What is PCB Glue?
PCB glue, also known as PCB adhesive, is a specialized type of adhesive used in the assembly and manufacturing of printed circuit boards (PCBs). These adhesives play a crucial role in ensuring the reliability, durability, and performance of electronic devices. PCB glue is designed to bond various components to the PCB substrate, provide electrical insulation, and protect the components from environmental factors such as moisture, vibration, and thermal stress.
Importance of PCB Adhesives
PCB adhesives are essential in the electronics industry for several reasons:
-
Bonding: PCB glue securely bonds electronic components, such as integrated circuits (ICs), capacitors, and resistors, to the PCB substrate. This ensures that the components remain in place during the manufacturing process and throughout the product’s lifecycle.
-
Electrical Insulation: Many PCB adhesives have excellent electrical insulation properties, preventing short circuits and current leakage between components and the PCB substrate.
-
Thermal Management: Some PCB glues, particularly thermal adhesives, help dissipate heat generated by electronic components, preventing overheating and ensuring optimal performance.
-
Vibration and Shock Resistance: PCB adhesives provide mechanical stability to the assembled components, protecting them from vibration and shock, which can cause damage or lead to device failure.
-
Miniaturization: As electronic devices become smaller and more compact, PCB adhesives enable the tight packaging of components, allowing for higher component density and reduced device size.
Key Applications of PCB Glue
PCB adhesives are used in a wide range of applications across various industries:
Consumer Electronics
PCB glue is extensively used in the production of consumer electronic devices, such as:
- Smartphones and tablets
- Laptops and computers
- Televisions and displays
- Wearable devices (e.g., smartwatches, fitness trackers)
- Gaming consoles and controllers
Automotive Electronics
In the automotive industry, PCB adhesives are used in the assembly of various electronic systems, including:
- Engine control units (ECUs)
- Infotainment systems
- Advanced driver assistance systems (ADAS)
- Electronic power steering
- Lighting systems
Medical Devices
PCB glue plays a crucial role in the manufacturing of medical devices, ensuring reliability and performance in critical applications, such as:
- Patient monitoring systems
- Diagnostic equipment
- Implantable devices (e.g., pacemakers, defibrillators)
- Surgical instruments
- Medical imaging systems
Aerospace and Defense
In the aerospace and defense sectors, PCB adhesives are used in the production of high-performance electronic systems, including:
- Avionics
- Radar and surveillance systems
- Satellite communication devices
- Military-grade computers and displays
- Unmanned aerial vehicles (UAVs)
Industrial Electronics
PCB glue is utilized in the assembly of industrial electronic devices, such as:
- Process control systems
- Automation equipment
- Power electronics
- Sensors and transducers
- Telecommunications infrastructure
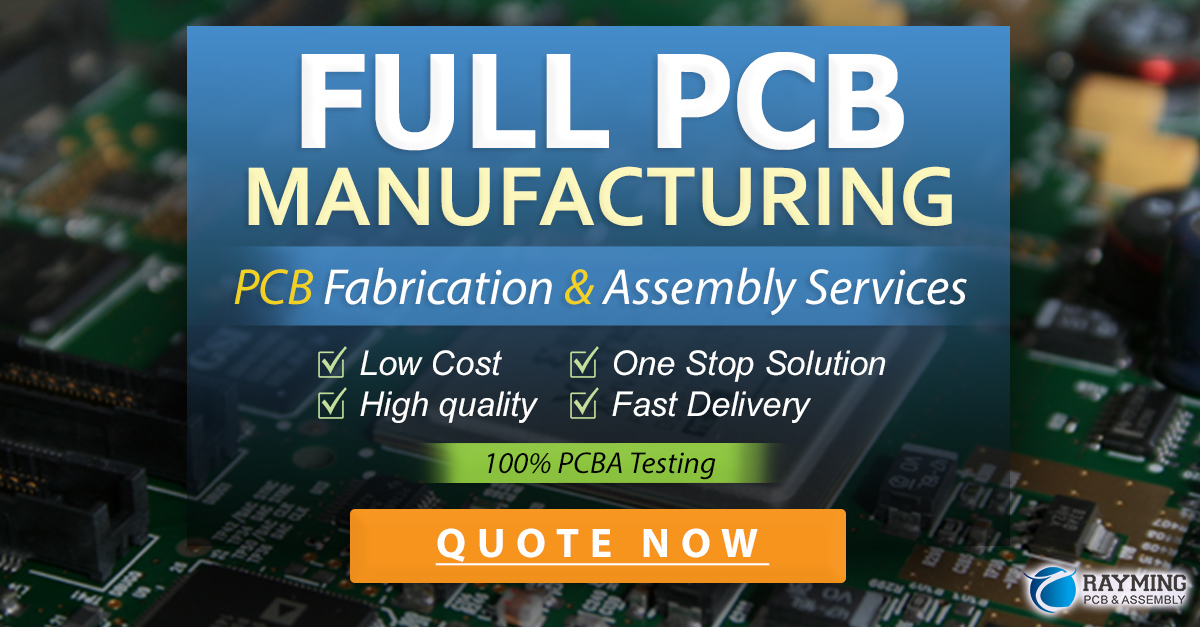
Types of PCB Adhesives
There are several types of PCB adhesives, each with unique properties and applications:
Epoxy Adhesives
Epoxy adhesives are the most common type of PCB glue. They offer excellent bonding strength, electrical insulation, and resistance to environmental factors. Epoxy adhesives are available in various formulations, including:
