Introduction to PCB Drilling
Printed Circuit Board (PCB) drilling is a crucial step in the manufacturing process of PCBs. It involves creating holes of various sizes and depths in the PCB substrate to accommodate components, vias, and mounting points. The accuracy and precision of these holes are essential for the proper functioning and reliability of the final product.
In this article, we will dive deep into the world of PCB hole sizes, exploring the different types of holes, their purposes, and the methods used to drill them. We will also discuss the factors that influence hole size selection and provide tips for achieving optimal results.
Types of PCB Holes
There are several types of holes commonly found in PCBs, each serving a specific purpose:
Component Holes
Component holes are drilled to accommodate the leads or pins of through-hole components such as resistors, capacitors, and integrated circuits. The hole size depends on the component’s lead diameter and the required clearance for soldering.
Via Holes
Via holes are used to connect different layers of a multi-layer PCB. They allow electrical signals to pass from one layer to another. The size of via holes depends on the current carrying capacity, manufacturing constraints, and signal integrity requirements.
Mounting Holes
Mounting holes are used to secure the PCB to an enclosure or chassis using screws, standoffs, or other fasteners. These holes are typically larger than component or via holes and may require additional reinforcement.
Tooling Holes
Tooling holes are used for aligning and registering the PCB during the manufacturing process. They are not electrically functional but are essential for ensuring the accuracy and repeatability of the drilling and assembly operations.
Factors Affecting PCB Hole Size
Several factors influence the selection of PCB hole sizes:
Component Requirements
The hole size must accommodate the leads or pins of the components used in the design. Manufacturers provide recommended hole sizes for their components, which should be followed to ensure proper fit and solderability.
Current Carrying Capacity
For via holes, the hole size should be large enough to handle the expected current flow without causing excessive heating or voltage drop. The thickness of the copper plating inside the hole also affects its current carrying capacity.
Manufacturing Constraints
The minimum hole size that can be reliably drilled depends on the capabilities of the PCB manufacturer. Smaller holes require more precise drilling equipment and may increase the manufacturing cost.
Signal Integrity
In high-speed designs, the hole size and placement can affect signal integrity. Smaller via holes minimize the discontinuity in the signal path, reducing reflections and improving signal quality.
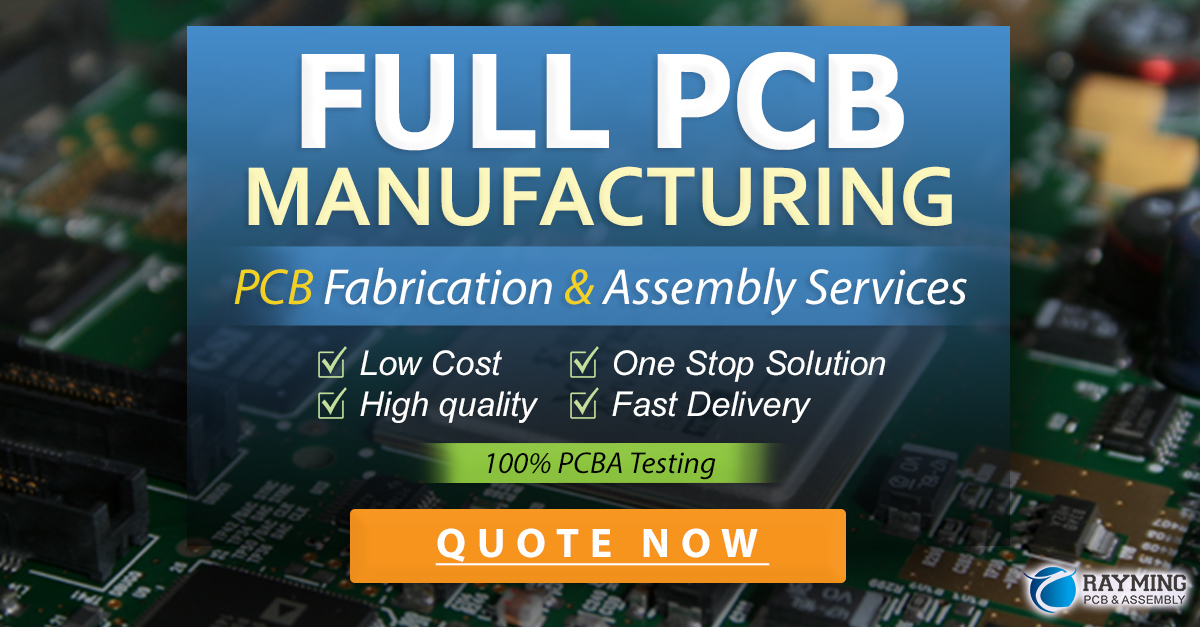
PCB Hole Size Standards
To ensure compatibility and consistency, the electronics industry has established standards for PCB hole sizes. The most common standard is the Imperial (inch) system, although metric sizes are also used in some regions.
