Introduction to PCB Insulation
Printed Circuit Board (PCB) insulation is a critical aspect of PCB design and manufacturing that involves using non-conductive materials to separate and isolate the electrical pathways on a PCB. The main purpose of PCB insulation is to prevent short circuits, signal interference, and other electrical issues that can arise when conductive traces or components come into contact with each other.
PCB insulation is achieved through the use of various non-conductive materials that are applied to the PCB surface or between the layers of a multi-layer PCB. These insulating materials act as barriers, preventing electrical current from flowing between adjacent traces or layers.
Importance of PCB Insulation
PCB insulation plays a crucial role in ensuring the proper functioning, reliability, and longevity of electronic devices. Here are some key reasons why PCB insulation is essential:
-
Preventing Short Circuits: Insulation prevents unintended electrical contact between conductive parts of the PCB, which can cause short circuits. Short circuits can lead to device malfunction, damage to components, and even fire hazards.
-
Reducing Signal Interference: Proper insulation helps to minimize electromagnetic interference (EMI) and crosstalk between adjacent traces or layers. This is particularly important in high-frequency and sensitive analog circuits where signal integrity is critical.
-
Enhancing Durability: Insulation protects the PCB and its components from environmental factors such as moisture, dust, and chemical contaminants. This protection improves the overall durability and lifespan of the electronic device.
-
Meeting Safety Standards: Adequate PCB insulation is necessary to comply with various safety standards and regulations, such as those set by Underwriters Laboratories (UL), the International Electrotechnical Commission (IEC), and other regulatory bodies.
Types of PCB Insulation Materials
Several types of insulation materials are used in PCB manufacturing, each with its own properties and applications. Some common PCB insulation materials include:
1. Solder Mask
Solder mask, also known as solder resist, is a thin layer of polymer that is applied to the outer surface of a PCB. Its primary functions are to:
- Insulate the copper traces from accidental contact with other conductive materials
- Prevent solder bridging between closely spaced pads during the soldering process
- Protect the copper traces from oxidation and corrosion
- Provide a surface for applying component designators and other markings
Solder mask is typically applied using screen printing or photoimaging techniques and is available in various colors, with green being the most common.
2. Prepreg
Prepreg, short for “pre-impregnated,” is a composite material used in multi-layer PCBs to insulate and bond the individual layers together. It consists of a glass fiber fabric that is pre-impregnated with a partially cured epoxy resin. During the PCB lamination process, the prepreg is placed between the PCB layers and subjected to heat and pressure, causing the resin to flow and fully cure, bonding the layers together.
Prepreg provides the following benefits:
- Electrical insulation between the PCB layers
- Mechanical strength and stability to the PCB structure
- Controlled dielectric constant and thickness for consistent electrical performance
The thickness and dielectric properties of the prepreg can be selected based on the specific requirements of the PCB design.
3. Core Materials
Core materials, also known as substrate materials, are used as the base layer in PCBs. They provide mechanical support and electrical insulation for the copper traces and components. The most common core materials used in PCBs are:
-
FR-4: A composite material made of woven fiberglass cloth impregnated with an epoxy resin. FR-4 is the most widely used core material due to its good mechanical and electrical properties, as well as its cost-effectiveness.
-
High-Tg FR-4: A variation of FR-4 with a higher glass transition temperature (Tg), which offers better thermal stability and resistance to delamination in high-temperature applications.
-
Polyimide: A high-performance polymer that offers excellent thermal stability, chemical resistance, and mechanical strength. Polyimide is often used in aerospace, military, and other demanding applications.
-
Teflon (PTFE): A fluoropolymer known for its low dielectric constant, low dissipation factor, and high thermal stability. Teflon is used in high-frequency and microwave PCBs.
The choice of core material depends on the specific requirements of the PCB, such as the operating temperature range, dielectric properties, and mechanical stability needed.