- One-part epoxies: These adhesives cure at elevated temperatures and provide strong, rigid bonds.
- Two-part epoxies: These adhesives consist of a resin and a hardener that are mixed prior to application. They offer better flexibility and lower curing temperatures compared to one-part epoxies.
- Conductive epoxies: These adhesives contain conductive fillers, such as silver or carbon, which allow electrical conductivity between components and the PCB substrate.
Silicone Adhesives
Silicone adhesives are known for their excellent flexibility, thermal stability, and resistance to moisture and chemicals. They are commonly used in applications that require low stress on components or where high-temperature performance is necessary. Silicone adhesives are available in various types, such as:
- Room temperature vulcanizing (RTV) silicones: These adhesives cure at room temperature upon exposure to moisture in the air.
- Heat-cured silicones: These adhesives require elevated temperatures for curing and offer better mechanical strength and chemical resistance compared to RTV silicones.
Acrylic Adhesives
Acrylic adhesives are known for their fast curing times, good adhesion to various substrates, and resistance to environmental factors. They are often used in applications that require quick assembly and where lower bonding strength is acceptable. Acrylic adhesives can be further classified into:
- Anaerobic acrylics: These adhesives cure in the absence of oxygen and presence of metal ions, making them suitable for bonding threaded fasteners and cylindrical parts.
- Cyanoacrylates: Also known as instant adhesives, cyanoacrylates cure rapidly upon contact with moisture on the substrate surface.
UV-Curable Adhesives
UV-curable adhesives, as the name suggests, cure upon exposure to ultraviolet (UV) light. These adhesives offer fast curing times, good adhesion, and minimal shrinkage during curing. UV-curable adhesives are ideal for applications that require quick assembly and where the bond line is accessible to UV light.
Thermal Adhesives
Thermal adhesives are designed to provide efficient heat transfer between electronic components and heat sinks or other cooling solutions. These adhesives often contain thermally conductive fillers, such as ceramic or metal particles, to enhance their thermal conductivity. Thermal adhesives help dissipate heat generated by components, preventing overheating and ensuring optimal performance.
Factors to Consider When Selecting PCB Glue
When choosing a PCB adhesive for a specific application, several factors should be considered:
-
Substrate Compatibility: Ensure that the adhesive is compatible with the materials used in the PCB substrate and components, such as FR-4, polyimide, or ceramic.
-
Environmental Conditions: Consider the environmental factors the device will be exposed to, such as temperature range, humidity, chemicals, and vibration, and select an adhesive that can withstand these conditions.
-
Curing Method: Choose an adhesive with a curing method that is suitable for the manufacturing process and production requirements, such as room temperature curing, heat curing, or UV curing.
-
Electrical Properties: For applications that require electrical insulation, select an adhesive with high dielectric strength and low conductivity. For conductive applications, choose an adhesive with the appropriate level of conductivity.
-
Thermal Management: If thermal management is a concern, opt for adhesives with good thermal conductivity to facilitate heat dissipation from components.
