Understanding Power Supply Noise and Its Impact
Power supply noise can have a significant impact on the performance and reliability of electronic systems. Noise can manifest in various forms, such as ripple, spikes, and ground bounce, which can lead to signal integrity issues, reduced efficiency, and even component failure.
Types of Power Supply Noise
- Ripple Noise
- Caused by incomplete filtering of the rectified AC voltage
- Introduces unwanted AC components on the DC power supply lines
-
Can affect sensitive analog circuits and cause instability
-
Switching Noise
- Generated by high-frequency switching of power converters
- Can couple into sensitive circuits through capacitive and inductive coupling
-
Requires proper layout techniques to minimize its impact
-
Ground Bounce
- Occurs when fast-switching currents flow through the ground plane
- Causes voltage fluctuations on the ground reference
- Can introduce noise into sensitive analog and digital circuits
Effects of Power Supply Noise on System Performance
Power supply noise can have several detrimental effects on system performance, including:
- Signal Integrity Degradation
- Noise can couple into signal lines, causing distortion and errors
-
High-frequency noise can lead to false triggering and timing issues
-
Reduced Efficiency
- Noise can increase power dissipation and reduce overall system efficiency
-
Excessive noise can cause components to operate outside their optimal range
-
Electromagnetic Interference (EMI)
- Power supply noise can radiate and cause interference with nearby electronic devices
- Compliance with EMI regulations is essential for product certification and market acceptance
PCB Layout Techniques for Power Supply Optimization
To optimize power supply performance and minimize noise, several key PCB layout techniques should be employed. These techniques focus on proper component placement, routing, and grounding to ensure a clean and stable power distribution network.
Power and Ground Plane Design
- Use dedicated power and ground planes
- Provides low-impedance paths for power distribution
- Minimizes voltage drops and improves transient response
-
Helps in reducing electromagnetic interference (EMI)
-
Maintain proper plane separation
- Adequate spacing between power and ground planes reduces capacitive coupling
-
Typical spacing ranges from 0.1 mm to 0.3 mm, depending on the dielectric material and operating frequency
-
Utilize plane capacitance
- The inherent capacitance between power and ground planes acts as a distributed decoupling capacitor
- Helps in suppressing high-frequency noise and improving power integrity
Decoupling Capacitor Placement
- Place decoupling capacitors close to ICs
- Minimizes the inductance between the capacitor and the IC power pins
- Provides a low-impedance path for high-frequency noise currents
-
Typical placement is within 5 mm to 10 mm from the IC power pins
-
Use a combination of capacitor values
- Different capacitor values target different frequency ranges
- Bulk capacitors (e.g., 10 µF to 100 µF) handle low-frequency noise and provide energy storage
-
Ceramic capacitors (e.g., 0.1 µF to 1 µF) suppress high-frequency noise and provide local decoupling
-
Minimize capacitor loop area
- Route the capacitor’s power and ground connections with short and wide traces
- Reduces the inductance of the capacitor connection
- Improves the effectiveness of the decoupling capacitor
Power Routing and Current Return Paths
- Route power traces with adequate width
- Wider traces have lower resistance and inductance
- Reduces voltage drops and improves transient response
-
Use PCB design tools to calculate the appropriate trace width based on current requirements
-
Provide a low-impedance return path
- Route the power and ground traces in close proximity to each other
- Minimizes the loop area and reduces electromagnetic radiation
-
Ensures a clean and predictable current return path
-
Use star routing for power distribution
- Connect each power consuming component directly to the power source
- Avoids daisy-chaining power connections, which can introduce noise and voltage drops
- Helps in isolating noise-sensitive circuits from noisy components
Grounding Techniques
- Implement a solid ground plane
- Provides a low-impedance reference for all components
- Acts as a shield against electromagnetic interference (EMI)
-
Helps in minimizing ground loops and reducing ground bounce
-
Use ground planes for different circuit sections
- Separate analog and digital ground planes to minimize noise coupling
- Connect the ground planes at a single point, usually near the power supply
-
Use ferrite beads or inductors to connect the ground planes if required
-
Avoid ground loops
- Ensure that each component has a single path to ground
- Avoid creating multiple ground connections for a single component
- Use star grounding or a ground plane to provide a common reference point
Sensitive Circuit Isolation
- Identify noise-sensitive circuits
- Analog circuits, high-precision ADCs/DACs, and RF circuits are often sensitive to noise
-
Isolate these circuits from noisy components and power supplies
-
Use separate power supplies or regulators
- Provide dedicated power supplies or regulators for sensitive circuits
-
Helps in isolating the sensitive circuits from power supply noise generated by other components
-
Implement guard rings or shielding
- Surround sensitive circuits with a grounded guard ring to provide shielding
- Use copper fills or ground planes to create a barrier against electromagnetic interference (EMI)
- Place sensitive circuits away from high-frequency or high-current components
Power Supply Filtering and Regulation
In addition to proper PCB layout, power supply filtering and regulation techniques play a crucial role in optimizing power supply performance. These techniques help in reducing noise, improving regulation, and ensuring a stable power supply for the system.