4. Conformal Coatings
Conformal coatings are thin, protective layers applied to the surface of a PCB after assembly. They provide additional insulation and protection against environmental factors such as moisture, dust, chemicals, and mechanical stress. Common types of conformal coatings include:
-
Acrylic: A general-purpose coating that offers good moisture and fungus resistance, as well as easy application and removal.
-
Silicone: A highly flexible and heat-resistant coating that provides excellent protection against thermal shock and vibration.
-
Polyurethane: A tough, abrasion-resistant coating that offers good chemical resistance and mechanical strength.
-
Parylene: A vapor-deposited polymer coating that provides uniform, pin-hole free coverage and excellent dielectric properties.
The selection of a conformal coating depends on the specific environmental conditions and performance requirements of the PCB.
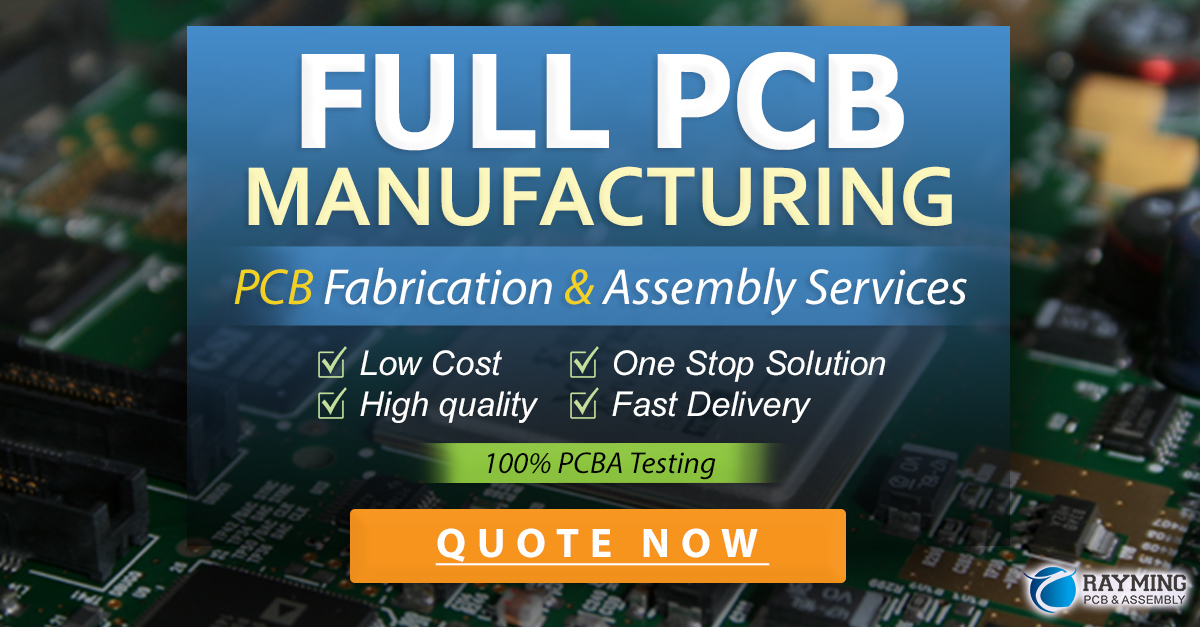
PCB Insulation Techniques
Several techniques are used to apply insulation materials to PCBs during the manufacturing process. These techniques ensure proper coverage, thickness, and adhesion of the insulating layers. Some common PCB insulation techniques include:
1. Screen Printing
Screen printing is a technique used to apply solder mask and other thick film coatings to PCBs. The process involves:
- Creating a stencil (screen) with the desired pattern
- Placing the screen over the PCB
- Applying the coating material using a squeegee
- Curing the coating using heat or ultraviolet (UV) light
Screen printing is a cost-effective method for applying solder mask and other coatings in high volumes.