-
Viscosity and Dispensing: Consider the adhesive’s viscosity and its compatibility with the dispensing equipment used in the manufacturing process, such as needle dispensers, jet dispensers, or screen printing.
-
Rework and Repair: In some cases, the ability to rework or repair the assembled PCB may be necessary. Select an adhesive that allows for easy removal or rework without damaging the components or substrate.
PCB Glue Application Methods
PCB adhesives can be applied using various methods, depending on the adhesive type, viscosity, and the manufacturing process:
Manual Dispensing
Manual dispensing involves applying the adhesive using hand-held tools, such as syringes, brushes, or spatulas. This method is suitable for low-volume production or prototype assembly, where precise control over the adhesive application is required.
Automated Dispensing
Automated dispensing systems, such as needle dispensers or jet dispensers, are used for high-volume production. These systems offer precise control over the adhesive volume, placement, and dispense pattern, ensuring consistent and accurate application.
Screen Printing
Screen printing is a method used for applying adhesives over a large area or in a specific pattern. A stencil or screen with the desired pattern is placed over the PCB substrate, and the adhesive is spread across the screen using a squeegee. This method is suitable for high-volume production and applications that require uniform adhesive thickness.
Stamping or Pin Transfer
Stamping or pin transfer involves using a stamping tool or pin to pick up a controlled amount of adhesive from a reservoir and transfer it to the PCB substrate. This method is useful for applying small dots of adhesive or for applications that require precise placement of the adhesive.
Curing Methods for PCB Glue
After the adhesive is applied, it must be cured to achieve its final properties and form a strong bond between the components and the PCB substrate. The curing method depends on the type of adhesive used:
Room Temperature Curing
Some adhesives, such as RTV silicones and certain epoxies, cure at room temperature upon exposure to moisture or air. These adhesives are suitable for applications where heating the PCB is not feasible or where a slower curing process is acceptable.
Heat Curing
Many adhesives, including epoxies and silicones, require elevated temperatures for curing. Heat curing can be achieved using ovens, hot plates, or inline heating systems. The curing temperature and duration depend on the specific adhesive formulation.
UV Curing
UV-curable adhesives are exposed to UV light of a specific wavelength to initiate the curing process. UV curing offers fast curing times and is suitable for applications where the bond line is accessible to UV light. UV curing systems can be integrated into automated assembly lines for high-volume production.
Quality Control and Testing
To ensure the reliability and performance of PCB assemblies, it is essential to implement quality control measures and conduct testing:
-
Visual Inspection: Visually inspect the assembled PCB for any defects, such as incomplete adhesive coverage, bridging, or component misalignment.
-
Adhesion Testing: Perform adhesion tests, such as lap shear or tensile tests, to evaluate the bond strength between the components and the PCB substrate.
-
Environmental Testing: Subject the assembled PCB to environmental tests, such as temperature cycling, humidity exposure, or vibration testing, to assess its durability and reliability under various conditions.
-
Electrical Testing: Conduct electrical tests, such as continuity, insulation resistance, or functional tests, to verify the electrical performance of the assembled PCB.
-
Thermal Imaging: Use thermal imaging cameras to identify hot spots or areas of poor thermal conductivity, indicating potential issues with the thermal management of the device.
Future Trends in PCB Adhesives
As the electronics industry continues to evolve, PCB adhesives are expected to advance to meet the changing requirements:
-
Increased Thermal Conductivity: With the growing demand for high-performance electronics, adhesives with higher thermal conductivity will be developed to efficiently dissipate heat from components.
-
Improved Flexibility: Flexible and stretchable electronics will require adhesives that can accommodate substrate deformation without compromising bond strength or electrical performance.
-
Environmental Sustainability: There will be a greater emphasis on developing eco-friendly and biodegradable PCB adhesives to reduce the environmental impact of electronic waste.
-
Nanomaterials: The incorporation of nanomaterials, such as carbon nanotubes or graphene, into PCB adhesives may enhance their mechanical, electrical, and thermal properties.
-
3D Printing Compatibility: As 3D printing technology advances, PCB adhesives that are compatible with 3D printing processes will be developed to enable the production of complex, three-dimensional electronic structures.