Input Filtering
- Use input filters to suppress incoming noise
- Common mode chokes and LC filters can be used to attenuate high-frequency noise
- Place the input filter close to the power supply input connector
-
Ensure proper grounding of the filter components
-
Select appropriate filter components
- Choose filter capacitors with low equivalent series resistance (ESR) and high ripple current ratings
- Use inductor cores with high permeability and low core losses
- Consider the frequency range and attenuation requirements when selecting filter components
Output Filtering
- Implement output filters to reduce output ripple and noise
- LC filters or ferrite beads can be used to suppress high-frequency noise
- Place the output filter close to the power supply output
-
Use low-ESR capacitors for effective high-frequency filtering
-
Consider the load requirements
- Ensure that the output filter is designed to handle the expected load current and transients
- Use larger capacitors or multiple capacitors in parallel for improved filtering and transient response
Voltage Regulation
- Select appropriate voltage regulators
- Linear regulators provide low-noise output but have limited efficiency and power handling capability
- Switching regulators offer higher efficiency but generate high-frequency noise
-
Consider the noise, efficiency, and transient response requirements when selecting regulators
-
Use local regulation for sensitive circuits
- Place voltage regulators close to the sensitive circuits they are powering
- Minimizes the distance between the regulator and the load, reducing noise pickup and voltage drops
-
Use low-dropout (LDO) regulators for low-noise and fast transient response
-
Implement proper regulation techniques
- Use feedback compensation networks to ensure stable regulation under varying load conditions
- Follow the manufacturer’s guidelines for component selection and layout
- Consider using voltage reference ICs for improved regulation accuracy
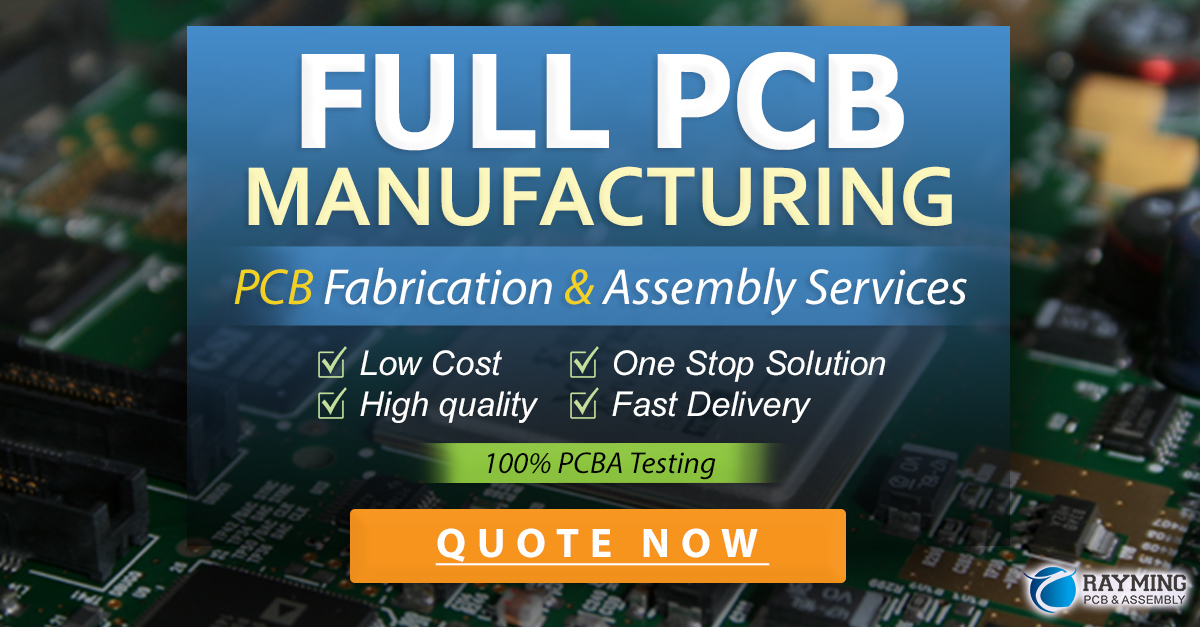
PCB Layout Simulation and Verification
To ensure the effectiveness of the PCB layout techniques and identify potential issues early in the design process, simulation and verification tools can be employed. These tools help in analyzing the power distribution network, identifying voltage drops, and predicting the impact of power supply noise on system performance.
Power Integrity Simulation
- Use PCB design tools with power integrity simulation capabilities
- Perform DC voltage drop analysis to identify areas of excessive voltage drop
- Analyze the impedance profile of the power distribution network
-
Identify resonances and high-impedance points that can amplify noise
-
Simulate the impact of decoupling capacitors
- Verify the effectiveness of decoupling capacitor placement and values
- Analyze the impedance curve with and without decoupling capacitors
- Optimize the decoupling capacitor network based on simulation results
Signal Integrity Simulation
- Perform signal integrity simulations to assess the impact of power supply noise
- Analyze the coupling between power supply noise and critical signal paths
- Identify potential signal integrity issues caused by power supply noise
-
Evaluate the effectiveness of isolation techniques and shielding
-
Use time-domain and frequency-domain simulations