2. Photoimaging
Photoimaging is a more precise method for applying solder mask and other coatings to PCBs. The process involves:
- Applying a photosensitive coating to the PCB
- Exposing the coating to UV light through a photomask with the desired pattern
- Developing the coating to remove the unexposed areas
- Curing the remaining coating using heat or UV light
Photoimaging offers higher resolution and finer pitch compared to screen printing, making it suitable for more complex PCB designs.
3. Lamination
Lamination is the process of bonding multiple layers of a PCB together using prepreg and heat and pressure. The process involves:
- Stacking the PCB layers with prepreg in between
- Placing the stack in a lamination press
- Applying heat and pressure for a specific duration
- Cooling the laminated PCB
Lamination ensures proper insulation and bonding between the layers of a multi-layer PCB.
4. Spraying and Dipping
Spraying and dipping are methods used to apply conformal coatings to PCBs after assembly. Spraying involves using a spray gun to apply a thin, even layer of the coating material to the PCB surface. Dipping involves immersing the PCB in a tank of the coating material and then allowing it to drain and cure.
Both spraying and dipping methods provide complete coverage of the PCB surface and components, offering protection against environmental factors.
PCB Insulation Design Considerations
When designing a PCB, several factors related to insulation need to be considered to ensure proper performance, reliability, and manufacturability. Some key PCB insulation design considerations include:
1. Clearance and Creepage Distances
Clearance is the shortest distance between two conductive parts through air, while creepage is the shortest distance between two conductive parts along the surface of an insulating material. Adequate clearance and creepage distances must be maintained to prevent electrical breakdown and ensure insulation integrity.
The required clearance and creepage distances depend on factors such as:
- Operating voltage
- Pollution degree (environment)
- Insulating material properties
- Altitude
Industry standards, such as IPC-2221, provide guidelines for determining the appropriate clearance and creepage distances based on these factors.
2. Insulation Thickness
The thickness of the insulating layers, such as solder mask and prepreg, must be sufficient to provide the necessary electrical insulation and mechanical strength. The minimum insulation thickness depends on factors such as:
- Operating voltage
- Layer count
- Dielectric strength of the insulating material
PCB manufacturers typically offer standard thicknesses for solder mask and prepreg, but custom thicknesses can be specified for special requirements.
3. Material Selection
The selection of insulation materials should be based on the specific requirements of the PCB, such as:
- Operating temperature range
- Dielectric constant and dissipation factor
- Thermal conductivity
- Mechanical strength and flexibility
- Chemical resistance
- Cost
For example, high-performance materials like polyimide and Teflon may be necessary for demanding applications, while FR-4 may be sufficient for general-purpose PCBs.
4. Manufacturing Capabilities
The PCB design must take into account the manufacturing capabilities of the PCB fabricator, such as:
- Minimum solder mask thickness and resolution
- Minimum prepreg thickness and layer count
- Available core materials and thicknesses
- Conformal coating options
Consultation with the PCB manufacturer during the design phase can help ensure that the insulation requirements are achievable and cost-effective.
PCB Insulation Testing and Inspection
To ensure the quality and reliability of PCB insulation, various testing and inspection methods are employed during and after the manufacturing process. Some common PCB insulation testing and inspection methods include:
1. Dielectric Withstanding Voltage (DWV) Test
The DWV test, also known as the high-potential (hipot) test, involves applying a high voltage between the conductive parts of the PCB to ensure that the insulation can withstand the specified voltage without breakdown. The test voltage is typically several times higher than the operating voltage of the PCB.
2. Insulation Resistance (IR) Test
The IR test measures the resistance between the conductive parts of the PCB through the insulating material. A high insulation resistance indicates good insulation quality and the absence of defects such as pinholes or contaminants.
3. Visual Inspection
Visual inspection is performed to check the coverage, uniformity, and adherence of the solder mask and other insulating layers. This can be done manually using a magnifying lens or automatically using automated optical inspection (AOI) systems.
4. Microsectioning
Microsectioning involves cutting a cross-section of the PCB and examining it under a microscope to verify the thickness and integrity of the insulating layers, as well as the clearance and creepage distances between conductive parts.