Conclusion
PCB glue plays a vital role in the assembly and reliability of electronic devices across various industries. By understanding the key applications, types, and properties of PCB adhesives, engineers and manufacturers can select the most suitable adhesive for their specific requirements. As the electronics industry continues to advance, PCB adhesives will evolve to meet the growing demands for performance, reliability, and sustainability.
Frequently Asked Questions (FAQ)
- What is the difference between electrically conductive and insulating PCB adhesives?
-
Electrically conductive PCB adhesives contain conductive fillers, such as silver or carbon, which allow electrical current to flow between components and the PCB substrate. In contrast, insulating PCB adhesives have high dielectric strength and prevent current flow, providing electrical isolation between components.
-
Can PCB adhesives be removed for rework or repair?
-
The ability to remove PCB adhesives depends on the specific type of adhesive used. Some adhesives, such as certain thermoplastics or UV-curable adhesives, can be softened or dissolved using heat or solvents, allowing for component removal and rework. However, other adhesives, like thermoset epoxies, form permanent bonds and are difficult to remove without damaging the components or substrate.
-
How do I select the right viscosity for my PCB adhesive?
-
The viscosity of the PCB adhesive should be selected based on the application method and the desired adhesive thickness. Low-viscosity adhesives are suitable for spray coating or dip coating, while medium-viscosity adhesives are ideal for needle dispensing or jet dispensing. High-viscosity adhesives are best for screen printing or stencil printing applications.
-
What is the shelf life of PCB adhesives, and how should they be stored?
-
The shelf life of PCB adhesives varies depending on the specific formulation and storage conditions. Most adhesives have a shelf life of six months to one year when stored in their original, unopened containers at the recommended temperature, typically between 5°C and 25°C. Some adhesives may require refrigeration to extend their shelf life. Always consult the manufacturer’s storage guidelines and use the adhesive within its specified shelf life to ensure optimal performance.
-
Are there any health and safety precautions to consider when working with PCB adhesives?
- Yes, it is essential to follow proper health and safety guidelines when working with PCB adhesives. Many adhesives contain chemicals that may be harmful if inhaled, ingested, or in contact with skin or eyes. Always read and follow the manufacturer’s safety data sheet (SDS) for the specific adhesive being used. Use appropriate personal protective equipment (PPE), such as gloves, safety glasses, and respiratory protection, when handling adhesives. Work in a well-ventilated area and avoid skin contact or inhalation of adhesive fumes. In case of accidental contact or exposure, follow the first-aid measures outlined in the SDS and seek medical attention if necessary.
Type of PCB Adhesive | Key Characteristics | Typical Applications |
---|---|---|
Epoxy (One-part) | – Strong, rigid bonds – High-temperature curing – Excellent chemical resistance |
– General-purpose bonding – Structural bonding – Harsh environment applications |
Epoxy (Two-part) | – Better flexibility than one-part epoxies – Lower curing temperatures – Good chemical resistance |
– Bonding dissimilar materials – Applications requiring some flexibility – Large-area bonding |
Silicone (RTV) | – Excellent flexibility – Room-temperature curing – Good thermal stability |
– Bonding delicate components – Applications with thermal cycling – Sealing and encapsulation |
Silicone (Heat-cured) | – Better mechanical strength than RTV silicones – Excellent chemical resistance – High-temperature performance |
– High-reliability applications – Harsh environment exposure – Automotive and aerospace electronics |
Acrylic (Anaerobic) | – Fast curing – Good adhesion to metals – Resistance to vibration and shock |
– Bonding threaded fasteners – Cylindrical part bonding – Securing connectors and terminals |
Acrylic (Cyanoacrylate) | – Rapid curing – Instant adhesion – Bonding dissimilar materials |
– Quick assembly applications – Bonding small components – Temporary fixturing |
UV-Curable | – Fast curing with UV exposure – Minimal shrinkage – Suitable for automated dispensing |
– High-volume production – Applications with accessible bond lines – Bonding transparent substrates |
Thermal Adhesive | – Enhanced thermal conductivity – Efficient heat dissipation – Electrical insulation |
– Bonding heat sinks to components – Thermal management of high-power devices – LED lighting assemblies |
Leave a Reply