- Time-domain simulations help in analyzing transient behavior and noise propagation
- Frequency-domain simulations provide insights into the frequency content of noise and its impact on signal quality
EMI/EMC Simulation
- Simulate the electromagnetic emissions from the PCB
- Identify potential sources of EMI, such as high-frequency switching components
- Analyze the impact of power supply noise on EMI performance
-
Evaluate the effectiveness of EMI mitigation techniques, such as filtering and shielding
-
Ensure compliance with EMI/EMC regulations
- Use simulation tools to predict the electromagnetic emissions of the PCB
- Compare the simulated emissions with the applicable EMI/EMC standards
- Make necessary modifications to the PCB layout and component selection to meet the regulatory requirements
Best Practices and Guidelines
To optimize power supply performance and ensure a robust PCB layout, consider the following best practices and guidelines:
- Start with a well-defined power distribution network (PDN) design
- Identify the power supply requirements for each component and circuit block
- Determine the expected current consumption and transient behavior
-
Plan the power distribution network architecture, including power planes, traces, and connectors
-
Follow component manufacturer recommendations
- Refer to the component datasheets and application notes for layout guidelines
- Adhere to the recommended Decoupling Capacitor Values and placement
-
Follow the specified thermal management and heat dissipation requirements
-
Use a hierarchical approach to PCB layout
- Start with the placement of critical components and power supply circuitry
- Route the power and ground traces first, followed by signal traces
-
Prioritize the routing of high-speed and noise-sensitive signals
-
Minimize trace lengths and loop areas
- Keep power supply traces as short as possible to reduce inductance and voltage drops
- Route signal traces in close proximity to their respective ground or power planes
-
Avoid creating large loop areas that can act as antennas for noise pickup
-
Utilize ground planes effectively
- Use a continuous ground plane to provide a low-impedance return path
- Avoid splitting the ground plane unnecessarily, as it can create ground loops
-
Connect ground planes of different circuit sections at a single point to minimize ground noise
-
Pay attention to component placement
- Place power supply components close to the power input connector
- Locate decoupling capacitors near the power pins of ICs
-
Arrange components to minimize the distance between power supply and load
-
Consider thermal management
- Ensure adequate heat dissipation for power supply components, such as voltage regulators
- Provide sufficient copper area for heat spreading and use thermal vias if necessary
-
Follow the manufacturer’s recommendations for thermal pad design and heatsink attachment
-
Perform thorough testing and validation
- Conduct power integrity measurements to verify the performance of the power distribution network
- Measure the noise levels at critical points and compare them with the simulation results
- Perform EMI/EMC testing to ensure compliance with regulatory standards
Frequently Asked Questions (FAQ)
- What is the importance of decoupling capacitors in PCB layout?