Imperial Size | Metric Size | Drill Bit Size |
---|---|---|
0.015″ | 0.38mm | #97 |
0.020″ | 0.51mm | #76 |
0.025″ | 0.64mm | #68 |
0.030″ | 0.76mm | #65 |
0.040″ | 1.02mm | #60 |
0.050″ | 1.27mm | #55 |
0.060″ | 1.52mm | #53 |
0.070″ | 1.78mm | #50 |
0.080″ | 2.03mm | #46 |
0.090″ | 2.29mm | #43 |
0.100″ | 2.54mm | #40 |
These standard sizes provide a range of options for various applications. However, custom hole sizes can also be specified when necessary, subject to the manufacturer’s capabilities.
PCB Drilling Methods
There are two primary methods for drilling holes in PCBs:
Mechanical Drilling
Mechanical drilling uses high-speed drill bits to create holes in the PCB substrate. The drill bits are typically made of carbide or diamond-coated materials to withstand the abrasive nature of the laminate. Mechanical drilling is the most common method for creating larger holes (>0.2mm) and is suitable for both prototype and high-volume production.
Advantages of mechanical drilling:
– Wide range of hole sizes
– Suitable for various materials
– High drilling speed
– Cost-effective for larger holes
Disadvantages of mechanical drilling:
– Limited precision for small holes
– Drill bit wear and breakage
– Potential for smear and burr formation
Laser Drilling
Laser drilling uses a focused laser beam to vaporize the PCB material, creating precise and small holes. This method is particularly useful for creating microvias (holes <0.1mm) in high-density interconnect (HDI) PCBs. Laser drilling offers higher precision and smaller hole sizes compared to mechanical drilling.
Advantages of laser drilling:
– High precision and accuracy
– Smaller hole sizes (down to 0.05mm)
– No drill bit wear or breakage
– Minimal material damage and burr formation
Disadvantages of laser drilling:
– Higher equipment cost
– Slower drilling speed compared to mechanical drilling
– Limited material compatibility (some materials may not be suitable for laser drilling)
The choice between mechanical and laser drilling depends on the specific requirements of the PCB design, such as hole size, precision, and material properties.
Optimizing PCB Hole Quality
To ensure the best possible hole quality and minimize manufacturing issues, consider the following tips:
- Follow the manufacturer’s recommended hole sizes for components and vias.
- Use a grid system for hole placement to maintain consistency and alignment.
- Avoid placing holes too close to the edge of the PCB or other features.
- Specify the correct drill bit size and tolerances in the manufacturing files.
- Use plated through-holes (PTH) for better mechanical and electrical integrity.
- Consider using a larger hole size and pad diameter for improved solderability and reliability.
- Perform regular maintenance and calibration of drilling equipment to ensure accuracy and repeatability.
By following these guidelines and working closely with your PCB manufacturer, you can achieve high-quality holes that meet your design requirements and ensure the reliability of your final product.
Frequently Asked Questions (FAQ)
1. What is the smallest hole size that can be drilled in a PCB?
The smallest hole size that can be drilled in a PCB depends on the manufacturing capabilities of the PCB fabricator. Most manufacturers can reliably drill holes down to 0.2mm (0.008″) using mechanical drilling. For smaller holes, such as microvias, laser drilling can achieve sizes as small as 0.05mm (0.002″).
2. How do I choose the right hole size for my components?
When selecting hole sizes for your components, refer to the manufacturer’s datasheet or application notes. They will provide recommended hole sizes for each component based on its lead diameter and soldering requirements. It’s essential to follow these recommendations to ensure proper fit and solderability.
3. Can I use the same hole size for all the vias in my PCB?
While it’s possible to use the same hole size for all the vias in your PCB, it may not always be the optimal choice. The hole size should be selected based on the current carrying capacity, signal integrity requirements, and manufacturing constraints. In some cases, using different hole sizes for different types of vias (e.g., power vias vs. signal vias) can be beneficial.
4. What is the difference between plated and non-plated holes?
Plated holes, also known as plated through-holes (PTH), have a layer of copper deposited on the walls of the hole, creating an electrical connection between the layers of the PCB. Non-plated holes, on the other hand, do not have this copper layer and are used for mechanical purposes, such as mounting holes or tooling holes.
5. How can I minimize drill bit breakage during PCB drilling?
To minimize drill bit breakage, consider the following tips:
- Use high-quality, sharp drill bits suitable for the PCB material.
- Ensure proper drilling parameters, such as feed rate and spindle speed.
- Regularly inspect and replace worn or damaged drill bits.
- Use a backing material to support the PCB during drilling.
- Avoid drilling through metal components or other hard materials.
By following these tips and working with an experienced PCB manufacturer, you can minimize drill bit breakage and improve the overall quality of your PCB holes.
Conclusion
PCB hole size is a critical aspect of PCB design and manufacturing. Understanding the different types of holes, their purposes, and the factors that influence hole size selection is essential for creating reliable and high-quality PCBs.
By following industry standards, selecting the appropriate drilling method, and optimizing hole quality, you can ensure that your PCBs meet the required specifications and perform as intended.
Remember to work closely with your PCB manufacturer, communicate your requirements clearly, and stay up-to-date with the latest advancements in PCB drilling technology. By doing so, you can stay ahead of the curve and create PCBs that are both functional and reliable.
Leave a Reply