5. Thermal Cycling and Shock Testing
Thermal cycling and shock testing involve subjecting the PCB to alternating high and low temperatures to simulate the thermal stresses encountered during operation. These tests help to evaluate the durability and reliability of the insulation materials and their adhesion to the PCB.
Regular testing and inspection of PCB insulation ensure that the manufactured boards meet the specified requirements and industry standards, minimizing the risk of failure in the field.
FAQ
1. What is the difference between clearance and creepage in PCB insulation?
Clearance refers to the shortest distance between two conductive parts through air, while creepage is the shortest distance between two conductive parts along the surface of an insulating material. Both clearance and creepage distances must be maintained to ensure proper insulation and prevent electrical breakdown.
2. What is the most common solder mask color used in PCBs?
The most common solder mask color used in PCBs is green. However, other colors such as red, blue, yellow, and black are also available. The choice of solder mask color is usually a matter of preference or for specific applications, such as white solder mask for LED lighting PCBs.
3. Can conformal coatings be removed from a PCB?
Yes, conformal coatings can be removed from a PCB if necessary, such as for rework or repair. The removal method depends on the type of coating material. For example, acrylic coatings can be removed using solvents, while silicone coatings may require mechanical abrasion. It is important to follow the manufacturer’s guidelines and take necessary precautions when removing conformal coatings to avoid damaging the PCB.
4. What is the purpose of microsectioning in PCB insulation testing?
Microsectioning is a destructive testing method that involves cutting a cross-section of the PCB and examining it under a microscope. The purpose of microsectioning is to verify the thickness and integrity of the insulating layers, as well as the clearance and creepage distances between conductive parts. This method provides a detailed view of the PCB structure and helps to identify any manufacturing defects or deviations from the design specifications.
5. How can I select the appropriate insulation material for my PCB design?
Selecting the appropriate insulation material for your PCB design depends on several factors, such as the operating temperature range, dielectric properties, mechanical requirements, and cost. Consider the following steps:
- Define the environmental and performance requirements of your PCB.
- Consult industry standards and guidelines, such as IPC-4101, for material classifications and properties.
- Compare the properties of different insulation materials, such as FR-4, polyimide, and Teflon, against your requirements.
- Consult with your PCB manufacturer for their material availability, capabilities, and recommendations.
- Consider the cost implications of your material choice and optimize for the best balance between performance and cost.
By carefully evaluating your requirements and working closely with your PCB manufacturer, you can select the most suitable insulation material for your specific PCB design.
Conclusion
PCB insulation is a critical aspect of PCB design and manufacturing that ensures the proper functioning, reliability, and safety of electronic devices. By using appropriate insulation materials, such as solder mask, prepreg, and conformal coatings, and following proper design guidelines and manufacturing processes, PCBs can be protected from short circuits, signal interference, and environmental factors.
Careful consideration of insulation requirements, material selection, and testing and inspection methods is essential for producing high-quality PCBs that meet industry standards and perform reliably in their intended applications.
As electronic devices continue to become more complex and compact, the importance of effective PCB insulation will only continue to grow. By staying up-to-date with the latest materials, technologies, and best practices in PCB insulation, designers and manufacturers can ensure that their products meet the evolving demands of the electronics industry.
Insulation Material | Key Properties | Common Applications |
---|---|---|
Solder Mask | Insulates and protects copper traces, prevents solder bridging | Outer layer of PCBs |
Prepreg | Insulates and bonds layers in multi-layer PCBs | Inner layers of multi-layer PCBs |
FR-4 | Good mechanical and electrical properties, cost-effective | General-purpose PCBs |
Polyimide | High thermal stability, chemical resistance, and strength | Aerospace, military, and high-temperature PCBs |
Teflon (PTFE) | Low dielectric constant, low dissipation factor, high thermal stability | High-frequency and microwave PCBs |
Leave a Reply