-
Decoupling capacitors provide a local energy storage reservoir for ICs, reducing the impact of power supply noise and improving transient response. They help in suppressing high-frequency noise and maintaining a stable voltage supply to the components.
-
How do I determine the appropriate trace width for power supply routing?
-
The appropriate trace width depends on factors such as the maximum current carrying capacity, allowable voltage drop, and temperature rise. PCB design tools often provide trace width calculators that take into account these factors. As a general rule, wider traces are preferred for power supply routing to minimize resistance and inductance.
-
What is the difference between analog and digital ground planes?
-
Analog and digital ground planes are used to separate noise-sensitive analog circuits from noisy digital circuits. Analog ground planes provide a clean reference for analog signals, while digital ground planes handle the return currents from digital components. Separating the ground planes helps in minimizing noise coupling between analog and digital sections of the PCB.
-
How can I minimize the impact of power supply noise on sensitive analog circuits?
-
To minimize the impact of power supply noise on sensitive analog circuits, several techniques can be employed. These include using separate power supplies or regulators for analog circuits, implementing local decoupling capacitors, using guard rings or shielding, and physically separating analog circuits from noisy digital components. Proper grounding and filtering techniques also play a crucial role in reducing noise coupling.
-
What are the common simulation tools used for power integrity analysis?
- There are several simulation tools available for power integrity analysis, including:
- ANSYS SIwave: A comprehensive tool for power integrity, signal integrity, and EMI analysis
- Cadence Sigrity: Offers power integrity analysis, including DC voltage drop, AC impedance, and decoupling capacitor optimization
- Mentor Graphics HyperLynx: Provides power integrity simulation, including DC and AC analysis, decoupling capacitor placement, and PDN impedance analysis
- Altium Designer: Integrates power distribution network analysis and simulation capabilities within the PCB design environment
These tools help in identifying potential power integrity issues, optimizing the PDN design, and ensuring the robustness of the power supply network.
Conclusion
Optimizing power supply performance through proper PCB layout is essential for achieving reliable and efficient electronic systems. By understanding the impact of power supply noise, employing effective layout techniques, and following best practices, designers can minimize noise, improve signal integrity, and ensure the overall system performance.
Key aspects of PCB layout for power supply optimization include proper power and ground plane design, strategic decoupling capacitor placement, careful power routing and current return paths, effective grounding techniques, and sensitive circuit isolation. Additionally, power supply filtering and regulation techniques, such as input and output filtering and appropriate voltage regulation, contribute to noise reduction and stable power delivery.
Simulation and verification tools play a vital role in analyzing the power distribution network, identifying potential issues, and optimizing the PCB layout. Power integrity, signal integrity, and EMI/EMC simulations help in predicting the impact of power supply noise on system performance and ensuring compliance with regulatory standards.
By following the guidelines and best practices discussed in this article, PCB designers can effectively optimize power supply performance, minimize noise and interference, and achieve robust and reliable electronic systems. Proper PCB layout, combined with careful component selection and design validation, is key to delivering high-quality and efficient power supply solutions.
Leave a Reply