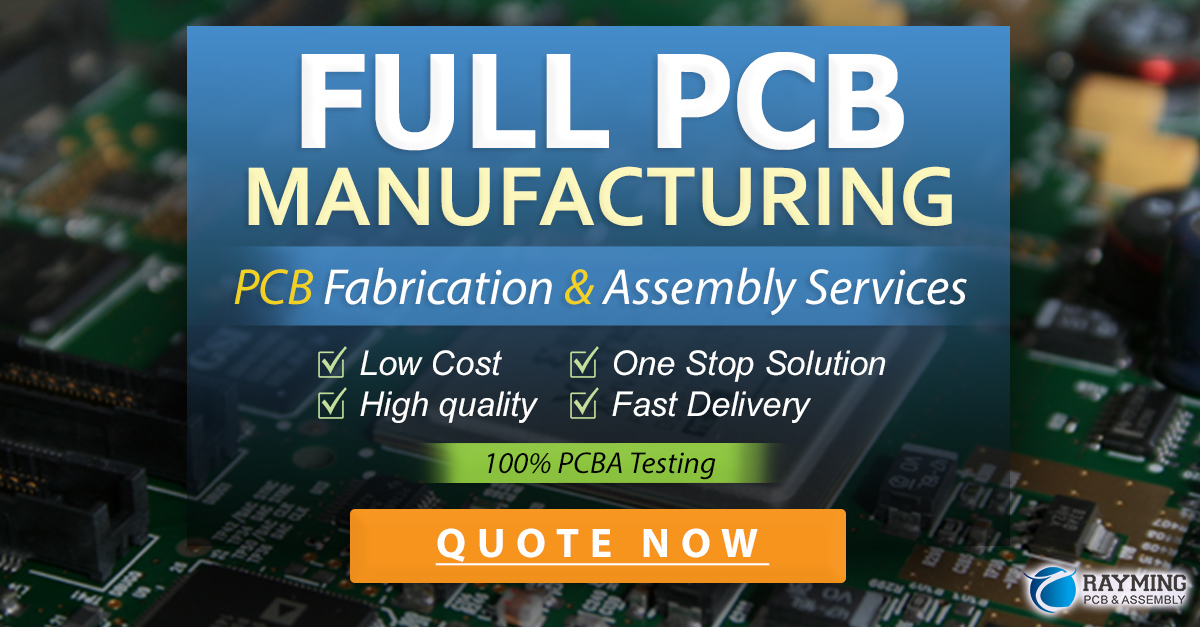
Common PCB Lay-up Defects and Their Causes
Despite careful control of the lay-up process, defects can still occur. Some common PCB lay-up defects and their causes include:
-
Delamination: Separation of the layers due to poor bonding, usually caused by insufficient pressure, temperature, or time during pressing, or contamination of the bonding surfaces.
-
Misregistration: Misalignment of the layers, resulting in incorrect electrical connections. This can be caused by improper use of registration pins or holes, or shifting of the layers during pressing.
-
Blistering: Formation of small bubbles or voids between the layers, often caused by moisture or volatile substances trapped in the prepreg or copper foil.
-
Resin Starvation: Insufficient resin flow between the layers, leading to poor bonding and mechanical weakness. This can be caused by using prepreg with too little resin content or insufficient pressing temperature or time.
-
Resin Squeeze-out: Excessive resin flow beyond the edges of the PCB, resulting in a messy appearance and potential contamination of the equipment. This can be caused by using prepreg with too much resin content or excessive pressing pressure or temperature.
Conclusion
PCB lay-up is a critical step in the multi-layer PCB fabrication process, directly impacting the quality, reliability, and functionality of the final product. By understanding the lay-up process, its key factors, and potential defects, PCB manufacturers can optimize their processes to produce high-quality, reliable multi-layer PCBs consistently.
Investing in advanced equipment, skilled personnel, and strict process control measures can help minimize lay-up defects and improve overall PCB Quality. As the demand for more complex and high-density PCBs continues to grow, mastering the art and science of PCB lay-up will remain a crucial competitive advantage for PCB manufacturers.
Frequently Asked Questions (FAQ)
-
What is the purpose of prepreg in PCB lay-up?
Prepreg, or pre-impregnated glass fiber sheets, serves as an insulating layer between the core and copper foil in a multi-layer PCB. During the lay-up pressing process, the prepreg melts and flows, bonding the layers together and providing electrical insulation between the conductive layers. -
Why is proper alignment critical in PCB lay-up?
Proper alignment of the layers during PCB lay-up is essential for maintaining the desired electrical connections and preventing short circuits or open connections. Misalignment can lead to incorrect functioning of the PCB and potentially damage the connected components. -
What are the typical pressing parameters for PCB lay-up?
The typical pressing parameters for PCB lay-up include a temperature between 180°C and 200°C, a pressure between 200 and 400 PSI, and a duration between 1 and 2 hours. These parameters may vary depending on the specific materials used and the PCB design requirements. -
How can PCB manufacturers prevent lay-up defects?
PCB manufacturers can prevent lay-up defects by selecting compatible materials, maintaining a controlled environment, optimizing press parameters, and employing skilled operators. Strict process control measures and regular inspections can also help identify and correct potential issues before they lead to defects. -
What are the consequences of PCB lay-up defects?
PCB lay-up defects can lead to various problems, such as incorrect electrical connections, reduced mechanical strength, and poor reliability of the final PCB. These defects can cause malfunctions in the connected components, ultimately leading to product failures and customer dissatisfaction. Preventing lay-up defects is crucial for maintaining the quality and reputation of the PCB manufacturer.
Leave a Reply